PROCEDIMIENTO PARA CONFORMAR PLÁSTICO.
Procedimiento para conformar plástico en una forma predeterminada a partir de un material particulado de plástico que tiene un punto de fusión,
y un material de carga de plástico de espuma expansible activada por calor, comprendiendo dicho procedimiento: proporcionar moldes complementarios primero y segundo fabricados de un material seleccionado del grupo que consiste en aluminio, aleaciones de aluminio, kirksite, metales, cerámicas, cerametales, plásticos de alta temperatura, materiales termorresistentes conformables, estando conformados dichos moldes en una forma predeterminada con al menos una parte de cara en cada uno de dichos moldes complementarios primero y segundo para conferir una forma deseada; calentar dichos moldes primero y segundo al menos en sus partes de cara hasta una temperatura elevada de desde aproximadamente 100ºC hasta aproximadamente 865ºC de manera que el molde está a una temperatura superior al punto de fusión del material particulado de plástico; poner en contacto los moldes primero y segundo con el material particulado de plástico mientras el material particulado de plástico está al menos a temperatura ambiente durante un periodo de tiempo de permanencia de desde aproximadamente un segundo hasta aproximadamente 30 minutos, preseleccionándose dicho periodo de tiempo de permanencia para fundir el material particulado de plástico en una piel moldeada de un artículo de plástico que tiene una piel con un grosor deseado de desde aproximadamente 0,001 cm hasta aproximadamente 3,0 cm antes de detener el contacto con el material particulado de plástico; poner en contacto el material de carga de plástico de espuma expansible activada por calor con la piel moldeada sobre una parte de cara de al menos uno de los dos moldes calentados complementarios; aproximar las partes de cara complementarias de los moldes primero y segundo calentados mediante lo cual el calor residual de los moldes calentados activará el material de carga de plástico de espuma expansible activada por calor para hacer que se adhiera a las dos pieles para formar una intercalación compuesta de manera que se forma un artículo que tiene una superficie moldeada en ambos lados
Tipo: Patente Internacional (Tratado de Cooperación de Patentes). Resumen de patente/invención. Número de Solicitud: PCT/US2002/003298.
Solicitante: ENVIRONMENTAL RECYCLING TECHNOLOGIES PLC.
Nacionalidad solicitante: Reino Unido.
Dirección: REGENT HOUSE 316 BEULAH HILL LONDON SE19 3HF REINO UNIDO.
Inventor/es: DINELLO,Panfilo,M, LINARES,Miguel,A, CARGILL,Lynn,E, POINTER,Robin,L, HAINES,Paul,A.
Fecha de Publicación: .
Fecha Solicitud PCT: 5 de Febrero de 2002.
Clasificación PCT:
- B29C41/02 TECNICAS INDUSTRIALES DIVERSAS; TRANSPORTES. › B29 TRABAJO DE LAS MATERIAS PLASTICAS; TRABAJO DE SUSTANCIAS EN ESTADO PLASTICO EN GENERAL. › B29C CONFORMACIÓN O UNIÓN DE MATERIAS PLÁSTICAS; CONFORMACIÓN DE MATERIALES EN ESTADO PLÁSTICO, NO PREVISTA EN OTRO LUGAR; POSTRATAMIENTO DE PRODUCTOS CONFORMADOS, p. ej. REPARACIÓN (fabricación de preformas B29B 11/00; fabricación de productos estratificados combinando capas previamente no unidas para convertirse en un producto cuyas capas permanecerán unidas B32B 37/00 - B32B 41/00). › B29C 41/00 Conformación por revestimiento de un molde, núcleo u otro soporte, es decir, depositando material para moldear y desmoldear el objeto formado; Aparatos a este efecto (con presión de compactado B29C 43/00). › para fabricar objetos de longitud definida, es decir, de objetos separados.
- B29C41/18 B29C 41/00 […] › Moldeo en hueco, es decir, vertiendo el material a moldear en un molde hueco y decantado el exceso de material.
- B29C69/00 B29C […] › Combinaciones de técnicas de conformación no previstas en un solo grupo principal B29C 39/00 - B29C 67/00, p. ej. asociaciones de técnicas de moldeo y ensamblaje; Aparatos a este efecto.
