Chasis de vehículo.
Método de fabricación de un chasis para un vehículo, que comprende preparar una pluralidad de secciones tubulares (12,
14, 16, 18, 20, 22), cortar las secciones en longitudes determinadas, perfilar los extremos de las secciones, combar las secciones según sea necesario, unir los extremos de al menos algunas de las secciones directamente a otras secciones para crear la estructura de armazón (10) del chasis, formar una lámina (50) a partir de una pluralidad de secciones unidas mediante un método permitiendo una tolerancia posicional con una forma cóncava compuesta para actuar como el suelo (54) de un zona de carga posterior y los respaldos de asiento (58), los cojines de asiento (60) y los reposapiés (62) para los pasajeros dentro del vehículo, colocar la lámina (50) sobre el armazón (10), teniendo la lámina (50) recesos curvados (70, 72, 74, 76) formados para que se correspondan con secciones tubulares en el armazón (10), de manera que cada receso se curve alrededor de un tubo del armazón (10) para unirse al mismo y unir la lámina (50) al armazón (10) para reforzar el armazón (10) y para formar una única estructura de soporte de carga en la cual se pueden instalar el motor, el tren de rodaje, los embellecedores internos y externos, etc.
Tipo: Patente Europea. Resumen de patente/invención. Número de Solicitud: E12197701.
Solicitante: Gordon Murray Design Limited.
Nacionalidad solicitante: Reino Unido.
Dirección: Wharfside Broadford Park Shalford, Surrey GU4 8EP REINO UNIDO.
Inventor/es: MURRAY,IAN GORDON.
Fecha de Publicación: .
Clasificación Internacional de Patentes:
- B62D23/00 TECNICAS INDUSTRIALES DIVERSAS; TRANSPORTES. › B62 VEHICULOS TERRESTRES QUE SE DESPLAZAN DE OTRO MODO QUE POR RAILES. › B62D VEHICULOS DE MOTOR; REMOLQUES (dirección o guiado de máquinas o instrumentos agrícolas según un recorrido determinado A01B 69/00; ruedas, ruedecillas pivotantes, mejora de la adherencia de ruedas B60B; neumáticos para vehículos, inflado de neumáticos, cambio o reparación de neumáticos B60C; conexiones entre vehículos de un mismo tren o de un conjunto similar B60D; vehículos raíl-carretera, vehículos anfibios o transformables B60F; disposiciones de suspensión B60G; calefacción, refrigeración, ventilación u otros dispositivos de tratamiento del aire B60H; ventanas, parabrisas, techos descapotables, puertas o dispositivos similares, cubiertas de protección para vehículos fuera de servicio B60J; disposiciones de conjuntos de propulsión, accionamientos auxiliares, transmisiones, disposición de instrumentos o tableros de a bordo B60K; equipo eléctrico o propulsión de vehículos de tracción eléctrica B60L; alimentación de energía eléctrica para vehículos de tracción eléctrica B60M; disposiciones para pasajeros no previstas en otro lugar B60N; vehículos adaptados al transporte de cargas o para llevar cargas u objetos especiales B60P; adaptación de los dispositivos de señalización o de iluminación, su montaje o soporte, circuitos a este efecto, para vehículos en general B60Q; vehículos, equipos o partes de vehículos, no previstos en otro lugar B60R; servicio,limpieza, reparación, elevación o maniobra, no previstos en otro lugar B60S; frenos, sistemas de control de frenos o partes de estos sistemas B60T; vehículos de colchón de aire B60V; ciclos de motor, sus accesorios B62J, B62K; ensayo de vehículos G01M). › Chasis y carrocería combinados, es decir, construcción monocasco (subconjuntos de carrocería B62D 25/00).
