INSTALACIÓN PARA LA FABRICACIÓN DE RECIPIENTES QUE COMPRENDE UN RECINTO DE PROTECCIÓN EQUIPADO CON UN SISTEMA DE SOPLADO DE AIRE FILTRADO.
Instalación (10) para la fabricación de recipientes (12), en especial de botellas,
por soplado o por estirado-soplado a partir de una preforma (14) de material termoplástico, que comprende al menos: - un dispositivo (24) de alimentación con preformas destinado a alimentar con preformas una entrada (E) de la instalación (10), -una unidad de acondicionamiento térmica (26) que comprende al menos un horno (28) que comprende medios de calefacción (30) de las preformas (14) que están dispuestas entre una zona de entrada (32) en la cual las preformas (14) son llevadas por el dispositivo de alimentación (24) y una zona de salida (34) que desemboca en una zona (36), llamada de transferencia, de la instalación (10), -un primer dispositivo de transferencia (38) el cual, dispuesto en la zona de transferencia (36), está destinado a transferir las preformas (14) acondicionadas térmicamente desde la zona de salida (34) del horno (28) hasta una zona (40), llamada de alimentación, de una unidad de moldeado (42), -comprendiendo la unidad de moldeado (42) una rueda (44) dotada de una pluralidad de moldes (46) repartidos circunferencialmente y medios asociados de soplado o de estirado soplado, estando la rueda (44) accionada para girar de manera que cada molde (46) recorre un ciclo de transformación desde dicha zona de alimentación (40) hasta una zona (48), llamada de evacuación, -un segundo dispositivo de transferencia (50) el cual, dispuesto en la zona de transferencia (36), está destinado a transferir los recipientes (12) obtenidos desde la zona de evacuación (48) de la unidad de moldeado (42) hasta una salida (S) de la instalación (10), y -al menos un recinto de protección (52) que forma un cajón dispuesto para envolver al menos a la unidad de moldeado (42), delimitando la zona de transferencia (36) y la zona de salida (34) del horno (28) de la instalación (10), el recinto (52) en especial alrededor de la rueda (44) una zona periférica (54) en U que, extendiéndose desde la zona de alimentación (40) hasta la zona de evacuación (48), comprende sucesivamente una primera zona (Z1), llamada lateral derecha, una segunda zona (Z2), llamada trasera, una tercera zona (Z3), lateral izquierda, comprendiendo la instalación (10) un sistema (70) de soplado de aire filtrado en el interior del recinto (52) para establecer en su interior una sobrepresión proyectándole un flujo (F) de aire caracterizado por el hecho de que el flujo de aire es introducido selectivamente en al menos la primera zona (Z1) correspondiente a la zona del volumen interior del recinto (52) en la cual se origina una corriente de aire (C) inducida por la rotación de la rueda (44), estando dicha primera zona (Z1) comprendida longitudinalmente entre una parte lateral de la rueda (44) que lleva los moldes (46) y una pared (56) del recinto (52) situada enfrente, y que se extiende por un lado transversalmente hacia atrás a partir de la zona de alimentación (40) de la unidad de moldeado (42) y, por otro lado, verticalmente desde el suelo (66) hasta el techo (68) del recinto (52), de manera que la corriente de aire (C) provocada por la rotación de la rueda (44) esté constituida por dicho aire filtrado para evitar los riesgos de contaminaciones particulares llevadas por el aire, en particular la contaminación de las preformas (14) en la zona de salida (34) del horno (28)
Tipo: Patente Europea. Resumen de patente/invención. Número de Solicitud: E08154668.
Solicitante: SIDEL PARTICIPATIONS.
Nacionalidad solicitante: Francia.
Dirección: AVENUE DE LA PATROUILLE DE FRANCE 76930 OCTEVILLE SUR MER FRANCIA.
Inventor/es: QUETEL, FRANCOIS, ADRIANSENS, ERIC.
Fecha de Publicación: .
Fecha Solicitud PCT: 17 de Abril de 2008.
Fecha Concesión Europea: 22 de Septiembre de 2010.
