PROCEDIMIENTO Y APARATO PARA LA FABRICACION DE DISIPADORES DE CALOR CON UNA ALTA DENSIDAD DE ALETAS.
Un procedimiento de fabricación de un disipador de calor de placa base dual (10),
dicho procedimiento comprendiendo:
- proporcionar una pluralidad de aletas conductoras del calor (22), cada una con extremos opuestos (24);
- proporcionar dos placas base conductoras del calor opuestas (12), cada una de dichas placas base (12) comprendiendo una superficie encarada hacia dentro (14) con una pluralidad de áreas de apoyo alargadas (11) en la misma, cada una de dichas áreas de apoyo (11) separada por un canal alargado (16);
- insertar dichos extremos (24) de dichas aletas (22) dentro del respectivo de dichos canales (16) de cada una de dichas placas base opuestas (12);
- colocar una primera parte de una herramienta de estampación (40, 42) entre dichas placas base opuestas (12), dicha herramienta de estampación (40, 42) comprendiendo una serie de puntas alargadas (42), dicha serie de puntas (42) dimensionadas para ser dispuestas adyacentes a cada una de dichas aletas (22), cada una de dichas puntas (42) incrementando en altura desde dicha primera parte hasta una segunda parte; mientras se mantiene la distancia relativa entre dichas placas base (12), deslizar dicha herramienta de estampación (40, 42) adyacente a dichas aletas (22) en una dirección paralela cada una a dicha superficie (14) de modo que dicha segunda parte de cada una de dichas puntas (42) aplica de forma creciente presión a un área de apoyo correspondiente (11) para estampar de forma creciente dicha área de apoyo (11) contra cada aleta adyacente (22); por lo que la estampación de cada una de dichas áreas de apoyo (11) fija cada una de dichas aletas (22) a cada una de dichas placas base (2)
Tipo: Patente Europea. Resumen de patente/invención. Número de Solicitud: E06007763.
Solicitante: R-THETA THERMAL SOLUTIONS INC.
Nacionalidad solicitante: Canadá.
Dirección: 6220 KESTREL ROAD,MISSISSAUGA ON L5T 1Y9.
Inventor/es: ZAGHLOL,AHMED.
Fecha de Publicación: .
Fecha Solicitud PCT: 13 de Abril de 2006.
Fecha Concesión Europea: 19 de Mayo de 2010.
Clasificación Internacional de Patentes:
- H01L21/48C5P
Clasificación PCT:
- H01L21/48 ELECTRICIDAD. › H01 ELEMENTOS ELECTRICOS BASICOS. › H01L DISPOSITIVOS SEMICONDUCTORES; DISPOSITIVOS ELECTRICOS DE ESTADO SOLIDO NO PREVISTOS EN OTRO LUGAR (utilización de dispositivos semiconductores para medida G01; resistencias en general H01C; imanes, inductancias, transformadores H01F; condensadores en general H01G; dispositivos electrolíticos H01G 9/00; pilas, acumuladores H01M; guías de ondas, resonadores o líneas del tipo guía de ondas H01P; conectadores de líneas, colectores de corriente H01R; dispositivos de emisión estimulada H01S; resonadores electromecánicos H03H; altavoces, micrófonos, cabezas de lectura para gramófonos o transductores acústicos electromecánicos análogos H04R; fuentes de luz eléctricas en general H05B; circuitos impresos, circuitos híbridos, envolturas o detalles de construcción de aparatos eléctricos, fabricación de conjuntos de componentes eléctricos H05K; empleo de dispositivos semiconductores en circuitos que tienen una aplicación particular, ver la subclase relativa a la aplicación). › H01L 21/00 Procedimientos o aparatos especialmente adaptados para la fabricación o el tratamiento de dispositivos semiconductores o de dispositivos de estado sólido, o bien de sus partes constitutivas. › Fabricación o tratamiento de partes, p. ej. de contenedores, antes del ensamblado de los dispositivos, utilizando procedimientos no cubiertos por un único grupo de H01L 21/06 - H01L 21/326.