PDF original: ES-2546498_T3.pdf
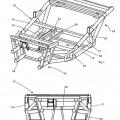
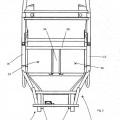
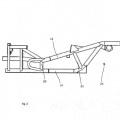
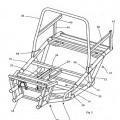
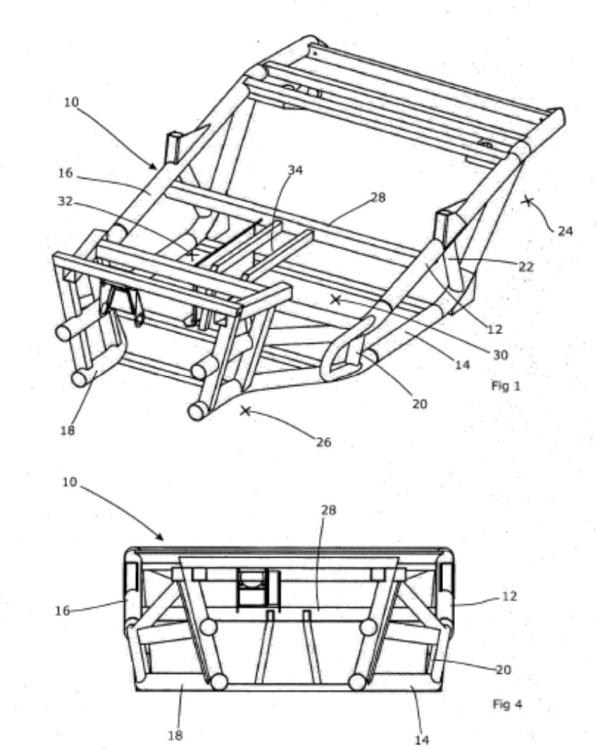
Fragmento de la descripción:
Chasis de vehículo Campo de la invención La presente invención proporciona un chasis de vehículo.
Técnica anterior No hace falta decir que el chasis es un componente crucial de un vehículo. Es el núcleo del vehículo en el que se sostienen todos los demás componentes ya sea directa o indirectamente. En última instancia es responsable de absorber y transmitir las fuerzas experimentadas por el vehículo; su rigidez determina (en gran medida) el comportamiento de conducción del vehículo y su comportamiento de deformación es un factor principal en la seguridad estructural a los choques del vehículo.
También es el componente individual más grande del vehículo y (además del motor, en algunos casos) el más pesado. Esto significa que los recursos necesarios para construir el chasis y su peso final serán una parte significativa de la huella ambiental del ciclo de vida del vehículo.
Por tanto, la reducción de peso y de las necesidades materiales del chasis darán lugar a beneficios en el rendimiento, economía de combustible y huella ambiental del vehículo. Sin embargo, esto se debe realizar sin afectar de manera adversa a la rigidez necesaria del chasis.
Históricamente, se ha construido un chasis de tipo escalera simple utilizando dos secciones longitudinales unidas por elementos transversales que (en efecto) proporcionaban los "peldaños" de la escalera. Las secciones longitudinales necesitaban ser de un calibre muy grande con el fin de proporcionar la resistencia necesaria. Esto dio como resultado un chasis que, por los estándares de hoy en día, es muy pesado e insuficientemente rígido en torsión. Sin embargo, fue muy fácil de producir en serie.
El uso de secciones longitudinales adicionales unidas por múltiples elementos transversales o particiones crea lo que normalmente se conoce como un chasis de bastidor tubular. Para vehículos fabricados en serie, sin embargo, éstas han sido descartadas ya que el tiempo requerido para la fabricación suele ser demasiado prolongado.
Aunque la rigidez de tal estructura es mayor que la de un chasis de tipo escalera, para proporcionar suficiente rigidez generalmente es necesario añadir elementos diagonales adicionales a la estructura de modo que se eviten los momentos de torsión y que todas las fuerzas sean absorbidas mediante compresión o tensión longitudinal de un elemento del bastidor. Una estructura de este tipo normalmente se conoce como bastidor espacial y es mucho más compleja para la producción en serie.
