METODO Y APARATO PARA LA FABRICACION DE ELEMENTOS OPTICOS DIFRACTIVOS.
La presente invención propone un método para la fabricación de elementos ópticos difractivos de una forma simple y económica.
Este método incluye los siguientes pasos: (a) situar un substrato transparente próximo a un material de partida, ambos ubicados en el interior de una cámara; (b) modular espacialmente una radiación proveniente de una fuente de radiación según un patrón de difracción requerido; (c) irradiar el substrato de forma que la radiación lo atraviese; (d) exponer el material de partida a la radiación transmitida a través del substrato, de modo que al incidir la radiación sobre el material de partida se produzca su evaporación o sublimación; (e) depositar la fase de vapor del material de partida sobre el substrato; y (f) registrar en el material depositado una estructura difractiva durante el proceso de deposición irradiando el material depositado de forma concurrente a través del substrato con la radiación modulada. El elemento fabricado presenta funcionalidad ópticadifractiva a causa de los cambios locales inducidos en su estructura, gobernados por la distribución de la intensidad luminosa empleada en el proceso de fabricación
Tipo: Patente de Invención. Resumen de patente/invención. Número de Solicitud: P200600446.
Solicitante: UNIVERSIDAD DE CADIZ.
Nacionalidad solicitante: España.
Provincia: CÁDIZ.
Inventor/es: GONZALEZ LEAL,JUAN MARIA, ANGEL RUIZ,JOSE ANDRES.
Fecha de Solicitud: 24 de Febrero de 2006.
Fecha de Publicación: .
Fecha de Concesión: 20 de Julio de 2010.
Clasificación Internacional de Patentes:
- C23C14/02 QUIMICA; METALURGIA. › C23 REVESTIMIENTO DE MATERIALES METALICOS; REVESTIMIENTO DE MATERIALES CON MATERIALES METALICOS; TRATAMIENTO QUIMICO DE LA SUPERFICIE; TRATAMIENTO DE DIFUSION DE MATERIALES METALICOS; REVESTIMIENTO POR EVAPORACION EN VACIO, POR PULVERIZACION CATODICA, POR IMPLANTACION DE IONES O POR DEPOSICION QUIMICA EN FASE VAPOR, EN GENERAL; MEDIOS PARA IMPEDIR LA CORROSION DE MATERIALES METALICOS, LAS INCRUSTACIONES, EN GENERAL. › C23C REVESTIMIENTO DE MATERIALES METALICOS; REVESTIMIENTO DE MATERIALES CON MATERIALES METALICOS; TRATAMIENTO DE MATERIALES METALICOS POR DIFUSION EN LA SUPERFICIE, POR CONVERSION QUIMICA O SUSTITUCION; REVESTIMIENTO POR EVAPORACION EN VACIO, POR PULVERIZACION CATODICA, POR IMPLANTACION DE IONES O POR DEPOSICION QUIMICA EN FASE VAPOR, EN GENERAL (fabricación de productos revestidos de metal por extrusión B21C 23/22; revestimiento metálico por unión de objetos con capas preexistentes, ver las clases apropiadas, p. ej. B21D 39/00, B23K; metalización del vidrio C03C; metalización de piedras artificiales, cerámicas o piedras naturales C04B 41/00; esmaltado o vidriado de metales C23D; tratamiento de superficies metálicas o revestimiento de metales mediante electrolisis o electroforesis C25D; crecimiento de monocristales C30B; mediante metalización de textiles D06M 11/83; decoración de textiles por metalización localizada D06Q 1/04). › C23C 14/00 Revestimiento por evaporación en vacío, pulverización catódica o implantación de iones del material que constituye el revestimiento. › Pretratamiento del material a revestir (C23C 14/04 tiene prioridad).