- H01L23/367 H01L […] › H01L 23/00 Detalles de dispositivos semiconductores o de otros dispositivos de estado sólido (H01L 25/00 tiene prioridad). › Refrigeración facilitada por la forma del dispositivo.
Países PCT: Austria, Bélgica, Suiza, Alemania, Dinamarca, España, Francia, Reino Unido, Grecia, Italia, Liechtensein, Luxemburgo, Países Bajos, Suecia, Mónaco, Portugal, Irlanda, Eslovenia, Finlandia, Rumania, Chipre, Lituania, Letonia, Ex República Yugoslava de Macedonia, Albania.
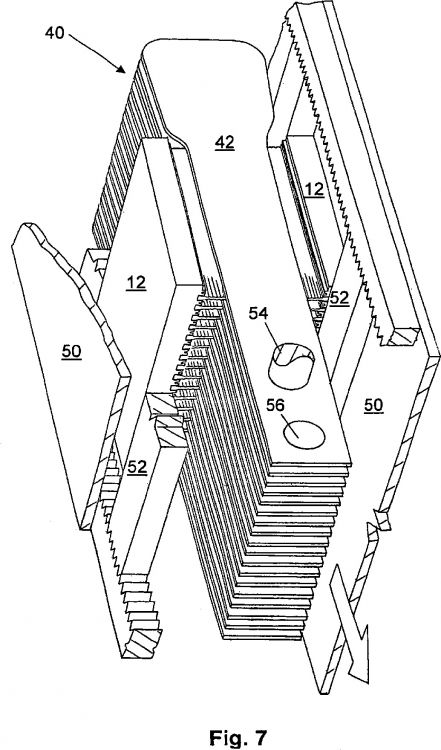
Fragmento de la descripción:
Procedimiento y aparato para la fabricación de disipadores de calor con una alta densidad de aletas.
Campo de la invención
Esta invención se refiere en general a la fabricación de disipadores de calor y más específicamente a un procedimiento para el acoplamiento de las aletas en un disipador de alta densidad de aletas a placas base duales de disipación del calor.
Antecedentes de la invención
Son conocidos los disipadores de calor en la técnica para la recepción y la disipación después del calor generado por circuitos electrónicos en los dispositivos modernos. Tales disipadores de calor muy conocidos típicamente comprenden un conjunto base al cual están montados los dispositivos electrónicos que generan calor y una pluralidad de aletas que se prolongan desde el conjunto base para la disipación del calor generado. Es un reto hacer máxima el área superficial de las aletas a fin de proporcionar una transferencia de calor óptima desde el disipador de calor a la atmósfera circundante mientras se asegura un buen contacto térmico entre el conjunto base y las aletas.
Han sido propuestos disipadores de calor fabricados mediante extrusión de metal, en el que las aletas y los conjuntos base son de una construcción integral y de ese modo tienen un óptimo contacto térmico. Sin embargo, como se describe en la exposición de la patente americana US Nº 5,406,698 (Lipinksi), se ha mostrado que existen límites al tamaño y a la forma de las aletas que se pueden realizar mediante la fabricación por extrusión. Por lo tanto han sido propuestos diversos procedimientos de fabricación en los que las aletas son extruidas separadamente del conjunto base y a continuación acopladas utilizando diversos procedimientos.
El documento USP 5,771,966 (Jacoby) expone un elemento plegado conductor del calor o aleta con por lo menos un inserto de metal recocido provisto de un grosor previamente determinado que corresponde a una distancia entre las partes conductoras del calor primera y segunda de la aleta y un grosor previamente determinado que corresponde a una profundidad de la ranura en la placa base de modo que el inserto de metal recocido se adapta a la forma de la ranura cuando se deforma para fijar la zona de acoplamiento de la parte de la base del elemento conductor del calor plegado en el interior de la ranura. La patente de Jacoby propone una matriz de estampación para llevar a cabo la función de deformación o estampación para deformar la aleta mientras está en la ranura de modo que no se pueda extraer.
