Método para estructurar la superficie de una chapa prensada o de una cinta sin fin.
Método para estructurar la superficie de una chapa metálica prensada (5) o de una cinta sin fin,
que consta de las siguientes etapas:
- colocación de la chapa prensada (5) o de la cinta sin fin sobre una mesa de trabajo (2) cuya superficie sea plana, para aplicar y endurecer una máscara (20),
- aplicación de una máscara formada por un barniz UV endurecible al menos en parte, para la pasivación parcial mediante un proceso de impresión digitalizado, empleando un dispositivo (1) adecuado
- que comprende un cabezal pulverizador (14) que se mueve en una pequeña distancia constante de 0,1 a 4 mm respecto a la superficie de las chapas prensadas (5) o de las cintas sin fin,
- irradiación, al menos parcial, de la máscara (20) con una fuente de luz UV inmediatamente después de la aplicación, preferiblemente dentro de un periodo de tiempo de hasta 60 segundos, para endurecerla,
- tratamiento químico de la superficie de la chapa prensada (5) o de la cinta sin fin.
Tipo: Patente Internacional (Tratado de Cooperación de Patentes). Resumen de patente/invención. Número de Solicitud: PCT/DE2007/000872.
Solicitante: HUECK ENGRAVING GMBH & CO. KG.
Nacionalidad solicitante: Alemania.
Dirección: HEIMHOLTZSTRASSE 9 41747 VIERSEN ALEMANIA.
Inventor/es: REICHERT,Jordi Fred.
Fecha de Publicación: .
Clasificación Internacional de Patentes:
- B29C59/00 TECNICAS INDUSTRIALES DIVERSAS; TRANSPORTES. › B29 TRABAJO DE LAS MATERIAS PLASTICAS; TRABAJO DE SUSTANCIAS EN ESTADO PLASTICO EN GENERAL. › B29C CONFORMACIÓN O UNIÓN DE MATERIAS PLÁSTICAS; CONFORMACIÓN DE MATERIALES EN ESTADO PLÁSTICO, NO PREVISTA EN OTRO LUGAR; POSTRATAMIENTO DE PRODUCTOS CONFORMADOS, p. ej. REPARACIÓN (fabricación de preformas B29B 11/00; fabricación de productos estratificados combinando capas previamente no unidas para convertirse en un producto cuyas capas permanecerán unidas B32B 37/00 - B32B 41/00). › Conformación de superficies, p. ej. grabado o estampado en relieve; Aparatos a este efecto.
- B44B5/02 B […] › B44 ARTES DECORATIVAS. › B44B MAQUINAS, APARATOS O UTILES PARA TRABAJOS DE ARTE, p. ej. PARA ESCULPIR, ENTALLAR, CINCELAR, PIROGRABAR O MARQUETEAR (decoración del cuero C14B). › B44B 5/00 Máquinas o aparatos para estampar motivos decorativos o marcas, p. ej. para acuñación de moneda (ondulación de chapas o de tubos metálicos, estampado combinado con operaciones de trabajo de chapas B21D; gofrado de materias plásticas o de sustancias en estado plástico en general B29C 59/02; estampado del papel o del cartón en general B31F 1/07; repujado de una forma de impresión B41C 1/08; máquinas de impresión para realizar operaciones de impresión combinadas con estampado en relieve B41F 19/02; máquinas de escribir o mecanismos de impresión adaptados para estampación B41J 3/38; aparatos o dispositivos para el sellado en hueco B41K 1/30, B41K 3/16; aparatos para estampación con medios para deformar el material a sellar B41K 3/36; estampado del cuero C14B 1/56). › Matrices; Accesorios.
- G03F1/00 FISICA. › G03 FOTOGRAFIA; CINEMATOGRAFIA; TECNICAS ANALOGAS QUE UTILIZAN ONDAS DISTINTAS DE LAS ONDAS OPTICAS; ELECTROGRAFIA; HOLOGRAFIA. › G03F PRODUCCION POR VIA FOTOMECANICA DE SUPERFICIES TEXTURADAS, p. ej. PARA LA IMPRESION, PARA EL TRATAMIENTO DE DISPOSITIVOS SEMICONDUCTORES; MATERIALES A ESTE EFECTO; ORIGINALES A ESTE EFECTO; APARELLAJE ESPECIALMENTE ADAPTADO A ESTE EFECTO (aparatos de composición fototipográfica B41B; materiales fotosensibles o procesos para la fotografía G03C; electrofotografía, capas sensibles o procesos a este efecto G03G). › Originales para la producción por vía fotomecánica de superficies texturadas, p. ej. mascaras, foto-mascaras o reticulas; Máscara en blanco o películas para ello; Contenedores especialmente adaptados a este efecto; Su preparación.