Clasificación Internacional de Patentes:
- B29C49/46 TECNICAS INDUSTRIALES DIVERSAS; TRANSPORTES. › B29 TRABAJO DE LAS MATERIAS PLASTICAS; TRABAJO DE SUSTANCIAS EN ESTADO PLASTICO EN GENERAL. › B29C CONFORMACIÓN O UNIÓN DE MATERIAS PLÁSTICAS; CONFORMACIÓN DE MATERIALES EN ESTADO PLÁSTICO, NO PREVISTA EN OTRO LUGAR; POSTRATAMIENTO DE PRODUCTOS CONFORMADOS, p. ej. REPARACIÓN (fabricación de preformas B29B 11/00; fabricación de productos estratificados combinando capas previamente no unidas para convertirse en un producto cuyas capas permanecerán unidas B32B 37/00 - B32B 41/00). › B29C 49/00 Moldeo por soplado, es decir, soplando una preforma o un parisón en un molde por obtener la forma deseada; Aparatos a este efecto. › caracterizado por la utilización de un medio particular o de un fluido de soplado que no sean el aire.
Clasificación PCT:
- B29C49/46 B29C 49/00 […] › caracterizado por la utilización de un medio particular o de un fluido de soplado que no sean el aire.
Países PCT: Austria, Bélgica, Suiza, Alemania, Dinamarca, España, Francia, Reino Unido, Grecia, Italia, Liechtensein, Luxemburgo, Países Bajos, Suecia, Mónaco, Portugal, Irlanda, Eslovenia, Finlandia, Rumania, Chipre, Lituania, Letonia, Ex República Yugoslava de Macedonia, Albania.
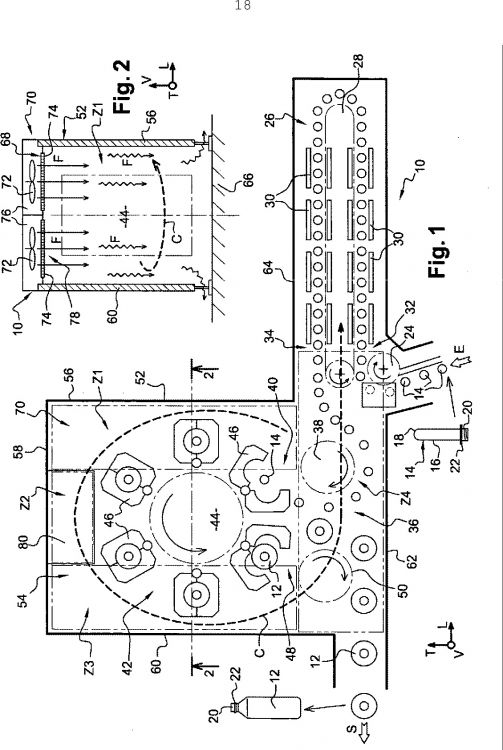
Fragmento de la descripción:
La presente invención se refiere a una instalación para la fabricación de recipientes que comprende un recinto de protección dotado de un sistema de soplado de aire filtrado. [0002] La invención se refiere más especialmente a una instalación para la fabricación de recipientes, en especial de botellas, por soplado o por estirado-soplado a partir de una preforma de material termoplástico, comprendiendo la instalación al menos:
- un dispositivo de alimentación con preformas destinado a alimentar con preformas una entrada de la instalación, -una unidad de acondicionamiento térmica que comprende al menos un horno que comprende medios de calefacción de las preformas que están dispuestas entre una zona de entrada en la cual las preformas son llevadas por el dispositivo de alimentación y una zona de salida que desemboca en una zona, llamada de transferencia, de la instalación, -un primer dispositivo de transferencia el cual, dispuesto en la zona de transferencia, está destinado a transferir las preformas acondicionadas térmicamente desde la zona de salida del horno hasta una zona, llamada de alimentación, de una unidad de moldeado, -comprendiendo la unidad de moldeado una rueda dotada de una pluralidad de moldes repartidos circunferencialmente y de medios asociados de soplado o de estirado-soplado, siendo la rueda accionada para girar de manera que cada molde recorre un ciclo de transformación desde dicha zona de alimentación hasta una zona, llamada de evacuación, -un segundo dispositivo de transferencia el cual, dispuesto en la zona de transferencia, está destinado a transferir los recipientes obtenidos desde la zona de evacuación de la unidad de moldeado hasta una salida de la instalación, y -al menos un recinto de protección que forma un cajón dispuesto para envolver al menos a la unidad de moldeado, la zona de transferencia y la zona de salida del horno de la instalación, delimitando el recinto en especial alrededor de la rueda una zona periférica en "U" que, extendiéndose desde la zona de alimentación hasta la zona de evacuación, comprende sucesivamente una primera zona, llamada lateral derecha, una segunda zona, llamada trasera, una tercera zona, lateral izquierda.
