PROCEDIMIENTO DE SOLDADURA Y SISTEMA DE SOLDADURA CON DETERMINACION DE LA POSICION DE SOPLETE PARA SOLDAR.
Procedimiento de soldadura usándose un soplete para soldar (10) cuya posición es determinada,
siendo emitida una señal (34) por un emisor (33), que es recibida por al menos un sensor (36) integrado en el soplete para soldar (10) o que está asignado a éste, siendo transmitidos los datos de medición recibidos a una unidad de valoración (40) y determinando la unidad de valoración (40) valores para la posición del soplete para soldar (10) en el espacio tridimensional, caracterizado porque además de los valores de las posiciones 3D se almacenan los parámetros de soldadura correspondientes para el proceso de soldadura realizado con el soplete para soldar (10) y se utilizan como valores de referencia para procesos de soldadura posteriores similares
Tipo: Patente Internacional (Tratado de Cooperación de Patentes). Resumen de patente/invención. Número de Solicitud: PCT/AT2006/000204.
Solicitante: FRONIUS INTERNATIONAL GMBH.
Nacionalidad solicitante: Austria.
Dirección: VORCHDORFER STRASSE 40,4643 PETTENBACH.
Inventor/es: WITTMANN, MANFRED, STOGER,MARKUS, LEKO,TOMAS.
Fecha de Publicación: .
Fecha Concesión Europea: 6 de Enero de 2010.
Clasificación Internacional de Patentes:
- B23K9/095D
- B23K9/127G4
Clasificación PCT:
- B23K9/127 TECNICAS INDUSTRIALES DIVERSAS; TRANSPORTES. › B23 MAQUINAS-HERRAMIENTAS; TRABAJO DE METALES NO PREVISTO EN OTRO LUGAR. › B23K SOLDADURA SIN FUSION O DESOLDEO; SOLDADURA; REVESTIMIENTO O CHAPADO POR SOLDADURA O SOLDADURA SIN FUSION; CORTE POR CALENTAMIENTO LOCALIZADO, p. ej. CORTE CON SOPLETE; TRABAJO POR RAYOS LASER (fabricación de productos revestidos de metal por extrusión de metales B21C 23/22; realización de guarniciones o recubrimientos por moldeo B22D 19/08; moldeo por inmersión B22D 23/04; fabricación de capas compuestas por sinterización de polvos metálicos B22F 7/00; disposiciones sobre las máquinas para copiar o controlar B23Q; recubrimiento de metales o recubrimiento de materiales con metales, no previsto en otro lugar C23C; quemadores F23D). › B23K 9/00 Soldadura o corte por arco voltaico (soldadura eléctrica por escoria B23K 25/00; transformadores de soldadura H01F; generadores de soldadura H02K). › Medios para seguir líneas durante la soldadura o el corte por arco (copiado en general B23Q 35/00).
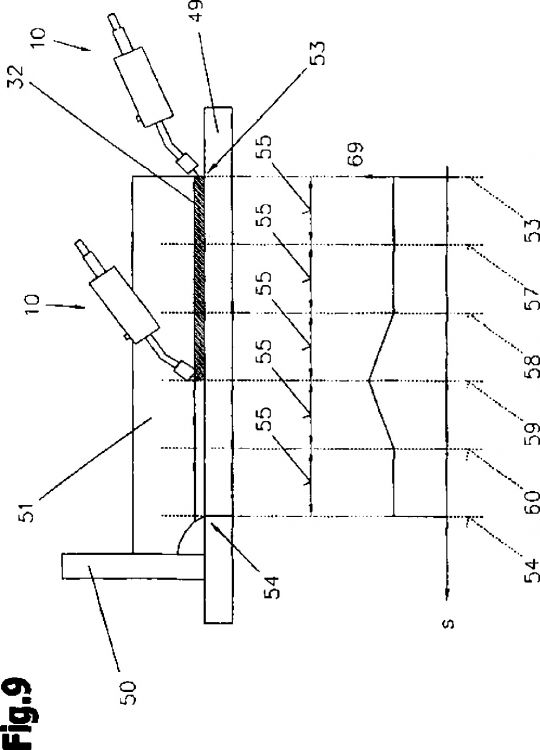
Fragmento de la descripción:
Procedimiento de soldadura y sistema de soldadura con determinación de la posición del soplete para soldar.