La patente de los Estados Unidos Nº 6,263,956 de Tang y otros establece una estructura de disipación de calor y un procedimiento de fabricación en el que cada muesca en la base tiene un ancho ligeramente inferior que el grosor de una parte de inserción de la aleta de disipación de calor asociada, de modo que permitirá que la aleta de disipación del calor se inserte apretadamente en su interior. Un bastidor de fijación se moldea entonces en su sitio para fijar las aletas. El bastidor de fijación se forma mediante la introducción de un material de fijación fundido en el interior de las entalladuras de fijación y después de eso se refrigera. Cuando el material solidifica, forma el bastidor de fijación que fija las aletas de disipación del calor sobre la base.
La solicitud de patente americana publicada US Nº 2002/0007936 (Woerner y otros) expone uno o más conjuntos de aletas plegadas "adheridas" a la base en puntos seleccionados mediante soldadura por láser. En una operación subsiguiente, la superficie completa de las partes de red inferior de los conjuntos de aletas plegadas se unen a la base, típicamente mediante soldadura fuerte. Según la exposición de Woerner, se utiliza algún medio mecánico adecuado para forzar las partes de red inferiores contra la base antes de la soldadura por láser, para optimizar el contacto entre las partes de red inferiores y la base cuando tiene lugar la soldadura fuerte subsiguiente. También, se utiliza una herramienta de peine para mantener la separación deseada entre aletas adyacentes antes de la soldadura por láser, para optimizar esa separación y evitar la posibilidad de que aletas adyacentes se coloquen no uniformemente o en contacto una con otra. El conjunto de disipadores de calor se dice que se descarga del aparato de soldadura por láser y se lleva para la soldadura fuerte, la soldadura de estaño y plomo o bien otra unión adecuada a la base. Como un ejemplo, el conjunto de disipador de calor puede recibir una aplicación de pulverización de fundente el cual es entonces secado al horno y se puede pasar a un horno de soldadura fuerte para calentarlo a una gama de temperaturas de 1100-1120ºF para realizar la soldadura fuerte.
La solicitud de patente americana publicada US Nº 2002/0043359 (Mizutani) establece un procedimiento para la fabricación de un disipador de calor en el que las aletas son presionadas por medio de un molde de modo que los salientes provistos en el lado posterior de la placa de metal son presionados dentro de "entalladuras expandidas en la parte inferior" para fijar las aletas de disipación de calor y la placa base juntas. Mizutani enseña un molde de matriz de estampación para presionar los salientes en la placa base contra las aletas para mantenerlas fijadas a la placa base.
Como se ha mencionado antes, la patente americana US Nº 5,406,698 (Lipinksi) propone un disipador de calor fabricado proporcionando una placa base con varias ranuras paralelas en su superficie. Se fabrican aletas individuales provistas de una cola de milano o una parte inferior en campana en sus extremos, siendo insertados entonces los extremos dentro de las ranuras respectivas. La placa base se deforma a continuación en las áreas entre los canales paralelos mediante la laminación de una pluralidad de rodillos coaxiales a través de las áreas a fin de apretar o estampar las aletas en el interior de las ranuras. El aparato de Lipinski es un diseño excelente que requiere que sea transmitida poca presión a través de las propias aletas, de modo que se minimiza su tendencia indeseable al alabeo bajo la presión hacia abajo. Sin embargo, en el proceso de deformación del conjunto base en las áreas entre los canales paralelos, el conjunto base entero tiende a torcerse. Con este propósito, la patente americana US Nº 5,638,715 (Lipinksi) establece un aparato para invertir a continuación el efecto de torcedura.
El documento DE 199 00 970 A1 (Glück Joachim) describe un disipador de calor de placa base dual.
