PROCEDIMIENTO PARA LA FABRICACION DE DISPOSITIVOS MICROMECANICOS QUE CONTIENEN UN MATERIAL GETTER Y DISPOSITIVOS FABRICADOS DE ACUERDO CON EL MISMO.
Procedimiento para la fabricación de dispositivos micromecánicos,
que comprende una etapa de unión directa entre dos partes de soporte, una de las cuales (12, 20) está fabricada a base de silicio y la otra está fabricada de silicio o de un material semiconductor, cerámico u óxido, de manera que elementos funcionales (11) y posibles elementos auxiliares del dispositivo se encuentran presentes, como mínimo, sobre una de estas partes de soporte y en el que un depósito de material getter (13, 24) se encuentra presente sobre una parte de soporte de silicio, comprendiendo las siguientes etapas: proporcionar una primera parte de soporte (10) sobre la que los elementos funcionales (11) y posibles elementos auxiliares del dispositivo son incorporadas; disponer una segunda parte de soporte (20); estando formadas dichas primera y segunda partes de soporte, de manera tal que cuando se acoplan forman una cavidad (14) en la que están alojados dichos elementos funcional, auxiliares y depósito de material getter; aproximar las dos partes de soporte mencionadas para formar dicha cavidad y soldar las dos partes mencionadas por unión directa; caracterizándose dicho procedimiento porque dicho depósito de material getter es formado sobre dicha parte de soporte de silicio, por medio de una primera operación de formación sobre la parte de soporte de silicio de una capa intermedia (23) de un material vítreo, cerámico u óxido, que tiene un grosor mínimo de 50 nanómetros, y una segunda operación de depósito de una capa de material getter (24) que tiene un grosor no superior a 10 micras sobre dicha capa intermedia, y que el material getter utilizado es una aleación que contiene zirconio y, como mínimo, un segundo elemento escogido entre molibdeno, niobio, tántalo y tungsteno, encontrándose presente el zirconio en porcentajes comprendidos entre 70 y 97% en peso
Tipo: Patente Internacional (Tratado de Cooperación de Patentes). Resumen de patente/invención. Número de Solicitud: PCT/IT2006/000824.
Solicitante: SAES GETTERS S.P.A..
Nacionalidad solicitante: Italia.
Dirección: VIALE ITALIA, 77 20020 LAINATE (MILANO) ITALIA.
Inventor/es: RIZZI, ENEA.
Fecha de Publicación: .
Fecha Solicitud PCT: 28 de Noviembre de 2006.
Fecha Concesión Europea: 8 de Septiembre de 2010.
Clasificación PCT:
- B81C99/00 TECNICAS INDUSTRIALES DIVERSAS; TRANSPORTES. › B81 TECNOLOGIA DE LAS MICROESTRUCTURAS. › B81C PROCEDIMIENTOS O APARATOS ESPECIALMENTE ADAPTADOS PARA LA FABRICACION O EL TRATAMIENTO DE DISPOSITIVOS O SISTEMAS DE MICROESTRUCTURA (fabricación de microcápsulas o de microbolas B01J 13/02; procedimientos o aparatos especialmente adaptados para la fabricación o el tratamiento de elementos piezoeléctricos o electroestrictivos o magnetoestrictivos en sí H01L 41/22). › Materia no prevista en otros grupos de esta subclase.
Países PCT: Austria, Bélgica, Suiza, Alemania, Dinamarca, España, Francia, Reino Unido, Grecia, Italia, Liechtensein, Luxemburgo, Países Bajos, Suecia, Mónaco, Portugal, Irlanda, Eslovenia, Finlandia, Rumania, Chipre, Lituania, Letonia, Ex República Yugoslava de Macedonia, Albania.
