METODO DE PRODUCCION DE UN PRODUCTO FORMADO DE MATERIAL COMPUESTO REFORZADO CON FIBRAS.
Método de producción de un artículo moldeado de un material compuesto reforzado con fibras moldeando simultáneamente una pluralidad de láminas de material preimpregnado cortadas en una forma predeterminada,
caracterizado el método por incluir las etapas de:
(1) formar una pluralidad de muescas o cortes en los materiales preimpregnados respectivos de modo que se forma al menos un conjunto de una aleta separada parcialmente y una parte residual para cada material preimpregnado;
(2) disponer los materiales preimpregnados respectivos en partes predeterminadas de una matriz para prensa usando aletas parcialmente separadas de los materiales preimpregnados como piezas de colocación;
(3) conformar una forma tridimensional deseada prensando las aletas parcialmente separadas de los materiales preimpregnados respectivos; y
(4) conformar una forma tridimensional deseada como un todo solapando partes de borde de extremo de partes residuales sobre las aletas parcialmente separadas y prensándolas
Tipo: Resumen de patente/invención. Número de Solicitud: W03010516JP.
Solicitante: MITSUBISHI RAYON CO., LTD..
Nacionalidad solicitante: Japón.
Dirección: 6-41, KONAN 1-CHOME, MINATO-KU,TOKYO 108-8506.
Inventor/es: ITOU, AKIHIRO, C/O TOYOHASHI PLANTS, TAKANO,TSUNEO C/O TOYOHASHI PLANTS, NUMATA,KIHARU C/O TOYOHASHI PLANTS, TAGUCHI,MASATO C/O TOYOHASHI PLANTS, MURAMATSU,JUNNICHI C/O TOYOHASHI PLANTS.
Fecha de Publicación: .
Fecha Concesión Europea: 4 de Noviembre de 2009.
Clasificación Internacional de Patentes:
- B29C70/34 TECNICAS INDUSTRIALES DIVERSAS; TRANSPORTES. › B29 TRABAJO DE LAS MATERIAS PLASTICAS; TRABAJO DE SUSTANCIAS EN ESTADO PLASTICO EN GENERAL. › B29C CONFORMACIÓN O UNIÓN DE MATERIAS PLÁSTICAS; CONFORMACIÓN DE MATERIALES EN ESTADO PLÁSTICO, NO PREVISTA EN OTRO LUGAR; POSTRATAMIENTO DE PRODUCTOS CONFORMADOS, p. ej. REPARACIÓN (fabricación de preformas B29B 11/00; fabricación de productos estratificados combinando capas previamente no unidas para convertirse en un producto cuyas capas permanecerán unidas B32B 37/00 - B32B 41/00). › B29C 70/00 Conformación de materiales compuestos, es decir, materiales plásticos con refuerzos, cargas o partes preformadas, p. ej. inserciones. › conformación o impregnación por compresión.
- B29C70/34B
- B29C70/54C
Clasificación PCT:
- B29C70/34 B29C 70/00 […] › conformación o impregnación por compresión.
- B29K105/06 B29 […] › B29K SISTEMA DE INDEXACION ASOCIADO A LAS SUBCLASES B29B, B29C O B29D, RELATIVO A LAS MATERIAS A MOLDEAR O MATERIALES DE REFUERZO, CARGAS O PREFORMADAS, p. ej. INSERCIONES. › B29K 105/00 Presentación, forma o estado de la materia moldeada. › que contienen elementos de refuerzo, cargas o elementos insertos.
- B29L31/30 B29 […] › B29L SISTEMA DE INDEXACION ASOCIADO A LA SUBCLASE B29C, RELATIVO A OBJETOS PARTICULARES. › B29L 31/00 Otros objetos particulares. › Vehículos, p. ej. barcos o aviones o partes constitutivas de los mismos.
- B29L31/52 B29L 31/00 […] › Equipos de deporte; Juguetes (B29L 31/54 tiene prioridad).
Clasificación antigua:
- B29C70/68 B29C 70/00 […] › por incorporación o moldeo de partes preformadas, p. ej. inserciones o capas.
