Procedimiento de fabricación de una pieza con cuerpo hueco en material compuesto y pieza así obtenida.
Procedimiento de fabricación de una pieza con cuerpo hueco en material compuesto a partir de preformas (11,
12) que comprende las etapas sucesivas que prevén:
- disponer las preformas alrededor de un soporte (1) apropiado de manera que cada preforma (11, 12)presente unos bordes de unión (112, 113, 122, 123) que entran en contacto por recubrimiento con un bordede unión (122, 123, 112, 113) de otra preforma (12, 11) y mantener cada preforma (11, 12) sobre el soporte(1) gracias a unos medios de mantenimiento que comprenden una envolvente fibrosa (201, 202) aplicadasobre la preforma (11, 12) y apretándola sobre el soporte (1),
- unir entre sí los bordes de unión de cada preforma por costura;
- extraer el soporte e insertar en su lugar un noyo de moldeo antes de la colocación del conjunto en el interiorde un molde e inyección de resina según un procedimiento Resin Transfer Molding RTM/Liquid Resin InfusionLRI seguido de una polimerización de la resina.
Tipo: Patente Internacional (Tratado de Cooperación de Patentes). Resumen de patente/invención. Número de Solicitud: PCT/FR2009/050590.
Solicitante: AIRCELLE.
Nacionalidad solicitante: Francia.
Dirección: ROUTE DU PONT 8 76700 GONFREVILLE L''ORCHER FRANCIA.
Inventor/es: DESJOYEAUX,BERTRAND.
Fecha de Publicación: .
Clasificación Internacional de Patentes:
- B29B11/16 TECNICAS INDUSTRIALES DIVERSAS; TRANSPORTES. › B29 TRABAJO DE LAS MATERIAS PLASTICAS; TRABAJO DE SUSTANCIAS EN ESTADO PLASTICO EN GENERAL. › B29B PREPARACION O PRETRATAMIENTO DE MATERIAS A CONFORMAR; FABRICACION DE GRANULOS O DE PREFORMAS; RECUPERACION DE LAS MATERIAS PLASTICAS O DE OTROS CONSTITUYENTES DE MATERIALES DE DESECHO QUE CONTIENEN MATERIAS PLASTICAS. › B29B 11/00 Fabricación de preformas (B29C 61/06 tiene prioridad). › comprendiendo cargas o fibras de refuerzo.
- B29C70/48 B29 […] › B29C CONFORMACIÓN O UNIÓN DE MATERIAS PLÁSTICAS; CONFORMACIÓN DE MATERIALES EN ESTADO PLÁSTICO, NO PREVISTA EN OTRO LUGAR; POSTRATAMIENTO DE PRODUCTOS CONFORMADOS, p. ej. REPARACIÓN (fabricación de preformas B29B 11/00; fabricación de productos estratificados combinando capas previamente no unidas para convertirse en un producto cuyas capas permanecerán unidas B32B 37/00 - B32B 41/00). › B29C 70/00 Conformación de materiales compuestos, es decir, materiales plásticos con refuerzos, cargas o partes preformadas, p. ej. inserciones. › e impregnando los refuerzos en el molde cerrado, p. ej, moldeo por transferencia de resina [RTM].
PDF original: ES-2390750_T3.pdf
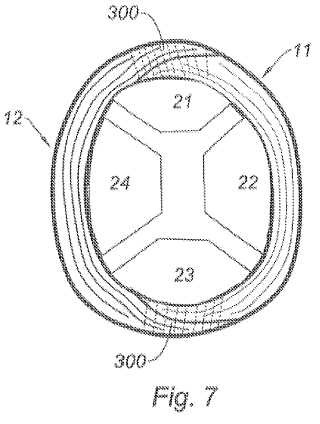
Fragmento de la descripción:
Procedimiento de fabricación de una pieza con cuerpo hueco en material compuesto y pieza así obtenida.
La presente invención se refiere a un procedimiento de fabricación de una pieza con cuerpo hueco de material compuesto.
La presente invención se refiere más particularmente a la realización de estructuras muy cargadas y que tienen un cuerpo principal hueco. Se podrán citar en particular la realización de bielas de tren de aterrizaje, boje, mástil de enganche de una góndola de turborreactor, poste de un turborreactor, etc.
