Procedimiento para la fabricación de conductos de aire de material plástico y molde utilizado.
Procedimiento y molde para la fabricación de conductos de aire (P) de material plástico especialmente blando,
de dureza entre shore 5 y shore 65, del tipo que comprende un cuerpo principal (P1) hueco provisto de al menos una protuberancia o nipple 5 (P2) que sobresale de la pared exterior del cuerpo principal (P1), comprendiendo las etapas de moldear por inyección al menos un nipple (P2) de material plástico en el interior de una primera cavidad (1) de un molde (M); la interconexión de la primera cavidad (1) con una segunda cavidad (3) dispuesta en el mismo molde (M) y situada adyacente a dicha primera cavidad (1) para formar un volumen único y moldear por soplado un cuerpo hueco a partir de un parison de material plástico moldeable en el interior de la segunda cavidad (3).
Tipo: Patente de Invención. Resumen de patente/invención. Número de Solicitud: P201131365.
Solicitante: FUNDACIO PRIVADA ASCAMM.
Nacionalidad solicitante: España.
Inventor/es: GUMA NOEL,JAUME, PLANTA TORRALBA,FRANCISCO JAVIER.
Fecha de Publicación: .
Clasificación Internacional de Patentes:
- B29C45/14 TECNICAS INDUSTRIALES DIVERSAS; TRANSPORTES. › B29 TRABAJO DE LAS MATERIAS PLASTICAS; TRABAJO DE SUSTANCIAS EN ESTADO PLASTICO EN GENERAL. › B29C CONFORMACIÓN O UNIÓN DE MATERIAS PLÁSTICAS; CONFORMACIÓN DE MATERIALES EN ESTADO PLÁSTICO, NO PREVISTA EN OTRO LUGAR; POSTRATAMIENTO DE PRODUCTOS CONFORMADOS, p. ej. REPARACIÓN (fabricación de preformas B29B 11/00; fabricación de productos estratificados combinando capas previamente no unidas para convertirse en un producto cuyas capas permanecerán unidas B32B 37/00 - B32B 41/00). › B29C 45/00 Moldeo por inyección, es decir, forzando un volumen determinado de material de moldeo a través de una boquilla en un molde cerrado; Aparatos a este efecto (moldeo por inyección-soplado B29C 49/06). › incorporando partes o capas preformadas, p. ej. moldeo por inyección alrededor de elementos insertos o sobre objetos a recubrir.
- B29C49/06 B29C […] › B29C 49/00 Moldeo por soplado, es decir, soplando una preforma o un parisón en un molde por obtener la forma deseada; Aparatos a este efecto. › Moldeo por inyección-soplado.
- B29C49/20 B29C 49/00 […] › de objetos que tienen elementos insertos o refuerzos.
- B29C49/48 B29C 49/00 […] › Moldes.
- B29C69/02 B29C […] › B29C 69/00 Combinaciones de técnicas de conformación no previstas en un solo grupo principal B29C 39/00 - B29C 67/00, p. ej. asociaciones de técnicas de moldeo y ensamblaje; Aparatos a este efecto. › de técnicas de moldeo solamente.
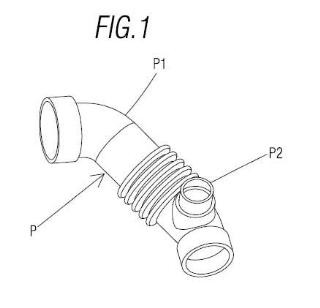
Fragmento de la descripción:
Procedimiento para la fabricación de conductos de aire de material plástico y molde utilizado.
OBJETO DE LA INVENCIÓN
La presente solicitud de patente de invención tiene por objeto el registro de un procedimiento y molde para la fabricación de conductos de aire de material plástico que incorpora notables innovaciones y ventajas.
Más concretamente, la invención propone el desarrollo de un nuevo procedimiento para la fabricación de conductos de aire de material plástico especialmente blando, de durezas entre shore 5 y shore 65, del tipo de los que disponen de al menos una segunda geometría o conector unida al cuerpo principal, de especial aplicación en el sector del automoción, permitiendo optimizar tiempos y costes de fabricación.
ANTECEDENTES DE LA INVENCIÓN
En el mundo de las canalizaciones de aire y en especial en su aplicación al sector de la automoción, son conocidas las piezas utilizadas para la conducción de aire conformadas por un cuerpo principal hueco que entre sus dos extremos dispone de una o varias boquillas acopladoras, también llamadas nipples que permiten la derivación del conducto principal para su conexión con otros dispositivos o canalizaciones, estando unidas y comunicadas dichos nipples al cuerpo principal.