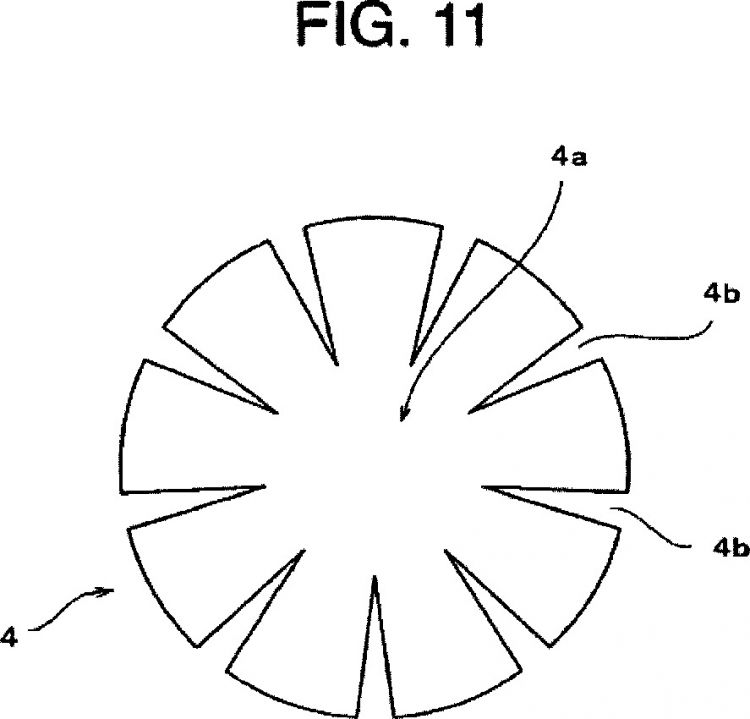
Fragmento de la descripción:
Método de producción de un producto formado de material compuesto reforzado con fibras.
Campo técnico
La invención se refiere a un método de producción de un artículo moldeado tridimensional de un material compuesto reforzado con fibras, y particularmente a un método de producción de un artículo moldeado de un material compuesto reforzado con fibras que es adecuado para producir de manera eficaz un artículo moldeado con una forma tridimensional con una alta curvatura y un buen aspecto usando una pluralidad de materiales preimpregnados.
Técnica anterior
De manera convencional, para conformar un artículo moldeado de un material compuesto reforzado con fibras con una forma tridimensional tal como una forma de tipo recipiente usando material preimpregnado obtenido impregnando una fibra de refuerzo con una resina de matriz, en el caso de que la forma tridimensional sea una forma moderadamente proyectada o rebajada con una pequeña curvatura, puede conformarse fácilmente prensando y extendiendo el material preimpregnado por ambos lados mediante una matriz para prensa que tiene una forma deseada.
Por ejemplo, en un método de producción de un palo de golf tal como se da a conocer en la solicitud de patente japonesa abierta a consulta por el público n.º 6-98933 (documento de patente 1), cuando se moldea preliminarmente una parte de una cabeza de un palo de golf con una forma tridimensional, la parte de la cabeza se divide en una pluralidad de partes y las partes respectivas se moldean prensando material preimpregnado cortado en formas predeterminadas. Las partes respectivas de la cabeza moldeada preliminarmente de esta manera y una varilla preliminarmente moldeada se insertan en una matriz de moldeo hueca, se aplica presión a estos artículos preliminarmente moldeados desde el lado interno de los artículos para calentarlos y moldearlos. Por consiguiente, la varilla y las partes respectivas de la cabeza se juntan y se unen para producir un palo de golf.
Sin embargo, en el caso en el que un artículo moldeado tiene una forma no uniforme con una alta curvatura, es inevitable que, para un método de producción de un artículo moldeado tridimensional moldeando en prensa material preimpregnado usando una matriz para prensa, se formen arrugas moldeando en prensa un material preimpregnado de tipo lámina en una cara de matriz para prensa que tiene de manera similar una cara no uniforme con una alta curvatura. Por tanto, en el caso del moldeo de una forma tridimensional con una alta curvatura, se forman previamente muescas o cortes en los materiales preimpregnados, y los materiales preimpregnados se laminan y moldean de tal manera que las partes de borde de extremo de las muescas o los cortes se superponen de modo que no se forman arrugas.
Por ejemplo, en el caso de conformar una forma semiesférica, tal como se ilustra en la figura 10, se corta en primer lugar el material preimpregnado para dar una forma circular y, dejando una parte central 3a de un material preimpregnado circular 3, se forma radialmente una pluralidad de muescas 3b a intervalos iguales, o alternativamente, tal como se ilustra en la figura 11, dejando una parte central 4a de un material preimpregnado circular 4, se forma radialmente una pluralidad de cortes 4b a intervalos iguales. Sucesivamente, teniendo las partes centrales 3a, 4a del material preimpregnado circular 3, 4 ajustadas en una parte superior de una matriz para prensa (una tercera matriz para prensa que va a describirse más adelante) 20 una parte proyectada semiesférica 20a tal como se ilustra en la figura 6 o teniendo ajustadas en la parte central inferior de una matriz para prensa (una cuarta matriz para prensa que va a describirse más adelante) 21 una parte cóncava semicircular 21a tal como se ilustra en la figura 7, el material preimpregnado se lamina en la matriz para prensa semiesférica 20 ó 21. En este caso, las partes de borde de extremo adyacentes de las muescas 3b o los cortes 4b se superponen. A continuación, se coloca la matriz para prensa homóloga y se lleva a cabo el moldeo en prensa para obtener un artículo moldeado con una forma semiesférica como un todo.