El documento DE 296 01 776 U1 (Alusuisse Lonza Services AG) describe un proceso de estampación para un disipador de calor.
Con la creciente demanda de los consumidores de sistemas electrónicos más complejos, ha aparecido la necesidad de una utilización más eficaz del espacio cuando se fabrican estos sistemas. Para ayudar a cubrir esta demanda, han sido propuestos disipadores de calor de placa base dual que están montados en más de un dispositivo electrónico pero que disipan el calor a través de un conjunto común de aletas. Con estas propuestas ha aparecido un conjunto correspondiente de retos para la fabricación de los disipadores de calor de acuerdo con especificaciones que promueven una transferencia excelente del calor y un buen contacto entre las placas pasen y las aletas. Por ejemplo, el aparato de Lipinksi no sería suficiente para la fabricación de disipadores de calor de placa base dual puesto que al conjunto de rodillos propuesto no se le permitiría pasar a través de los espacios entre las aletas una vez la segunda placa base estuviera colocada en su sitio.
Resumen de la invención
Según la presente invención, se fabrica un disipador de calor de placa base dual de alta densidad de aletas colocando las aletas una al lado de la otra en canales formados en cada una de dos placas bases opuestas. A fin de acoplar las placas base y las aletas, la distancia relativa entre las placas base se mantiene constante y una herramienta de estampar se pasa tanto entre las aletas adyacentes como entre las placas base en una dirección paralela a las placas base. La presión ejercida por la herramienta de estampación contra las placas base adyacentes a las aletas cuando las placas base son mantenidas a una distancia relativa constante estampa la placa base adyacente a cada aleta contra la aleta. Se aplica de ese modo presión al extremo de cada aleta insertada en cada canal fijando de ese modo la aleta a la placa base.
Breve descripción de los dibujos
Una descripción detallada de la forma de realización preferida se establece en detalle más adelante en este documento, con referencia...
Reivindicaciones:
1. Un procedimiento de fabricación de un disipador de calor de placa base dual (10), dicho procedimiento comprendiendo:
- proporcionar una pluralidad de aletas conductoras del calor (22), cada una con extremos opuestos (24);
- proporcionar dos placas base conductoras del calor opuestas (12), cada una de dichas placas base (12) comprendiendo una superficie encarada hacia dentro (14) con una pluralidad de áreas de apoyo alargadas (11) en la misma, cada una de dichas áreas de apoyo (11) separada por un canal alargado (16);
- insertar dichos extremos (24) de dichas aletas (22) dentro del respectivo de dichos canales (16) de cada una de dichas placas base opuestas (12);
- colocar una primera parte de una herramienta de estampación (40, 42) entre dichas placas base opuestas (12), dicha herramienta de estampación (40, 42) comprendiendo una serie de puntas alargadas (42), dicha serie de puntas (42) dimensionadas para ser dispuestas adyacentes a cada una de dichas aletas (22), cada una de dichas puntas (42) incrementando en altura desde dicha primera parte hasta una segunda parte; mientras se mantiene la distancia relativa entre dichas placas base (12), deslizar dicha herramienta de estampación (40, 42) adyacente a dichas aletas (22) en una dirección paralela cada una a dicha superficie (14) de modo que dicha segunda parte de cada una de dichas puntas (42) aplica de forma creciente presión a un área de apoyo correspondiente (11) para estampar de forma creciente dicha área de apoyo (11) contra cada aleta adyacente (22); por lo que la estampación de cada una de dichas áreas de apoyo (11) fija cada una de dichas aletas (22) a cada una de dichas placas base (2).