PDF original: ES-2379118_T3.pdf
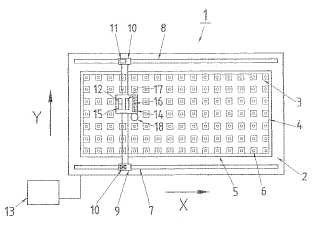
Fragmento de la descripción:
Método para estructurar la superficie de una chapa prensada o de una cinta sin fin La presente invención se refiere a un método para estructurar la superficie de una chapa prensada o de una cinta sin fin, que consiste en producir una estructura superficial, aplicando primero una máscara para la pasivación parcial mediante un dispositivo y a continuación un tratamiento químico de la superficie, así como a un dispositivo para llevar a cabo el método.
Según el estado técnico actual las chapas prensadas y las cintas sin fin se elaboran de manera que una chapa pretratada, por ejemplo mediante un proceso serigráfico o un recubrimiento fotosensible, seguido de un tratamiento corrosivo, recibe una estructura superficial. La impresión serigráfica se aplica sobre chapas de gran formato y éstas se someten seguidamente a un tratamiento corrosivo de la superficie. En este caso todas las áreas que forman la estructura superficial con relieve se cubren con una máscara, de manera que la superficie solo pueda ser corroída en las zonas atacadas directamente por el líquido corrosivo. Las zonas corroídas forman luego los valles del perfil de la estructura deseada. Después del tratamiento corrosivo se limpia la superficie y, sobre todo, se retira la máscara, para que la superficie pueda someterse a un proceso adicional de endurecimiento, por ejemplo de cromado duro, en etapas posteriores.
Como alternativa se puede usar un método fotográfico, aplicando primero una capa fotosensible que luego debe iluminarse según la máscara prevista para producir la estructura superficial. Después hay que revelar la capa fotográfica y entremedias se requieren extensas etapas de lavado, a fin de preparar y purificar la superficie para las siguientes etapas del proceso. Así, tras el revelado de la capa fotográfica se obtiene una máscara que puede usarse como plantilla del tratamiento corrosivo. Por tanto, en este método, primero se aplica una capa por toda la superficie, que luego se ilumina y seguidamente se libera de los componentes no fijados; y solo entonces puede utilizarse la máscara revelada para grabar una estructura. La reproducibilidad de la máscara así preparada es muy difícil y problemática, porque el positivo o negativo empleado para iluminar la capa fotosensible siempre debe colocarse exactamente en la misma posición respecto a dicha capa, cuando hay que realizar varias etapas sucesivas de iluminación y grabado para conseguir estructuras tridimensionales complejas sobre la superficie de una chapa prensada. Esto no es así, por ejemplo, cuando el positivo o el negativo empleado para iluminar la capa fotosensible se coloca directamente sobre ésta y no guarda exactamente la misma distancia respecto a ella en cada posición de la capa. En el método fotográfico la reproducibilidad de la aplicación de la máscara es de especial importancia para conseguir una imagen muy exacta. Las dificultades pueden aumentar cuando se trata de producir una estructura tridimensional mediante sucesivas etapas de iluminación y grabado y ello requiere la aplicación sucesiva de varias máscaras, con un tratamiento corrosivo entre cada aplicación de máscara. Por tanto la colocación exacta de las máscaras y el número necesario de ellas complican y encarecen mucho la elaboración de las chapas prensadas o de las cintas sin fin. La resolución de las máscaras aplicables depende mucho del proceso empleado y además se necesita un considerable número de etapas de trabajo, que requieren una manipulación laboriosa, sobre todo por el tamaño de las chapas prensadas o de las cintas sin fin.