La invención se refiere a un procedimiento de soldadura usándose un soplete para soldar cuya posición es determinada, según el preámbulo de la reivindicación 1.
La invención se refiere también a un sistema de soldadura con un aparato de soldadura y un soplete para soldar que puede conectarse mediante un paquete de mangueras, estando previsto un dispositivo para la determinación de la posición del soplete para soldar, según el preámbulo de la reivindicación 21 o de la reivindicación 31.
Los sistemas de determinación de posición conocidos para sopletes para soldar están basados en sistemas ópticos o magnéticos, detectándose una junta o un cordón de soldadura o pudiendo vigilarse la extensión de la soldadura a lo largo de la junta. Aquí, las unidades de emisión y recepción del sistema de determinación de la posición están fijados de forma externa en el soplete para soldar, por ejemplo en la tobera de gas, o forman un aparato o componente independiente. Por lo tanto, puede detectarse, por ejemplo, una costura de garganta o una costura a tope, usándose durante el proceso de soldadura el sistema de determinación de la posición para conseguir un cordón de soldadura a lo largo de la junta. Los sistemas de determinación de la posición de este tipo se conocen, por ejemplo, por los documentos JP 63 286276 AA y JP 58 038672 AA.
El documento US 2005/055127 A1 se refiere a una máquina para realizar procesos de mecanizado en una pieza de trabajo y a un procedimiento para el control de éstos, usándose un sistema de determinación de la posición que incluye un láser para corregir errores en la posición del cabezal de mecanizado debido a movimientos incontrolados de la máquina o de la pieza de trabajo. Para ello, un sistema de determinación de la posición por láser compara la relación espacial real entre la pieza de trabajo y la herramienta y la compara con valores predeterminados almacenados.
Aquí es un conveniente que en los sistemas de este tipo no es posible la determinación de una posición en el espacio, es decir, de la posición del soplete manual para soldar en el espacio tridimensional, sino solamente el seguimiento de una junta.
El objetivo de la invención es crear un procedimiento de soldadura y un sistema de soldadura para un soplete para soldar, en particular un soplete manual para soldar, con el que se permita una determinación de la posición del soplete para soldar en el espacio tridimensional.
Respecto al procedimiento, el objetivo de la invención se consigue porque, además de los valores de las posiciones tridimensionales, se almacenan los parámetros de soldadura correspondientes para el proceso de soldadura realizado con el soplete para soldar usándose para procesos de soldadura posteriores similares como valores de referencia. Aquí es ventajoso que los valores determinados durante la determinación de la posición de las posiciones 3D del soplete para soldar y el cordón de soldadura que resulta de ello pueden usarse para aplicaciones o piezas de trabajo posteriores similares. De este modo se permite de forma sencilla un control de calidad, una reproducibilidad del cordón de soldadura, así como una asignación de parámetros de soldadura a un sistema de soplete para soldar, en particular un sistema de soplete manual para soldar. Gracias a la medida de almacenar además de los valores de las posiciones 3D los parámetros de soldadura correspondientes para el proceso de soldadura realizado con el soplete para soldar se consigue que durante la unión por soldadura de piezas de trabajo similares, en la que deben realizarse distintos cordones de soldadura con parámetros de soldadura preferiblemente diferentes, los parámetros de soldadura se ajustan o modifican automáticamente durante la soldadura en función de la posición, por lo que se acelera una producción en serie y pueden excluirse ajustes incorrectos del soldador.
Es ventajoso almacenar los datos de medición recibidos y/o los valores determinados de la posición 3D del soplete para soldar.
Los valores para la posición 3D del soplete para soldar se determinan preferiblemente en momentos que pueden fijarse a libre elección, en particular al principio y al final de un proceso de soldadura realizado con el soplete para soldar.