El documento US 3550948 describe una estructura de carrocería unitaria para un automóvil que consiste en unas secciones de carrocería superior e inferior formadas de material compuesto que juntas definen un espacio sustancialmente estanco y alojan un bastidor tubular de metal. Las secciones de carrocería superior e inferior se unen y se sellan entre sí y con el bastidor de manera que las partes de metal quedan completamente cubiertas y juntas definen la carrocería de vehículo además del bastidor de chasis. El documento US 3550948 describe en detalle un método para hacer un bastidor de chasis para un vehículo, comprendiendo el método preparar una pluralidad de secciones tubulares, combar las secciones según sea necesario, unir los extremos de al menos algunas de las secciones directamente a otras secciones para crear la estructura del armazón del bastidor de chasis de vehículo, formar una lámina con una forma cóncava compuesta para actuar como los respaldos de asiento, cojines de asiento y reposapiés para pasajeros dentro del vehículo, colocar la lámina sobre el armazón, teniendo la lámina recesos formados para que se correspondan con secciones tubulares en el armazón y para formar una única estructura de soporte de carga en la cual se pueden instalar el motor, el tren de rodaje, los embellecedores internos y externos, etc.
Por tanto, los vehículos modernos producidos en gran cantidad utilizan universalmente un chasis de acero prensado. El chasis se forma mediante una operación de prensado/estampado que implica una o más etapas. Esto produce un chasis de acero que tiene la rigidez necesaria, aunque es muy pesado y requiere mecanizado considerable para su producción. Las partes necesarias restantes de la estructura del vehículo se sueldan después por puntos al conjunto.
Las herramientas necesarias para formar el chasis son físicamente grandes, y por tanto se deben alojar en una instalación grande. Por tanto, un importante coste de material (con la huella ambiental consecuente) está asociado al chasis, a las herramientas y a la instalación, imponiendo el peso del chasis resultante una huella ambiental sustancial permanente como resultado del consecuente gasto energético del vehículo, e imponiendo el tamaño grande de la instalación una consecuente huella ambiental permanente en lo que se refiere a su calentamiento, su
iluminación, su mantenimiento, etcétera. La necesaria soldadura por puntos implica un consumo de energía significativo.
Resumen de la invención La presente invención pretende proporcionar un chasis .para un vehículo que combina la rigidez necesaria con suficiente velocidad de fabricación para permitir la producción en serie, aunque con una huella ambiental que es muy pequeña comparada con aquella de un chasis de acero prensado convencional.
Un chasis de acero prensado no puede cumplir estos requisitos por las razones expuestas anteriormente.
Un chasis de bastidor tubular convencional no puede cumplir el requisito que se refiere a la velocidad de fabricación. Para la producción en serie, buscamos un requisito de tiempo total del orden de 120 segundos por chasis; un chasis de bastidor tubular actual requiere la atención continua de un operario experimentado y por consiguiente es un proceso que lleva mucho tiempo.
Por tanto, proponemos un método para fabricar un chasis para un vehículo, que comprende preparar una pluralidad de secciones tubulares, cortar las secciones en longitudes determinadas, perfilar los extremos de las secciones, combar las secciones según sea necesario, unir los extremos de al menos algunas de las secciones directamente a otras secciones para crear la estructura de armazón del chasis, formar una lámina a partir de una pluralidad de secciones unidas mediante un método permitiendo una tolerancia posicional con una forma cóncava compuesta para actuar como el suelo de un zona de carga posterior y los respaldos de asiento, los cojines de asiento y los reposapiés para los pasajeros dentro del vehículo, colocar la lámina en el armazón, teniendo la lámina recesos curvados formados para que se correspondan con secciones tubulares en el armazón, de manera que cada receso se curve alrededor de un tubo del armazón para unirse al mismo y unir la lámina al armazón para reforzar el armazón y para formar una única estructura de soporte de carga en la cual se puedan instalar el motor, el tren de rodaje, los embellecedores internos y externos, etc. Con el uso de métodos de fabricación modernos, tales como corte con láser, combado CNC y soldadura controlada por ordenador, el tiempo de producción requerido para tal chasis se puede mantener dentro de nuestro objetivo de 120 segundos. Mientras tanto, la lámina unida al armazón actúa como una parte estructural del chasis y añade rigidez a la estructura como un todo que le permite alcanzar el grado de rigidez requerido.