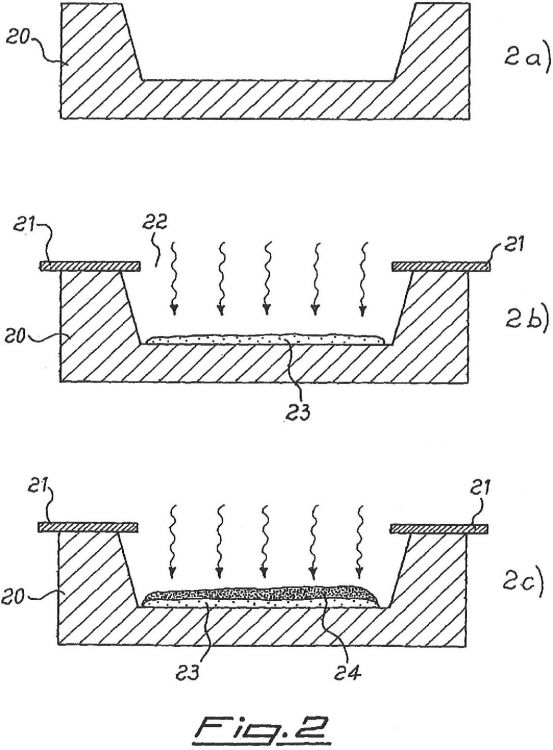
Fragmento de la descripción:
La presente invención se refiere a un procedimiento para la fabricación de dispositivos micromecánicos que contienen un material getter y a los dispositivos fabricados mediante este procedimiento. En particular, la invención se refiere a un procedimiento para la fabricación de dispositivos que comprenden una etapa de unión conjunta de dos obleas por fusión en el interfaz entre ellas, siendo fabricada una de las obleas mediante silicio, y la otra mediante un semiconductor, material cerámico u óxido; la invención se refiere también a los dispositivos finales y a materiales getter específicos capaces de resistir las condiciones del procedimiento.
Los dispositivos micromecánicos se conocen de manera general como “Sistemas microelectromecánicos” o “Sistemas microoptoelectromecánicos”, y con sus abreviaturas MEMS y MOEMS (a continuación se hará referencia solamente a MEMS, que tendrá también el significativo de MODEMS). Estos dispositivos están formados a base de una cavidad estanqueizada, dentro de la que se encuentran piezas micromecánicas capaces de llevar a cabo movimientos predeterminados o piezas capaces de interaccionar con radiaciones electromagnéticas, además de piezas auxiliares y alimentaciones eléctricas tanto para el suministro de potencia para el dispositivo como para la transmisión al exterior de la señal generada por el dispositivo. Se encuentran entre los ejemplos de dichos dispositivos los microacelerómetros, descritos en numerosas patentes tales como US 5.594.170, US 5.656.778 y US 5.952.572; resonadores miniaturizados, utilizados en el campo de las telecomunicaciones, y particularmente en la fabricación de teléfonos móviles que se describen en las patentes US 5.821.836 y US 6.058.027; o bien sensores miniaturizados IR, un ejemplo de los cuales se describe en la patente US 5.895.233.
Al final del procedimiento de fabricación, diferentes gases quedan contenidos en la cavidad de un MEMS, siendo residuales del procedimiento o debidos a la desgasificación de las paredes de
la misma cavidad, los cuales pueden interferir con el funcionamiento de los MEMS: por ejemplo, pueden modificar la conducción térmica en el sistema alterando, por lo tanto, lamedición de temperatura en el caso de un sensor IR, que por lo tanto requiere el mayor grado posible de vacío en la cavidad. Otros dispositivos MEMS no tienen esta exigencia tan estricta de niveles de vacío extremadamente elevados. Por ejemplo, en acelerómetros una
baja presión de gas en la cavidad ayuda a amortiguar la vibración de la pieza móvil después de que ha sido puesta en movimiento; esto permite la recuperación rápida de la situación de “reposo” del dispositivo, haciéndolo más fácilmente disponible para otras detecciones de movimiento; con este objetivo, la fabricación de algunos MEMS prevé el relleno de la cavidad antes de su cierre estanco con un gas determinado (por ejemplo, un gas noble) a presiones del orden de miles de Pascal (Pa). En estos casos, no obstante, también es necesario que la atmósfera en la cavidad tenga una presión y composición química constantes, porque las variaciones de sus parámetros podrían alterar la viscosidad del medio alrededor de las partes móviles, alterando por lo tanto las mediciones.