- B29C70/46 B29C […] › B29C 70/00 Conformación de materiales compuestos, es decir, materiales plásticos con refuerzos, cargas o partes preformadas, p. ej. inserciones. › con moldes enfrentados, p. ej. para deformar compuestos de moldeo en láminas [SMC] o preimpregnados [prepegs].
Países PCT: Austria, Bélgica, Suiza, Alemania, Dinamarca, España, Francia, Reino Unido, Grecia, Italia, Liechtensein, Luxemburgo, Países Bajos, Suecia, Mónaco, Portugal, Irlanda, Eslovenia, Finlandia, Rumania, Chipre, Lituania, Letonia, Ex República Yugoslava de Macedonia, Albania.
PDF original: ES-2359047_T3.pdf
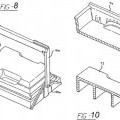
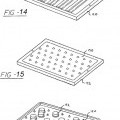
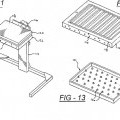
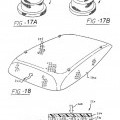
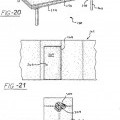
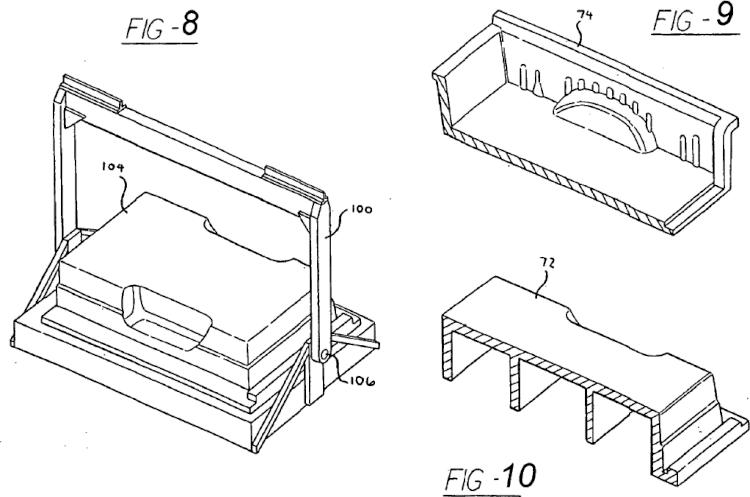
Fragmento de la descripción:
ANTECEDENTES DE LA INVENCIÓN
Esta solicitud de patente se refiere en general a la conformación de plástico y, más específicamente, se refiere a la conformación de plástico usando un molde calentado en contacto con partículas de plástico, ya estén en forma de polvo, resinas, gránulos o similares.
Aunque los métodos convencionales de conformación de plásticos son buenos, siempre hay espacio para mejoras. Existen muchas maneras de preparar plásticos, pero hay pocas maneras de preparar artículos de plástico que sean ligeros, resistentes, ignífugos, antibalas, aislantes, resistentes a impactos, así como que tengan una piel decorativa, texturizada o funcional, o preparados con plástico en una única capa sobre un molde calentado. Además, se enseñan pocas maneras en la técnica anterior de incrustar artículos dentro del plástico, con el fin o bien de reforzar el artículo o bien de cambiar sus propiedades. Además, existen incluso menos maneras conocidas en la técnica para incluir diversos materiales a lo largo del cuerpo de un artículo sin tener juntas, incluyendo estructuras de múltiples capas y diversos materiales dispersados a través de la superficie del artículo.
Aunque se conoce poner piezas de inserción en artículos de plástico moldeados por inyección, los presentes inventores no conocen ningún otro método a baja temperatura y baja presión que pueda suspender completamente una pieza de inserción, refuerzo, núcleo de espuma u otro material intercalado dentro del propio material de plástico. Sería ventajoso para tal método de conformación de plástico, así como para uno que utilice tales temperaturas relativamente bajas, presiones ambientales y la capacidad de usar moldes económicos y fácilmente mecanizados que duraran durante toda la producción de un artículo. Por supuesto, también sería ventajoso que un método de este tipo pudiera usar materiales reciclados.