Es ventajoso si además de los valores de las posiciones 3D se almacenan los tiempos correspondientes de un proceso de soldadura realizado con el soplete para soldar. De este modo se consigue un control de calidad y se determina, por ejemplo, la velocidad de soldadura y se documenta el momento de la soldadura.
Gracias a la medida de usar los tiempos que corresponden a los valores de las posiciones 3D para procesos de soldadura posteriores, similares como valores de referencia, se consigue de forma ventajosa que independientemente del soldador se obtenga un resultado de soldadura aproximadamente igual para cordones de soldadura similares de distintas piezas de trabajo similares.
También es ventajoso si los valores determinados para las posiciones 3D y los tiempos se comparan con los valores de referencia depositados corrigiéndose dado el caso los parámetros de soldadura y almacenándose las modificaciones realizadas. También de este modo se garantiza una calidad constante del cordón de soldadura.
Gracias a la medida de que se detectan los datos relevantes para la calidad de soldadura, en particular la velocidad de soldadura, el orden de los cordones de soldadura, y el ángulo de inclinación del soplete para soldar durante el proceso de soldadura y se almacenan preferiblemente en el dispositivo de control, se consigue una documentación y un control de calidad automáticos. Por lo tanto, también puede realizarse fácilmente una trazabilidad en un momento posterior.
Según otra característica de la invención, los valores almacenados para las posiciones 3D del soplete para soldar de al menos un proceso de soldadura realizado, dado el caso los valores de referencia y las modificaciones almacenadas se leen para el análisis, preferiblemente para fines de aprendizaje del aparato de soldadura, en particular mediante un equipo externo. De este modo se permite una formación más rápida y más eficiente de personal nuevo.
También es ventajoso si los parámetros de soldadura de un proceso de soldadura se ajustan automáticamente con ayuda de los valores determinados para la posición 3D. Por lo tanto, pueden realizarse varios cordones de soldadura con distintos procedimientos de soldadura, en particular procedimientos de soldadura estándar y por arco pulsado en el marco de un proceso de soldadura, realizándose los ajustes o conmutaciones necesarios en el aparato de soldadura automáticamente con ayuda de una posición determinada del soplete para soldar durante el proceso de soldadura.
Los valores determinados para la posición 3D del soplete para soldar se comparan preferiblemente con valores de referencia y se indican acústica u ópticamente al usuario del soplete para soldar. Por lo tanto, puede predeterminarse e indicarse al usuario del aparato de soldadura con ayuda de señales de aviso o representaciones gráficas la posición correcta del soplete para soldar para el proceso de soldadura correspondiente o durante un proceso de soldadura determinado. Gracias a esta retroalimentación (feedback), el soldador puede reaccionar inmediatamente a errores en la soldadura, por ejemplo un empeoramiento del aspecto del cordón y evitarlo o reducirlo.
A partir de los valores determinados para la posición 3D en función del tiempo puede determinarse la velocidad de soldadura y compararse con valores predeterminados para la velocidad de soldadura e indicarse acústica u ópticamente al usuario del soplete para soldar. De este modo se consigue que el soldador pueda reaccionar gracias a la retroalimentación inmediatamente a errores en la soldadura, por ejemplo una penetración insuficiente debido a una velocidad de soldadura excesiva. Además, se consigue de forma ventajosa que pueda detectarse sin dispositivos auxiliares externos la velocidad de soldadura no limitándose, por lo tanto, la libertad de movimiento del soplete para soldar.
Si el inicio de un proceso de soldadura sólo se permite en posiciones 3D predeterminadas, pueden evitarse cordones de soldadura en lugares incorrectos, Además, puede conseguirse de este modo que pueda determinarse un orden predefinido para los cordones de soldadura, que el soldador debe realizar posteriormente para cada pieza de trabajo. Por lo...