Se conocen numerosas instalaciones de este tipo para la fabricación de recipientes (ver por ejemplo el documento FR 2 766 121 A) en las cuales el recinto de protección comprende generalmente unas paredes verticales y al menos una pared horizontal que hace de techo para formar un cajón dispuesto para envolver al menos a la unidad de moldeado, la zona de transferencia y la zona de salida del horno de la instalación. [0004] El recinto de protección está en especial destinado a asegurar una separación física "hombre-máquina" por razones de seguridad de funcionamiento, así como un aislamiento acústico con el fin de respetar la normativa en vigor. [0005] Este tipo de recinto no es por ello estanco y existe una posible circulación de aire, aunque reducida, entre el entorno exterior y el volumen interior delimitado por el recinto. Sin embargo, el aire en libre circulación puede ser portador de contaminaciones particulares, tales como gérmenes, esporas o bacterias. [0006] De manera conocida, la instalación comprende generalmente medios de esterilización de las preformas que están destinados a descontaminar las preformas antes y/o durante su acondicionamiento térmico en el horno pero no comprende en cambio medios de esterilización o de aseptización particulares que estén asociados a la unidad de soplado. [0007] Efectivamente, las preformas son sopladas mediante aire estéril y cada preforma se encuentra, en el transcurso del ciclo de su transformación en recipiente, introducida en el interior de un molde que por lo tanto la aísla cerrándose y la protege de los riesgos de contaminaciones particulares llevadas por el aire. [0008] Así, es constante para un experto en la materia que las preformas no queden expuestas a unos riesgos de contaminaciones en esta parte de la instalación y la parte de la instalación de fabricación de recipientes situada aguas abajo del horno queda entonces usualmente desprovista de medios de esterilización o de aseptización particulares. [0009] Sin embargo, en contra de los prejuicios del experto en la materia, se ha constatado que los recipientes obtenidos con las instalaciones de última generación que funcionan con elevadas cadencias presentaban de manera sorprendente tasas de contaminación particulares superiores a los valores de umbral que se solían constatar habitualmente y, sin embargo, sin que el origen de estas contaminaciones haya sido explicada. [0010] Esta es la razón por la cual, el Solicitante ha procedido a unos estudios y ensayos con el fin de establecer su origen. Obviamente, la hipótesis según la cual la contaminación de las preformas tendría por origen una deficiencia de los medios de esterilización ha quedado descartada, siendo necesario por lo tanto buscar el origen de estas tasas de contaminación en otro sitio. [0011] Unos ensayos llevados a cabo por el Solicitante le han permitido por un lado constatar que la contaminación particular de las preformas sobrevenía de manera sorprendente aguas arriba de la zona de alimentación, en particular en la zona de salida del horno y, por otro lado, establecer una correlación entre el aumento de la tasa de contaminación y la utilización de velocidad de rotación elevada de la rueda de la unidad de moldeado/ soplado. [0012] Se recordará al respecto que, para estas instalaciones, las cadencias de producción no han cesado de aumentar, alcanzando actualmente la velocidad de rotación de la rueda de la unidad de soplado unas velocidades del orden de 20 a 40 tours / minuto para una rueda que presenta un diámetro comprendido entre 1 y 4 metros. [0013] Por lo tanto, en las instalaciones que funcionan a cadencias muy elevadas, la rueda provoca por su velocidad de rotación fenómenos aerodinámicas considerables en el interior del recinto. [0014] Unos estudios de estos fenómenos han permitido en especial al Solicitante poner de manifiesto que, en funcionamiento a cadencias elevadas, la rueda actúa como un ventilador que provoca una corriente de aire considerable, corriente de aire que recorre sucesivamente la zona periférica que