2. El procedimiento de la reivindicación 1 en el que cada una de dichas áreas de apoyo (11) comprende pares de mordazas alargadas (18), cada mordaza (20) en dichos pares de mordazas (18) estando provista de una sección transversal uniforme que se ensancha primero progresivamente y después se estrecha desde su extremo distante hasta dicha superficie (14), dicho ensanchamiento correspondiendo a una reducción en la distancia entre partes correspondientes de las mordazas (20) en cada uno de dichos pares de mordazas (18) y en el que dicha etapa de deslizamiento comprende la aplicación de forma creciente de una presión de acuñamiento a dichas mordazas (20) para estampar dichas mordazas (20) contra dichas aletas (22).
3. El procedimiento de la reivindicación 1 o 2 adicionalmente comprendiendo la prevención de que dichas aletas (22) se muevan con relación a dichas placas base (12) durante dicha etapa de deslizamiento.
4. El procedimiento de la reivindicación 3 en el que dicha prevención se efectúa aplicando presión sobre dichas placas base (12) para incrementar la fricción entre dichas aletas (22) y dichas placas base (12).
5. El procedimiento de la reivindicación 3 o 4 en el que dicha prevención se efectúa apoyando una pared que evita el deslizamiento (52) contra un extremo de cada una de dichas placas base (12).
6. Una herramienta de estampación (40, 42, 50) para utilizarla en el acoplamiento de dos placas base conductoras del calor opuestas (12) cada una provista de una superficie encarada hacia dentro (14) con una pluralidad de áreas de apoyo alargadas (11) separadas por un canal alargado (16), a una pluralidad de aletas conductoras del calor (22) cada una provista de extremos opuestos (24), dicha herramienta de estampación (40, 42) comprendiendo:
- una estructura de retención (50, 52) para mantener la distancia relativa entre dichas placas base (12), con los extremos (24) de dichas aletas (22) insertados en el interior de los respectivos de dichos canales (16);
- una serie de puntas planas paralelas (42) colocadas entre dichas placas base opuestas (12) y entre las respectivas de dichas aletas (22), cada una de dichas puntas (42) estando provista de un primer extremo que crece en altura hacia un segundo extremo y dimensionada para deslizar paralela a dicha superficie (14) entre dichas placas base (12) y adyacente a la respectiva área de apoyo (11); y
- un aparato (54, 56) para deslizar dichas series de puntas planas paralelas (42) adyacentes a dichas aletas (22) en una dirección paralela cada una a dicha superficie (14) de modo que dicha segunda parte de cada una de dichas puntas (42) aplica de forma creciente presión al área de apoyo respectiva (11), para estampar de forma creciente cada una de dichas áreas de apoyo (11) contra cada aleta adyacente (22) para fijarla a cada una de dichas placas base (12).
7. La herramienta de estampación de la reivindicación 6 en la que cada una de dichas áreas de apoyo (11) comprende pares de mordazas alargadas (18), cada mordaza (20) en dichos pares de mordazas (20, 18) estando provista de una sección transversal uniforme que primero se ensancha progresivamente y después se estrecha desde su extremo distante hasta dicha superficie (14) dicho ensanchamiento correspondiendo a una reducción en la distancia entre partes correspondientes de las mordazas (20) en cada uno de dichos pares de mordazas (18) y en el que por lo menos dicha segunda parte de cada punta (42) en dichas series es de forma acuñada en sus bordes para facilitar la aplicación de presión de acuñamiento a dichas mordazas (20) para estampar dichas mordazas contra dichas aletas (22).
8. La herramienta de la reivindicación 6 o 7 en la que dicha estructura de retención (50, 52) adicionalmente comprende un par de paredes que evitan la expansión (50) para mantener la distancia relativa entre dichas placas base (12).
9. La herramienta de estampación de cualquiera de las reivindicaciones 6 a 8 en la que dicha estructura de retención (50, 52) adicionalmente comprende un par de paredes que evitan el deslizamiento (52) para evitar que dichas aletas (22) deslicen con relación a dichas placas base (12) durante dicho deslizamiento de dichas series de puntas planas paralelas (42).
