Procedimiento de fabricación de una alfombrilla para la protección de un tapizado original de un vehículo automóvil y alfombrilla obtenida.
Procedimiento de fabricación de una alfombrilla, en particular para la protección de un tapizado original de un vehículo automóvil,
caracterizado porque comprende las siguientes etapas:
a) proporcionar y cortar según una forma determinada un panel (1) flexible que tiene caras (1a) interna y (1b) externa opuestas;
b) disponer una abertura (2, 3, 4, 5) en dicho panel (1) flexible, estando delimitado el contorno (2a, 3a, 4a, 5a) de dicha abertura (2, 3, 4, 5) por un borde (10) intermedio dispuesto entre bordes (11) interno y (12) externo;
c) proporcionar un molde (19) que comprende un fondo (19a) del que sobresale al menos un primer elemento (20, 21, 22, 23) de separación que tiene un vértice (24), delimitando dicho primer elemento (20, 21, 22, 23) de separación un volumen (20a, 21a, 22a, 23a) interior determinado;
d) disponer dicho panel (1) flexible en el molde (19), estando dispuestos dicho panel (1) flexible y dicho elemento (20, 21, 22, 23) de separación de manera que los bordes (12) externo y (11) interno sobresalen al menos en parte respectivamente hacia el interior y hacia el exterior de dicho volumen (20a, 21a, 22a, 23a) interior, estando el borde (10) intermedio apoyado al menos en parte sobre el vértice (24) del primer elemento (20, 21, 22, 23) de separación;
e) proporcionar un contramolde dispuesto de manera que actúa conjuntamente con dicho molde (19) y atrapar el borde (10) intermedio contra el vértice (24) de dicho primer elemento (20, 21, 22, 23) de separación;
f) inyectar al menos un polímero en estado fundido en dicho volumen (20a, 21a, 22a, 23a) interior mediante medios de distribución dispuestos en el molde (19) y el contramolde de manera que se sobremoldea al menos en parte dicho borde (12) externo y se rellena total o parcialmente dicha abertura (2, 3, 4, 5) mediante la formación de una parte (13, 14, 15, 16) sobremoldeada que desemboca en las caras (1a) interna y (1b) externa del panel (1) flexible.
Tipo: Patente Europea. Resumen de patente/invención. Número de Solicitud: E13188285.
Solicitante: Gery Trentesaux Investissements.
Nacionalidad solicitante: Francia.
Dirección: 47 Avenue de l'Europe Cit de Roncq 59223 Roncq FRANCIA.
Inventor/es: TRENTESAUX,GERY, ESCRICHE PEREZ,VICTOR.
Fecha de Publicación: .
Clasificación Internacional de Patentes:
- B29C45/14 TECNICAS INDUSTRIALES DIVERSAS; TRANSPORTES. › B29 TRABAJO DE LAS MATERIAS PLASTICAS; TRABAJO DE SUSTANCIAS EN ESTADO PLASTICO EN GENERAL. › B29C CONFORMACIÓN O UNIÓN DE MATERIAS PLÁSTICAS; CONFORMACIÓN DE MATERIALES EN ESTADO PLÁSTICO, NO PREVISTA EN OTRO LUGAR; POSTRATAMIENTO DE PRODUCTOS CONFORMADOS, p. ej. REPARACIÓN (fabricación de preformas B29B 11/00; fabricación de productos estratificados combinando capas previamente no unidas para convertirse en un producto cuyas capas permanecerán unidas B32B 37/00 - B32B 41/00). › B29C 45/00 Moldeo por inyección, es decir, forzando un volumen determinado de material de moldeo a través de una boquilla en un molde cerrado; Aparatos a este efecto (moldeo por inyección-soplado B29C 49/06). › incorporando partes o capas preformadas, p. ej. moldeo por inyección alrededor de elementos insertos o sobre objetos a recubrir.
- B60N3/04 B […] › B60 VEHICULOS EN GENERAL. › B60N ASIENTOS ESPECIALMENTE ADAPTADOS PARA VEHÍCULOS; ADAPTACIONES DE VEHICULOS PARA PASAJEROS NO PREVISTAS EN OTRO LUGAR. › B60N 3/00 Instalaciones o adaptaciones de otros accesorios para pasajeros, no previstos en otro lugar (de aparatos de radio, de televisión, de teléfono, de cinturones de seguridad o aparatos similares B60R). › de alfombras de suelo.