envuelve a la rueda, luego la zona de transferencia y finalmente la zona de salida del horno antes de ser mayoritariamente evacuada fuera de la instalación por la parte superior abierta del horno. [0015] De este modo el Solicitante ha podido establecer que el origen de las contaminaciones particulares estaba directamente relacionada con la corriente de aire provocada por la rotación de la rueda a hautes velocidades. [0016] Efectivamente, las partículas tales como los gérmenes, bacterias, etc. son entonces susceptibles de ser transportadas por esta corriente de aire desde la parte de la instalación provista de la unidad de moldeado/ soplado y los dispositivos de transferencia hasta el horno cuya parte superior forma una chimenea por la cual se evacua mayoritariamente la corriente de aire. [0017] Esta es la razón por la cual, tanto el cuerpo como el cuello de la preforma son en particular susceptibles de ser contaminados en la zona de salida del horno, cuando las preformas que desfilan desde aguas arriba hacia aguas abajo son sucesivamente lamidas por la corriente de aire susceptible de ser portados de las contaminaciones particulares. [0018] La presente invención se propone en especial resolver los inconvenientes precitados y muy especialmente remediar los riesgos de contaminaciones particulares llevadas por el aire por la corriente de aire provocada por la rotación a elevadas velocidades de la rueda de la unidad de moldeado. [0019] Con este objetivo, la invención propone una instalación para la fabricación de recipientes del tipo descrito anteriormente, caracterizada por el hecho de que la instalación comprende un sistema de soplado de aire filtrado en el interior del recinto para establecer en su interior una sobrepresión proyectándole un flujo de aire que es introducido selectivamente en al menos dicha primera zona de manera que la corriente de aire provocada por la rotación de la rueda esté constituida por dicho aire filtrado para evitar los riesgos de contaminaciones particulares llevadas por el aire, en particular la contaminación de las preformas en la zona de salida del horno. [0020] Según la invención, la primera zona Z1 corresponde a la zona del volumen interior del recinto que se extiende transversalmente hacia atrás a partir de la zona de alimentación de la unidad de moldeado, que se extiende verticalmente desde el suelo hasta el techo del recinto y que está comprendida longitudinalmente entre una parte lateral de la rueda que lleva los moldes y la pared del recinto situada enfrente, siendo...
Reivindicaciones:
1. Instalación (10) para la fabricación de recipientes (12), en especial de botellas, por soplado o por estirado-soplado a partir de una preforma (14) de material termoplástico, que comprende al menos:
- un dispositivo (24) de alimentación con preformas destinado a alimentar con preformas una entrada (E) de la instalación (10), -una unidad de acondicionamiento térmica (26) que comprende al menos un horno
(28) que comprende medios de calefacción (30) de las preformas (14) que están dispuestas entre una zona de entrada (32) en la cual las preformas (14) son llevadas por el dispositivo de alimentación (24) y una zona de salida (34) que desemboca en una zona (36), llamada de transferencia, de la instalación (10), -un primer dispositivo de transferencia (38) el cual, dispuesto en la zona de transferencia (36), está destinado a transferir las preformas (14) acondicionadas térmicamente desde la zona de salida (34) del horno (28) hasta una zona (40), llamada de alimentación, de una unidad de moldeado (42), -comprendiendo la unidad de moldeado (42) una rueda (44) dotada de una pluralidad de moldes (46) repartidos circunferencialmente y medios asociados de soplado o de estirado soplado, estando la rueda (44) accionada para girar de manera que cada molde