- C23C14/34C
Clasificación PCT:
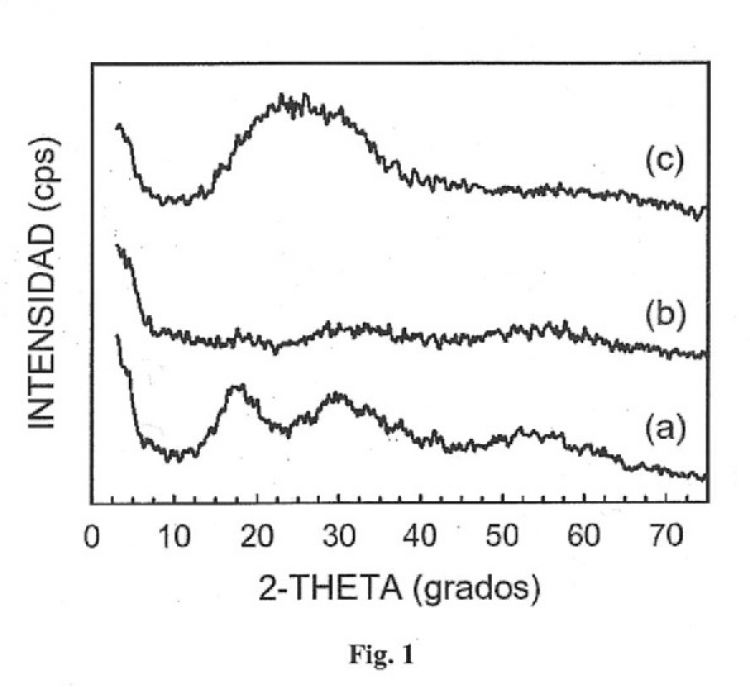
Fragmento de la descripción:
Método y aparato para la fabricación de elementos ópticos difractivos.
Referencias citadas
US 5,910,256 | 6/1999 | Tsunetomo et al. |
US 6,110,291 | 8/2000 | Haruta et al. |
US 6,452,698 B1 | 9/2002 | Vlcek et al. |
US 6,649,861 B2 | 11/2003 | Duignan |
US 6,766,764 B1 | 7/2004 | Chrisey et al. |
US 6,924,457 B2 | 8/2005 | Koyama et al. |
J. Teteris y M. Reinfelde, "Holographic recording in amorphous chalcogenide semiconductor thin films", Journal of Non-Crystalline Solids 326&327 (2003) 494.
A.V. Kolobov y Ka. Tanaka, en "Photoinduced Phenomena in Amorphous Chalcogenides: From Phenomenology to Nanoscale", Handbook of Advanced Electronic and Photonic Materials and Devices, Vol. 5, Hari Singh Nalwa, ed. (Academic Press, San Diego, 2001), p. 47.
A. Zakery, Y. Ruan, A. V. Rode, M. Samoc y B. Luther-Davies, "Low-loss waveguides in ultrafast laser-deposited As2S3 chalcogenide films", J. Opt. Soc. Am. B 20 (2003) 1844.
Campo de la invención
La presente invención se enmarca en el campo de los elementos ópticos con funcionalidad difractiva, y los métodos para fabricarlos.
Estado de la técnica
Los elementos ópticos tienen una gran importancia en todos aquellos campos tecnológicos en los que se necesita modular la distribución espacial de la luz. Ante tal demanda, se hace necesaria la optimización de las técnicas de fabricación de estructuras ópticas simples, así como la producción de estructuras ópticas con nuevas funcionalidades.
Existe una variedad de métodos para la fabricación de elementos ópticos difractivos, así como para el registro de estructuras difractivas en medios semiconductores, los cuales se basan en el procesado de un material soporte empleando técnicas fotolitográficas clásicas, u otras más modernas de ablación láser [US 5,910,256] [US 6,924,457 B2], o registro holográfico [US 6,452,698 B1] [Teteris y Reinfelde]. A diferencia de la presente invención, todos ellos comparten el carácter secuencial (no concurrente) del proceso, es decir, los métodos incluyen (a) la preparación previa del material soporte, y (b) su procesado posterior.
Por otro lado, por su relevancia con la invención aquí expuesta y reclamada, y al entender de los firmantes, son de destacar los métodos de deposición asistidos por luz, los cuales son ampliamente conocidos y usados en tecnologías planares [US 6,110,291]. En estas tecnologías se emplean láseres pulsados para la deposición de compuestos conductores, semiconductores y superconductores, destinados a integrar dispositivos ópticos y/o electrónicos, tanto activos como pasivos. Así, pueden encontrarse patentes reclamando derechos sobre la explotación industrial de un variado número de dispositivos planares basados en el método de deposición asistido por láser pulsado o PLD. Una búsqueda avanzada demuestra, además, que en todos los casos las invenciones evitan la interacción entre el haz láser y la fase de vapor, o pluma de plasma, generada a partir del material de partida, de forma que la configuración de los sistemas empleados consideran que el haz pulsado que produce la ablación del material de partida y la pluma del material eyectado son no colineales, y en ningún caso se considera actuación concurrente alguna sobre el depósito durante su crecimiento, vía irradiación luminosa.