De manera convencional, la etapa de colocar el material preimpregnado en la matriz para prensa y solapar las partes de borde de extremo de las muescas o los cortes se lleva a cabo en general de manera manual. Por tanto, mediante el método mencionado anteriormente, se obtiene un artículo moldeado con calidad insuficiente en cuanto a la estabilidad y también insatisfactorio en cuanto a la uniformidad y productividad. Además, en el momento de colocar la matriz para prensa homóloga para llevar a cabo el moldeo en prensa, en el caso en el que el solapamiento de las partes de borde de extremo de las muescas o los cortes sea insuficiente o inestable, tiende a producirse arrugamiento en las partes de borde de extremo debido al arrastre de las mismas y también se desordena la disposición de la fibra de refuerzo. Por tanto, el método mencionado anteriormente se considera difícil de emplear para producir un artículo moldeado que se requiere que tenga una alta resistencia y un buen aspecto.
El documento EP 0319895 A2 da a conocer un método de conformado de un material laminado termoplástico que tiene un espesor de material laminado deseado, a partir de una pluralidad de capas de material compuesto termoplástico precurado al menos parcialmente, que comprende las etapas de: (a) colocar una pluralidad de capas de material compuesto termoplástico precurado parcialmente, no pegajoso, una encima de otra, (b) colocar una bolsa de vacío sobre la pila de láminas y herramienta de conformado, (c) aplicar presión a la bolsa de vacío para reducir el volumen de la pila de láminas, (d) tensionar la bolsa de vacío para eliminar las arrugas y (e) sellar la bolsa de vacío a la herramienta de conformado.
El documento FR 1092605 da a conocer también un método para conformar un artículo reforzado con fibras en una forma predeterminada prensando una pluralidad de láminas de material preimpregnado.
La invención se ha realizado de modo que se solucionan los problemas mencionados anteriormente, y un objeto de la invención es proporcionar un método de producción de un artículo moldeado de un material compuesto reforzado con fibras que tiene una forma tridimensional mediante prensado usando material preimpregnado cortado en una forma predeterminada, que es un método de producción estable y eficaz de un artículo moldeado de un material compuesto reforzado con fibras que tiene calidad uniforme sin arrugas, y proporcionar un artículo preliminarmente moldeado y un artículo moldeado acabado mediante el método.
Descripción de la invención
Una característica de la invención es básicamente un método de producción de un artículo moldeado de un material compuesto reforzado con fibras moldeando simultáneamente una pluralidad de láminas de material preimpregnado cortado en una forma predeterminada, incluyendo el método las etapas de:
(1) formar una pluralidad de muescas o cortes en los materiales preimpregnados respectivos de modo que se forma al menos un conjunto de una aleta separada parcialmente y una parte residual para cada material preimpregnado;
(2) disponer los materiales preimpregnados respectivos en partes predeterminadas de una matriz para prensa usando las aletas parcialmente separadas de los materiales preimpregnados como piezas de colocación;
(3) conformar una forma tridimensional deseada prensando las aletas parcialmente separadas de los materiales preimpregnados respectivos; y
(4) conformar una forma tridimensional deseada como un todo solapando partes de borde de extremo de las partes residuales en las aletas parcialmente separadas y prensándolas.
El artículo moldeado del material compuesto reforzado con fibras producido mediante el método de la invención incluye no sólo el producto final en sí sino también un artículo preliminarmente moldeado antes del conformado para que sea el producto final juntando y uniendo otra parte o conformándolo adicionalmente mediante otro método. Solapar y disponer una pluralidad de materiales preimpregnados en la invención significa que se superpone y se dispone una pluralidad de láminas cuando se fijan en una matriz y también incluye solapar de manera sucesiva las láminas mientras se coloca cada lámina una a una en la matriz; o laminar una pluralidad de materiales preimpregnados antes de que se fijen en una matriz y entonces colocar el material laminado resultante en la matriz mientras se coloca el material laminado.
Además, un método de formación respectiva...