Tal chasis también tiene una huella de carbono excepcionalmente baja. El uso de secciones tubulares (preferiblemente huecas) , que pueden ser de un material metálico tal como acero o aluminio, es mucho más económico en el uso de material que un chasis de acero prensado y se puede formar con herramientas significativamente más pequeñas que por consiguiente tienen (en sí mismas) una huella más pequeña. El espacio físico requerido para fabricar tal chasis también es mucho más pequeño, permitiendo una reducción de los costes de calentamiento, iluminación, fabricación y otros costes y de la huella de carbono de la instalación en la que se fabrican.
La lámina puede ser metálica, tal como aluminio o panal de aluminio, o puede ser un material compuesto. Varios materiales compuestos son adecuados, incluidos material compuesto de fibra de carbono, material compuesto de fibra de Kevlar, material compuesto de fibra de vidrio, y otros materiales compuestos tales como materiales compuestos de matriz de metal. Un material compuesto especialmente adecuado es uno que comprende un núcleo de un material y un revestimiento de un segundo material; núcleos adecuados incluyen materiales a base de papel y revestimientos adecuados incluyen materiales de plásticos reforzados con fibra.
La lámina no es plana debido a que esto permitirá un mayor grado de rigidez... [Seguir leyendo]
Reivindicaciones:
1. Método de fabricación de un chasis para un vehículo, que comprende preparar una pluralidad de secciones tubulares (12, 14, 16, 18, 20, 22) , cortar las secciones en longitudes determinadas, perfilar los extremos de las secciones, combar las secciones según sea necesario, unir los extremos de al menos algunas de las secciones directamente a otras secciones para crear la estructura de armazón (10) del chasis, formar una lámina (50) a partir de una pluralidad de secciones unidas mediante un método permitiendo una tolerancia posicional con una forma cóncava compuesta para actuar como el suelo (54) de un zona de carga posterior y los respaldos de asiento (58) , los cojines de asiento (60) y los reposapiés (62) para los pasajeros dentro del vehículo, colocar la lámina (50) sobre el armazón (10) , teniendo la lámina (50) recesos curvados (70, 72, 74, 76) formados para que se correspondan con secciones tubulares en el armazón (10) , de manera que cada receso se curve alrededor de un tubo del armazón (10) para unirse al mismo y unir la lámina (50) al armazón (10) para reforzar el armazón (10) y para formar una única estructura de soporte de carga en la cual se pueden instalar el motor, el tren de rodaje, los embellecedores internos y externos, etc.
2. Método de acuerdo con la reivindicación 1, en el que los tubos (12, 14, 16, 18, 20, 22) se cortan mediante un proceso de corte con láser.
3. Método de acuerdo con la reivindicación 1 o 2, en el que los extremos de tubo se cortan y perfilan en la misma etapa.
4. Método de acuerdo con cualquiera de las reivindicaciones 1 a 3, en el que los tubos se comban mediante un proceso de combado CNC.
5. Método de acuerdo con cualquiera de las reivindicaciones 1 a 4, en el que los extremos de tubo se unen mediante un proceso de soldadura automático.
6. Método de acuerdo con cualquiera de las reivindicaciones anteriores, que comprende además, posteriormente, las etapas de empaquetar una pluralidad de armazones (10) en un único contenedor de envío, transportar el contenedor desde el emplazamiento en el que se llevan a cabo las etapas a un segundo emplazamiento, y además montar el vehículo en el segundo emplazamiento.