Se conocen varios procedimientos para fabricar unas piezas con cuerpo hueco compuestas, en particular los procedimientos RTM/LRI (Resin Transfer Molding/Liquid Resin Infusion) y el procedimiento preimpregnado. Se conocen también unas técnicas de drapeado de pliegues o de arrollamiento filamentosos que pueden ser aplicadas a uno o al otro de los procedimientos citados.
En un procedimiento RTM/LRI, se posiciona un conjunto de elementos fibrosos de mantera particular alrededor de un soporte. Este conjunto de elementos fibrosos forma una preforma que, con su soporte, se coloca a continuación en un molde en cuyo interior se inyecta una resina, generalmente bajo vacío o a presión. La resina se polimeriza a continuación formando así un material compuesto rígido y ligero formado por fibras y por resina polimerizada.
El procedimiento RTM/LRI presenta una gran flexibilidad y permite la realización de piezas de geometría compleja. En efecto, como las fibras de los elementos fibrosos están inicialmente secas, se pueden colocar más fácilmente para adoptar la forma del soporte.
El procedimiento RTM/LRI presenta asimismo la ventaja de necesitar menos operaciones de ensamblaje puesto que esta posibilidad de realizar unas piezas de forma compleja permite evitar realizar varias piezas de forma menos compleja para ensamblarlas a continuación entre ellas.
Sin embargo, al estar los elementos fibrosos inicialmente secos, sus fibras también son más susceptibles de cambiar de orientación o presentar unos defectos de alineación antes del colado y polimerización de la resina.
Dado que en un material compuesto de este tipo la alineación de las fibras define y determina las líneas de transmisión de esfuerzos, en particular en compresión y en pandeo, se comprende que la presencia de defectos de alineación de las fibras en la pieza final tiene unas repercusiones negativas sobre las propiedades mecánicas de absorción y de transmisión de los esfuerzos de dicha pieza.
Se puede aportar una mejora a este defecto utilizando una preforma que incluya una parte muy pequeña de resina que sirve de fijador con el fin de reforzar la unión de las fibras entre sí, necesitando este procedimiento, además de la operación de adición del fijador, una operación de estufado de la preforma formada para que actúe este fijador.
En un procedimiento preimpregnado, los elementos fibrosos ya no están secos, sino pre-impregnados de resina por lo menos parcialmente polimerizada.
El hecho de que las fibras de estos elementos fibrosos estén ya impregnadas de resina limita en gran manera su movilidad y cambio de orientación.
Sin embargo, el procedimiento preimpregnado adolece de inconvenientes y no permite en particular o difícilmente la realización de piezas de geometría compleja, limitando la resina en gran manera la conformación de los elementos fibrosos. También es difícil por tanto obtener un buen grado de compresión de las fibras entre el soporte y el molde durante la polimerización final.
Por otra parte, un procedimiento de este tipo multiplica las etapas de fabricación puesto que los elementos fibrosos deben sufrir una preimpregnación antes del drapeado y eventualmente una prepolimerización parcial antes del conformado y polimerización final.
Existe por tanto un interés importante en perfeccionar los procedimientos RTM/LRI y proporcionar un procedimiento que permita conservar sus ventajas asegurando al mismo tiempo una buena orientación de las fibras, una buena compactación de estas en número importante.
Varios documentos de la técnica anterior han intentado ya resolver este problema.
El documento WO 2007/060306 describe un procedimiento para la fabricación de una biela de material compuesto a partir de una sola preforma seca conformada antes de colado de la resina. En este procedimiento, la preforma presenta unos bordes opuestos que presentan cada una uno superficie biselada complementaria creada durante su arrollamiento alrededor el soporte, estando dichos bordes superpuestos antes de ser unidos por la resina.
Sin embargo, en dicho procedimiento, existe también un riesgo importante de desplazamiento de las fibras antes de moldeo. Este procedimiento adolece también de inconvenientes de optimización de masa para asegurar la alineación de las fibras longitudinales.
El documento WO 2007/031649 describe un procedimiento para fabricar una pieza compuesta a partir de una pluralidad de preformas secas y preimpregnadas. La alineación correcta de las fibras está asegurada localmente por esta utilización de preformas preimpregnadas. El documento mva EP-A-749 825 describe las características de la reivindicación 1 salvo el mantenimiento de cada preforma sobre un soporte gracias a unos medios de mantenimiento
que comprenden una envolvente fibrosa aplicada sobre la preforma y apretándola sobre el soporte.
Sin embargo, este procedimiento necesita todavía varias etapas de polimerización.