(46) recorre un ciclo de transformación desde dicha zona de alimentación (40) hasta una zona (48), llamada de evacuación, -un segundo dispositivo de transferencia (50) el cual, dispuesto en la zona de transferencia (36), está destinado a transferir los recipientes (12) obtenidos desde la zona de evacuación (48) de la unidad de moldeado (42) hasta una salida (S) de la instalación (10), y -al menos un recinto de protección (52) que forma un cajón dispuesto para envolver al menos a la unidad de moldeado (42), delimitando la zona de transferencia (36) y la zona de salida (34) del horno (28) de la instalación (10), el recinto (52) en especial alrededor de la rueda (44) una zona periférica (54) en "U" que, extendiéndose desde la zona de alimentación (40) hasta la zona de evacuación (48), comprende sucesivamente una primera zona (Z1), llamada lateral derecha, una segunda zona (Z2), llamada trasera, una tercera zona (Z3), lateral izquierda, comprendiendo la instalación (10) un sistema (70) de soplado de aire filtrado en el interior del recinto (52) para establecer en su interior una sobrepresión proyectándole un flujo (F) de aire caracterizado por el
hecho de que el flujo de aire es introducido selectivamente en al menos la primera zona (Z1) correspondiente a la zona del volumen interior del recinto (52) en la cual se origina una corriente de aire (C) inducida por la rotación de la rueda (44), estando dicha primera zona (Z1) comprendida longitudinalmente entre una parte lateral de la rueda (44) que lleva los moldes (46) y una pared (56) del recinto (52) situada enfrente, y que se extiende por un lado transversalmente hacia atrás a partir de la zona de alimentación (40) de la unidad de moldeado (42) y, por otro lado, verticalmente desde el suelo (66) hasta el techo (68) del recinto (52), de manera que la corriente de aire (C) provocada por la rotación de la rueda (44) esté constituida por dicho aire filtrado para evitar los riesgos de contaminaciones particulares llevadas por el aire, en particular la contaminación de las preformas (14) en la zona de salida (34) del horno (28).
2. Instalación (10) según la reivindicación 1, caracterizada por el hecho de que el sistema de soplado de aire (70) es capaz de proyectar un flujo (F) de aire filtrado en la segunda zona (Z2) y/o la tercera zona (Z3) del recinto (52) que, complementarios de la primera zona (Z1), definen la zona periférica (54) que envuelve a la rueda (44).
3. Instalación (10) según cualquiera de las reivindicaciones 1 ó 2, caracterizada por el hecho de que el sistema de soplado de aire (70) es capaz de proyectar un flujo (F) de aire filtrado en una cuarta zona (Z4) del recinto (52) que comprende al menos la zona de transferencia (36) y la zona de salida (34) del horno (28).
4. Instalación (10) según cualquiera de las reivindicaciones 1 a 3, caracterizada por el hecho de que el sistema de soplado de aire (70) es capaz de proyectar permanentemente un flujo (F) de aire filtrado o estéril en todo o parte de las zonas (Z1, Z2, Z3, Z4) del recinto (52), independientemente de la puesta en rotación de la rueda (44), para preservar el grado de higiene en el interior del recinto (52) manteniendo en su interior una sobrepresión cuando la rueda (44) está parada por un lado, y, evitar la contaminación particular de la corriente de aire (C) provocada, en funcionamiento, por la rotación de la rueda (44) que actúa como un ventilador por otro lado, dicha corriente de aire (C) constituido mayoritariamente por dicho aire filtrado impulsado por el sistema (70) que recorre sucesivamente en primer lugar la zona periférica (54) constituida por dichas zonas primera, segunda y tercera (Z1), (Z2), y (Z3) luego la zona de transferencia (36) y finalmente la zona de salida (34) del horno (28).
5. Instalación (10) según cualquiera de las reivindicaciones anteriores, caracterizada por el hecho de que el sistema de soplado de aire (70) comprende medios de ventilación (72) asociados a unos medios de filtración (74) que están destinados a filtrar el aire antes de su proyección en el interior del recinto (52).
6. Instalación (10) según la reivindicación 5, caracterizada por el hecho de que los medios de filtración (74) del sistema (70) están constituidos por al menos un filtro de tipo « ULPA » o « HEPA ».