También es sabido del estado técnico que en vez de un procedimiento serigráfico se puede preparar una máscara por aplicación de cera, que es químicamente resistente a los agentes corrosivos empleados y por tanto permite que se graben las zonas cuya superficie no está recubierta por la cera. En este método se usa un cabezal de impresión que proyecta la cera sobre la superficie a lo largo de un sistema de ejes X Y, para aplicar la estructura requerida mediante una serie de operaciones individuales. Por tanto en este procedimiento la máscara se aplica directamente sobre la chapa prensada, sin operaciones de iluminación, revelado y eliminación de las partes no reveladas de la capa. En principio los cabezales de impresión empleados pueden ser de forma parecida a los de una impresora de chorro de tinta, pero que en vez de una tinta proyecten una cera que se endurezca sobre la superficie de las chapas prensadas o de las cintas sin fin, de modo que luego pueda llevarse a cabo la grabación requerida. Aunque con este procedimiento del estado técnico se puede conseguir un enorme avance, en la práctica se ha demostrado que la eliminación de la capa de cera es muy problemática, ya que la cera no puede quitarse con un tratamiento químico y por tanto la limpieza de las chapas tras el proceso de grabado resulta sumamente difícil y solo puede efectuarse, por ejemplo, con un limpiador de alta presión. Este tipo elaboración también requiere mucho tiempo, pues si hay que aplicar sucesivamente varias capas de cera, intercalando un tratamiento corrosivo entre cada aplicación de máscara, para obtener, por ejemplo, una estructura profunda, no se alcanza ninguna ventaja especial. Las características de la cera limitan la exactitud y la finura de la estructura de la máscara, y en particular no es posible resolver estructuras finas. Los límites vienen determinados por la adhesión puramente física mediante humectación, pues, al proyectar la cera líquida caliente sobre la chapa prensada fría, la cera solidifica con demasiada rapidez y forma estructuras que humectan de manera incompleta, como "puntos de soldadura fríos". El calentamiento de la placa prensada tampoco da resultado, porque la cera líquida se escurre y disminuye la resolución alcanzable.
A través de la patente WO 01/17794 A1 se conoce un método para elaborar una superficie de una placa estampada, en el cual se usa barniz UV para aplicar una máscara. El barniz UV se endurece mediante una fuente de luz UV, de manera que pueda grabarse la placa estampada.
A través de la patente US 5, 495, 803 se conoce además un dispositivo que tiene la posibilidad de aplicar un barniz
UV, por ejemplo, sobre una superficie mecanizable de pequeño formato. En este dispositivo se mueve un cabezal de impresión mediante elementos de accionamiento en dirección x e y, de manera que permite aplicar una máscara sobre la superficie imprimible.
Partiendo de este estado técnico la presente invención tiene por objeto indicar un método y un dispositivo mediante los cuales se evitan las desventajas del estado técnico conocido y se mejora claramente la reproducibilidad y la resolución de las máscaras producidas.
Este planteamiento se resuelve, según la presente invención, mediante un método que consta de las siguientes etapas descritas a continuación:
- colocación de la chapa prensada o de la cinta sin fin sobre una mesa de trabajo cuya superficie sea plana, para aplicar y endurecer una máscara,
- aplicación de una máscara formada por un barniz UV endurecible al menos en parte, para la pasivación parcial mediante un proceso de impresión digitalizado, empleando un dispositivo adecuado,
- el cual comprende un cabezal pulverizador que se mueve en una pequeña distancia constante de 0, 1 a 4 mm respecto a la superficie de las chapas prensadas o de las cintas sin fin,
- irradiación, al menos parcial, de la máscara con una fuente de luz UV inmediatamente después de la aplicación, preferiblemente dentro de un periodo de tiempo de hasta 60 segundos, para endurecerla,
- tratamiento químico de la superficie de la chapa prensada o de la cinta sin fin.
De las reivindicaciones secundarias se desprenden otras formas de ejecución ventajosas.
Para aplicar el barniz UV se usa preferentemente un cabezal pulverizador provisto de varias boquillas que están dispuestas en forma de matriz y pueden controlarse individualmente. El propio cabezal puede desplazarse dentro de un plano en dirección X o Y, asistido por un procesador informático, en particular por un PC, siguiendo cualquier trayectoria deseada, de manera similar a un trazador de gráficos.