Las técnicas de arrollamientos filamentosos, además de que presentan las mismas dificultades que las citadas 15 anteriormente con los procedimientos RTM o preimpregnado, pueden presentar la obligación de continuidad de las fibras para efectuar el arrollamiento y por tanto un hándicap para optimizar la masa de la estructura obtenida.
La presente invención prevé evitar los inconvenientes mencionados anteriormente y consiste para ello en un procedimiento de fabricación de una pieza con cuerpo hueco en material compuesto, como la definida en la 20 reivindicación 1.
Así, realizando una etapa de costura entre los bordes de unión de las preformas, se aumenta en gran manera el comportamiento de estas últimas alrededor del soporte y en consecuencia, la cohesión de las fibras.
Según una primera variante de realización, la conexión de los bordes de unión de las preformas se realiza según un procedimiento de costura por pespunte, denominado habitualmente "stitching" o "blind stitching", costura de tipo punto de cadeneta que se puede obtener utilizando un solo hilo.
Según una segunda variante de realización, la conexión de los bordes de unión de las preformas se realiza según un 30 procedimiento de costura por insertado de fibras, denominado comúnmente "tufting".
Según una tercera variante de realización, la conexión de los bordes de unión de las preformas se realiza según un procedimiento de costura por claveteado, denominado comúnmente "Z- pinning".
De manera preferida, la costura se realiza con la ayuda de un hilo de carbono seco.
Según una variante de realización, el hilo de carbono es un hilo pultrusionado, es decir recubierto de resina y polimerizado (Z- pinning, y otros) .
Ventajosamente, las preformas son unas preformas secas. Así, el procedimiento de fabricación no necesita la etapa de preimpregnación de las preformas.
Preferentemente, por lo menos una parte de las preformas están realizadas inicialmente de plano.
45 De manera alternativa o complementaria, por lo menos una parte de las preformas están realizadas inicialmente en conformación floja.
De manera alternativa o complementaria, por lo menos una parte de las preformas está previamente conformada entre un punzón y una vejiga bajo vacío o a presión antes de la colocación sobre el soporte.
50 Según una primera variante de realización, la preforma se mantiene por medio de los extremos de sus bordes de unión.
De manera preferida, la preforma se mantiene por medio de pinzas que equipan el soporte y aptas para recibir un 55 extremo de un borde de unión o de la envolvente fibrosa correspondiente.
Ventajosamente, el procedimiento comprende una etapa suplementaria... [Seguir leyendo]
Reivindicaciones:
1. Procedimiento de fabricación de una pieza con cuerpo hueco en material compuesto a partir de preformas (11,
12) que comprende las etapas sucesivas que prevén: 5
- disponer las preformas alrededor de un soporte (1) apropiado de manera que cada preforma (11, 12) presente unos bordes de unión (112, 113, 122, 123) que entran en contacto por recubrimiento con un borde de unión (122, 123, 112, 113) de otra preforma (12, 11) y mantener cada preforma (11, 12) sobre el soporte
(1) gracias a unos medios de mantenimiento que comprenden una envolvente fibrosa (201, 202) aplicada 10 sobre la preforma (11, 12) y apretándola sobre el soporte (1) ,
- unir entre sí los bordes de unión de cada preforma por costura;
- extraer el soporte e insertar en su lugar un noyo de moldeo antes de la colocación del conjunto en el interior
de un molde e inyección de resina según un procedimiento Resin Transfer Molding RTM/Liquid Resin Infusion LRI seguido de una polimerización de la resina.
2. Procedimiento según la reivindicación 1, caracterizado porque la conexión de los bordes de unión (112, 113, 122,
123) de las preformas (11, 12) se realiza según un procedimiento de costura por pespunte, denominado 20 comúnmente "stitching" o "blind stitching".
3. Procedimiento según la reivindicación 1, caracterizado porque la conexión de los bordes de unión (112, 113, 122, 123) de las preformas (11, 12) se realiza según un procedimiento de costura por insertado de fibras, denominado comúnmente "tufting".
4. Procedimiento según la reivindicación 1, caracterizado porque la conexión de los bordes de unión (112, 113, 122, 123) de las preformas (11, 12) se realiza según un procedimiento de costura por claveteado, denominado comúnmente "Z-pinning".
5. Procedimiento según cualquiera de las reivindicaciones 1 a 4, caracterizado porque la costura se realiza con la ayuda de un hilo (300) de carbono.
