PROCEDIMIENTO DE FABRICACION DE PLACAS DE CIRCUITO IMPRESO CON MATERIALES BASE DE ALTA CONDUCTIBILIDAD TERMICA APTAS PARA LA INSERCION DE COMPONENTES NO SUPERFICIALES.
Procedimiento de fabricación de placas de circuito impreso con materiales base de alta conductibilidad térmica aptas para la inserción de componentes no superficiales.
El procedimiento comprende como etapas esenciales de la invención el troquelado de una placa metálica (1) para obtener taladros (2) numérica y posicionalmente adecuados para la inserción de los componentes no superficiales; la disposición de la placa base metálica (1) , sobre una plantilla de aspiración (3) provista de orificios de aspiración (4) dispuestos en correspondencia con los taladros (2); el descenso del cabezal de inyección (5) de una máquina de impresión convencional sobre la placa base metálica (1) e inyección de una resina aislante (7) a través de orificios de inyección (6), mientras se evacua el aire de los taladros (2) a través de los orificios de aspiración (4); y el troquelado del conjunto así obtenido para obtener un troquelado de inserción (12) de menor diámetro que el taladro (2), inicial, correspondiente
Tipo: Patente de Invención. Resumen de patente/invención. Número de Solicitud: P200703342.
Solicitante: EUROCIR S.A.
Nacionalidad solicitante: España.
Provincia: BARCELONA.
Inventor/es: LLONGUERAS AROLA,JUAN.
Fecha de Solicitud: 17 de Diciembre de 2007.
Fecha de Publicación: .
Fecha de Concesión: 4 de Enero de 2011.
Clasificación Internacional de Patentes:
- H05K3/44 ELECTRICIDAD. › H05 TECNICAS ELECTRICAS NO PREVISTAS EN OTRO LUGAR. › H05K CIRCUITOS IMPRESOS; ENCAPSULADOS O DETALLES DE LA CONSTRUCCIÓN DE APARATOS ELECTRICOS; FABRICACION DE CONJUNTOS DE COMPONENTES ELECTRICOS. › H05K 3/00 Aparatos o procedimientos para la fabricación de circuitos impresos. › Fabricación de circuitos con ánima metálica aislada.
Clasificación PCT:
- H05K3/44 H05K 3/00 […] › Fabricación de circuitos con ánima metálica aislada.
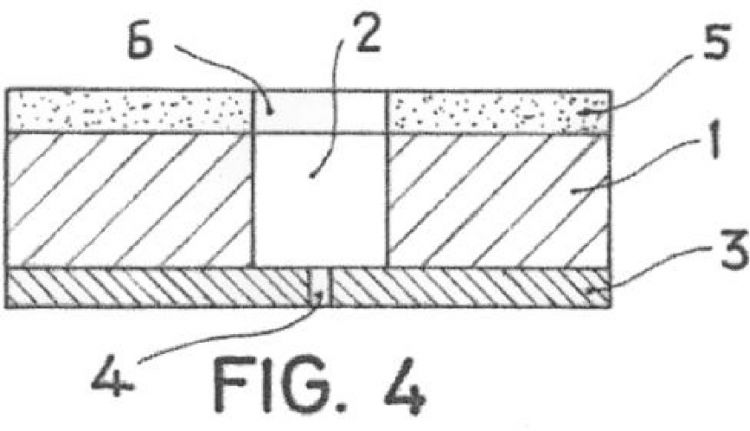
Fragmento de la descripción:
Procedimiento de fabricación de placas de circuito impreso con materiales base de alta conductibilidad térmica aptas para la inserción de componentes no superficiales.
La presente invención se refiere a la introducción de mejoras tecnológicas a fin de potenciar la funcionalidad y eficacia de las placas de circuito impreso fabricadas con materiales de alta conductividad térmica (IMS) basados en el uso de materiales metálicos, generalmente aluminio, como soporte físico de un laminado metálico, normalmente cobre, en una de sus caras.
Este tipo de materiales y placas de circuito impreso han sido desarrolladas como respuesta a la evolución de los requerimientos de la industria electrónica en relación a nuevas aplicaciones donde, debido al uso de componentes de alto poder calorífico, la temperatura de trabajo presenta un problema.
La placa de circuito impreso obtenida por el procedimiento de la invención es utilizable ventajosamente en un amplio espectro de aplicaciones donde la disipación térmica es un factor decisivo, por ejemplo:
Antecedentes de la invención
Debido al aumento del uso de componentes de alto poder calorífico, se ha hecho necesario el desarrollo de circuitos impresos basados en nuevas tecnologías que, mediante la utilización de nuevos procesos y nuevos materiales, permiten aportar las mejoras necesarias en cuanto a la disipación del calor generado por dichos componentes. Así, se han desarrollado nuevos materiales de alta conductividad térmica dando lugar a nuevas tecnologías y procesos.