7. Chasis para un vehículo fabricado de acuerdo con el método de cualquiera de las reivindicaciones anteriores, en el que la lámina (50) es de un material compuesto que comprende un núcleo de un material y un revestimiento de un segundo material.
8. Chasis de acuerdo con la reivindicación 7, en el que las secciones tubulares (12, 14, 16, 18, 20, 22) son huecas.
9. Chasis de acuerdo con la reivindicación 7 u 8, en el que el núcleo es papel.
10. Chasis de acuerdo con la reivindicación 7 u 8, en el que el núcleo es un material termoplástico.
11. Chasis de acuerdo con cualquiera de las reivindicaciones 7 a 10, en el que el revestimiento es un material plástico reforzado con fibras.
12. Chasis de acuerdo con cualquiera de las reivindicaciones 7 a 11, que comprende además un motor montado en el mismo.
13. Chasis de acuerdo con la reivindicación 12, en el que el motor está montado en una cara inferior del chasis.
14. Vehículo que comprende un chasis de acuerdo con cualquiera de las reivindicaciones 7 a 13.
Patentes similares o relacionadas:
Automóvil eléctrico con estructura modular preensamblada, del 8 de Abril de 2020, de Interactive Fully Electrical Vehicles S.r.l: Un vehículo de motor accionado eléctricamente, que comprende: - un bastidor principal ; - un conjunto de eje delantero ; y - un conjunto de eje trasero […]
Vehículo de motor eléctrico para el transporte de mercancías constituido por un cuerpo rotomoldeado sostenido por un bastidor tubular modular, del 25 de Marzo de 2020, de Interactive Fully Electrical Vehicles S.r.l: Un vehículo de motor accionado eléctricamente para el transporte de mercancías, que comprende:
- un bastidor principal ;
- un conjunto de eje delantero […]
Procedimientos de fabricación de un elemento tridimensional de refuerzo interior de un marco de puerta de un vehículo, para fabricar un marco de puerta de un vehículo y para fabricar una estructura de refuerzo para un vehículo, del 4 de Marzo de 2020, de Arcelormittal: Procedimiento de fabricación de un elemento tridimensional de refuerzo interior de un marco de puerta de un vehículo , comprendiendo dicho elemento de refuerzo […]
Nodos formados modulares para chasis de vehículo y sus métodos de uso, del 13 de Noviembre de 2019, de Divergent Technologies, Inc: Un miembro de junta que comprende: un núcleo central ; dos o más puertos de aceptación que se extienden lejos del […]
Chasis de vehículo eléctrico y vehículo eléctrico que usa el mismo, del 13 de Noviembre de 2019, de Guangdong Hua'chan Research Institute of Intelligent Transportation System Co., Ltd: Un chasis de vehículo eléctrico que comprende un sistema de bastidor , un sistema de amortiguación de motor de dirección montado en el sistema de bastidor […]
Vehículo eléctrico con chasis segmentado y chasis auxiliar en estructura reticular, del 14 de Agosto de 2019, de Interactive Fully Electrical Vehicles S.r.l: Un automóvil de propulsión eléctrica , del tipo que comprende: - un chasis principal , - una unidad de eje delantero , - una unidad de eje trasero […]
Procedimientos para fabricar un elemento tridimensional de refuerzo interior de un marco de puerta de un vehículo, para fabricar un marco de puerta de vehículo y para fabricar una estructura de refuerzo para un vehículo, del 12 de Junio de 2019, de Arcelormittal: Procedimiento para fabricar un elemento tridimensional de refuerzo interior de un marco de puerta de un vehículo , dicho elemento de refuerzo […]
Estructuras de chasis de vehículo, del 20 de Marzo de 2019, de Gordon Murray Design Limited: Un chasis de vehículo que comprende un armazón de elementos metálicos de sección tubular interconectados y una pluralidad de paneles de material compuesto […]