Procedimiento y dispositivo para la fabricación de componentes compuestos de fibra.
Procedimiento para la fabricación de componentes compuestos de fibra mediante impregnación de un producto defibra semiacabado (2) con una matriz de plásticos (3),
preferentemente una resina duroplástica o termoplástica, quese dispone sobre o bajo el producto de fibra semiacabado (2), caracterizado porque la matriz de plásticos (3) seaplica en una cantidad de resina que se dosifica por zonas de superficie localmente diferentes, que se seleccionaen función del respectivo espesor de pared en la región del componente compuesto de fibra que se va a fabricar.
Tipo: Patente Europea. Resumen de patente/invención. Número de Solicitud: E10189668.
Solicitante: C-Con GmbH.
Nacionalidad solicitante: Alemania.
Dirección: Konradin-Kreutzer-Strasse 28 71069 Sindelfingen ALEMANIA.
Inventor/es: GEORGII,Andreas.
Fecha de Publicación: .
Clasificación Internacional de Patentes:
- B29C43/18 TECNICAS INDUSTRIALES DIVERSAS; TRANSPORTES. › B29 TRABAJO DE LAS MATERIAS PLASTICAS; TRABAJO DE SUSTANCIAS EN ESTADO PLASTICO EN GENERAL. › B29C CONFORMACIÓN O UNIÓN DE MATERIAS PLÁSTICAS; CONFORMACIÓN DE MATERIALES EN ESTADO PLÁSTICO, NO PREVISTA EN OTRO LUGAR; POSTRATAMIENTO DE PRODUCTOS CONFORMADOS, p. ej. REPARACIÓN (fabricación de preformas B29B 11/00; fabricación de productos estratificados combinando capas previamente no unidas para convertirse en un producto cuyas capas permanecerán unidas B32B 37/00 - B32B 41/00). › B29C 43/00 Moldeo por compresión, es decir, aplicando una presión externa para hacer que fluya el material de moldeo; Aparatos a este efecto. › incorporando partes o capas preformadas, p. ej. moldeo por prensado alrededor de elementos insertos o sobre objetos a recubrir.
- B29C70/34 B29C […] › B29C 70/00 Conformación de materiales compuestos, es decir, materiales plásticos con refuerzos, cargas o partes preformadas, p. ej. inserciones. › conformación o impregnación por compresión.
- B29C70/46 B29C 70/00 […] › con moldes enfrentados, p. ej. para deformar compuestos de moldeo en láminas [SMC] o preimpregnados [prepegs].
PDF original: ES-2451766_T3.pdf
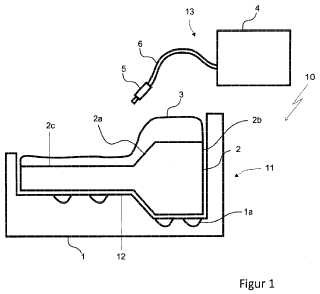
Fragmento de la descripción:
Procedimiento y dispositivo para la fabricación de componentes compuestos de fibra La presente invención se refiere a un procedimiento y a un dispositivo para la fabricación de componentes compuestos de fibra según el concepto de la reivindicación 1 o de la reivindicación 7.
Un procedimiento de este tipo y un dispositivo de este tipo se conocen, por ejemplo, del documento US-A2006/0220273.
Los materiales compuestos de fibra (FVW) presentan debido a su perfil de propiedades específico ventajas técnicas esenciales frente a materias de la competencia convencionales como, por ejemplo, acero o aluminio. Por su alta resistencia y rigidez a la vez que densidad relativamente baja se usan materiales compuestos ya en una gran 10 número de campos industriales como en la aviación y la astronáutica, en la construcción así como en el ámbito del deporte y del tiempo libre. Mediante aprovechamiento de las propiedades anisótropas de plásticos reforzados con fibras se pueden configurar piezas tales que se pueda minimizarla masa de estructuras o componentes. Adicionalmente los materiales compuestos de fibras se benefician de otras propiedades como muy buen comportamiento frente a fatiga así como una baja dilatación térmica. En los plásticos reforzados con fibras se 15 combinan entre sí las ventajas de al menos dos materiales. El material compuesto se compone de fibras (por ejemplo, fibras de vidrio o de carbono) como componentes de refuerzo, que están incrustadas de forma orientada o no orientada en un sistema de matriz de plástico. Las fibras se protegen de las influencias exteriores y se mantienen en su posición. El sistema de matriz se compone de polímeros con propiedades reticulantes bien duroplásticos o termoplásticos. En los sistemas de matriz duroplásticos usados particularmente se usan principalmente resinas de 20 poliéster (UP) insaturados y resinas epoxi (EP) . En lo sucesivo se designan los materiales de matriz duroplásticos o termopásticos en general como “resinas“. A pesar de las ventajas técnicas anteriormente citadas y del potencial de mercado resultante de estas aún no podrían aprovecharse industrialmente los materiales compuestos de fibras. Son motivos para ello la rentabilidad desventajosa de los plásticos reforzados con fibras comparativamente con los costes de materiales, fabricación y procedimiento así como un grado de automatización bajo en las piezas de alto rendimiento de materiales compuestos de fibra.