El conseguir grados de vacío muy elevados o una atmósfera constante durante toda la vida de un dispositivo MEMS se puede asegurar introduciendo en la cavidad un material getter, es decir, un material capaz de eliminar la mayor parte de gases no nobles. Son materiales getter usualmente utilizados los metales, tales como zirconio, titanio o aleaciones de los mismos; es preferente una aleación con un porcentaje en peso de zirconio 80%cobalto 15%-tierras raras 5%, comercializado por la solicitante con la designación St 787. La utilización de materiales getter en los dispositivos MEMS se describe, por ejemplo, en las patentes USA Nºs 5.952.572, 6.499.354, 6.590.850, 6.621.134, 6.635.509 y
6.923.625.
Los MEMS son fabricados con tecnologías derivadas de la fabricación de circuitos semiconductores de integrados, que consisten de manera típica en depósitos localizados de los materiales deseados sobre soportes planos de cristal, de cuarzo, de material cerámico (por ejemplo, carburo de silicio) o de un material semiconductor (el silicio es preferente), y eliminaciones selectivas de zonas de capas de diferente material. En particular, los MEMS de última generación, descritos en la siguiente referencia a la figura 1, son fabricados normalmente por la soldadura de dos piezas entre sí, siendo formada una primera pieza –10habitualmente a base de un soporte plano, en general de silicio, sobre el que se constituyen los elementos funcionales –11-y los elementos auxiliares (los cuales no se han mostrado en el dibujo), y una segunda parte –12-que puede ser fabricada a base de cristal, cuarzo, material cerámico o un material semiconductor y que en
general tiene sólo la función de cerrar el dispositivo a efectos de proteger los elementos internos. Dado que esta segunda parte se encuentra, en general, libre de elementos funcionales y, por lo tanto, proporciona mayor espacio libre, el material getter –13está dispuesto preferentemente sobre esta parte, tal como se describe, por ejemplo, en la patente USA 6.897.551. La técnica
preferente para el depósito de capas de material getter en esta solicitud es el depósito catódico, habitualmente conocido como “bombardeo iónico” (“sputtering”). Tal como es sabido, en estatécnica, un cuerpo que tiene en general forma de un cilindro de poca longitud (llamado “objetivo”), fabricado del material que se desea depositar, y el soporte sobre el que se desea formar el depósito, son dispuestos en una cámara cerrada; la cámara es llenada con un gas noble, en general argón, a una presión inferior a la atmosférica, aplicando una diferencia de potencial de una magnitud de miles de voltios (o más baja, dependiendo de la configuración utilizada) entre el objetivo (mantenido a potencial catódico) y un ánodo, siendo ionizado el gas noble y los iones producidos de este modo son acelerados hacia el objetivo, erosionándolo por impacto; el material erosionado se deposita sobre las superficies disponibles incluyendo el soporte; utilizando sistemas de enmascarado dotados de aberturas adecuadas es posible reducir el área del soporte en el que se ha formado el depósito. Como alternativa, el bombardeo iónico puede ser llevado a cabo en condiciones reactivas, a saber, añadiendo al gas noble un pequeño porcentaje de un gas reactivo, por ejemplo, oxígeno, que reacciona con las partículas erosionadas por el objetivo en la fase gaseosa produciendo un depósito del material que resulta de la reacción del gas reactivo con dichas partículas. Una vez que la totalidad de los elementos necesarios para el funcionamiento de los MEMS han sido formados sobre las dos partes, éstas son unidas entre sí por soldadura a lo largo de una línea que encierra los elementos del dispositivo. El micro-dispositivo queda, por lo tanto, cerrado de forma estanca en un espacio cerrado –14-y está protegido mecánica y químicamente con respecto al ambiente externo.