PDF original: ES-2552927_T3.pdf
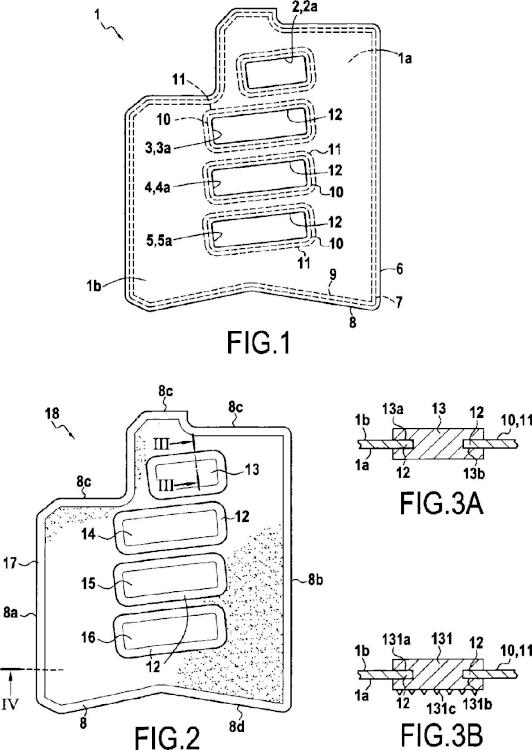
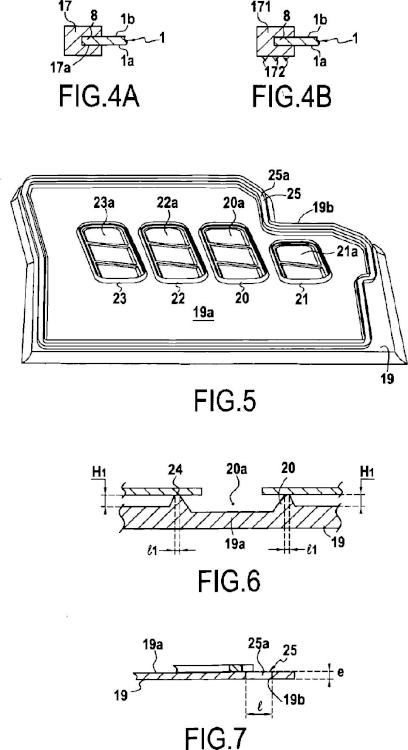
Patentes similares o relacionadas:
Elemento de protección, elemento de hormigón y procedimiento para la fabricación de un elemento de hormigón, del 22 de Julio de 2020, de HERRENKNECHT AG: Elemento de protección para la conexión con un elemento de hormigón de una entibación de túnel, que presenta al menos una sección de protección , […]
Un método de fabricación de un sistema de apertura para un recipiente, del 13 de Mayo de 2020, de TETRA LAVAL HOLDINGS & FINANCE S.A.: Un método de fabricación de un sistema de apertura para un recipiente, comprendiendo el recipiente un material de envasado que tiene un exterior […]
Procedimiento de producción de una pieza, del 13 de Mayo de 2020, de Flex-N-Gate France: Procedimiento de producción de una pieza que incluye, al menos, un elemento de refuerzo fabricado a partir de un inserto fibroso de material […]
Recipiente con bolsa moldeada en el conjunto de válvula y proceso de fabricación correspondiente, del 22 de Abril de 2020, de Dow Global Technologies LLC: Un proceso que comprende: colocar una bolsa de manga en el conjunto de válvula (SBoV) en un aparato de molde de soplado que tiene dos moldes opuestos y móviles , […]
Método para fabricar un elemento de conexión, del 8 de Abril de 2020, de GOTTLIEB BINDER GMBH & CO. KG: Método para fabricar un elemento de conexión usando un método de moldeo por inyección de espuma, en donde una parte de sujeción con elementos […]
Método para fabricar un elemento de conexión, elemento de conexión fabricado utilizando el método, herramienta para fabricar dicho elemento de conexión y un sistema de sujeción con dicho elemento de conexión, del 8 de Abril de 2020, de GOTTLIEB BINDER GMBH & CO. KG: Método para fabricar un elemento de conexión utilizando un método de moldeo por inyección, en donde, en una primera etapa, una parte de sujeción […]
MOLDE, MÁQUINA Y PROCEDIMIENTO PARA LA FABRICACIÓN DE ARTÍCULOS TRIDIMENSIONALES Y PLANTA DE FABRICACIÓN ASOCIADA A LA MISMA, del 2 de Abril de 2020, de SIMPLICITY WORKS EUROPE, S. L. (100.0%): Molde para la fabricación de artículos tridimensionales, que comprende un cuerpo ; una tapa configurada para cerrar dicho cuerpo ; y medios de cierre […]
MÁQUINA Y PROCEDIMIENTO PARA LA FABRICACIÓN DE ARTÍCULOS TRIDIMENSIONALES Y PLANTA DE FABRICACIÓN ASOCIADA A LA MISMA, del 30 de Marzo de 2020, de SIMPLICITY WORKS EUROPE, S. L. (100.0%): Máquina para la fabricación de artículos tridimensionales, que comprende un módulo de recepción configurado para recibir un molde (M1) formado por un cuerpo (M2) y […]