Para la fabricación de piezas en serie industriales se usa frecuentemente el procedimiento RTM. En el procedimiento RTM se intercalan productos de fibra semiacabados como, por ejemplo, tejidos o telas en un molde, el molde se cierra y a continuación se embebe el material de fibra con resina líquida. La resina se presiona al molde puntualmente con ayuda de presión (“inyección de resina”) desde un recipiente de materias primas que se encuentra fuera del molde. La resina en exceso se evacúa por orificios del molde a través de conductos. A continuación se endurece la resina con una reacción química. Para la reducción de fallas por burbujas de aire englobadas se puede proteger el proceso también mediante aplicación de vacío al molde.
Las piezas que se producen en el procedimiento RTM se caracterizan por altos contenidos en volumen de fibra, con lo que hasta ahora se tienen en cuenta principalmente en aplicaciones de altas prestaciones.
Para series a gran escala como en la industria del automóvil son insuficientes hasta ahora los tiempos de acabado del procedimiento RTM. Por un lado debido a la duración de la inyección de resina y del flujo de resina necesario por el material de fibra, por otro lado debido a los tiempos de reacción química necesarios para el endurecimiento de la resina.
Para la duración de la inyección de resina se puede usar la ecuación de Darcy que parte de los datos de corriente. A 40 continuación se puede calcular la corriente de resina con la siguiente fórmula:
en la que: Q –cantidad de resina; [Q] = m3/s kf–coeficiente de permeabilidad; [kf] = m/s
hA–altura del nivel del tubo vertical en la posición A; [hA] = m hB–altura del nivel del tubo vertical en la posición B; [hB] = m L –recorrido de flujo entre A y B; [L] = m A –superficie por la que se circula; [A] = m2
De esto resulta que el trayecto de flujo de la resina a presión constante e iguales unidades de tiempo, siempre será 50 más corto con la distancia creciente al punto de vertido.
La imprimación de fibras como componente determinante del tiempo en el proceso de consolidación debe discurrir tan rápido como sea posible para hacer posible tiempos de contacto cortos en la fabricación en serie. A partir de la fórmula se puede reconocer que se puede conseguir esto mediante la ampliación del gradiente de presión.
Por tanto se prueba en aplicación industrial del procedimiento RTM prensar mediante presión muy elevada y tan rápido como sea posible, la resina por el material de fibra. Para ello se incorporan los moldes RTM en prensas de altas prestaciones, para conseguir tiempos de acabado lo más cortos posibles. Esta forma de proceder tiene sin embargo varias desventajas:
• Las presiones aplicadas de más de 600000 kPa (6000 bar) se pueden alcanzar solo con prensas de altas prestaciones muy caras.
• Debido a las altas presiones de prensa se deben proyectar los moldes de RTM constructivamente también de forma especial para estas presiones elevadas.
• Los moldes deben ajustarse de forma precisa en las prensas, con lo que un cambio de herramienta rápido es problemático.
• Con las presiones elevadas se da el riesgo de que se desplace el material de fibra.
La permeabilidad del material de fibra en configuración del coeficiente de permeabilidad se predetermina con la combinación de matriz de fibra usada de la fibra compuesta y de la matriz de plásticos y se puede ajustar por tanto solo de forma condicionada. Por tanto se mantiene la viscosidad para influir en la velocidad de flujo. La viscosidad es fuertemente dependiente de la temperatura y baja con temperaturas crecientes hasta un límite que no se puede cruzar. Altas temperaturas significan sin embargo tiempos de calentamiento más prolongados del molde y dificultan el dimensionamiento de los útiles de prensa. A esta dificultad se añade que a partir del comienzo de la reacción química aumente de forma constante la viscosidad, con lo que es más difícil el flujo de resina.
