UTILIZACIÓN DE MoO3 COMO INHIBIDOR DE LA CORROSIÓN.
Tipo: Patente Europea. Resumen de patente/invención. Número de Solicitud: E08101487.
Solicitante: NOF METAL COATINGS EUROPE.
Nacionalidad solicitante: Francia.
Dirección: 120, RUE GALILEE ZAET DE CREIL / SAINT-MAXIMIN 60100 CREIL FRANCIA.
Inventor/es: MAZE, ETIENNE, MOCQUERY,CARMEN, MILLET,BENOIT, Espinosa,Antonio Francisco Iandoli.
Fecha de Publicación: .
Fecha Solicitud PCT: 12 de Noviembre de 2001.
Clasificación Internacional de Patentes:
- C09D5/08B2
- C09D5/10 QUIMICA; METALURGIA. › C09 COLORANTES; PINTURAS; PULIMENTOS; RESINAS NATURALES; ADHESIVOS; COMPOSICIONES NO PREVISTAS EN OTRO LUGAR; APLICACIONES DE LOS MATERIALES NO PREVISTAS EN OTRO LUGAR. › C09D COMPOSICIONES DE REVESTIMIENTO, p. ej. PINTURAS, BARNICES, LACAS; EMPLASTES; PRODUCTOS QUIMICOS PARA LEVANTAR LA PINTURA O LA TINTA; TINTAS; CORRECTORES LIQUIDOS; COLORANTES PARA MADERA; PRODUCTOS SOLIDOS O PASTOSOS PARA ILUMINACION O IMPRESION; EMPLEO DE MATERIALES PARA ESTE EFECTO (cosméticos A61K; procedimientos para aplicar líquidos u otros materiales fluidos a las superficies, en general B05D; coloración de madera B27K 5/02; vidriados o esmaltes vitreos C03C; resinas naturales, pulimento francés, aceites secantes, secantes, trementina, per se , C09F; composiciones de productos para pulir distintos del pulimento francés, cera para esquíes C09G; adhesivos o empleo de materiales como adhesivos C09J; materiales para sellar o guarnecer juntas o cubiertas C09K 3/10; materiales para detener las fugas C09K 3/12; procedimientos para la preparación electrolítica o electroforética de revestimientos C25D). › C09D 5/00 Composiciones de revestimiento, p. ej. pinturas, barnices o lacas, caracterizados por su naturaleza física o por los efectos que producen; Emplastes. › que contienen polvo metálico.
- C23C22/74 C […] › C23 REVESTIMIENTO DE MATERIALES METALICOS; REVESTIMIENTO DE MATERIALES CON MATERIALES METALICOS; TRATAMIENTO QUIMICO DE LA SUPERFICIE; TRATAMIENTO DE DIFUSION DE MATERIALES METALICOS; REVESTIMIENTO POR EVAPORACION EN VACIO, POR PULVERIZACION CATODICA, POR IMPLANTACION DE IONES O POR DEPOSICION QUIMICA EN FASE VAPOR, EN GENERAL; MEDIOS PARA IMPEDIR LA CORROSION DE MATERIALES METALICOS, LAS INCRUSTACIONES, EN GENERAL. › C23C REVESTIMIENTO DE MATERIALES METALICOS; REVESTIMIENTO DE MATERIALES CON MATERIALES METALICOS; TRATAMIENTO DE MATERIALES METALICOS POR DIFUSION EN LA SUPERFICIE, POR CONVERSION QUIMICA O SUSTITUCION; REVESTIMIENTO POR EVAPORACION EN VACIO, POR PULVERIZACION CATODICA, POR IMPLANTACION DE IONES O POR DEPOSICION QUIMICA EN FASE VAPOR, EN GENERAL (fabricación de productos revestidos de metal por extrusión B21C 23/22; revestimiento metálico por unión de objetos con capas preexistentes, ver las clases apropiadas, p. ej. B21D 39/00, B23K; metalización del vidrio C03C; metalización de piedras artificiales, cerámicas o piedras naturales C04B 41/00; esmaltado o vidriado de metales C23D; tratamiento de superficies metálicas o revestimiento de metales mediante electrolisis o electroforesis C25D; crecimiento de monocristales C30B; mediante metalización de textiles D06M 11/83; decoración de textiles por metalización localizada D06Q 1/04). › C23C 22/00 Tratamiento químico de la superficie de materiales metálicos por reacción de la superficie con un medio reactivo quedando productos de reacción del material de la superficie en el revestimiento, p. ej. revestimiento por conversión, pasivación de metales. › para obtener revestimientos de conversión cocidos.