Un nuevo método de conformación de plástico de este tipo podría usarse para una enorme multitud de aplicaciones, incluyendo, pero definitivamente sin limitarse a: componentes de vehículos industriales y de automóviles; paneles de alojamiento modulares; componentes de aviones; mobiliario de consumo e industrial tal como mesas, tableros de mesa y similares; puertas; ventanas; palés de manipulación de material y otros artículos; artículos de consumo; artículos industriales; aplicaciones marinas y cascos de barcos; moldes y componentes, incluyendo malecones, cascos de barcos y similares; aparatos médicos y otras aplicaciones; andamiajes y otros artículos de construcción de edificios; contenedores marinos; contenedores para trenes; ruedas compuestas para trenes, vehículos y contenedores de envío de alimentos incluyendo contenedores de alimentos de todos los tamaños y formas, por nombrar sólo algunas de las aplicaciones. Cada una de esas aplicaciones incluirá diversas formas de los artículos de plástico, incluyendo diversos materiales intercalados entre dos o más pieles con el fin de producir las propiedades de material deseadas.
Una de las mayores aplicaciones para la presente invención y tecnología es la creación de componentes de vehículos automóviles, incluyendo cajas de camioneta, componentes de techo, componentes de bajos de carrocería, y similares. En una industria que usaba tradicionalmente acero para sus componentes, los fabricantes de vehículos automóviles en Detroit y en otras partes buscan componentes de plástico ligeros para sus vehículos porque los nuevos reglamentos de ahorro de combustible más estrictos les están forzando a replantearse cómo fabrican vehículos. Políticos preocupados por el medio ambiente en diversos gobiernos, incluyendo en Washington, DC, están respaldando reglamentos que presionan fuertemente a la industria del automóvil a desarrollar vehículos más rentables en cuanto al combustible. Actualmente, los vehículos con mayores ventas en los Estados Unidos son los camiones de gran tonelaje y vehículos todoterreno, que tienen todos poco ahorro de combustible debido a su excesivo tamaño y pesos increíblemente altos. Para la mayoría de esos vehículos que pesan de 4.000 a 6.500 libras, las carreteras secundarias normales con un límite de peso total de una tonelada y media se agrietarán bajo un peso sostenido tal como el de esos vehículos.
La manera más fácil de lograr un vehículo más rentable en cuanto al combustible es reducir el peso. Una manera de reducir el peso es eliminar diversas partes de acero y sustituirlas por plástico ligero, resistente, tal como el objeto de la presente invención. La Corporate Average Fuel Economy, o “CAFE”, está presentando cada vez más demandas a la industria del automóvil debido a la creciente evidencia del efecto invernadero y otros problemas medioambientales provocados por la contaminación de vehículos. El cambio a componentes de plástico tiene enormes implicaciones para la industria del automóvil americana que ya está enfrentándose a beneficios escasos y ventas afectadas con la economía lenta. Los 3 grandes fabricantes de automóviles en los Estados Unidos dicen que normas de kilometraje más estrictas, particularmente para vehículos todoterreno, podrían costar a cada una de las empresas varios miles de millones de dólares a lo largo de los próximos años y dañarían gravemente a sus beneficios. En una respuesta para cumplir con las nuevas normas de la CAFE, algunos de los fabricantes de automóviles han prometido lanzar los nuevos vehículos híbridos altamente eficaces, que en parte son eléctricos y en parte funcionan con gasolina que tienen emisiones de contaminación muy inferiores.
Sin embargo, se reconoce ampliamente que la nueva tecnología híbrida por sí sola no será suficiente para cumplir con las normas de la CAFE que están en el horizonte. Los fabricantes de automóviles admiten que tendrán que comenzar a vender muchos más vehículos más ligeros, tales como vehículos todoterreno compactos, para cumplir las nuevas normas de ahorro de combustible. De los 11,4 millones de vehículos que vendieron los fabricantes de automóviles de Detroit el último año, el 59 por ciento fueron camiones o todoterrenos. Y de los diez camiones, vehículos todoterreno y monovolúmenes más vendidos de América, todos se quedan muy lejos de cumplir las normas de combustibles actuales, medido por sus millas por galón en ciudad y en autopista promedio combinadas. La norma actual de la CAFE para camiones es de 20,7 millas por galón, aunque la mayoría de los camiones y todoterrenos tienen eficacias de combustible de desde 13 mpg hasta 18 mpg.