Reivindicaciones:
1. Procedimiento de soldadura usándose un soplete para soldar (10) cuya posición es determinada, siendo emitida una señal (34) por un emisor (33), que es recibida por al menos un sensor (36) integrado en el soplete para soldar (10) o que está asignado a éste, siendo transmitidos los datos de medición recibidos a una unidad de valoración (40) y determinando la unidad de valoración (40) valores para la posición del soplete para soldar (10) en el espacio tridimensional, caracterizado porque además de los valores de las posiciones 3D se almacenan los parámetros de soldadura correspondientes para el proceso de soldadura realizado con el soplete para soldar (10) y se utilizan como valores de referencia para procesos de soldadura posteriores similares.
2. Procedimiento de soldadura según la reivindicación 1, caracterizado porque se almacenan los datos de medición recibidos y/o los valores determinados de la posición 3D del soplete para soldar (10).
3. Procedimiento de soldadura según la reivindicación 1 ó 2, caracterizado porque los valores para la posición 3D del soplete para soldar (10) se determinan en momentos a elegir libremente, que pueden ser definidos, en particular al principio y al final de un proceso de soldadura realizado con el soplete para soldar (10).
4. Procedimiento de soldadura según una de las reivindicaciones 1 a 3, caracterizado porque además de los valores de las posiciones 3D se almacenan los tiempo correspondientes de un proceso de soldadura realizado con el soplete para soldar (10).
5. Procedimiento de soldadura según la reivindicación 4, caracterizado porque los tiempos que corresponden a los valores de las posiciones 3D se usan como valores de referencia para procesos de soldadura posteriores simi- lares.
6. Procedimiento de soldadura según una de las reivindicaciones 1 a 5, caracterizado porque los valores determinados para las posiciones 3D, dado el caso con los parámetros de soldadura y tiempos correspondientes, se comparan con los valores de referencia depositados, corrigiéndose dado el caso, los parámetros de soldadura y almacenándose las modificaciones realizadas.
7. Procedimiento de soldadura según una de las reivindicaciones 1 a 6, caracterizado porque los datos relevantes para la calidad del cordón de soldadura, en particular la velocidad de soldadura, el orden de los cordones de soldadura (32) y el ángulo de inclinación (69) del soplete para soldar (10) durante el proceso de soldadura son registrados y almacenados.
8. Procedimiento de soldadura según una de las reivindicaciones 1 a 7, caracterizado porque los valores almacenados para las posiciones 3D del soplete para soldar (10) de al menos un proceso de soldadura realizado, dado el caso, los valores de referencia y modificaciones almacenadas, son leídos para un análisis.
9. Procedimiento de soldadura según una de las reivindicaciones 1 a 8, caracterizado porque los parámetros de soldadura de un proceso de soldadura se ajustan automáticamente con ayuda de los valores determinados para la posición 3D.
10. Procedimiento de soldadura según una de las reivindicaciones 1 a 9, caracterizado porque los valores determinados para la posición 3D del soplete para soldar (10) se comparan con valores de referencia y se indican al usuario del soplete para soldar (10) de forma acústica u óptica.
11. Procedimiento de soldadura según una de las reivindicaciones 1 a 10, caracterizado porque la velocidad de soldadura se determina a partir de los valores determinados para la posición 3D en función del tiempo y se compara con valores predeterminados para la velocidad de soldadura y se indica al usuario del soplete para soldar (10) de forma acústica u óptica.
12. Procedimiento de soldadura según una de las reivindicaciones 1 a 11, caracterizado porque el inicio de un proceso de soldadura sólo está permitido en posiciones 3D predeterminadas del soplete para soldar (10).
13. Procedimiento de soldadura según una de las reivindicaciones 1 a 12, caracterizado porque el valor de referencia para una posición 3D del soplete para soldar (10) de la posición inicial (53) de un cordón de soldadura (32) se adapta a la dirección de soldadura preferida del usuario del soplete para soldar (10).
14. Procedimiento de soldadura según una de las reivindicaciones 1 a 13, caracterizado porque la posición 3D del soplete para soldar (10) se determina con el aparato de soldadura (1) desactivado.
15. Procedimiento de soldadura según una de las reivindicaciones 1 a 14, caracterizado porque los datos de medición de al menos un sensor (43) integrado en la ropa de trabajo, en particular, en una pulsera o en un guante del usuario del soplete para soldar (10) se transmiten preferiblemente a la unidad de valoración (40).