- C23F11/18E
Clasificación PCT:
- C09D5/08 C09D 5/00 […] › Pinturas anticorrosivas.
- C23F11/18 C23 […] › C23F LEVANTAMIENTO NO MECANICO DE MATERIAL METALICO DE LAS SUPERFICIES (trabajo del metal por electroerosión B23H; despulido por calentamiento a la llama B23K 7/00; trabajo del metal por láser B23K 26/00 ); MEDIOS PARA IMPEDIR LA CORROSION DE MATERIALES METALICOS; MEDIOS PARA IMPEDIR LAS INCRUSTACIONES, EN GENERAL (tratamiento de superficies metálicas o revestimiento de metales mediante electrolisis o electroforesis C25D, C25F ); PROCESOS EN MULTIPLES ETAPAS PARA EL TRATAMIENTO DE LA SUPERFICIE DE MATERIALES METALICOS UTILIZANDO AL MENOS UN PROCESO CUBIERTO POR LA CLASE C23 Y AL MENOS UN PROCESO CUBIERTO BIEN POR LA SUBCLASE C21D BIEN POR LA SUBCLASE C22F O POR LA CLASE C25. › C23F 11/00 Inhibición de la corrosión de materiales metálicos por aplicación de inhibidores a la superficie en peligro de corrosión, o adición de los mismos al agente corrosivo. › utilizando inhibidores inorgánicos.
Países PCT: Austria, Bélgica, Suiza, Alemania, Dinamarca, España, Francia, Reino Unido, Grecia, Italia, Liechtensein, Luxemburgo, Países Bajos, Suecia, Mónaco, Portugal, Irlanda, Eslovenia, Finlandia, Rumania, Chipre, Lituania, Letonia.
PDF original: ES-2332865_T3.pdf
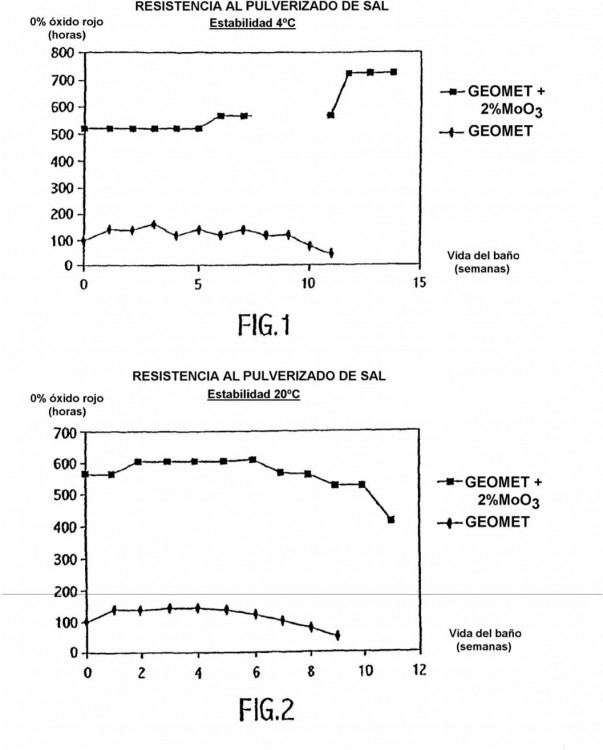
Fragmento de la descripción:
El objetivo de la presente invención consiste en desarrollar un revestimiento anticorrosión para partes metálicas, preferentemente un revestimiento libre de cromo hexavalente, que presenta unas propiedades anticorrosión mejoradas.
La presente invención se aplica a las partes metálicas de un tipo cualquiera, en particular las realizadas en 5 acero o hierro fundido, que necesita tener un buen comportamiento a la corrosión, por ejemplo debido a su aplicación en la industria automotriz. La geometría de las partes que se deben tratar tiene poca importancia siempre que se puedan aplicar las composiciones anticorrosión mediante procedimientos fiables e industrializables.
Uno de los objetivos de la presente invención consiste, en particular, en mejorar las propiedades anticorrosión de las partes tratadas sin la utilización de una composición a base de cromo hexavalente en la 10 formulación de los revestimientos.
Hasta ahora se han propuesto muchas disoluciones a base de cromo hexavalente destinadas a tratamientos anticorrrosión. Aunque en general resultan satisfactorias con respecto a la protección de las partes metálicas tratadas, están resultando, sin embargo, progresivamente más criticados debido al riesgo tóxico que implican y en particular debido a las consecuencias negativas para el ambiente. 15
Como consecuencia, se han recomendado múltiples tratamientos anticorrosión libres de cromo hexavalente. Algunas de estas composiciones están basadas en un metal en particular, tal como el cinc o el aluminio. Sin embargo, cuando tales composiciones se encuentran en forma de dispersión acuosa su estabilidad es limitada. Ello evita largos períodos de almacenamiento y preservación.
