Método para tratamiento de residuos.
El procedimiento comprende: - Generación de un lecho metálico fundido,
que se desplaza según una dirección de avance, describiendo, de forma cíclica y continua, un circuito cerrado, y cuya superficie comprende, al menos un tramo sustancialmente exento de escorias. - Carga de un residuo sobre el citado tramo sustancialmenteexento de escorias, siendo el residuo arrastrado, en flotación, por el lecho metálico fundido, en la citada dirección de avance. -Retención del residuo en la superficie del lecho metálico fundido, según la citada dirección de avance. - Procesado del residuo por efecto del constante y continuo intercambio térmico generado por el desplazamiento del lecho metálico fundido bajo el residuo que permanece retenido.
Tipo: Patente Internacional (Tratado de Cooperación de Patentes). Resumen de patente/invención. Número de Solicitud: PCT/ES2006/000032.
Solicitante: DIGIMET 2013 SL.
Nacionalidad solicitante: España.
Inventor/es: COBOS JIMENEZ,LUIS, ONCALA AVILÉS,JOSE LUIS.
Fecha de Publicación: .
Clasificación Internacional de Patentes:
- C22B7/00 QUIMICA; METALURGIA. › C22 METALURGIA; ALEACIONES FERROSAS O NO FERROSAS; TRATAMIENTO DE ALEACIONES O METALES NO FERROSOS. › C22B PRODUCCION O AFINADO DE METALES (fabricación de polvos metálicos o sus suspensiones B22F 9/00; producción de metales por electrólisis o electroforesis C25 ); PRETRATAMIENTO DE MATERIAS PRIMAS. › Tratamiento de materias primas distintas a los minerales, p. ej. residuos, para producir metales no ferrosos o sus compuestos.
PDF original: ES-2528114_T3.pdf
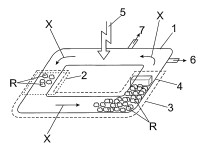
Fragmento de la descripción:
Método para tratamiento de residuos Objeto de la invención
La presente invención se refiere a un método para tratamiento de residuos, en especial para la valorización de residuos tales como polvos de acería, virutas y escorias de aluminio, chatarras electrónicas, residuos que contienen metales preciosos o la inertización de materiales peligrosos, como fibra de amianto.
Los residuos son vertidos en un lecho metálico fundido, realizándose el procesado completo de los mismos, prácticamente en la superficie del lecho metálico fundido. Este procesado, permite por ejemplo recuperar la fracción metálica contenida en el residuo.
Antecedentes de la invención
Los procesos utilizados para el tratamiento de residuos procedentes de diferentes industrias están basados en el empleo de grandes instalaciones que incluyen hornos en los que se realiza la fusión, vitrificación o volatilización del residuo a recuperar, inertizar o eliminar, instalaciones que generalmente resultan costosas y con poca eficiencia energética, por lo que el tratamiento de recuperación de los residuos se convierte en un proceso muy caro.
Cuando se utiliza un metal fundido, el tratamiento de los residuos que presentan una densidad menor que la del metal fundido se hace complicado debido a que no llegan a introducirse en el mismo como consecuencia de la existencia de una capa de escorias en la superficie del mismo, cuya menor densidad impide el contacto de los residuos con el metal fundido.
Asimismo, los residuos normalmente incorporan materiales de distinta clase mezclados, tales como plásticos, metales y otros, que al fundir pueden provocar humos o gases contaminantes de difícil tratamiento. Esto implica tener que realizar tratamientos previos, de separación o selección de los residuos.
Un tipo de residuo a tratar sería por ejemplo los polvos de acería que contienen cantidades importantes de Zn, Pb o Cd y que son generados en las operaciones de fusión y afino en los procesos de producción de acero, que se recogen en los sistemas de purificación de humos, y que constituyen un residuo peligroso debido fundamentalmente a la presencia de Pb o Cd.
Actualmente los polvos de acería se tratan por distintas vías:
- Vertido en vertederos para productos peligrosos. Esta es la opción menos empleada ya que resulta costosa y existen otras alternativas mejores.
- Inertización mediante su mezcla con aditivos aglomerantes capaces de generar un encapsulado que permita superar el test de lixiviación que establece la normativa.
- Recuperación por tratamiento térmico de los metales valorizables y separación y depuración de los gases que contienen metales volatilizables.
Existe un importante número de métodos diseñados específicamente para el tratamiento de los polvos de acería en los que, mediante la aplicación de técnicas muy diversas, se pretende alcanzar el objetivo de recuperar los metales contenidos en dicho residuo. Así, por ejemplo, en las patentes US6322745, US594223 y US6494933 se describen métodos de tratamiento en los que, tanto la técnica empleada como el resultado obtenido, difieren de forma sustancial en función del proceso aplicado. En las citadas patentes se engloba el estado de la técnica actualmente vigente, ya que recoge el tratamiento del polvo de acería por los tres métodos más utilizados a escala mundial.