Igualmente, por su relevancia con la presente invención, y con el fin de demostrar su actividad inventiva, citamos el único caso encontrado [US 6,766,764 B1] en el que un haz láser pulsado incide a través de una de las caras de un substrato transparente. En esta patente, el substrato transparente no está destinado a servir de soporte al depósito y permitir su fotomodelado estructural durante el crecimiento, sino que, por el contrario, soporta al material de partida. La invención citada considera que el substrato soporta una capa de un material que es fotoevaporable, la cual a su vez soporta a una capa del material destinado a ser depositado sobre un segundo substrato. La base de esta invención es que la evaporación fotoinducida del material de transferencia, a través del substrato transparente, produce la eyección del material de interés en una zona localizada del substrato receptor. Al igual que en los casos anteriores, en esta invención no se considera actuación concurrente alguna sobre el depósito durante su crecimiento, vía irradiación luminosa.
Finalmente, destacamos, de nuevo hasta donde ha alcanzado nuestra búsqueda, que en el único caso encontrado en el que se contempla la estructuración del depósito, ésta se realiza de forma secuencial, en dos pasos, dentro del sistema de fabricación, produciendo un depósito planar previo, vía irradiación luminosa, y la ablación posterior de éste, también mediante irradiación luminosa, que está condicionada a un cambio en la configuración del sistema que permite la exposición del material ya depositado al haz luminoso [US 6,649,861 B2]. En cualquier caso, el objeto de la invención (tecnologías planares) no es relevante para la actividad inventiva aquí expuesta.
Bases de la invención
La presente invención propone un método para la fabricación asistida por luz de depósitos de compuestos semiconductores que sirven de soporte a estructuras ópticas difractivas, que se sustenta en las siguientes evidencias físicas:
Sobre la base de las anteriores evidencias, los firmantes de la presente patente proponen un método sencillo, no obvio, para la fabricación de estructuras ópticas difractivas en medios semiconductores.
Un escenario preferido para la invención, no exclusivo en lo que se refiere al material usado, ni a la configuración del sistema de fabricación, es aquel en el que un haz láser continuo, con una longitud de onda de 532 nm, y con una distribución espacial de la intensidad luminosa con su fase siguiendo el patrón de las zonas de Fresnel, atraviesa perpendicularmente un substrato transparente de caras planoparalelas antes de alcanzar un material blanco situado a pocos milímetros del substrato. Tal modulación...
Reivindicaciones:
1. Método para la fabricación de elementos ópticos difractivos caracterizado porque comprende las siguientes fases operativas:
2. Método para la fabricación de elementos ópticos difractivos según reivindicación 1, caracterizado porque la vaporización o sublimación del material de partida (5) se realiza por medios lumínicos.
3. Método para la fabricación de elementos ópticos difractivos según reivindicaciones 1 y 2, caracterizado porque las radiaciones luminosas implicadas en el proceso son continuas o pulsadas.
4. Método para la fabricación de elementos ópticos difractivos según reivindicaciones 1 a 3, caracterizado porque las radiaciones luminosas implicadas en el proceso son monocromáticas o policromáticas.
5. Método para la fabricación de elementos ópticos difractivos según reivindicaciones 1 a 4, caracterizado porque las radiaciones luminosas implicadas en el proceso son coherentes o incoherentes.
6. Método para la fabricación de elementos ópticos difractivos según reivindicaciones 1 a 5, caracterizado porque el material de partida (5) es un lingote o una pastilla formada a partir del polvo prensado del material a depositar.
7. Método para la fabricación de elementos ópticos difractivos según reivindicaciones 1 a 6, caracterizado porque el material de partida (5) puede ser una mezcla homogénea o heterogénea, de aleaciones semiconductoras que contengan algún elemento calcógeno (O, S, Se y/o Te) y otros reactivos, que actúen como elementos tanto pasivos, como activos, para una determinada radiación luminosa.
8. Método para la fabricación de elementos ópticos difractivos según reivindicaciones 1 a 7, caracterizado porque el proceso se realiza a presión y atmósfera controladas.
9. Método para la fabricación de elementos ópticos difractivos según reivindicaciones 1 a 8, caracterizado porque la fase de vapor o plasma presente en el proceso procede de la evaporación y/o sublimación del material de partida (5) mediante la acción conjunta del calentamiento y la radiación luminosa.
