PROCEDIMIENTO DE IMPRESIÓN DIRECTA DESTINADO AL ESMALTADO Y DECORACIÓN.
Procedimiento de impresión directa destinado al esmaltado y decoración.
Procedimiento de impresión directa destinado al esmaltado y/o decoración sobre superficies en general (materiales cerámicos, vidrios o metales, entre otros), sometidas a un tratamiento térmico posterior a la impresión, que consiste en la transferencia, mediante el uso de un equipo de emisión de energía en forma de ondas electromagnéticas, preferentemente laser, de un esmalte/tinta desde un vehículo portador hasta la superficie de impresión sin que exista contacto entre el citado vehículo y la superficie de impresión. El tratamiento térmico, realizado a temperaturas superiores a 500 ºC, es necesario para que el esmalte/tinta se adhiera al substrato y se genere el efecto cerámico y/o cromático final.
Tipo: Patente de Invención. Resumen de patente/invención. Número de Solicitud: P201331076.
Solicitante: TORRECID, S.A..
Nacionalidad solicitante: España.
Inventor/es: CORTS RIPOLL,JUAN VICENTE, SANMIGUEL ROCHE,FRANCISCO, CONCEPCION HEYDORN,CARLOS, RUIZ VEGA,OSCAR.
Fecha de Publicación: .
Clasificación Internacional de Patentes:
- B41M1/00 TECNICAS INDUSTRIALES DIVERSAS; TRANSPORTES. › B41 IMPRENTA; MAQUINAS COMPONEDORAS DE LINEAS; MAQUINAS DE ESCRIBIR; SELLOS. › B41M PROCESOS DE IMPRESION, DE REPRODUCCION, DE MARCADO O COPIADO; IMPRESION EN COLOR (corrección de errores tipográficos B41J; procedimientos para aplicar imágenes transferencia o similares B44C 1/16; productos fluidos para corregir errores tipográficos C09D 10/00; impresión de textiles D06P). › Entintado o impresión con una forma de impresión.
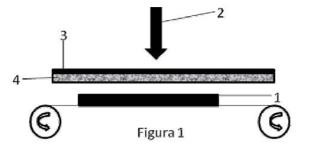
Fragmento de la descripción:
PROCEDIMIENTO DE IMPRESIÓN DIRECTA DESTINADO AL ESMALTADO Y
DECORACIÓN
Objeto de la invención
Procedimiento de impresión directa destinado al esmaltado y/o decoración sobre superficies en general, sometidas a un tratamiento térmico posterior a la impresión, que consiste en la transferencia, mediante el uso de un equipo de emisión de energía en forma de ondas electromagnéticas, de un esmalte/tinta desde un vehículo portador hasta la superficie de impresión.
El tratamiento térmico es necesario para que el esmalte/tinta se adhiera al substrato y se genere el efecto cerámico y/o cromático final. Para ello dicho tratamiento térmico se realiza a temperaturas superiores a 500 °C.
Descripción del estado de la técnica
En la actualidad, existen varios procesos de aplicación y diferentes composiciones para esmaltar y decorar superficies de cualquier tipo, tanto porosas como no porosas.
La técnica de inyección de tinta se viene empleando desde hace años en el sector cerámico y del vidrio para imprimir motivos decorativos, habiendo sustituido parcialmente a otras técnicas de decoración como la serigrafía, la huecografía, etc. Estas tintas para inyección se caracterizan por contener principalmente partículas de pigmentos inorgánicos que son las que aportan los colores y tonalidades necesarias y, opcionalmente, fritas que acompañan a los pigmentos cerámicos, tal y como se describe en las patentes US7976906, US6357868 y US5407474. Sin embargo, la tecnología de inyección de tinta, con el fin de asegurar una correcta impresión, requiere que el tamaño de las partículas que componen las tintas sea submicrométrico, siendo muy aconsejable que no supere los 500 nanómetros. Esto supone una limitación, ya que no es posible conseguir una amplia e intensa gama cromática y de efectos cerámicos con partículas tan pequeñas.