Reivindicaciones:
1. Método de producción de un artículo moldeado de un material compuesto reforzado con fibras moldeando simultáneamente una pluralidad de láminas de material preimpregnado cortadas en una forma predeterminada, caracterizado el método por incluir las etapas de:
(1) formar una pluralidad de muescas o cortes en los materiales preimpregnados respectivos de modo que se forma al menos un conjunto de una aleta separada parcialmente y una parte residual para cada material preimpregnado;
(2) disponer los materiales preimpregnados respectivos en partes predeterminadas de una matriz para prensa usando aletas parcialmente separadas de los materiales preimpregnados como piezas de colocación;
(3) conformar una forma tridimensional deseada prensando las aletas parcialmente separadas de los materiales preimpregnados respectivos; y
(4) conformar una forma tridimensional deseada como un todo solapando partes de borde de extremo de partes residuales sobre las aletas parcialmente separadas y prensándolas.
2. Método de producción de un artículo moldeado de un material compuesto reforzado con fibras según la reivindicación 1, en el que, en la etapa (1), partes o toda la pluralidad de materiales preimpregnados se laminan para obtener un material laminado, y al material laminado se le hacen muescas o se corta para formar al menos un conjunto de la aleta parcialmente separada y la parte residual para cada material preimpregnado.
3. Método de producción de un artículo moldeado de un material compuesto reforzado con fibras según la reivindicación 1, en el que, en la etapa (1), a cada material preimpregnado se le hacen muescas o se corta para formar al menos un conjunto de la aleta parcialmente separada y la parte residual para el material preimpregnado.
4. Método de producción de un artículo moldeado de un material compuesto reforzado con fibras según una de las reivindicaciones 1 a 3, en el que las formas de las aletas parcialmente separadas formadas en los materiales preimpregnados respectivos son similares o coinciden entre sí, y las posiciones de las muescas o los cortes están desplazadas para los materiales preimpregnados respectivos.
5. Método de producción de un artículo moldeado de un material compuesto reforzado con fibras según una de las reivindicaciones 1 a 3, en el que las formas de las aletas parcialmente separadas formadas en los materiales preimpregnados respectivos son similares o coincidentes entre sí, y las muescas o los cortes se forman de tal manera que la anchura de la aleta parcialmente separada que va a disponerse en el lado de la cara cóncava del artículo moldeado mediante prensado no es más estrecha que la anchura de la aleta parcialmente separada que va a disponerse en el lado de la cara convexa con respecto a todas las aletas parcialmente separadas que van a superponerse en la misma posición.
6. Método de producción de un artículo moldeado de un material compuesto reforzado con fibras según una de las reivindicaciones 1 a 3, en el que, en la pluralidad de materiales preimpregnados que van a laminarse, las muescas o los cortes de los materiales preimpregnados respectivos que van a laminarse se forman de tal manera que los bordes de corte en el lado central están separados a una distancia de 2 mm o mayor uno de otro.
7. Método de producción de un artículo moldeado de un material compuesto reforzado con fibras según una de las reivindicaciones 1 a 3, en el que se hace que la anchura de las aletas parcialmente separadas formadas mediante las muescas o los cortes sea paralela o se estreche hacia la circunferencia externa.
8. Método de producción de un artículo moldeado de un material compuesto reforzado con fibras según una de las reivindicaciones 1 a 7, en el que una fibra de refuerzo que va a emplearse para el material preimpregnado es al menos un tipo de fibras seleccionado de fibra de carbono, fibra de vidrio y fibra orgánica.
9. Método de producción de un artículo moldeado de un material compuesto reforzado con fibras según una de las reivindicaciones 1 a 8, en el que la fibra de refuerzo que va a emplearse para el material preimpregnado es un material unidireccional de la fibra de refuerzo dispuesto de manera uniforme en una dirección o un material que tiene una estructura de material textil.
10. Método de producción de un artículo moldeado de un material compuesto reforzado con fibras según una de las reivindicaciones 1 a 9, en el que una resina de matriz que va a emplearse para el material preimpregnado es una resina termoendurecible.
11. Método de producción de un artículo moldeado de un material compuesto reforzado con fibras según la reivindicación 10, en el que la resina termoendurecible es una composición de resina epoxídica.
12. Método de producción de un artículo moldeado de un material compuesto reforzado con fibras según la reivindicación 11, en el que la composición de resina epoxídica comprende el siguiente componente A, componente B, componente C y componente D:
componente A: una resina epoxídica;
componente B: un compuesto de amina (componente B-1) que tiene al menos un átomo de azufre en una molécula y/o un producto de reacción (componente B-2) de un compuesto de amina que tiene al menos un átomo de azufre en una molécula con una resina epoxídica;
componente C: un compuesto de urea; y
componente D: una dicianodiamida.