La soldadura puede ser llevada a cabo por numerosas técnicas conocidas por la definición habitual de “unión” (“bond-ing”). Una primera posibilidad consiste en insertar entre las dos partes un metal maleable, tal como indio, plomo u oro, y provocar su fusión y solidificación, posiblemente ejerciendo una
cierta presión (“unión a presión”): no obstante, esta técnica tiene como resultado soldaduras que no son completamente fiables desde el punto de vista de resistencia mecánica. Otro tipo de unión es la anódica (utilizada principalmente en el caso en el que uno de los soportes está realizado a base de cristal o cuarzo y el otro es de silicio), de manera que se aplica una diferencia de potencial de unos 1000 V entre las dos partes mantenidas a una temperatura aproximada de 300-500ºC; en estas condiciones existe una migración de iones positivos desde el soporte mantenido a un potencial positivo (por ejemplo, iones sodio del cristal) hacia el soporte mantenido a un potencial negativo, y una migración de iones negativos (por ejemplo, oxígeno del silicio) a la dirección opuesta; esta migración de material entre los dos soportes tiene como resultado su soldadura entre sí. Otra posible técnica es la unión eutéctica, en la que una capa de metal o aleación capaz de formar una composición eutéctica con el material de, como mínimo, uno de los dos soportes,...
Reivindicaciones:
1. Procedimiento para la fabricación de dispositivos micromecánicos, que comprende una etapa de unión directa entre dos partes de soporte, una de las cuales (12, 20) está fabricada a base de silicio y la otra está fabricada de silicio o de un material semiconductor, cerámico u óxido, de manera que elementos funcionales (11) y posibles elementos auxiliares del dispositivo se encuentran presentes, como mínimo, sobre una de estas partes de soporte y en el que un depósito de material getter (13, 24) se encuentra presente sobre una parte de soporte de silicio, comprendiendo las siguientes etapas: proporcionar una primera parte de soporte (10) sobre la que los elementos funcionales (11) y posibles elementos auxiliares del dispositivo son incorporadas; disponer una segunda parte de soporte (20); estando formadas dichas primera y segunda partes de soporte, de manera tal que cuando se acoplan forman una cavidad (14) en la que están alojados dichos elementos funcional, auxiliares y depósito de material getter; aproximar las dos partes de soporte mencionadas para formar dicha cavidad y soldar las dos partes mencionadas por unión directa; caracterizándose dicho procedimiento porque dicho depósito de material getter es formado sobre dicha parte de soporte de silicio, por medio de una primera operación de formación sobre la parte de soporte de silicio de una capa intermedia (23) de un material vítreo, cerámico u óxido, que tiene un grosor mínimo de 50 nanómetros, y una segunda operación de depósito de una capa de material getter (24) que tiene un grosor no superior a 10 micras sobre dicha capa intermedia, y que el material getter utilizado es una aleación que contiene zirconio y, como mínimo, un segundo elemento escogido entre molibdeno, niobio, tántalo y tungsteno, encontrándose presente el zirconio en porcentajes comprendidos entre 70 y 97% en peso.
2. Procedimiento, según la reivindicación 1, en el que dichos segundo elemento es escogido entre niobio y tántalo, y el zirconio se encuentra presente en dicha aleación en porcentajes comprendidos entre 85 y 95% en peso.
3. Procedimiento, según la reivindicación 1, en el que dicha capa intermedia está constituida por óxido o nitruro de silicio y su formación es llevada a cabo por medio de reacción de la parte de soporte de silicio con oxígeno o nitrógeno.
4. Procedimiento, según la reivindicación 1, en el que dicha capa intermedia está realizada en óxido o nitruro de silicio y su formación es llevada a cabo por medio de implantación de iones de oxígeno o de nitrógeno en el silicio.
5. Procedimiento, según la reivindicación 4, en el que la implantación de iones es llevada a cabo por tratamientos térmicos de difusión de oxígeno o nitrógeno en el silicio.
6. Procedimiento, según la reivindicación 1, en el que dicha capa intermedia es formada por depósito catódico.
7. Procedimiento, según la reivindicación 6, en el que el depósito catódico tiene lugar en condiciones reactivas.
8. Procedimiento, según la reivindicación 6, en el que el depósito catódico es llevado a cabo sobre una zona reducida de la parte (20) de soporte de silicio, colocando sobre dicha parte de soporte una máscara (21) con una abertura (22) que define un área de dicha parte de soporte de silicio, en la que se formará el depósito.