Hoy en día se pretende también aprovechar la tecnología digital para el esmaltado de baldosas cerámicas. Así la solicitud de patente española P201231722 describe una serie de esmaltes que se aplican mediante la tecnología de inyección digital con cabezales que trabajan en el sistema Drop-on-Demand (DOD), enfocados a esmaltar baldosas cerámicas de grandes formatos que requieren una cantidad baja de esmalte, por debajo de 200 g/m2. En este caso la tecnología digital de inyección,
además de las limitaciones ya indicadas asociadas al tamaño de partícula que restringen las composiciones a emplear, presenta el inconveniente de que no es posible depositar elevados gramajes. Estos dos aspectos limitan las posibilidades de acabado de los productos cerámicos, impidiendo que se pueda conseguir toda la gama y variedad actual, principalmente cuando se quiere conseguir productos con efectos cerámicos tales como metalizado, lustre o micas entre otros.
El término efecto cerámico en el contexto de la presente invención incluye cualquier efecto obtenido a partir de una mezcla de fritas o materias primas o pigmentos cerámicos o bien mezclas de ellos, que se somete a un tratamiento térmico bien sea para conseguir superficies completamente recubiertas o bien zonas seleccionadas. Asimismo incluye los conceptos conocidos por cualquier experto en la materia como esmaltado, vidriado, vitrificado o similares.
Si bien la patente ES2386267 y la solicitud de patente P201330061 describen tintas esmaltes digitales y esmaltes digitales respectivamente, que permiten aplicar gramajes elevados mediante tecnología digital de inyección, la calidad de imagen que se consigue no es lo suficientemente elevada para cumplir con los requerimientos que en este sentido se exigen en la mayoría de los productos del sector cerámico. En consecuencia, el ámbito de aplicación de ambas patentes queda restringido a productos cerámicos en los que no se requiere una elevada calidad de imagen del esmalte depositado o simplemente se necesita depositar una capa continua de esmalte en toda la superficie.
Por otra parte, la patente US2005/0212888 describe un procedimiento de impresión de una composición con la ayuda de un equipo de emisión de ondas electromagnéticas, preferentemente láser, que provoca un cambio en volumen y/o posición de la composición para impresión con la ayuda de cuerpos absorbedores de dicha radiación láser. Dicha patente US2005/0212888 divulga un procedimiento de impresión indirecto caracterizado por una doble transferencia de la composición de impresión, en primer lugar, desde el vehículo portador de dicha composición a un segundo vehículo portador, mediante un cambio de volumen y/o posición de la composición, y en segundo lugar, desde éste último vehículo portador a la superficie de impresión mediante contacto. Este procedimiento es inviable en el sector cerámico puesto que es habitual el uso de substratos con relieves más o menos pronunciados y por lo tanto, el esmaltado y/o decoración por contacto imposibilita acceder a las zonas profundas del relieve.
Además, la patente US2005/0212888 no describe en su procedimiento la distancia a la superficie de impresión, aspecto esencial en el esmaltado y la decoración de productos cerámicos y de vidrio, tanto para asegurar una buena calidad de imagen como para evitar el contacto entre el elemento impresor y el substrato en cuestión debido a las diferencias de espesor existentes entre diferentes piezas dentro del proceso productivo.
Para conseguir productos cerámicos y de vidrio de toda la gama cromática y efectos cerámicos que se utilizan en el sector, se requiere el uso de esmaltes/tintas con contenidos en sólidos por encima del 50% y con un tamaño de las partículas que presenten un D90 de hasta 40 micrómetros, lo que da lugar a viscosidades superiores a los 500 cPs. La patente US2005/0212888 divulga una composición de impresión caracterizada por una viscosidad comprendida entre 0.05 y 0.5 Pas, o lo que es lo mismo, entre 50 y 500 cPs, lo que impide realizar la totalidad de la gama cromática y efectos cerámicos demandados por el sector.