Los nuevos materiales introducen como soporte físico de los circuitos impresos una base metálica, principalmente aluminio o cobre, sobre los que se dispone un laminado metálico generalmente cobre, donde se establecen las pistas conductoras que definen el diseño del circuito, dando lugar a las conexiones entre los diferentes componentes electrónicos convenientemente soldados a las mismas. A fin de proporcionar el necesario aislamiento eléctrico entre las pistas conductoras y la base metálica, se introduce entre ambos metales un material dieléctrico que garantiza el aislamiento eléctrico preciso con la mínima resistencia térmica.
De esta forma se evita el contacto eléctrico entre metales, ofreciendo a la vez la transferencia de calor necesaria que va a permitir a la base metálica absorber la temperatura acumulada en el circuito y facilitar su consiguiente disipación.
La estructura que se acaba de describir garantiza una elevada disipación térmica, pero plantea una importante limitación en cuanto al tipo de componentes electrónicos aplicables sobre este tipo de circuito impreso, siendo necesaria la utilización de componentes de montaje superficial (SMD) puesto que el ensamblado de cualquier tipo de componente que requiera ser insertado, conlleva la pérdida del aislamiento, por conexión eléctrica entre los metales de la base disipadora y las pistas conductoras a través del propio componente (patilla de inserción), o debido al propio proceso de soldadura.
En consecuencia, es un objetivo de la presente invención el disponer de una placa de circuito impreso que, manteniendo una elevada capacidad de disipación térmica, permita el montaje de componentes electrónicos de inserción, desarrollando el procedimiento necesario para su fabricación.
Descripción de la invención
Para alcanzar el objetivo propuesto se ha concebido una placa de circuito impreso en la que los taladros de la base metálica previstos para alojar las patillas de los componentes de inserción están convenientemente aislados. El procedimiento para fabricar la placa de circuito impreso, generando y manteniendo el aislamiento de los taladros a lo largo del mismo, es el objeto de la presente invención.
Para ello, se parte de la base metálica utilizada como disipador del circuito impreso, sobre la que se realiza un taladrado en las zonas en donde, a posteriori, sobre la placa de circuito impreso acabado, deberán insertarse los componentes electrónicos.
A continuación se procede al relleno de los taladros mecanizados mediante la aplicación de una resina de naturaleza aislante, de forma que el taladro quede totalmente inundado y relleno por esa resina. Esta operación es la más delicada, ya que es esencial el conseguir que la resina no desborde por la parte inferior del taladro y se adhiera a la superficie de la base metálica opuesta a las pistas conductoras.
Para conseguir esto, la resina de relleno, junto a su naturaleza aislante, debe ofrecer unas características en cuanto a sus propiedades físicas que permitan a la vez su fluidez para penetrar en el interior del taladro, junto con una tixotropía que garantice el recubrimiento total del interior del taladro. Sin embargo, esto no es suficiente para alcanzar el objetivo propuesto, por lo que deben tomarse medidas específicas respecto a los medios utilizados para la aplicación de la resina de relleno. En nuestro caso, se ha utilizado el sistema de aspiración utilizado para la impresión serigráfica de las pistas conductoras, modificado convenientemente.
Habitualmente, las máquinas de impresión utilizadas para la fabricación de circuitos impresos llevan un sistema de aspiración en el mismo conjunto de la máquina. Este sistema está dispuesto en el plato de impresión; es decir, en la superficie donde se coloca el material sobre el que se va a realizar la impresión. El objetivo es garantizar un correcto posicionamiento, planitud y fijación del material para poder realizar la impresión serigráfica con la necesaria precisión.
El sistema de aspiración se consigue mediante una bomba y una pluralidad de orificios de aspiración distribuidos de forma regular sobre el plato de impresión destinado a recibir el material a imprimir.
En el caso que nos atañe, al pretender recubrir de resina aislante un taladro en su totalidad, puede adaptarse el mismo sistema de aspiración para garantizar la "caída" de la resina en el interior del mismo. El problema a resolver es que, si se deposita la base metálica taladrada sobre una superficie plana, el taladro pasante se convierte en un taladro ciego y la presión que ejerce el aire ocluido en el mismo es superior a la presión de inyección de la resina de relleno, por lo que ésta no puede penetrar en el taladro de forma uniforme. La solución propuesta consiste en aspirar el aire ocluido a través de un pequeño orificio de aspiración dispuesto en la superficie sobre la que descansa la base metálica.