9. Procedimiento, según la reivindicación 1, en el que dicha operación de depósito de la capa (24) de material getter tiene lugar por medio de depósito catódico.
10. Procedimiento, según la reivindicación 1, en el que dicha operación de depósito de la capa de material getter (24) es llevada a cabo solamente sobre la capa intermedia colocando sobre la parte (20) de soporte de silicio una máscara con una abertura que tiene unas dimensiones menores o iguales a las de la máscara utilizada en la formación de la capa intermedia y alineada de forma tal con respecto a la parte (20) de soporte de silicio que el material getter se deposita solamente sobre dicha capa intermedia.
11. Procedimiento, según la reivindicación 10, en el que las operaciones de formación de las capas intermedia y de material getter tienen lugar utilizando la misma máscara (21) con una alineación constante con respecto a la parte (20) de soporte de silicio.
12. Procedimiento, según la reivindicación 1, en el que
el grosor de la capa de material getter está comprendido entre 0,1 y 10 µm.
13. Procedimiento, según la reivindicación 1, en el que las superficies de las dos partes de soporte mencionadas a soldar entre sí son sometidas a limpieza y tratamiento de modificación superficial antes de la soldadura.
14. Procedimiento, según la reivindicación 13, en el que dichos tratamientos son escogidos entre pulido mecánico, lapeado o lavados químicos.
15. Procedimiento, según la reivindicación 1, en el que dicha operación de soldadura de las dos partes de soporte mencionadas por unión directa es llevada a cabo en presencia de un gas noble a una presión inferior a la atmosférica.
Patentes similares o relacionadas:
Método para producir microportadores, del 11 de Marzo de 2020, de MyCartis NV: Un método para producir microportadores que comprende las siguientes etapas: (a) proporcionar una oblea que tiene una estructura de tipo […]
Procedimiento para la fabricación de micro-objetos, del 16 de Octubre de 2018, de UNIVERSITAT KASSEL: Procedimiento para la fabricación de micro-objetos , en el que en una etapa de procedimiento se disponen micropartículas magnéticas […]
Método para la fabricación de una microaguja, del 23 de Agosto de 2017, de UNIVERSITY COLLEGE, CORK: Un método para la fabricación de una microaguja usando un molde que tiene una cavidad de formación de la aguja, caracterizado porque el método comprende las […]
Estructuras microfluídicas con sección transversal circular, del 7 de Junio de 2017, de THE CHARLES STARK DRAPER LABORATORY INC: Método para fabricar una estructura microfluídica, que comprende: (a) proporcionar una oblea impresa que comprende al menos una región eléctricamente […]
Métodos para fabricar micro- y nanoestructuras usando litografía blanda o de impresión, del 15 de Marzo de 2017, de THE UNIVERSITY OF NORTH CAROLINA AT CHAPEL HILL: Método para fabricar partículas de tamaño micro o nanométrico monodispersas, que comprende: introducir un material en una plantilla con patrón […]
Matriz de microagujas integrada y su método de fabricación, del 1 de Diciembre de 2015, de STICHTING VOOR DE TECHNISCHE WETENSCHAPPEN: Método de fabricación de una matriz de microagujas que comprende las etapas de:
- seleccionar un molde de producción blando que comprende una serie de incisiones microscópicas […]
Capa de polímero colada con alta relación de aspecto, del 16 de Noviembre de 2015, de SICPA HOLDING SA: Método de producción de una capa de polímero estructurada (4, 4') que se adhiere a un sustrato (3, 3'), que comprende las etapas de:
(a) […]
MÉTODO Y SISTEMA DE CARACTERIZACIÓN DE ESTRUCTURAS NANO Y MICRO MECÁNICAS, del 12 de Diciembre de 2013, de CONSEJO SUPERIOR DE INVESTIGACIONES CIENTIFICAS (CSIC): Método y sistema de microscopia óptica basada en la deflexión de estructuras micro y nano mecánicas al incidir un haz láser en ellas que provee simultáneamente […]