El procedimiento con más perspectivas mantiene la minimización de las distancias de flujo. Para ello se desarrollaron distintos procedimientos como “RTM de compresión“ y “RTM avanzado“ , en los que por ejemplo se probó cerrar completamente el molde hasta una ranura de algunos milímetros hasta centímetros para dar a la resina la posibilidad de fluir sobre la superficie del producto de fibra semiacabado y distribuirse de este modo. A continuación se cierra el molde por completo. El sellado y limpieza del molde es problemático en este procedimiento de modo que esto no tiene que llevarse a cabo. El flujo de resina en estos procedimientos se realiza en el procedimiento RTM desde un lugar de inyección puntual de forma similar al vertido por inyección.
Hasta ahora se usaron en el procedimiento RTM como resinas principalmente resinas duroplásticas. Sin embargo, para la aplicación en la industria del automóvil, donde desempeñan un importante papel también los puntos de vista del reciclaje, los duroplásticos son problemáticos.
• Si las resinas se usan en relación con fibras de carbono, resulta una desventaja adicional, ya que la fabricación de fibras de carbono necesita un consumo de energía muy elevado. Con el estado de la técnica actual en la fabricación de vehículos es mayor el elevado gasto de energía en comparación con materiales metálicos que el del combustible ahorrado por el peso reducido durante la vida útil de un vehículo. La causa de ello se encuentra en la mayor cuota de reciclaje de materiales metálicos. El aluminio tiene, por ejemplo, en la construcción de vehículos una tasa de reciclaje de aproximadamente un 85 %.
• No hay procedimiento con el que se reciclen duroplásticos endurecidos y se puedan volver a usar. En plantas de experimentación se probó destruir las resinas mediante temperaturas muy altas en hornos de tambor. Este proceso es sin embargo muy costoso energéticamente y las fibras recicladas así obtenidas son de muy mala calidad y no se pueden procesar en nuevas mechas. Adicionalmente a este respecto no se pueden reciclar las resinas que suman aproximadamente 1/3 de material usado.
• Especialmente en... [Seguir leyendo]
Reivindicaciones:
1. Procedimiento para la fabricación de componentes compuestos de fibra mediante impregnación de un producto de fibra semiacabado (2) con una matriz de plásticos (3) , preferentemente una resina duroplástica o termoplástica, que se dispone sobre o bajo el producto de fibra semiacabado (2) , caracterizado porque la matriz de plásticos (3) se aplica en una cantidad de resina que se dosifica por zonas de superficie localmente diferentes, que se selecciona en función del respectivo espesor de pared en la región del componente compuesto de fibra que se va a fabricar.
2. Procedimiento según la reivindicación 1, caracterizado porque el producto de fibra semiacabado (2) se introduce en una mitad de molde (1) en un molde para prensado (11) con la matriz de plásticos (3) aplicada sobre su superficie
o el producto de fibra semiacabado (2) se introduce en una mitad de molde (1) de un molde para prensado (11) y luego se aplica la matriz de plásticos (3) sobre la superficie del producto de fibra semiacabado (2) .
3. Procedimiento según la reivindicación 1, caracterizado porque la matriz de plásticos (3) se introduce en una mitad de molde (1) de un molde para prensado (11) y luego el producto de fibra semiacabado (2) se coloca sobre la matriz de plásticos (3) en la mitad de molde (1) .
4. Procedimiento según al menos una de las reivindicaciones anteriores, caracterizado porque antes del cierre del molde para prensado (11) se cubre la superficie del producto de fibra semiacabado (2) o la superficie del fondo (12) de la mitad de molde (1) con la matriz de plásticos (3) .
5. Procedimiento según al menos una de las reivindicaciones anteriores, caracterizado porque con el cierre del molde para prensado (11) la matriz de plásticos (3) fluye transversalmente por el producto de fibra semiacabado (2) .
6. Procedimiento según al menos una de las reivindicaciones anteriores, caracterizado porque la viscosidad de la matriz de plásticos (3) se ajusta de forma que la matriz de plásticos (3) no fluye saliendo de la mitad de molde (1) o de la superficie del producto de fibra semiacabado (2) .
7. Dispositivo (10) para la fabricación de componentes compuestos de fibra mediante impregnación de un producto de fibra semiacabado (2) con una matriz de plásticos (3) , preferentemente de una resina duroplástica o termoplástica, con un molde para prensado (11) constituido por dos mitades de molde (1) , en donde el producto de fibra semiacabado (2) se puede introducir en una mitad de molde (1) y la matriz de plásticos (3) se puede alimentar desde un dispositivo de alimentación (13) , que está dirigido a la superficie del producto de fibra semiacabado (2) o a una superficie del fondo (12) de una mitad de molde del molde para prensado (11) , caracterizado porque el dispositivo de alimentación (13) se puede dosificar para la aplicación de la matriz de plásticos (3) en una cantidad de resina distinta localmente, dosificada por zonas de superficie, sobre o bajo el producto de fibra semiacabado (2) en función del espesor de pared respectivo del componente compuesto de fibra que se va a fabricar.