Es bien conocida la fabricación de piezas de material plástico constituidas por un cuerpo interiormente hueco y partes adicionales periféricas unidas a éste, tales como por ejemplo, tubos de canalizaciones, depósitos o cualquier otro elemento hueco cerrado que suele formar parte de un vehículo motor. Este tipo de conectores o nipples suelen caracterizarse por ser de formas precisas, de espesores delgados (incluso menor a 2mm) y con una precisión y/o tolerancia en la zona de unión con el cuerpo principal muy exigente.
Para la obtención del cuerpo principal hueco, se utiliza habitualmente un proceso de extrusión-soplado convencional mientras que la obtención del resto de conectores unidos al cuerpo principal, tales como nipples, orejas, pipetas, inclusión de sensores, se lleva a cabo en etapas adicionales mediante procesos de inyección, corte, etc.
Para conseguir el producto final se requiere una unión física entre el cuerpo principal y los diferentes conectores. Esta unión se hace posteriormente al proceso de fabricación unitaria y mediante procesos complementarios, tales como, soldadura, clipaje manual, etc.
En general, el tipo de piezas anteriormente mencionadas, obtenidas en diversas etapas del proceso de fabricación, presentan una gran incerteza en lo que se refiere a la calidad del producto acabado, produciéndose de forma indeseada un número elevado de rechazos del producto debido a la poca robustez del proceso, el cual está ligado a tareas manuales y procesos imperfectos (soldadura y encolado) , hecho que se acentúa especialmente cuando el tipo de plástico a utilizar es del tipo blando de dureza entre shore 5 y shore 65.
Tales deficiencias en el producto final, frecuentemente están asociadas a defectos en la unión de los nipples asociados al conducto principal.
Además, otro inconveniente no menos importante es el hecho de que el método de fabricación actual implica unos costes derivados elevados, por un lado, por la necesidad de disponer de utillajes para la realización de los tres procesos de transformación (molde extrusión-soplado, molde de inyección y utillajes destinados a la unión de las múltiples partes) y, por otro lado, de los elevados tiempos de ciclo debidos a que cada uno de los tres procesos de fabricación son completamente independientes entre sí.
En el estado de la técnica son conocidas por el solicitante diversas técnicas con la finalidad de resolver los problemas anteriormente citados. Tales técnicas pueden resumirse básicamente en tres métodos:
1) Método tradicional: Consiste en la obtención del cuerpo principal del conducto por extrusión soplado y los nipples por inyección, en utillajes y procesos totalmente independientes. De este modo, una vez obtenidas las dos geometrías, se unen mediante un proceso de soldadura (placa caliente, ultrasonidos, etc.) lo que requiere una máquina y un utillaje específico para esa parte del proceso. El problema principal de este método estriba en un incremento de coste derivado de los costes individuales de los subprocesos de manufactura, control de calidad de los subprocesos, logística del propio proceso, mayor necesidad de espacio en planta, costes de la no calidad, etc.; además de los problemas derivados de que las piezas no soportan de forma adecuada el ciclo de vida para el cual han sido diseñadas, especialmente cuando el plástico empleado es de dureza entre shore 5 y shore 65.
2) Método integrado: Es una variante del método anterior, consistente en fabricar primero el nipple por inyección y disponerlo en el interior del molde del proceso de extrusión soplado como si fuera un inserto, de modo que el polímero abrazaría la pieza o inserto en el soplado de forma que el nipple quede solidario al cuerpo principal hueco obtenido en el segundo proceso. El problema de este método consiste en que requiere de un tercer proceso, externo, que comunique interiormente el nipple y el cuerpo principal hueco. Además como la unión entre ambas geometrías se realiza de forma física o de interferencia mecánica y no en caliente (ya que el nipple ha sido producido en una etapa anterior independiente) las prestaciones mecánicas de dicha unión y la flexibilidad en cuanto al diseño se ven drásticamente reducidas, hecho que se agudiza de forma extrema cuando el material utilizado es de dureza comprendida entre shore 5 y shore 65.
3) Método de extrusión soplado e inyección integrado: Es la técnica de extrusión soplado e inyección en el mismo utillaje pero de forma secuencial. Este método no es aplicable cuando el material empleado es de dureza entre shore 5 y shore 65 debido a que la sobre presión derivada del proceso de inyección sobre la geometría obtenida por soplado deforma ésta haciéndola invalida para su uso final.