Dado que la llegada de los vehículos híbridos eléctricos no son la única solución para los fabricantes de automóviles que cumplen con las normas de la CAFE, resulta claro que mejorar el consumo de combustible por milla de vehículos todoterreno y camiones es el objetivo fácil. Es un objetivo fácil porque los todoterrenos y los camiones son muy pesados y obtienen el peor ahorro de combustible de casi cualquier vehículo en la carretera. Por ejemplo, el todoterreno Excursion de la Ford Motor Company sólo alcanza 13 millas por galón para una conducción en ciudad. Las predicciones actuales por los fabricantes de automóviles de Detroit es que si las propuestas actuales elevan las normas para camiones a 24 mpg, con un aumento de 3,3 millas por galón desde las normas actuales de 20,7 mpg, esto haría que los fabricantes de automóviles pierdan ventas de más de 1 millón de camionetas grandes y todoterrenos. Y, como siempre, la industria advierte de que no serán los únicos afectados. Dicen que el precio añadido a vehículos para hacer que sean más rentables en cuanto al combustible costará a nuestra economía aproximadamente 300.000 puestos de trabajo. La solución convencional en Japón para aumentar el consumo de combustible por milla de vehículos es, en toda la industria, mejorar los coches pequeños y su consumo de combustible por milla, sacrificar potencia en caballos de vapor para obtener rentabilidad en cuanto al combustible, particularmente para vehículos todoterreno, estimular la investigación y el desarrollo de la rentabilidad en cuanto al combustible con el fin de desarrollar motores rentables en cuanto al combustible para coches y todoterrenos, así como frenar la producción de los todoterrenos más grandes que son los principales causantes de la reducción de la rentabilidad en cuanto al combustible promedio para camiones en Detroit.
Por tanto, tendría una gran ventaja reducir significativamente el peso de camionetas y vehículos todoterreno, estimulando así el ahorro de combustible y aliviando así el pago de multas por superar las normas de... [Seguir leyendo]
Reivindicaciones:
1. Procedimiento para conformar plástico en una forma predeterminada a partir de un material particulado de plástico que tiene un punto de fusión, y un material de carga de plástico de espuma expansible activada por calor, comprendiendo dicho procedimiento:
proporcionar moldes complementarios primero y segundo fabricados de un material seleccionado del grupo que consiste en aluminio, aleaciones de aluminio, kirksite, metales, cerámicas, cerametales, plásticos de alta temperatura, materiales termorresistentes conformables, estando conformados dichos moldes en una forma predeterminada con al menos una parte de cara en cada uno de dichos moldes complementarios primero y segundo para conferir una forma deseada;
calentar dichos moldes primero y segundo al menos en sus partes de cara hasta una temperatura elevada de desde aproximadamente 100ºC hasta aproximadamente 865ºC de manera que el molde está a una temperatura superior al punto de fusión del material particulado de plástico;
poner en contacto los moldes primero y segundo con el material particulado de plástico mientras el material particulado de plástico está al menos a temperatura ambiente durante un periodo de tiempo de permanencia de desde aproximadamente un segundo hasta aproximadamente 30 minutos, preseleccionándose dicho periodo de tiempo de permanencia para fundir el material particulado de plástico en una piel moldeada de un artículo de plástico que tiene una piel con un grosor deseado de desde aproximadamente 0,001 cm hasta aproximadamente 3,0 cm antes de detener el contacto con el material particulado de plástico;
poner en contacto el material de carga de plástico de espuma expansible activada por calor con la piel moldeada sobre una parte de cara de al menos uno de los dos moldes calentados complementarios;
aproximar las partes de cara complementarias de los moldes primero y segundo calentados mediante lo cual el calor residual de los moldes calentados activará el material de carga de plástico de espuma expansible activada por calor para hacer que se adhiera a las dos pieles para formar una intercalación compuesta de manera que se forma un artículo que tiene una superficie moldeada en ambos lados.
2. Procedimiento según la reivindicación 1, que comprende además una etapa de colocar una pieza de inserción entre dichos moldes primero y segundo antes de la etapa de aproximar los moldes primero y segundo y adherir las pieles juntas.