10. La herramienta de estampación de cualquiera de las reivindicaciones 6 a 9 en la que dicho aparato adicionalmente comprende un árbol (54) que pasa a través de un taladro en cada una de dichas puntas planas (42) para arrastrar dichas series de puntas planas paralelas (42) entre las respectivas de dichas aletas (22).
11. Una placa base (12) para un disipador de calor de placa base dual (10) fabricada a partir de aletas extruidas separadamente (22), dicha placa base (12) comprendiendo:
- un conjunto base conductor del calor globalmente plano, dicho conjunto base estando provisto de una superficie principal (14) con una pluralidad de pares de mordazas conductoras del calor alargadas (18) que dependen de dicha superficie principal (14), cada uno de dichos pares de mordazas (18) separado por un canal alargado (16) para recibir el extremo respectivo de una de dichas aletas (22), cada una de las mordazas (20) en dichos pares de mordazas (18) estando provista de una sección transversal uniforme que primero se ensancha progresivamente y después se estrecha desde su extremo distante hasta dicha superficie, el ensanchamiento correspondiendo a una reducción en la distancia entre las partes correspondientes de las mordazas (20) en cada uno de dichos pares de mordazas (18), por lo que el estrechamiento proporciona a dichas mordazas (20) una flexibilidad incrementada de modo que cuando cada una de dichas aletas (22) es recibida por un canal respectivo (16), una estampación subsiguiente separada de las mordazas (20) contra dichas aletas (22) para acoplar dichas aletas (22) a dicha placa base (12) transmite un momento de plegado bajo al dicho conjunto base.
Patentes similares o relacionadas:
SISTEMA DE GESTIÓN TÉRMICA, del 24 de Noviembre de 2011, de GRAFTECH INTERNATIONAL HOLDINGS INC: Sistema de gestión térmica, que comprende una fuente de calor que tiene una superficie exterior y un esparcidor de calor que comprende una única lámina […]
ENSAMBLADO COMBINADO DE BASE DE FIJACION Y TUBO DE CALOR, del 18 de Marzo de 2010, de GOLDEN SUN NEWS TECHNIQUES CO., LTD.
CPUMATE INC: Un ensamblado combinado de una base de fijación y un tubo de calor, que comprende:
un base de fijación que presenta un cuerpo de placa, una superficie […]
Disipador de calor para enfriar electrónica de energía, del 8 de Julio de 2020, de CARRIER CORPORATION: Un dispositivo disipador de calor para enfriar un módulo de electrónica de energía que comprende: una plataforma de base que tiene una primera superficie […]
Aparato y procedimiento para interfaz térmica, del 18 de Marzo de 2020, de Emblation Limited: Un aparato para su uso como un amplificador que comprende: un transistor de radiofrecuencia o microondas para proporcionar amplificación de señal; […]
Estructura de protección para el aislamiento de señal y procedimiento para su fabricación, del 1 de Mayo de 2019, de Thales Solutions Asia Pte Ltd: Un procedimiento de fabricación de una estructura de protección eléctrica para proporcionar el aislamiento de señal que comprende las etapas de: proporcionar […]
Placa de circuitos impresos, circuito impreso y procedimiento para la fabricación de un circuito impreso, del 28 de Noviembre de 2018, de AUTO-KABEL MANAGEMENT GMBH: Placa de circuito impreso (2a) con - una placa de soporte metálica , - una capa aislante que aísla eléctricamente la placa de soporte metálica […]
Disipador de calor, del 2 de Noviembre de 2018, de SIMON, S.A.U: Disipador de calor, que comprende: · un cuerpo central ; y · primeras aletas (3a) y segundas aletas (3b) que se prolongan del cuerpo central y que se distribuyen […]
Recubrimiento no metálico y método de su producción, del 16 de Agosto de 2017, de Cambridge Nanolitic Limited: Un método de formación de un recubrimiento no metálico sobre una superficie de un sustrato metálico o semimetálico que comprende las etapas de: […]