6. Procedimiento según la reivindicación 5, caracterizado porque el hilo de carbono es un hilo pultrusionado, es
decir recubierto de resina. 35
7. Procedimiento según cualquiera de las reivindicaciones 1 a 6, caracterizado porque las preformas (11, 12) son unas preformas secas.
8. Procedimiento según cualquiera de las reivindicaciones 1 a 7, caracterizado porque por lo menos una parte de 40 las preformas (11, 12) están realizadas inicialmente de plano.
9. Procedimiento según cualquiera de las reivindicaciones 1 a 8, caracterizado porque por lo menos una parte de las preformas están realizadas inicialmente en conformado flojo.
45 10. Procedimiento según cualquiera de las reivindicaciones 1 a 9, caracterizado porque por lo menos una parte de las preformas (11, 12) están previamente conformadas entre un punzón y una vejiga bajo vacío o a presión antes de la colocación sobre el soporte.
11. Procedimiento según cualquiera de las reivindicaciones 1 a 10, caracterizado porque la preforma (11) se
50 mantiene por medio de pinzas que equipan el soporte (1) y aptas para recibir un extremo de un borde de unión (112, 113) o de la envolvente fibrosa (201, 202) correspondiente.
12. Procedimiento según cualquiera de las reivindicaciones 1 a 11, caracterizado porque comprende una etapa
suplementaria de compactado, realizada preferentemente antes de la costura, de las preformas (11, 12) sobre el 55 noyo o sobre el soporte (1) por expansión de este último en dirección al molde o a una envolvente rígida equivalente.
13. Procedimiento según las reivindicaciones 1 a 12, caracterizado porque las preformas (11, 12) presentan unos bordes de unión (112, 113, 122, 123) biselados.
60 14. Pieza con cuerpo hueco en material compuesto que se puede obtener mediante uno de los procedimientos según cualquiera de las reivindicaciones 1 a 13.
Patentes similares o relacionadas:
Método y molde para la fabricación de piezas de material compuesto, del 15 de Abril de 2020, de AIRBUS OPERATIONS, S.L: Método para la fabricación de piezas de material compuesto, en el que al menos una primera pieza de material compuesto se une a una segunda […]
Proceso para la fabricación de productos de material compuesto empleando un molde con cojinetes, del 19 de Febrero de 2020, de AUTOMOBILI LAMBORGHINI S.P.A.: Proceso para la fabricación de productos elaborados de materiales compuestos, caracterizado por comprender las siguientes fases operativas: - la disposición de uno […]
Método y dispositivo para la fabricación de plástico reforzado con fibra, del 19 de Febrero de 2020, de TORAY INDUSTRIES, INC.: Un método de producción para un plástico reforzado con fibra, en el que una preforma hecha de un sustrato de fibra de refuerzo y que tiene una forma tridimensional y […]
Molde elaborado de un material compuesto y proceso para su fabricación, del 12 de Febrero de 2020, de AUTOMOBILI LAMBORGHINI S.P.A.: Molde para la fabricación de productos elaborado de materiales compuestos, en donde el molde comprende al menos una porción funcional (24, […]
Componente compuesto de fibra, del 29 de Enero de 2020, de Sogefi HD Suspensions Germany GmbH: Un componente compuesto de fibra con al menos una sección de resorte y al menos una estructura de transferencia de fuerza , en el que el material compuesto de fibra […]
Procedimiento de fabricación de una cuaderna circundante de abertura para un fuselaje de aeronave, y cuaderna, del 1 de Enero de 2020, de AIRBUS OPERATIONS, S.L: Procedimiento de fabricación de una cuaderna circundante de abertura para un fuselaje de aeronave, comprendiendo el procedimiento las etapas de: […]
Procedimiento en molde abierto para un material compuesto de matriz de poliamida semicristalina reforzada con fibras, a partir de una composición precursora reactiva de prepolímero, del 1 de Enero de 2020, de ARKEMA FRANCE: Procedimiento de fabricación de un material compuesto termoplástico en molde abierto, comprendiendo dicho material fibras de refuerzo y una matriz […]
Método para la producción de un marco con forma de anillo, del 11 de Diciembre de 2019, de Conseil et Technique: Un método para fabricar un marco en forma de anillo hecho de material compuesto, que comprende al menos los siguientes pasos: - deslizar al menos […]