En el contexto de la presente invención, el solicitante ha descubierto que es posible mejorar las 20 propiedades anticorrosión y la estabilidad de múltiples composiciones de revestimientos anticorrosión mediante la incorporación en éstos de óxido de molibdeno MoO3 como inhibidor de la corrosión.
Hasta ahora, la utilización de óxido de molibdeno MoO3 como inhibidor de la corrosión en sistemas de fase acuosa no era conocida. Ciertos iones de molibdato, es decir, MoO42- se han presentado ya como inhibidores de la corrosión. Sin embargo, el solicitante ha podido demostrar que en cierto número de composiciones anticorrosión 25 convencionales la adición de un molibdato, por ejemplo, el molibdato de cinc, no mejora sus propiedades en modo alguno.
La presente invención se refiere, más particularmente, a la utilización de un óxido de molibdeno MoO3 como agente destinado a amplificar las propiedades anticorrosión de una composición de revestimiento a base de un metal en partículas que comprende cinc o una aleación de cinc en fase acuosa. Este descubrimiento se ha 30 extendido incluso a composiciones que comprenden cromo hexavalente. Este es otro objetivo de la presente invención.
Sin desear en modo alguno resultar limitativo, parecería que en el caso particular de una composición de revestimiento anticorrosión a base de un metal en partículas, la presencia de óxido de molibdeno MoO3 permite mejorar el control de la protección sacrificial ejercida por el metal en partículas en suspensión en la composición. 35
Según un aspecto particular, los metales en partículas presenta una forma laminar con escamas de un grosor comprendido entre 0,05 y 1 µm y un diámetro equivalente (D50) medido mediante difracción de láser comprendido entre 5 m y 25 µm. Más particularmente, el objetivo de la presente invención es utilizar óxido de molibdeno MoO3 en una composición que comprende cinc en fase acuosa.
Según otro aspecto de la presente invención, el óxido de molibdeno MoO3 se utiliza en una forma cristalina 40 ortorrómbica esencialmente pura, con un contenido en molibdeno superior a aproximadamente 60% en masa.
Ventajosamente, el óxido de molibdeno MoO3 se utilizará en las composiciones anticorrosión en forma de partículas con dimensiones comprendidas entre 1 y 200 µm.
Más específicamente, el objeto de la presente invención son las composiciones de revestimientos anticorrosión destinadas a partes metálicas, que comprenden: 45
- por lo menos un metal en partículas;
- un disolvente orgánico;
- un espesante;
- un aglutinante a base de silano, preferentemente portador de grupos funcionales epoxi;
1. óxido de molibdeno (MoO3); 50
2. posiblemente un silicato de sodio, potasio o litio y;
- agua.
Las proporciones relativas de los múltiples constituyentes de tal composición pueden oscilar ampliamente. Sin embargo, el contenido en óxido de molibdeno (MoO3) se encuentra preferentemente comprendido entre el 0,5 y el 7% en peso y todavía más preferentemente en la zona del 2% en peso de composición total.
El metal en partículas presente en la composición se puede seleccionar de entre cinc, aluminio, cromo, 5 manganeso, níquel, titanio, sus aleaciones y compuestos intermetálicos, y mezclas de los mismos. Se debe advertir que, si la composición de revestimiento recomendada está preferentemente libre de CrVI, puede, sin embargo, comprender una cierta proporción de cromo metálico. En la práctica, es muy deseable la presencia de cinc.
Ventajosamente, el contenido en metal en partículas está comprendido entre el 10% y el 40% en peso de metal con respecto al peso de la composición. 10
Preferentemente, la composición de revestimiento anticorrosión según la presente invención comprende cinc y/o aluminio, y preferentemente comprende cinc.
Tal como se mencionó anteriormente, este tipo de composición es principalmente de naturaleza acuosa y por consiguiente preferentemente comprende entre un 30% y un 60% en peso de agua. La composición puede, no obstante, estar enriquecida por la presencia de un disolvente orgánico, preferentemente un disolvente orgánico 15 soluble en agua, que hace posible mejorar el comportamiento anticorrosión de la composición. A tal fin, la composición comprenderá, por ejemplo, entre el 1% y el 30% en peso con respecto a la composición total. Sin embargo, parece ser importante no exceder el 30% en contenido de disolvente orgánico.