En estos procesos, la reducción del óxido de hierro contenido en el polvo de acería se consigue en todos los casos mediante la aportación de material carbonoso como elemento reductor. Las diferencias radican en la forma y momento en que los materiales se introducen al horno, la geometría de éste y el sistema de calentamiento utilizado.
Dichas diferencias se manifiestan particularmente en las limitaciones operativas que los distintos procesos presentan. Podemos mencionar como ejemplo los sistemas de calentamiento. En las patentes citadas se utiliza, en el orden indicado, la combustión de carbón por inyección de oxígeno, el arco de plasma DC y la combustión de carbón por soplado de aire respectivamente.
Con la inyección de oxígeno y el plasma se obtienen altas temperaturas de proceso que provocan importantes problemas de desgaste en los refractarios de los hornos o reactores. La necesidad imperiosa de incorporar paneles y sistemas de refrigeración repercute directamente en la reducción del rendimiento energético.
Con el soplado con aire, las temperaturas son menores pero una parte variable del hierro contenido en el polvo de acería queda sin reducir y, además, el material obtenido debe ser reprocesado en horno de arco por que no se
alcanza la temperatura de fusión del metal que permitiría la extracción directa del hierro.
Otro tipo de residuo de difícil tratamiento serían las virutas de aluminio que presentan una densidad muy pequeña frente al metal fundido, resultan de difícil fusión y presentan asimismo la problemática de que se oxidan fácilmente con el aire. Un dispositivo para su tratamiento se describe en la Patente US 6.36.745. En este caso se describe un horno de calentamiento de grandes dimensiones que está comunicado con dos depósitos interconectados a los que se dirige el metal fundido del horno con ayuda de una bomba o grupo de bombas. En el primer depósito se introducen por un lado las partículas sólidas de metal desde el exterior y por otro el metal fundido procedente del horno, la mezcla así formada se dirige a continuación a un segundo depósito desde el que las impurezas, espumas y escorias del baño se dirigen hacia el exterior, retornando el metal fundido al horno.
Este horno cuenta con un pequeña salida en un lado para ocasionar con ayuda de la bomba un flujo de metal hacia el primer depósito en el que se encuentra un divisor que crea una circulación en espiral que facilita la inmersión de las partículas de residuos en el flujo de metal, para a continuación pasar este flujo de metal, a través de un conducto situado en el fondo del citado primer depósito, a un segundo depósito donde se liberan espumas, escorias e impurezas, tal y como se ha mencionado anteriormente, y seguidamente el flujo de metal se introduce en el horno.
Por tanto, el procesado de las virutas o escorias de aluminio se realiza por inmersión en el caldo contenido en el primer depósito, mediante la generación de un flujo espiral descendente que arrastra las virutas desde la superficie del metal fundido al interior del mismo.
Este horno es de grandes dimensiones, está calentado por resistencias que precisan de una gran potencia y requiere de una elevada longitud, resultando básicamente rentable en grandes instalaciones de tratamiento de residuos.
La instalación presenta una geometría complicada debido a la incorporación por un lado del horno y por otro lado de los depósitos interconectados y los conductos de comunicación que aumentan la complejidad en el mantenimiento de la instalación, apagado, encendido y vaciado de la misma.
Asimismo es de destacar que en la instalación objeto de esta patente se utilizan unas bombas sumergidas para mover el metal fundido con la complejidad que supone el mantenimiento de las mismas.
Esta instalación es adecuada para el tratamiento de virutas de aluminio, pero presenta peligros por la inmersión rápida de aluminio en el caldo de metal fundido, ya que puede provocar explosiones si las virutas de aluminio incorporan agua o humedad, pues éste agua se convierte en hidrógeno que puede explotar con gran violencia.
Otras instalaciones se describen en las patentes US 6.217.823, US 4.598.899 y US 5.143.357, todas ellas centradas en el tratamiento de virutas de aluminio.
Descripción de la invención
El método de tratamiento de residuos objeto de la invención, comprende las siguientes fases:
- Generación de un lecho metálico fundido, que se desplaza según una dirección de avance, describiendo, de forma cíclica y continua, un circuito cerrado, y cuya superficie comprende, al menos un tramo sustancialmente exento de escorias.
- Carga de un residuo sobre el citado tramo sustancialmente exento de escorias, siendo el residuo arrastrado, en flotación, por el lecho metálico fundido, en la citada dirección de avance.
- Retención del residuo en la superficie del lecho metálico fundido, según la citada dirección de avance.
- Procesado del residuo por efecto del constante y continuo intercambio térmico generado por el desplazamiento del lecho metálico fundido bajo el residuo que permanece retenido.