3. Procedimiento según la reivindicación 1 o la reivindicación 2, que comprende además una etapa de colocar un refuerzo entre dichos moldes primero y segundo antes de la etapa de aproximar los moldes primero y segundo y adherir las pieles juntas, de manera que el refuerzo se fija permanentemente en su sitio dentro de las pieles.
4. Procedimiento según cualquiera de las reivindicaciones anteriores, que comprende además enfriar al menos uno de los moldes primero y segundo para extraer el artículo resultante.
5. Procedimiento según cualquiera de las reivindicaciones anteriores, en el que dicho calentamiento de los moldes se logra calentando los moldes primero y segundo hasta una temperatura elevada de desde aproximadamente 160ºC hasta aproximadamente 220ºC.
6. Procedimiento según cualquiera de las reivindicaciones anteriores, en el que el periodo de tiempo de permanencia es de desde aproximadamente 3 hasta aproximadamente 10 minutos.
7. Procedimiento según cualquiera de las reivindicaciones anteriores, en el que la etapa de aproximar los moldes primero y segundo se logra manteniéndolos separados, poniéndolos a una separación predeterminada.
8. Procedimiento según cualquiera de las reivindicaciones 1 a 7, para producir una caja de plataforma de camioneta de plástico para instalar en el chasis de una camioneta, que comprende:
pieles de plástico macho y hembra separadas, estando ambas adaptadas para ajustarse sobre el chasis de la camioneta, estando formadas dichas pieles macho y hembra por un material poliolefínico, teniendo cada una un grosor de desde aproximadamente 0,001 cm hasta aproximadamente 1,0 cm;
el material de carga de plástico de espuma expandida intercalado entre dichas pieles macho y hembra, que tiene un grosor de desde aproximadamente 1,0 cm hasta aproximadamente 5,0 cm;
un refuerzo de malla de acero para las pieles macho y hembra, insertándose dicho refuerzo de acero entre los moldes macho y hembra, incrustándose en y rodeándose por el plástico expandido, de manera que la caja de camioneta está reforzada por la fuerza del acero; y
raíles de carga insertados en el molde hembra antes que el material de plástico expandido, estando ubicados dichos raíles de carga en el fondo de la caja de la camioneta resultante, estando rodeados por las pieles de plástico y el plástico expandido, de manera que la caja de plataforma de camioneta de plástico está adaptada para montarse fácilmente en un chasis de camioneta.
9. Procedimiento según cualquiera de las reivindicaciones 1 a 8, para producir un tablero de mesa industrial para montarse sobre patas de mesa, que comprende:
pieles de plástico macho y hembra separadas, estando adaptadas ambas para ajustarse sobre patas de mesa, estando formadas dichas pieles macho y hembra por un material poliolefínico, teniendo cada una un grosor de desde aproximadamente 0,001 cm hasta aproximadamente 1,0 cm;
el material de carga de plástico de espuma expandida intercalado entre dichas pieles macho y hembra, que tiene un grosor de desde aproximadamente 1,0 cm hasta aproximadamente 5,0 cm;
un refuerzo de malla de acero para las pieles macho y hembra, insertándose dicho refuerzo de acero entre los moldes macho y hembra, incrustándose en y rodeándose por el plástico expandido, de manera que el tablero de mesa está reforzado por la fuerza del acero.
10. Procedimiento según cualquiera de las reivindicaciones 1 a 8, para producir una puerta de cabina de avión de plástico, que comprende:
pieles de plástico macho y hembra separadas, estando ambas adaptadas para ajustarse en una cabina de avión, estando formadas dichas pieles macho y hembra por un material poliolefínico, teniendo cada una un grosor de desde aproximadamente 0,001 cm hasta aproximadamente 1,0 cm;
el material de carga de plástico de espuma expandida intercalado entre dichas pieles macho y hembra, que tiene un grosor de desde aproximadamente 1,0 cm hasta aproximadamente 5,0 cm;
una lámina de Kevlar® insertada entre las pieles de plástico macho y hembra y que está encapsulada y rodeada por el materiales de plástico expandido; y
un refuerzo de malla de acero conformado como los moldes para las pieles macho y hembra, insertándose dicho refuerzo de acero entre los moldes macho y hembra, incrustándose en y rodeándose por el plástico expandido, de manera que la puerta de la cabina de avión está reforzada por la fuerza del acero y se vuelve antibalas por la inclusión de la lámina de Kevlar®.