Según la presente invención el cabezal pulverizador se mantiene siempre a la misma distancia del substrato por medio de un servomotor, a fin de compensar las ligeras distorsiones que puede tener una gran placa prensada. Para ello el cabezal pulverizador se puede desplazar en altura, es decir en la dirección z. En este caso se procura dirigir el cabezal manteniendo una pequeña distancia de 0, 1 a 4 mm, preferiblemente... [Seguir leyendo]
Reivindicaciones:
1. Método para estructurar la superficie de una chapa metálica prensada (5) o de una cinta sin fin, que consta de las siguientes etapas:
- colocación de la chapa prensada (5) o de la cinta sin fin sobre una mesa de trabajo (2) cuya superficie sea plana, para aplicar y endurecer una máscara (20) ,
- aplicación de una máscara formada por un barniz UV endurecible al menos en parte, para la pasivación parcial mediante un proceso de impresión digitalizado, empleando un dispositivo (1) adecuado
- que comprende un cabezal pulverizador (14) que se mueve en una pequeña distancia constante de 0, 1 a 4 mm respecto a la superficie de las chapas prensadas (5) o de las cintas sin fin,
- irradiación, al menos parcial, de la máscara (20) con una fuente de luz UV inmediatamente después de la aplicación, preferiblemente dentro de un periodo de tiempo de hasta 60 segundos, para endurecerla,
- tratamiento químico de la superficie de la chapa prensada (5) o de la cinta sin fin.
2. Método según la reivindicación 1, caracterizado porque el barniz UV se precalienta antes de la aplicación y se aplica a temperatura constante, manteniéndolo preferiblemente a una temperatura de 50º C hasta 100º C, sobre todo de 65º C hasta 75º C.
3. Método según la reivindicación 1 o 2, caracterizado porque el barniz UV contiene pequeñas proporciones de disolvente.
4. Método según una de las reivindicaciones 1 a 3, caracterizado porque para aplicar el barniz UV se emplea un cabezal pulverizador (14) en forma de cabezal de boquillas.
5. Método según la reivindicación 4, caracterizado porque el cabezal pulverizador (14) lleva varias boquillas que están dispuestas en forma de una matriz y se regulan individualmente.
6. Método según la reivindicación 4 o 5, caracterizado porque se elige al azar una boquilla de la matriz para imprimir un punto de un motivo prefijado, de modo que esta boquilla, al pasar por encima de la zona de impresión, imprime el punto y luego más de una boquilla elegida aleatoriamente proyecta barniz UV sobre el mismo punto.
7. Método según una de las reivindicaciones 4 a 6, caracterizado porque el cabezal pulverizador (14) está diseñado de forma que puede dirigirse en la dirección x y/o y de un plano, así como en la dirección z perpendicular al plano, o bien porque el cabezal pulverizador (14) se mantiene fijo en una posición y solamente puede desplazarse en la dirección z, mientras que las chapas prensadas (5) o las cintas sin fin pueden moverse respecto al cabezal pulverizador (14) .
8. Método según una de las reivindicaciones 4 a 7, caracterizado porque el cabezal pulverizador (14) se mueve a una distancia de 0, 8 mm de las chapas prensadas o de las cintas sin fin, mientras un dispositivo automático de nivelación dirige el cabezal de las boquillas manteniendo la distancia escogida respecto a la chapa prensada (5) o la cintas sin fin.
9. Método según una de las reivindicaciones 4 a 8, caracterizado porque el cabezal pulverizador (14) forma la máscara aplicada (20) en varios pasos sucesivos.
10. Método según una de las reivindicaciones 4 a 9, caracterizado porque las boquillas del cabezal pulverizador
(14) están dispuestas de manera adyacente en dirección X e Y y el cabezal pulverizador (14) se mueve en dirección de un eje X e Y, de modo que las boquillas están reunidas funcionalmente en grupos de al menos dos boquillas y tras el proceso en la dirección del eje Y las boquillas y/o las chapas prensadas (5) o las cintas sin fin se mueven a una nueva posición respecto al eje X y el paso de avance del movimiento en la dirección del eje X corresponde a la anchura de la matriz de boquillas, menos o más la distancia respecto a boquillas vecinas de la matriz, dividida por el número de boquillas en una fila.
11. Método según una de las reivindicaciones 1 a 10, caracterizado porque hay una fuente de luz UV que emite exclusivamente la luz UV cuando el cabezal pulverizador está proyectando material para imprimir la máscara.
12. Método según una de las reivindicaciones 1 a 11, caracterizado porque se usa una máscara negra para la lámpara UV y/o una pantalla de lámpara, a fin de evitar reflexiones.
13. Método según una de las reivindicaciones 1 a 12, caracterizado porque se utiliza un filtro de luz para la lámpara UV que no deja pasar luz de onda corta, eligiendo el borde de absorción de manera que la luz pasante sea absorbida totalmente por el material de la chapa prensada (5) o de la cinta sin fin.