El método comprende una extracción de escorias para que la superficie del lecho metálico fundido presente el citado tramo sustancialmente exento de escorias, que coincidirá, con la zona de carga... [Seguir leyendo]
Reivindicaciones:
1. Un método de tratamiento de residuos, que comprende las siguientes etapas:
- generación de un lecho metálico fundido, que se desplaza según una dirección de avance, describiendo, de forma cíclica y continua, un circuito cerrado, teniendo dicho lecho metálico fundido una superficie que comprende al menos una zona de carga (2) sustancialmente exenta de escorias,
- carga de un residuo sobre la citada zona de carga (2) sustancialmente exenta de escorias, siendo el residuo arrastrado, en flotación, por el lecho metálico fundido, en la citada dirección de avance, en el que el residuo comprende una fracción metálica soluble en el lecho metálico fundido a la temperatura del lecho metálico fundido,
- retención del residuo en una zona de retención de residuos en dicha superficie del lecho metálico fundido, mientras el residuo se desplaza en la citada dirección de avance,
- procesado del residuo por efecto del constante y continuo intercambio térmico generado por el desplazamiento del lecho metálico fundido bajo el residuo que permanece retenido en dicha zona de retención de residuos, llevándose a cabo el procesado del residuo sustancialmente en la superficie del metal fundido, sin la necesidad de sumergir el residuo en el metal fundido, de manera que una zona de procesado (3) de residuos comienza después de la zona de carga (2) de residuos hacia una zona de extracción de escoria (6) para que el procesado del residuo se complete en la zona de retención de residuos, comprendiendo el procesado la incorporación al lecho metálico fundido de la fracción metálica del residuo soluble a la temperatura del lecho metálico fundido,
- extracción de la escoria en una zona de extracción de escoria (6) de dicho circuito, ubicándose dicha zona de extracción de escoria (6) tras la zona de procesado de residuos y la zona de retención de residuos, y antes de la zona de carga (2) de residuos.
2. Método de acuerdo con la reivindicación 1, que comprende además la etapa de calentamiento adicional del lecho metálico fundido en proximidad a la zona de retención de residuos para acelerar su procesado.
3. Método de acuerdo con la reivindicación 1, en el que el residuo comprende una fracción volatilizable.
4. Método de acuerdo con la reivindicación 1, que comprende una fase de extracción y tratamiento de la fracción volatilizable.
5. Método de acuerdo con la reivindicación 1, en el que el procesado del residuo produce la incorporación al lecho metálico fundido, en forma de escoria, de la fracción no soluble a la temperatura del lecho metálico fundido y no volatilizable.
6. Método de acuerdo con la reivindicación 1, que comprende el calentamiento del lecho metálico fundido para conseguir una temperatura homogénea en la zona sustancialmente exenta de escorias.
7. Método de acuerdo con reivindicación 1, que comprende una fase de sangrado discrecional de una parte del lecho metálico fundido.
Patentes similares o relacionadas:
Horno de plasma y oxigas, del 10 de Junio de 2020, de UMICORE: Aparato para la fusión de cargas metalúrgicas que comprende un horno de baño susceptible de contener una carga fundida hasta un nivel determinado, […]
Proceso para recuperar metales a partir de una corriente rica en hidrocarburos y residuos carbonáceos, del 27 de Mayo de 2020, de ENI S.P.A.: Un proceso para recuperar metales de mezclas bituminosas que consisten en - Componentes sólidos no solubles en tetrahidrofurano. - Especies […]
Procedimiento para el tratamiento de lodo que contiene hierro, del 13 de Mayo de 2020, de Arcelormittal: Un procedimiento para el tratamiento de un lodo de alto horno que contiene hierro y entre el 4,5 % y el 12 % en peso de zinc, comprendiendo dicho procedimiento […]
Procedimiento de recuperación y reciclaje de materiales que constituyen membranas para la separación de hidrógeno, del 15 de Abril de 2020, de KT - Kinetics Technology S.p.A: Un procedimiento de recuperación y reciclaje de materiales que constituyen membranas para la separación de hidrógeno, caracterizado porque comprende: […]
Clasificación de aleaciones de aluminio mediante valores de conductividad eléctrica, del 15 de Abril de 2020, de Hydro Aluminium Recyling Deutshland GmbH: Procedimiento para clasificar aleaciones de aluminio en chatarra de aluminio, caracterizado por que las chatarras de aluminio se suministran a una estación de medición, […]
Procedimiento para fundir chatarra, del 25 de Marzo de 2020, de L'AIR LIQUIDE, SOCIETE ANONYME POUR L'ETUDE ET L'EXPLOITATION DES PROCEDES GEORGES CLAUDE: Procedimiento para fundir chatarra en un horno, comprendiendo dicho procedimiento las etapas de: - alimentar una carga de chatarra sólida al horno, […]
Procedimiento y sistema para reciclar baterías y placas de circuito impreso de desecho en sales fundidas o metales fundidos, del 11 de Marzo de 2020, de Riedewald, Frank: Sistema de reciclaje de materiales de alimentación compuestos de desecho tales como placas de circuito impreso (PCB), baterías, teléfonos […]
Planta y método para recuperar y tratar residuos del machacado de chatarra ferrosa, del 19 de Febrero de 2020, de DANIELI & C. OFFICINE MECCANICHE S.P.A.: Planta para recuperar y tratar residuos del machacado de chatarra , caracterizada por que comprende: - una primera parte de planta provista de: un […]