16. Procedimiento de soldadura según una de las reivindicaciones 1 a 15, caracterizado porque unos valores de referencia, por ejemplo para la posición inicial (53) del cordón de soldadura (32) y los parámetros de soldadura, se almacenan en una memoria (48) en el soplete para soldar (10).
17. Procedimiento de soldadura según una de las reivindicaciones 5 a 16, caracterizado porque para los valores de referencia se almacena un identificador para identificar los valores de referencia para piezas de trabajo (16) similares.
18. Procedimiento de soldadura según una de las reivindicaciones 1 a 17, caracterizado porque se detecta el tiempo durante el proceso de soldadura realizado con el soplete para soldar (10).
19. Procedimiento de soldadura según la reivindicación 18, caracterizado porque los valores determinados de las posiciones 3D durante un proceso de soldadura y el tiempo correspondiente para el cálculo de la velocidad de soldadura del proceso de soldadura se transmiten al dispositivo de control (4) del aparato de soldadura (1).
20. Procedimiento de soldadura según una de las reivindicaciones 1 a 19, caracterizado porque se ajusta la distancia entre el emisor (33) y un punto de referencia en el espacio tridimensional.
21. Sistema de soldadura, con un aparato de soldadura (1) y un soplete para soldar (10) que puede conectarse mediante un paquete de mangueras (23), estando previsto un dispositivo para la determinación de la posición del soplete para soldar (10), estando dispuesto para la determinación de la posición del soplete para soldar (10) en el espacio tridimensional al menos un emisor (33) y al menos un sensor (36) en el soplete para soldar (10) o estando asignado a éste, estando conectado el sensor (36) con una unidad de valoración (40), de modo que pueden determinarse los valores de la posición 3D del soplete para soldar (10) mediante los datos de medición registrados por el sensor (36), caracterizado porque en el soplete para soldar (10) está prevista una memoria (48) para almacenar los valores determinados para la posición 3D del soplete para soldar (10) así como los parámetros de soldadura correspondientes para un proceso de soldadura realizado con el soplete para soldar (10).
22. Sistema de soldadura según la reivindicación 21, caracterizado porque el emisor (33) está formado por una bobina, una estación de radio, una estación de radar o emisores (33) móviles, como satélites, en particular según el sistema GPS.
23. Sistema de soldadura según la reivindicación 21 ó 22, caracterizado porque el emisor (33) del dispositivo de determinación de la posición presenta al menos una bobina para la generación de un campo magnético en la zona (27) del proceso de soldadura del soplete para soldar (10) y porque al menos un sensor (36) para registrar el campo magnético generado por la bobina está dispuesto en el soplete para soldar (10) o está asignado a éste.
24. Sistema de soldadura según una de las reivindicaciones 21 a 23, caracterizado porque el emisor (33) cubre varias zonas de procesos de soldadura (27) y, por lo tanto, varios sopletes para soldar (10), pudiendo determinarse por lo tanto la posición 3D de varios sopletes para soldar (10) mediante sensores (36-38) integrados en éstos o asignados a éstos.
25. Sistema de soldadura según una de las reivindicaciones 21 a 24, caracterizado porque cada zona de procesos de soldadura (27) tiene asignado un punto de referencia (62) en el espacio tridimensional.
26. Sistema de soldadura según una de las reivindicaciones 21 a 25, caracterizado porque el sensor (36) está formado por un sensor (36) magnetorresistivo.
27. Sistema de soldadura según una de las reivindicaciones 21 a 26, caracterizado porque está previsto un dispositivo (39) para la filtración de campos magnéticos parásitos, que son generados en particular por la fuente de corriente (2) del aparato de soldadura (1) y un arco voltaico (15).
28. Sistema de soldadura según una de las reivindicaciones 21 a 27, caracterizado porque está previsto un dispositivo indicador para la indicación acústica y/u óptica de la posición 3D determinada o de desviaciones de posiciones de referencia para favorecer medidas de corrección que han de realizarse.