11. Procedimiento según cualquiera de las reivindicaciones 1 a 8, para producir un panel de alojamiento modular de plástico, que comprende:
pieles de plástico macho y hembra separadas, estando adaptadas ambas para ajustarse junto con otros paneles de alojamiento modulares, estando formadas dichas pieles macho y hembra por un material poliolefínico, teniendo cada una un grosor de desde aproximadamente 0,001 cm hasta aproximadamente 1,0 cm;
el material de carga de plástico de espuma expandida intercalado entre dichas pieles macho y hembra, que tiene un grosor de desde aproximadamente 1,0 cm hasta aproximadamente 5,0 cm; y
material térmicamente aislante insertado entre las pieles de plástico macho y hembra y que está encapsulado y rodeado por el material de plástico expandido.
12. Procedimiento según cualquiera de las reivindicaciones 1 a 8, para producir un palé de manipulación de material de plástico ligero, que comprende:
pieles de plástico macho y hembra separadas, estando ambas adaptadas para soportar cargas de material industrial, estando formadas dichas pieles macho y hembra por un material poliolefínico, teniendo cada una un grosor de desde aproximadamente 0,001 cm hasta aproximadamente 1,0 cm;
el material de carga de plástico de espuma expandida intercalado entre dichas pieles macho y hembra, que tiene un grosor de desde aproximadamente 1,0 cm hasta aproximadamente 5,0 cm; y
refuerzos cónicos de acero incrustados en y rodeados por el material de plástico expandido, estando ubicados dichos refuerzos entre los moldes macho y hembra, proporcionando así resistencia y durabilidad al palé.
Patentes similares o relacionadas:
Sistema de control avanzado y método para fabricar láminas y objetos de polietilentereftalato, del 20 de Mayo de 2020, de OCTAL SAOC FZC: Un método para fabricar objetos de PET que comprende: hacer reaccionar un primer precursor de PET y un segundo precursor de PET para producir un fundido de […]
MÉTODO Y MÁQUINA DE ENVASADO, del 21 de Noviembre de 2019, de Ulma Packaging Technological Center, S.Coop: Máquina y método de envasado que comprende disponer un conjunto de bandejas con al menos una hilera formada por una pluralidad de bandejas […]
Procedimiento para la fabricación de cuerpos huecos a partir de materia sintética termoplástica así como dispositivo para la realización del procedimiento, del 10 de Julio de 2019, de KAUTEX TEXTRON GMBH & CO. KG.: Procedimiento para la fabricación de cuerpos huecos a partir de materia sintética termoplástica, que comprende el moldeo de al menos dos […]
Método para fabricar una montura de gafas en acetato de celulosa multicolor, del 5 de Junio de 2019, de Wang, Daomin: Un método para fabricar una montura de gafas de acetato de celulosa multicolor, comprendiendo el método las siguientes etapas: S10, proporcionar […]
Aparato y procedimiento para el embalado en piel al vacío de un producto, del 3 de Junio de 2019, de CRYOVAC, INC.: Un aparato para embalar un producto dispuesto sobre un soporte , teniendo dicho soporte una pared de base y una pared lateral, comprendiendo dicho […]
Método para fabricar geles que tienen revestimientos exentos de pegajosidad permanentes, del 7 de Marzo de 2019, de APPLIED MEDICAL RESOURCES CORPORATION: Un método para preparar un gel exento de pegajosidad, que comprende las etapas de: proporcionar un molde; aplicar un polietileno de peso molecular […]
Método, dispositivo y un programa informático para fabricar un segmento de armazón preaislado, del 29 de Noviembre de 2017, de Mopac Systems International SA: Un método para fabricar un segmento de armazón preaislado para edificios de varias dimensiones, en donde el método comprende las etapas de: a) recibir un ensamblaje […]
Procedimiento y dispositivo para fabricar un material compuesto de fibra en forma de al menos una banda de fibra ancha impregnada con un polímero, del 6 de Septiembre de 2017, de THERMOPLAST COMPOSITE GMBH: Un procedimiento para fabricar un material compuesto de fibra en forma de al menos una banda de fibra ancha impregnada con un polímero, que […]