Por su parte la patente US2012/0164777 describe una composición para impresión por láser de pistas conductoras, especialmente destinada para la producción de células solares y que se somete a un tratamiento térmico posterior una vez depositada sobre el substrato, preferentemente semiconductor. Las fritas, materias primas y pigmentos empleados en el esmaltado y/o decoración de productos cerámicos y de vidrio no están contemplados en esta patente. De hecho la composición de frita adecuada para la aplicación que se describe en la patente US2012/0164777 comprende especialmente Óxido de Bismuto, Óxido de Silicio y/o Óxido de Teluro. En este sentido, una composición de frita basada únicamente en uno o varios de estos tres óxidos, no es adecuada para desarrollar las propiedades y acabados requeridos por el sector cerámico y del vidrio.
Finalmente, la patente US2012/0164777 recoge el uso de nanopartículas de Au, Ag, Pt, Pd, W, Ni, In, Sn02, TiC y Ti3N4 así como compuestos organometálicos, preferentemente de Al, Bi, Zn, V, B y Si, como absorbedores del láser. A este respecto indicar que si bien en el sector cerámico y del vidrio se emplean compuestos organometálicos en algunas composiciones especiales para conseguir efectos metálicos, tal y como se describe en la solicitud de patente española P201231372, éstas se caracterizan por emplear compuestos organometálicos de metales preciosos en vez de nanopartículas. Además, al margen de estas composiciones especiales que desarrollan el efecto metálico mencionado, las nanopartículas descritas en la patente US2012/0164777 no se pueden utilizar en
una composición habitual para esmaltado y/o decoración ya que no aportan ningún efecto cerámico o de color de acuerdo con los requerimientos del sector cerámico.
El objeto de la presente invención cumple las siguientes características:
Es un procedimiento de impresión destinado al esmaltado y/o decoración sobre superficies en general, sometidas a un tratamiento térmico posterior a la impresión, como puede ser el caso de materiales cerámicos, vidrio o metales, entre otros.
Consiste en la transferencia de un esmalte/tinta para impresión desde un vehículo portador hasta la superficie de impresión mediante el empleo de un equipo de emisión de energía en forma de ondas electromagnéticas, preferentemente láser.
Permite desarrollar una amplia e intensa gama cromática y de efectos cerámicos una vez sometidos los substratos esmaltados y/o decorados al tratamiento térmico correspondiente.
Permite depositar el gramaje (entre 0-500 g/m2) de esmalte/tinta necesario para conseguir los acabados requeridos industrialmente, manteniendo la calidad de imagen exigida por el usuario final.
...
Reivindicaciones:
1. Procedimiento de impresión directa destinado al esmaltado y/o decoración sobre superficies en general, sometidas a un tratamiento térmico posterior a la impresión, que consiste en la transferencia, mediante el uso de un láser como equipo de emisión de energía en forma de ondas electromagnéticas, de un esmalte/tinta desde un vehículo portador del elemento impresor hasta una superficie de impresión, caracterizado porque:
La distancia entre el elemento impresor y la superficie de impresión es mayor de 500 micrómetros y menor de 2,5 milímetros.
La viscosidad del esmalte/tinta está comprendida entre 500 cPs y 10000 cPs.
2. Procedimiento de impresión de acuerdo con la reivindicación 1
caracterizado porque las superficies de impresión son lisas.
3. Procedimiento de impresión de acuerdo con la reivindicación 1
caracterizado porque las superficies de impresión presentan relieve.
4. Procedimiento de impresión de acuerdo con la reivindicación 1
caracterizado porque las superficies son de materiales cerámicos y/o de vidrio.
5. Procedimiento de impresión de acuerdo con las reivindicaciones anteriores caracterizado porque deposita el esmalte/tinta en zonas seleccionadas de la superficie de impresión
6. Procedimiento de impresión de acuerdo con las reivindicaciones 1 a 4 caracterizado porque deposita el esmalte/tinta en toda la superficie de impresión.