8. Dispositivo según la reivindicación 7, caracterizado porque el molde para prensado (11) está configurado de modo que con su cierre en la capa incorporada de matriz de plásticos (3) y de producto de fibra semiacabado (3) fluye transversalmente la matriz de plásticos (3) por el producto de fibra semiacabado (2) .
9. Dispositivo según la reivindicación 7, caracterizado porque el dispositivo de alimentación (13) presenta al menos un cabezal de pulverización (5) o bien un dispositivo de goteo, que preferentemente está dispuesto de forma relativamente móvil respecto al producto de fibra semiacabado (2) o respecto a una mitad de molde (1) .
10. Dispositivo según la reivindicación 9, caracterizado porque la matriz de plásticos (3) se puede alimentar al menos desde un depósito de reserva (4) .
11. Dispositivo según la reivindicación 9 ó 10, caracterizado porque la matriz de plásticos (3) se compone de dos o más componentes, que se mezclan en el cabezal de pulverización (5) o bien en los cabezales de pulverización (5) .
12. Dispositivo según al menos una de las reivindicaciones 9 a 11, caracterizado porque al menos una de las mitades de molde (1) está provista por la parte del fondo y preferentemente a ambos lados del producto de fibra semiacabado (2) de cámaras (1a) para recibir el exceso de matriz de plásticos (3) .
13. Dispositivo según la reivindicación 12, caracterizado porque las cámaras de matriz de plásticos (1a) presentan una o varias paredes (2a) oblicuas y/o porque las cámaras de matriz de plásticos (1a) presentan una o varias aberturas por las cuales se puede aplicar una presión negativa al molde para prensado (11) .
14. Dispositivo según al menos una de las reivindicaciones 12 a 13, caracterizado porque las cámaras de matriz de plásticos (1a) están provistas de eyectores (8) .
15. Dispositivo según una de las reivindicaciones 12 a 14, caracterizado porque las cámaras de matriz de plásticos (1a) están recubiertas de teflón.
Patentes similares o relacionadas:
Método para minimizar inconsistencias que aparecen sobre la superficie de un componente compuesto y una tira compuesta precurada, del 6 de Mayo de 2020, de THE BOEING COMPANY: Método para aplicar una tira compuesta precurada a un componente compuesto , comprendiendo la tira compuesta precurada una primera capa de material […]
Material de compuesto reforzado con fibra, del 6 de Mayo de 2020, de KABUSHIKI KAISHA TOYOTA JIDOSHOKKI: Un material de compuesto reforzado con fibra construido al impregnar una capa de paquete de fibras laminada formada al laminar una pluralidad de capas […]
Procedimiento de realización de preformas tridimensionales mediante el conformado de preformas iniciales con velos, del 26 de Febrero de 2020, de Coriolis Group: Procedimiento de realización de una preforma tridimensional que comprende - la realización de una preforma inicial que comprende varias capas superpuestas, […]
Procedimiento de fabricación de una cuaderna circundante de abertura para un fuselaje de aeronave, y cuaderna, del 1 de Enero de 2020, de AIRBUS OPERATIONS, S.L: Procedimiento de fabricación de una cuaderna circundante de abertura para un fuselaje de aeronave, comprendiendo el procedimiento las etapas de: […]
Composición de resina epoxídica, material preimpregnado, material compuesto reforzado con fibra de carbono y métodos de fabricación para los mismos, del 11 de Diciembre de 2019, de TOHO TENAX CO., LTD: Composición de resina epoxídica, que comprende al menos: componente [A]; de 3 a 20 partes en masa de componente [B] con respecto a 100 partes en masa del componente […]
Un método para fabricar un cajón multilarguero de una sola pieza de material compuesto dentro de un molde cerrado, del 11 de Diciembre de 2019, de Leonardo S.p.A: Un método para fabricar un cajón multilarguero de una sola pieza hecho de material compuesto para aviones, que comprende dos paneles que están unidos por […]
Procedimiento de conformado por estampado de un material compuesto termoplástico con refuerzo de fibras continuo, del 30 de Octubre de 2019, de DAHER AEROSPACE: Procedimiento para la realización de una pieza en forma de extrusión constituida por un material compuesto con refuerzo de fibras continuo, […]
Proceso de moldeo por compresión de un material compuesto con escamas cuasiisotrópicas, del 4 de Septiembre de 2019, de THE BOEING COMPANY: Un método para formar una pieza moldeada que tiene propiedades cuasiisotrópicas, comprendiendo el método: consolidar una primera capa formada […]