29. Sistema de soldadura según la reivindicación 28, caracterizado porque el dispositivo indicador está integrado en una prenda de trabajo del soldador, en particular en el casco de soldador.
30. Sistema de soldadura según una de las reivindicaciones 21 a 29, caracterizado porque al menos un sensor (36) está dispuesto en una prenda de vestir del soldador, en particular en una pulsera o un guante.
31. Sistema de soldadura, con un aparato de soldadura (1) y un soplete para soldar (10) que puede conectarse mediante un paquete de mangueras (23), estando previsto un dispositivo para la determinación de la posición del soplete para soldar (10), estando dispuesto para la determinación de la posición del soplete para soldar (10) al menos un emisor (33) en el soplete para soldar (10) o estando asignado a éste, y estando dispuesto al menos un sensor (36) en el espacio tridimensional, estando conectado este sensor (36) con una unidad de valoración (40), de modo que pueden determinarse los valores de la posición 3D del soplete para soldar (10) mediante los datos de medición registrados por el sensor (36), caracterizado porque en el soplete para soldar (10) está prevista una memoria (48) para almacenar los valores determinados para la posición 3D del soplete para soldar (10) así como los parámetros de soldadura correspondientes para un proceso de soldadura realizado con el soplete para soldar (10).
Patentes similares o relacionadas:
SISTEMA DE CONTROL DE MOVIMIENTO EN SOLDADURA, del 16 de Marzo de 2008, de AUTOMATIZACIONES BADIOLA, S.L.: Sistema de control de movimiento en soldadura, que consiste en incorporar unas bobinas en el cabezal de realización de las soldaduras, en las cuales […]
PROCEDIMIENTO Y DISPOSITIVO PARA EL REGISTRO DE LA CALIDAD DE UN CORDÓN DE SOLDADURA DURANTE LA SOLDADURA DE PIEZAS DE TRABAJO, del 20 de Julio de 2011, de PRECITEC VISION GMBH & CO. KG: Procedimiento para el registro de la calidad de un cordón de soldadura durante la soldadura de piezas de trabajo , en el que con un procedimiento […]
SISTEMA DE CAPTACION DE LUZ PARA EL MONITORIZADO ESPECTROSCOPICO DE SOLDADURAS ORBITALES, del 28 de Enero de 2010, de UNIVERSIDAD DE CANTABRIA: Sistema de captación de luz para el monitorizado espectroscópico de soldaduras orbitales.
La invención facilita la captura de la luz generada […]
Procedimiento para el aprendizaje/ensayo de una secuencia de movimiento de un robot de soldadura, robot de soldadura y control asociado, del 12 de Abril de 2019, de FRONIUS INTERNATIONAL GMBH: Procedimiento para el aprendizaje de un robot de soldadura en el que se fija y guarda una posición por medio de un proceso de posicionamiento realizado manualmente, […]
Antorcha de corte de metales de accionamiento manual, del 4 de Octubre de 2017, de WELDCUT PUNTO PLASMA, S.L: 1. Antorcha de corte de metales, de accionamiento manual; que comprende una empuñadura de agarre manual y un cabezal de corte mediante […]
SISTEMA Y PROCEDIMIENTO DE FABRICACIÓN DE NUDOS, del 1 de Junio de 2017, de NAVANTIA, S.A.: Sistema y procedimiento de fabricación de nudos. El sistema de fabricación de nudos comprende primeros medios de captación de imagen, un sistema de soldadura, […]
Medios de posicionamiento para producir señales luminosas para posicionar una herramienta robótica con relación a un pieza de trabajo; método de utilización de tales medios de posicionamiento, del 27 de Marzo de 2012, de Turner, Andrew: Un dispositivo de posicionamiento para producir una señal luminosa para posicionar una herramienta robótica con relación a una pieza de trabajo , que comprende:
un […]
ROBOT SOLDADOR DE ESTRUCTURAS METALICAS, del 17 de Marzo de 2010, de TESOL, S.L.: Robot soldador de estructuras metálicas.
Comprende un módulo de control para gobernar el funcionamiento del robot el cual se ubica sobre unas […]