En este sentido, es conocida la patente nº US 5198174 que describe la obtención de soportes radiales adicionales a un tubo a partir de la aplicación de un proceso de sobremoldeado que consiste en una primera fase de obtención del tubo hueco por soplado, posteriormente, el molde es modificado a una segunda disposición y se suministra material al mismo. En último lugar, la parte movible del molde es modificada a una tercera posición que hace que el material sea presurizado y forme la porción radial integrada en la primera porción soplada anteriormente.
También es conocida la patente nº ES 2104846, que describe un proceso de fabricación integrado para el mismo tipo de componentes. Este proceso consiste en una primera fase de moldeo por soplado que permite la obtención del cuerpo hueco, la modificación del molde y la posterior fase de inyección de unas pestañas adheridas al primer cuerpo.
Por otra parte, las patentes americanas nº US 6793870 y US 5266262 hacen referencia a sendos procesos de unión de dos componentes de material plástico de forma que el componente hueco ha sido obtenido en un primer proceso. Posteriormente, esta pieza ya formada es introducida en un segundo molde donde tiene lugar el proceso para obtener el segundo componente, de manera que durante el segundo proceso se crea una unión entre ambos componentes.
Sin embargo, a pesar de las ventajas que los procesos citados pueden presentar respecto al proceso de fabricación convencional, éstos también presentan una serie de inconvenientes:
-No son adecuados para la fabricación de tubos con espesores inferiores a 2mm ya que la presión en el segundo proceso de sobremoldeado deforma el cuerpo principal hueco;
-Son aplicables en materiales muy técnicos (PA, PA6, PA66, PPS, PET, PBT, PEEK, etc.) habitualmente reforzados, no resultando aptos para la transformación de otros materiales, tales como elastómeros termoplásticos blandos, PP, PE, EPDM, etc. de durezas entre shore 5 y shore 65.
-El tiempo de ciclo es elevado (sobre un 30% mayor que en los procesos tradicionales) , debido a que es la única forma de minimizar las deformaciones durante el proceso de llenado en la fase de sobremoldeado pero que en cambio afecta en la compactación interna de la pieza hecho que imposibilita conseguir una estructura del polímero adecuada, este aspecto afecta sobre todo a la calidad final de la pieza ya que La parte sobremoldeada se encuentra siempre alineada a los ejes radiales y/o axiales del cuerpo hueco.
-Los métodos antes descritos no son adecuados para obtener piezas y componentes completamente huecos, cuerpo principal y protuberancias, en una sola fase de manufactura. Siempre...
Reivindicaciones:
1. Procedimiento para la fabricación de conductos de aire de material plástico de dureza entre shore 5 y shore 65 (P) , en particular del tipo que comprende un cuerpo principal (P1) interiormente hueco provisto de al menos una protuberancia o nipple (P2) , interiormente también hueco, que sobresale de la pared exterior del cuerpo principal (P1) , encontrándose el cuerpo principal (P1) y la protuberancia o nipple (P2) comunicados entre sí y formando un único volumen interior al final del procedimiento, caracterizado por el hecho de que dicho volumen interior único es obtenido mediante una manufactura de acuerdo con las siguientes etapas del procedimiento:
a) Moldeo por inyección de al menos una protuberancia o nipple (P2) hueca en su interior, de material plástico de dureza comprendida entre shore 5 y shore 65 en el interior de una primera cavidad (1) definida por al menos dos semi-moldes (M1, M2) de un molde (M) y un dispositivo interior (6) cilíndrico ubicado entre dichos semi-moldes (M1, M2) , mediante el suministro del material por el lado perpendicular o como mínimo no paralelo o alineado con el eje central del nipple (P2) que confiere su volumen interior;
b) Desplazamiento del dispositivo interior (6) que confiere el volumen interno de la protuberancia o nipple (P2) de la etapa a) hacia una segunda cavidad (3) dispuesta en el mismo molde (M) de la etapa a) , estando tal segunda cavidad (3) situada de forma adyacente a la primera cavidad (1) , intersectando y comunicando las cavidades internas del cuerpo principal (P1) y la protuberancia o nipple (P2) ; y
c) Moldeo por soplado del cuerpo principal (P1) hueco a partir de un parison de material plástico moldeable de dureza comprendida entre shore 5 y shore 65 en el interior de la segunda cavidad (3) ; en el que dicha protuberancia o nipple (P2) es sostenida por unos elementos de bloqueo (5) movibles perpendicularmente respecto el eje central de dicha protuberancia o nipple (P2) .