10. Método para la fabricación de elementos ópticos difractivos según reivindicaciones 1 a 9, caracterizado porque la temperatura del substrato (6) es diferente de la temperatura ambiente.
11. Método para la fabricación de elementos ópticos difractivos según cualquiera de las reivindicaciones 1 a 10, caracterizado porque las caras enfrentadas del material de partida (5) y el substrato (6) son paralelas.
12. Elemento óptico difractivo obtenido mediante el método según cualquiera de las reivindicaciones 1 a 11.
13. Aparato para la fabricación de elementos ópticos difractivos, que comprende:
14. Aparato para la fabricación de elementos ópticos difractivos, según reivindicación 13, caracterizado porque dispone de un sistema de inyección de gases.
15. Aparato para la fabricación de elementos ópticos difractivos según reivindicación 13, caracterizado porque dispone de una fuente calefactora para el material de partida (5).
16. Aparato para la fabricación de elementos ópticos difractivos según reivindicación 13, caracterizado porque dispone de una fuente calefactora para el substrato (6).
17. Aparato para la fabricación de elementos ópticos difractivos según reivindicaciones 13 a 16, caracterizado porque dispone de fuentes de radiación luminosa adicionales para producir la eyección del material de partida (5).
18. Aparato para la fabricación de elementos ópticos difractivos según reivindicaciones 13 a 16, caracterizado porque dispone de fuentes de radiación luminosa adicionales para el registro de las estructuras difractivas.
19. Aparato para la fabricación de elementos ópticos difractivos según reivindicaciones 17 o 18, caracterizado porque las radiaciones luminosas presentes en el proceso son iguales en su coherencia, cromaticidad, y carácter temporal (pulsado o continuo).
20. Aparato para la fabricación de elementos ópticos difractivos según reivindicaciones 17 o 18, caracterizado porque las radiaciones luminosas presentes en el proceso son diferentes en su dirección de propagación, intensidad, coherencia, cromaticidad, o carácter temporal (pulsado o continuo).
Patentes similares o relacionadas:
Procedimiento de tratamiento de una chapa para reducir su ennegrecimiento o su deslustre durante su almacenamiento y la chapa tratada mediante dicho procedimiento, del 6 de Mayo de 2020, de Arcelormittal: Procedimiento de tratamiento de una tira metálica en desplazamiento que comprende las etapas según las cuales: - se suministra una tira de acero , revestida […]
Revestimiento duro y elemento recubierto con un revestimiento duro, del 15 de Enero de 2020, de OSG Corporation: Un revestimiento duro que recubre la superficie de un substrato , de manera que dicho revestimiento duro tiene un espesor total de 0,5-20 μm y comprende […]
Recubrimiento duro y miembro cubierto con recubrimiento duro, del 8 de Enero de 2020, de OSG Corporation: Un recubrimiento duro que cubre una superficie de un sustrato, en donde dicho recubrimiento duro tiene un grosor total de 0,5-20 μm e incluye una […]
Sustratos metalizados, del 20 de Noviembre de 2019, de AR Metallizing N.V: Un método de fabricación de un sustrato metalizado adecuado para retener, durante el lavado cáustico, la tinta retentiva aplicada al mismo, que comprende: […]
Herramienta de corte de metal con revestimiento multicapa, del 16 de Octubre de 2019, de WALTER AG: Una herramienta de corte de metal que comprende un cuerpo principal hecho de carburo cementado, cermet, cerámica, acero o acero de alta velocidad, […]
Método para aumentar la conductividad eléctrica de una superficie de una pieza de material compuesto, del 31 de Julio de 2019, de AIRBUS DEFENCE AND SPACE, S.A.U: Método para aumentar la conductividad eléctrica de una superficie de una pieza de material compuesto adecuado para una aeronave, la pieza de […]
Procedimiento para fabricar cuerpos multicapa metalizados a partir de policarbonatos especiales, del 15 de Mayo de 2019, de Covestro Deutschland AG: Procedimiento para fabricar cuerpos multicapa, en el que un material de sustrato, que contiene un copolicarbonato, que contiene al menos un elemento constructivo de bisfenol […]
Procedimiento de fabricación de una pieza fosfatable a partir de una lámina revestida con un revestimiento a base de aluminio y un revestimiento de cinc, del 3 de Abril de 2019, de Arcelormittal: Lámina de acero, para endurecimiento por prensado, revestida con un revestimiento a base de aluminio que comprende además un segundo revestimiento de cinc […]