14. Método según una de las reivindicaciones 1 a 13, caracterizado porque las chapas prensadas (5) o las cintas sin fin se elaboran en una posición horizontal o vertical.
15. Método según una de las reivindicaciones 1 a 14, caracterizado porque las chapas prensadas (5) se aspiran al vacío.
16. Método según una de las reivindicaciones 1 a 15, caracterizado porque las chapas prensadas (5) o las cintas sin fin se someten a un tratamiento previo.
17. Método según una de las reivindicaciones 1 a 16, caracterizado porque para el tratamiento previo se realiza una limpieza mecánica y un lavado con isopropanol, etanol o alcohol y/o un tratamiento con una imprimación, por ejemplo con un compuesto orgánico de sililo.
18. Método según una de las reivindicaciones 1 a 17, caracterizado porque la superficie de las chapas prensadas (5) o de las cintas sin fin se corroe antes de aplicar la máscara.
19. Método según una de las reivindicaciones 1 a 18, caracterizado porque la chapa prensada se somete a un pretratamiento químico que produce una superficie mate para evitar la reflexión de la luz.
20. Método según una de las reivindicaciones 1 a 19, caracterizado porque para estructurar químicamente la superficie se usa una técnica de grabado.
21. Método según una de las reivindicaciones 1 a 20, caracterizado porque tras el proceso de grabado se elimina la máscara con un disolvente.
22. Método según la reivindicación 21, caracterizado porque la eliminación de la máscara se facilita con la ayuda de ultrasonidos.
23. Método según una de las reivindicaciones 1 a 22, caracterizado porque las chapas prensadas (5) o las cintas sin fin reciben un recubrimiento de acabado.
24. Método según una de las reivindicaciones 1 a 23, caracterizado porque el acabado de las chapas prensadas (5) o de las cintas sin fin consiste en cromar toda la superficie, preferentemente mediante un cromado duro, con carbono diamantino o con boruro de titanio.
25. Dispositivo para aplicar y endurecer una máscara de barniz curable por UV sobre una superficie metálica de una chapa prensada o de una cinta sin fin, de cara a un tratamiento superficial posterior, que comprende una mesa soporte (2) de superficie plana para las chapas prensadas o las cintas sin fin en proceso de elaboración, un cabezal pulverizador desplazable mediante una unidad de control (13) y una guía deslizante (10) para moverlo a cualquier posición dentro de un plano marcado por unas coordenadas x e y, así como unos elementos de accionamiento (11, 12, 15) para alcanzar la posición, de modo que el cabezal pulverizador consta de un cabezal de boquillas para la aplicación de un barniz curable por UV y va provisto de una fuente de luz UV que, una vez completada la aplicación de la máscara por secciones, irradia la sección recién aplicada, y de modo que el cabezal pulverizador se puede mover adicionalmente mediante un dispositivo nivelador en la dirección z perpendicular a la superficie definida por las coordenadas x e y, manteniendo una pequeña distancia constante de 0, 1 hasta 4 mm respecto a la superficie de las chapas prensadas o de las cintas sin fin.
26. Dispositivo según la reivindicación 25, caracterizado porque el cabezal pulverizador (14) lleva varias boquillas que están dispuestas en forma de una matriz y se pueden regular individualmente.
27. Dispositivo según la reivindicación 25 o 26, caracterizado porque el cabezal pulverizador (14) se conduce a una distancia de 0, 8 mm respecto a la superficie de las chapas prensadas (5) o de las cintas sin fin, con la ayuda de un dispositivo automático de nivelación.
28. Dispositivo según la reivindicación 25, 26 o 27, caracterizado porque el cabezal pulverizador (14) forma la máscara (20) mediante sucesivas aplicaciones.
29. Dispositivo según una de las reivindicaciones 24 a 28, caracterizado porque las boquillas del cabezal están dispuestas de manera adyacente en dirección X e Y y el cabezal pulverizador (14) se puede mover en la dirección de un eje X e Y, de modo que las boquillas están reunidas funcionalmente en grupos de al menos dos boquillas y tras el proceso en la dirección del eje Y las boquillas y/o las chapas prensadas (5) o las cintas sin fin se pueden mover hacia una nueva posición respecto al eje X y el paso de avance del movimiento en la dirección del eje X corresponde a la anchura de la matriz de boquillas, menos o más la distancia respecto a boquillas vecinas de la matriz (20) , dividida por el número de filas de grupos.