7. Procedimiento de impresión de acuerdo con las reivindicaciones anteriores caracterizado porque deposita gramajes de esmalte/tinta de hasta 500 g/m2
8. Procedimiento de impresión de acuerdo con las reivindicaciones anteriores caracterizado porque las superficies se encuentran fijas y es el sistema comprendido por el equipo de emisión de energía-vehículo portador- esmalte/tinta el que se desplaza en un sistema de coordenadas X-Y-Z.
9. Procedimiento de impresión de acuerdo con las reivindicaciones 1 a 7 caracterizado porque el sistema equipo de emisión de energía -vehículo portador-esmalte/tínta se encuentra fijo y son las superficies las que se
desplazan mediante un sistema de transporte en un sistema de coordenadas X-Y-Z.
10. Procedimiento de impresión de acuerdo con las reivindicaciones 1 a 7 caracterizado porque el sistema equipo de emisión de energía-vehículo portador-esmalte/tinta_se desplaza en los ejes Y-Z de un sistema de coordenadas X-Y-Z y las superficies se desplazan mediante un sistema de transporte en el eje X de un sistema de coordenadas X-Y-Z.
11. Procedimiento de impresión de acuerdo con la reivindicación anterior caracterizado porque se realiza a una velocidad del sistema de transporte de las superficies inferior a 70 m/min.
12. Procedimiento de impresión de acuerdo con la reivindicación 1,
caracterizado porque el láser emite la luz láser a una determinada longitud de onda.
13. Procedimiento de impresión de acuerdo con la reivindicación 1,
caracterizado porque el láser emite la luz láser en un intervalo de longitudes de onda.
14. Procedimiento de impresión de acuerdo con la reivindicación 1
caracterizado porque el esmalte/tinta comprende:
Al menos una parte sólida a temperatura ambiente, responsable de conferir el efecto cerámico y/o cromático correspondiente, que comprende al menos una sustancia sólida absorbedora de la energía emitida por el equipo de emisión de energía, que es seleccionada entre óxidos sencillos, óxidos mixtos, estructuras cristalinas de cualquier estructura o composición química, carbono, carburos, nitruros o bien mezcla de ellos, para transformar dicha energía en calor y provocar el cambio de volumen y/o posición del esmalte/tinta, y
Al menos una parte líquida a temperatura ambiente.
15. Procedimiento de impresión de acuerdo con la reivindicación anterior, caracterizado porque la parte sólida se encuentra en el esmalte/tinta en un porcentaje en peso entre el 50% y el 80%.
16. Procedimiento de impresión de acuerdo con la reivindicación 14, caracterizado porque la parte sólida del esmalte/tinta se caracteriza por tener un tamaño de partícula D90 que puede llegar a los 40 micrómetros.
17. Procedimiento de impresión de acuerdo con la reivindicación 14, caracterizado porque la sustancia absorbedora se encuentra en el esmalte/tinta en un porcentaje no superior al 10%.
18. Procedimiento de impresión de acuerdo con la reivindicación 14,
caracterizado porque la parte líquida se encuentra en el esmalte/tinta en un porcentaje en peso entre el 20% y el 50%.
19. Procedimiento de impresión de acuerdo con la reivindicación 14,
caracterizado porque la parte líquida comprende al menos un agente ligante que se encuentra en el esmalte/tinta en un porcentaje en peso no superior al 10%.
20. Procedimiento de impresión de acuerdo con la reivindicación 14,
caracterizado porque la parte líquida comprende al menos un agente dispersante que se encuentra en el esmalte/tinta en un porcentaje en peso no superior al 5%.
21. Procedimiento de impresión de acuerdo con la reivindicación 14,
caracterizado porque la parte líquida comprende al menos un agente antisedimentante tixotropante que se encuentra en el esmalte/tinta en un porcentaje en peso no superior al 2%.