13. Método de producción de un artículo moldeado de un material compuesto reforzado con fibras según la reivindicación 12, en el que el contenido en átomo de azufre y el componente C en la composición de resina epoxídica es del 0,2 al 7% en masa y del 1 al 15% en masa, respectivamente.
14. Método de producción de un artículo moldeado de un material compuesto reforzado con fibras según la reivindicación 12 ó 13, en el que el componente C es un material granular con un diámetro de partícula promedio de 150 µm o menor.
15. Método de producción de un artículo moldeado de un material compuesto reforzado con fibras según una de las reivindicaciones 10 a 14, en el que la resina termoendurecible no está curada y el artículo moldeado está preliminarmente moldeado.
16. Método de producción de un artículo moldeado de un material compuesto reforzado con fibras según una de las reivindicaciones 10 a 14, en el que la resina termoendurecible está curada.
17. Método de producción de un artículo moldeado de un material compuesto reforzado con fibras según la reivindicación 15, incluyendo el método la etapa (5) de:
calentar y presurizar adicionalmente el artículo preliminarmente moldeado de un material compuesto reforzado con fibras para el curado y el moldeo.
18. Método de producción de un artículo moldeado de un material compuesto reforzado con fibras según la reivindicación 17, en el que la etapa (5) se lleva a cabo mediante moldeo por compresión.
19. Método de producción de un artículo moldeado de un material compuesto reforzado con fibras según la reivindicación 18, en el que el moldeo por compresión se lleva a cabo a presión de moldeo de 20 kgf/cm2 o superior y tiempo de moldeo en 15 minutos.
20. Método de producción de un artículo moldeado de un material compuesto reforzado con fibras según la reivindicación 16 ó 19, en el que la temperatura de moldeo en el momento del moldeo por compresión es de 120ºC o superior.
21. Método de producción de un artículo moldeado de un material compuesto reforzado con fibras según una de las reivindicaciones 17 a 20, en el que una pluralidad de materiales preimpregnados laminados se unen y se curan.
Patentes similares o relacionadas:
Método para minimizar inconsistencias que aparecen sobre la superficie de un componente compuesto y una tira compuesta precurada, del 6 de Mayo de 2020, de THE BOEING COMPANY: Método para aplicar una tira compuesta precurada a un componente compuesto , comprendiendo la tira compuesta precurada una primera capa de material […]
Material de compuesto reforzado con fibra, del 6 de Mayo de 2020, de KABUSHIKI KAISHA TOYOTA JIDOSHOKKI: Un material de compuesto reforzado con fibra construido al impregnar una capa de paquete de fibras laminada formada al laminar una pluralidad de capas […]
Procedimiento de realización de preformas tridimensionales mediante el conformado de preformas iniciales con velos, del 26 de Febrero de 2020, de Coriolis Group: Procedimiento de realización de una preforma tridimensional que comprende - la realización de una preforma inicial que comprende varias capas superpuestas, […]
Procedimiento de fabricación de una cuaderna circundante de abertura para un fuselaje de aeronave, y cuaderna, del 1 de Enero de 2020, de AIRBUS OPERATIONS, S.L: Procedimiento de fabricación de una cuaderna circundante de abertura para un fuselaje de aeronave, comprendiendo el procedimiento las etapas de: […]
Un método para fabricar un cajón multilarguero de una sola pieza de material compuesto dentro de un molde cerrado, del 11 de Diciembre de 2019, de Leonardo S.p.A: Un método para fabricar un cajón multilarguero de una sola pieza hecho de material compuesto para aviones, que comprende dos paneles que están unidos por […]
Composición de resina epoxídica, material preimpregnado, material compuesto reforzado con fibra de carbono y métodos de fabricación para los mismos, del 11 de Diciembre de 2019, de TOHO TENAX CO., LTD: Composición de resina epoxídica, que comprende al menos: componente [A]; de 3 a 20 partes en masa de componente [B] con respecto a 100 partes en masa del componente […]
Procedimiento de conformado por estampado de un material compuesto termoplástico con refuerzo de fibras continuo, del 30 de Octubre de 2019, de DAHER AEROSPACE: Procedimiento para la realización de una pieza en forma de extrusión constituida por un material compuesto con refuerzo de fibras continuo, […]
Proceso de moldeo por compresión de un material compuesto con escamas cuasiisotrópicas, del 4 de Septiembre de 2019, de THE BOEING COMPANY: Un método para formar una pieza moldeada que tiene propiedades cuasiisotrópicas, comprendiendo el método: consolidar una primera capa formada […]