30. Dispositivo según una de las reivindicaciones 24 a 29, caracterizado porque el cabezal pulverizador (14) presenta un apantallamiento que evita el endurecimiento de la máscara (20) aplicada de manera incompleta, o de puntos individuales de la máscara, durante el proceso.
31. Dispositivo según una de las reivindicaciones 24 a 30, caracterizado porque la mesa soporte (2) se puede colocar, al menos aproximadamente, en una posición horizontal o vertical.
32. Dispositivo según una de las reivindicaciones 24 a 31, caracterizado porque la mesa soporte (2) presenta
una superficie plana (3) dividida en múltiples superficies parciales en cuyo interior hay orificios (6) para un equipo de aspiración al vacío.
33. Dispositivo según una de las reivindicaciones 24 a 32, caracterizado porque como fuente lumínica de UV se prevé una lámpara de vapor de mercurio, una lámpara de xenón o LEDs UV potentes, diodos láser o un láser. 10
34. Dispositivo según una de las reivindicaciones 24 a 33, caracterizado porque como fuente lumínica de UV se prevé un láser pulsado que solamente emite luz cuando el cabezal pulverizador proyecta material para imprimir la máscara.
35. Dispositivo según una de las reivindicaciones 24 a 34, caracterizado porque se prevé una máscara negra y/o una pantalla de lámpara para proteger el cabezal pulverizador y evitar reflexiones no deseadas de la luz hacia dicho cabezal.
36. Dispositivo según una de las reivindicaciones 24 a 35, caracterizado porque la fuente lumínica de UV o la lámpara de UV sigue al cabezal de impresión a cierta distancia o corre en sentido contrario a él, de manera que la fuente lumínica de UV o la lámpara de UV próxima al cabezal de impresión se desconecta cuando el cabezal y la fuente lumínica se encuentran.
Patentes similares o relacionadas:
Película de máscara para formar imágenes en relieve, del 9 de Enero de 2019, de Miraclon Corporation: Una película, que comprende: una lámina de soporte transparente y que tiene sobre ella, en orden: una capa transparente que tiene un grosor de desde […]
Una placa original de impresión flexográfica, del 6 de Septiembre de 2017, de TOYOBO CO., LTD.: Una placa original de impresión flexográfica fotosensible y revelable por agua, en la que están estratificados sucesivamente al menos un miembro de soporte, una capa de resina […]
Fabricación de placas de impresión flexográficas a partir de fotopolímeros, del 4 de Enero de 2017, de CHEMENCE, INC: Un negativo de chorro de tinta a base de disolvente, caracterizado porque se proporciona una película polimérica compatible con tinta basada […]
Método para hacer una imagen en relieve, del 21 de Septiembre de 2016, de EASTMAN KODAK COMPANY: Un método de hacer una imagen en relieve, comprendiendo el método: A) formar una imagen máscara formando regiones expuestas y no expuestas en una película filmada, […]
Proceso de prevención de curado de borde, del 15 de Octubre de 2014, de MACDERMID PRINTING SOLUTIONS, LLC: Un método para evitar el curado no deseado de los bordes de una placa de impresión fotosensible, comprendiendo el método las etapas de: a) proporcionar […]
Procedimiento que comprende irradiación UV-LED para la fabricación de placas de impresión flexográficas, del 9 de Julio de 2014, de FLINT GROUP GERMANY GMBH: Procedimiento para la fabricación de placas de impresión flexográficas, en el que se usa como material de partida un elemento de impresión flexográfico que […]
Método de prevención de curado prematuro de superficies de corte de un elemento de impresión fotosensible, elemento de impresión fotosensible que puede obtenerse mediante un método de este tipo, del 3 de Octubre de 2012, de MACDERMID PRINTING SOLUTIONS, LLC: Un método de prevención de curado prematuro de superficies de corte de un elemento de impresión fotosensible,comprendiendo el método las etapas […]
PROCEDIMIENTO PARA MOLDEAR SUPERFICIES DE MATERIALES CURABLES, del 25 de Julio de 2012, de UNIVERSIDAD DE EXTREMADURA: Procedimiento para moldear superficies de materiales curables. Se describe un procedimiento para moldear la superficie de materiales curables que comprende las etapas de: […]