22. Procedimiento de impresión de acuerdo con la reivindicación 14,
caracterizado porque la parte líquida comprende al menos un agente humectante que se encuentra en el esmalte/tinta en un porcentaje en peso no superior al 2%.
23. Procedimiento de impresión de acuerdo con la reivindicación 14,
caracterizado porque la parte líquida comprende al menos un agente nivelante que se encuentra en el esmalte/tinta en un porcentaje en peso no superior al 2%.
24. Procedimiento de impresión de acuerdo con la reivindicación 14,
caracterizado porque la parte líquida comprende al menos un agente antiespumente que se encuentra en el esmalte/tinta en un porcentaje en peso no superior al 2%.
25. Procedimiento de impresión de acuerdo con la reivindicación 14,
caracterizado porque la parte líquida comprende al menos un esmalte/tinta que contiene conservantes en un porcentaje en peso no superior al 2%.
Patentes similares o relacionadas:
PROCEDIMIENTO PARA LA IMPRESIÓN DE IMÁGENES SOBRE CANTOS DE LIBROS, del 2 de Marzo de 2020, de LIBROPIEL, S.L: Procedimiento para imprimir imágenes en los cantos de los libros en el que se prepara con apertura e igualado del poro y aplicación de mordiente el canto […]
Artículo con motivos curvos formados por copos de pigmento alineados, del 12 de Marzo de 2019, de Viavi Solutions Inc: Un método de formación de un artículo, en donde el método comprende: proporcionar un substrato y un recubrimiento que comprende copos de pigmento que […]
Procedimiento para la producción de impresiones decorativas de igual calidad, independientemente del procedimiento de impresión utilizado, y un dispositivo para la ejecución de este procedimiento, del 27 de Febrero de 2019, de FLOORING TECHNOLOGIES LTD.: Procedimiento para la producción de impresiones decorativas de igual calidad sobre al menos dos materiales de soporte que comprende las etapas a) proporcionar al menos […]
Dispersión de cera de base acuosa que comprende una cera hidrocarbonada y un dialquiléter para el revestimiento de productos de papel, del 13 de Febrero de 2019, de SASOL WAX GMBH: Una dispersión de cera que comprende a) una fase dispersa que comprende: - al menos una cera hidrocarbonada y - al menos un dialquiléter; […]
Procedimiento para la generación de impresiones decorativas de idéntica calidad independientemente del procedimiento de impresión usado y un dispositivo para la realización de este procedimiento, del 30 de Diciembre de 2015, de FLOORING TECHNOLOGIES LTD.: Procedimiento para la generación de impresiones decorativas de idéntica calidad sobre al menos dos materiales de soporte, que comprende […]
Procedimiento para la generación de impresiones decorativas con igual calidad independientemente del procedimiento de impresión usado y un dispositivo para la realización de este procedimiento, del 25 de Noviembre de 2015, de FLOORING TECHNOLOGIES LTD.: Procedimiento para la generación de impresiones decorativas con igual calidad sobre al menos dos materiales de soporte, que comprende las etapas a) […]
Procedimiento para la fabricación de al menos un dispositivo de aparato doméstico, y dispositivo de aparato doméstico, del 1 de Octubre de 2014, de BSH ELECTRODOMESTICOS ESPAÑA S.A.: Procedimiento para la fabricación de al menos un dispositivo de aparato doméstico, y dispositivo de aparato doméstico.
Con el fin de poner a disposición un procedimiento genérico […]
COMPOSICIÓN PARA EL SECTOR DE LAS ARTES GRÁFICAS, PROCEDIMIENTO Y UTILIZACIÓN DE LA MISMA, del 19 de Enero de 2012, de PRIMUS RAIN, S. L: Composición para el sector de las artes gráficas, procedimiento y utilización de la misma. La presente invención se refiere a composiciones […]