7. Instalación (10) según cualquiera de las reivindicaciones anteriores, caracterizada por el hecho de que el sistema de soplado de aire (70) comprende al menos un elemento (76) que está montado en el exterior del recinto (52) sobre al menos una de las paredes verticales (56, 58, 60, 62) y/o la pared horizontal (68) que hace de techo, comprendiendo el recinto (52) unas aberturas (78) para permitir el soplado del flujo (F) de aire filtrado según un flujo inicialmente laminar que fluye globalmente verticalmente de arriba abajo.
8. Instalación (10) según la reivindicación 7, caracterizada por el hecho de que los elementos (76) del sistema de soplado de aire (70) están integrados estructuralmente en el recinto (52) para formar la pared (68) que constituye el techo.
9. Instalación (10) según cualquiera de las reivindicaciones anteriores, en la cual el recinto (52) comprende una esclusa (80) destinada a permitir a un operador acceder al interior del recinto (52) desde el exterior de la instalación (10), en especial con vistas a proceder a unas operaciones sobre la rueda (44) tales como ajustes o cambios de molde (46), caracterizada por el hecho de que el sistema de soplado de aire (70) es capaz de proyectar selectivamente un flujo (F) de aire filtrado en el interior de la esclusa (80) para evitar cualquier contaminación externa del volumen interior delimitado por el recinto (52) cuando se utiliza la esclusa (80) se utiliza.
10. Instalación (10) según la reivindicación 9, caracterizada por el hecho de que la esclusa (80) está dispuesta en la segunda zona (Z2) de la zona periférica (54) que está situada detrás de la rueda (44) y diametralmente opuesta a la zona de transferencia (36).
Patentes similares o relacionadas:
Línea y método de embotellado, del 8 de Julio de 2020, de SACMI COOPERATIVA MECCANICI IMOLA SOCIETA' COOPERATIVA: Línea de embotellado de ciclo continuo para recipientes de material termoplástico, que comprende: - al menos una unidad de moldeo para la fabricación de preformas […]
Método y aparato para esterilizar una botella, del 3 de Junio de 2020, de DAI NIPPON PRINTING CO., LTD.: Un método para esterilizar una botella , que comprende las operaciones de: gasificar una solución de peróxido de hidrógeno, descargar desde una boquilla un […]
Método y dispositivo para fabricar botellas, del 25 de Marzo de 2020, de DAI NIPPON PRINTING CO., LTD.: Un método para fabricar una botella esterilizada , que comprende las etapas de: esterilizar bacterias que se adhieren a una preforma hecha […]
Inyector de fluido y procedimiento para fabricar cuerpos huecos mediante la técnica de inyección de fluido, del 4 de Septiembre de 2019, de Westphal, Friedrich: Inyector de fluido para fabricar cuerpos huecos mediante la técnica de inyección de fluido, a través del que una mezcla de fases múltiples en forma de una niebla pulverizada […]
Línea de embotellado y método, del 25 de Octubre de 2017, de SACMI COOPERATIVA MECCANICI IMOLA SOCIETA' COOPERATIVA: Una línea de embotellado de ciclo continúo para recipientes de material termoplástico, que comprende: - al menos 5 una unidad de moldeo para fabricar […]
Línea y procedimiento de embotellado, del 15 de Junio de 2016, de SACMI COOPERATIVA MECCANICI IMOLA SOCIETA' COOPERATIVA: Una línea de embotellado de ciclo continuo para envases de material termoplástico, que comprende: - una unidad de moldeo para fabricar parisones de material […]
Método y planta para la producción, el llenado y el cierre de contenedores, del 6 de Noviembre de 2013, de GEA PROCOMAC S.P.A: Planta para la producción, el llenado y el cierre de contenedores con tecnología aséptica, que comprende:
- al menos una unidad operativa para la esterilización […]
Procedimiento de esterilización de preformas e instalación para la producción de botellas esterilizadas a partir de estas preformas, del 1 de Octubre de 2013, de SIDEL PARTICIPATIONS: Procedimiento de esterilización de una preforma de material plástico destinada a moldearse, en particular mediante soplado, en una instalación (10, […]