2. Molde (M) para fabricación de piezas de material plástico de dureza comprendida entre shore 5 y shore 65 para moldear una pieza (P) formada por un cuerpo principal (P1) interiormente hueco y al menos una protuberancia o nipple (P2) adicional adherida lateralmente y exteriormente respecto al cuerpo principal (P1) , caracterizado por el hecho de que comprende al menos dos semi-moldes (M1, M2) y un dispositivo interior (6) cilíndrico situado entre dichos semi-moldes (M1, M2) , definiendo dichos semi-moldes (M1, M2) y dicho dispositivo interior (6) al menos una primera cavidad (1) para conformar la protuberancia o nipple (P2) , de geometría cilíndrica, hueca en su interior y de espesor constante, mediante un proceso de moldeo por inyección, estando vinculada dicha primera cavidad (1) con una región de entrada de material fluido a través de una boquilla, una cámara o del propio husillo de inyección, comprendiendo además una segunda cavidad (3) alargada, para conformar el cuerpo principal (P1) , mediante soplado y unos elementos de bloqueo (5) movibles ubicados entre las dos cavidades (1, 3) , siendo capaces dichos elementos de bloqueo (5) de desplazarse perpendicularmente respecto el eje central de la protuberancia o nipple (P2) de modo que permiten la sujeción de dicha protuberancia o nipple (P2) durante la conformación del cuerpo principal (1) .
3. Molde (M) según la reivindicación 2, caracterizado por el hecho de que los elementos de bloqueo (5) conforman un mecanismo desplazable mediante corredera, patín o esclusa para la separación de las primera y segunda cavidades (1, 3) , disponiendo la unión de una geometría en forma de escalón o cola de milano que garantiza la unión de ambos materiales.
4. Molde (M) según la reivindicación 2, caracterizado por el hecho de que dicho dispositivo interior (6) es desplazable a lo largo del eje central de la protuberancia o nipple (P2) , de manera que el cuerpo principal (P1) y dicha protuberancia o nipple (P2) entran en contacto para conformar la pieza (P) .
Patentes similares o relacionadas:
Procedimiento de fabricación de lentes polarizadas para gafas, del 4 de Abril de 2018, de SAFILO SOCIETA' AZIONARIA FABBRICA ITALIANA LAVORAZIONE OCCHIALI S.P.A.: Un procedimiento de fabricación de una lente polarizada para gafas, en el que la lente es producida por moldeo por co - inyección de la lente sobre una […]
Máquina para fabricar bolsas de filtro para productos de infusión, del 10 de Mayo de 2017, de I.M.A. INDUSTRIA MACCHINE AUTOMATICHE S.P.A.: Una máquina para fabricar bolsas de filtro para productos de infusión formados a partir de longitudes de material de filtro, caracterizada porque […]
Panel de insonorización del tablero de un vehículo automóvil, del 9 de Noviembre de 2016, de CENTRE D'ETUDE ET DE RECHERCHE POUR L'AUTOMOBILE (CERA): Panel de insonorización del tablero de un vehículo automóvil, dicho panel que comprende: * una cubierta hecha de una capa de fieltro de densidad sensiblemente […]
Dispositivo de impregnación, unidad de fabricación de un perfil hueco por pultrusión que comprende tal dispositivo y correspondiente procedimiento de fabricación, del 7 de Septiembre de 2016, de STRUCTIL S.A: Dispositivo para la impregnación de fibras con resina , con posibilidad de ser especialmente utilizado en una unidad de fabricación […]
Procedimiento continuo para la fabricación de placas de guía de luz, del 27 de Abril de 2016, de EVONIK ROHM GMBH: Procedimiento para la fabricación de placas de guía de luz con estructuras que influyen en la luz, en el que - se produce una banda de plástico - se emplea […]
Pastilla de limpieza de inodoros, del 22 de Octubre de 2014, de JEYES GROUP LIMITED: Una pastilla de limpieza de inodoros que comprende un cuerpo formado por una primera composición, teniendo el cuerpo al menos una abertura pasante que contiene […]
Procedimiento y molde para la fabricación componentes decorativos para interiores de vehículos automóviles, del 20 de Noviembre de 2013, de KEY SAFETY SYSTEMS, INC.: Procedimiento de fabricación de un componente para un interior de vehículo, que comprende las etapas de: (a) preparar una capa de laminado que comprende una capa […]
Puerta de lavadora y/o secadora, del 23 de Abril de 2013, de BSH ELECTRODOMESTICOS ESPAÑA S.A.: Puerta para lavadora y/o secadora.
La presente invención está dirigida a una puerta para aparato electrodoméstico, como por ejemplo una lavadora y/o […]