Sin embargo, la distribución habitual de los puntos de aspiración sobre el plato de la máquina de impresión es regular, puesto que su finalidad consiste en mantener fija una placa de material sin taladros. En consecuencia, es preciso prever una plantilla de aspiración, dispuesta por encima y separada del plato de la máquina, y provista de orificios de aspiración situados en correspondencia con los taladros de la base metálica que precisamos recubrir con la resina de relleno. De esta forma y con un correcto posicionamiento relativo entre la base metálica y la plantilla de aspiración, se garantiza que todos los taladros a rellenar de resina tienen la aspiración necesaria para evitar la presión que impide la "caída" de la misma.
El orificio de aspiración siempre será de diámetro considerablemente menor que el del taladro a rellenar, para evitar que la resina se introduzca entre la base metálica y la plantilla de aspiración. En el proceso de inyección de la resina de relleno, la intensidad de la aspiración junto con la presión de inyección de la resina son factores críticos en la obtención de la calidad deseada. La combinación de ambos parámetros con el diámetro del orificio de aspiración y las características físicas de la resina dependen del diseño del circuito a fabricar y deben ser ajustadas por el procedimiento de prueba y error.
Una vez rellenado con resina el taladro realizado sobre la base metálica, se procede a la aplicación del dieléctrico que permite la correcta adhesión del laminado metálico donde se realizará el posterior diseño de las pistas conductoras, garantizando a...
Reivindicaciones:
1. Procedimiento de fabricación de placas de circuito impreso con materiales base de alta conductividad térmica aptas para la inserción de componentes no superficiales, caracterizado por comprender las siguientes etapas:
2. Procedimiento de fabricación de placas de circuito impreso de acuerdo con la reivindicación 1, caracterizado porque la resina aislante (7) comprende un polímero del acrilato obtenido por exposición a la luz ultravioleta.
Patentes similares o relacionadas:
Método de fabricación de substrato base metálico y método de placa de circuito de fabricación, del 5 de Abril de 2017, de Denka Company Limited: Un método de fabricación de un sustrato a base de metal que tiene una capa adhesiva aislante (2b) y una lámina conductora laminada en […]
Procedimiento para fabricar unos montajes de circuitos usando unas composiciones de recubrimiento dieléctrico electrodepositables, del 6 de Marzo de 2013, de PPG INDUSTRIES OHIO, INC.: Un procedimiento para formar unas vías metalizadas que se extienden hasta un sustrato que comprende lassiguientes etapas: (I) formar un recubrimiento […]
Soporte de circuito, del 13 de Junio de 2012, de AB MIKROELEKTRONIK GESELLSCHAFT MIT BESCHRÄNKTER HAFTUNG: Soporte de circuito con una capa soporte metálica sobre la que se dispone al menos por zonas una capa
dieléctrica, poseyendo la capa dieléctrica una […]
Tarjeta de circuito impreso de una o múltiples capas con lengüetas de ruptura alargadas y procedimiento de fabricación de la misma, del 26 de Marzo de 2012, de PPG INDUSTRIES OHIO, INC.: Una tarjeta de circuito que comprende: una lámina conductora emparedada entre una capa superior aislante y una capa inferior aislante, definiendo […]
PLACA DE CIRCUITO IMPRESO DE DOBLE CARA, CON SUBSTRATO METALICO AISLADO Y CONEXIONES ENTRE CARAS POR ESPIGAS, Y METODO PARA SU PRODUCCION., del 16 de Agosto de 2004, de LEAR AUTOMOTIVE (EDDS) SPAIN S.L: Placa de circuito impreso de doble cara, con substrato metálico aislado y conexiones entre caras por espigas, y método para su producción. La placa comprende pares […]
PERFECCIONAMIENTOS EN PLACAS DE CIRCUITOS ELECTRICOS, del 16 de Abril de 1982, de NORTHERN TELECOM LIMITED: PLACA DE CIRCUITO ELECTRICO CON SUSTRATO METALICO ELECTRICAMENTE CONDUCTIVO, QUE LLEVA UN RECUBRIMIENTO DE UNA CAPA DE PORCELANA, AL MENOS SOBRE UNA DE SUS SUPERFICIES, Y UN […]
PROCEDIMIENTO PARA CREAR VÍAS PARA MONTAJES DE CIRCUITOS, del 26 de Septiembre de 2011, de PPG INDUSTRIES OHIO, INC.: Un procedimiento para exponer áreas predeterminadas de un sustrato que comprende las siguientes etapas: (a) aplicar una composición de recubrimiento curable por […]
MONTAJE DE CIRCUITO MULTICAPA Y PROCEDIMIENTO DE PREPARACION, del 1 de Abril de 2008, de PPG INDUSTRIES OHIO, INC.: Un procedimiento para fabricar un montaje de circuito multicapa que comprende las siguientes etapas: a) proporcionar un substrato al menos una de cuyas áreas comprende […]