En una forma de realización ventajosa de la presente invención, la composición utilizará un disolvente orgánico, por ejemplo un glicol éter, en particular dietilenglicol, trietilenglicol y dipropilenglicol. 20
Según otro aspecto de la presente invención, la composición anticorrosión también comprende entre el 0,005% y el 2% en peso de un agente espesante, en particular de una derivado de celulosa, más particularmente hidoximetilceluolosa, hidoxietilcelulosa, hidroxipropilcelulosa, hidroxipropilmetilcelulosa, goma de xantano o un espesante asociante de tipo poliuretano o acrílico.
La composición de la presente invención también puede comprender agentes reológicos minerales de tipo 25 arcilla silícea u organofílica.
Dicha composición también utiliza un aglutinante, preferentemente un silano organofuncional, utilizado en una cantidad comprendida entre el 3% y el 20% en peso. La función orgánica se puede representar mediante vinilo, metacriloxi y amino, pero es preferible una funcionalidad epoxi con el fin de amplificar el comportamiento del revestimiento así como también la estabilidad de la composición. El xilano se puede dispersar ventajosamente con 30 facilidad en medio acuoso y es soluble preferentemente en tal medio. Preferentemente, el silano de utilidad es un silano epoxi funcional tal como beta-(3,4-epoxiciclohexil)etiltrimetoxisilano, 4(tremetoxisilil)butan-1,2 epoxi o -glicidoxipropil-tremetoxisilano.
Finalmente, la composición de revestimiento anticorrosión de la presente invención puede contener también, además del disolvente orgánico anteriormente mencionado, hasta una cantidad máxima de 35 aproximadamente el 10% en peso de disolvente Stoddard con el fin de mejorar la capacidad de aplicación de la composición anticorrosión a las partes metálicas por pulverización, inmersión o inmersión rotación.
Ventajosamente, la composición también puede comprender un silicato sódico, potásico o de litio, preferentemente en una cantidad comprendida entre el 0,05% y el 0,5% en peso.
Naturalmente, la presente invención también se refiere... [Seguir leyendo]
Reivindicaciones:
1. Utilización del MoO3 como agente para aumentar las propiedades anticorrosión de una composición de revestimento anticorrosión a base de un metal en partículas que contiene cinc o una aleación de cinc en fase acuosa.
2. Utilización según la reivindicación 1 para mejorar la eficacia de la protección sacrificial ejercida por el metal en partículas, utilizado preferentemente en forma laminar. 5
3. Utilización según la reivindicación 1 ó 2, caracterizada porque la composición de revestimiento anticorrosión contiene de 30% a 60% de agua en peso.
4. Utilización según cualquiera de las reivindicaciones 1 a 3, caracterizada porque la composición de revestimiento anticorrosión contiene un aglutinante a base de silano, portador preferentemente de grupos funcionales epoxi. 10
5. Utilización según cualquiera de las reivindicaciones 1 a 4, caracterizada porque el óxido de molibdeno MoO3 está en una forma cristalina ortorrómbica esencialmente pura, que presenta un contenido de molibdeno superior a aproximadamente 60% en masa.
6. Utilización según cualquiera de las reivindicaciones 1 a 5, caracterizada porque el óxido de molibdeno MoO3 está en forma de partículas que presentan unas dimensiones de entre 1 y 200 µm. 15
7. Utilización según cualquiera de las reivindicaciones 1 a 6, caracterizada porque la composición de revestimiento anticorrosión contiene un silicato de sodio, potasio o litio, preferentemente en una cantidad comprendida entre 0,05% y 0,5% en peso.
Patentes similares o relacionadas:
Recubrimiento pulverizado resistente a la corrosión y método para formar el mismo, del 3 de Junio de 2020, de Yoshikawa Kogyo Co., Ltd: Un recubrimiento pulverizado de aleación de Al-Mg resistente a la corrosión que cubre la superficie del sustrato, donde el recubrimiento pulverizado de […]
Composición en solución para tratamiento superficial de lámina de acero, superficie de lámina de acero chapada a base de zinc, tratada con la misma, y su procedimiento de fabricación, del 20 de Mayo de 2020, de POSCO: Una composición en solución para el tratamiento superficial de lámina de acero, que comprende: 30 % en peso a 60 % en peso de un compuesto de cromo trivalente […]
Capa de estaño-níquel con elevada dureza, del 2 de Octubre de 2019, de DR.ING. MAX SCHLÖTTER GMBH & CO. KG: Capa de estaño-níquel con una fase de NiSn, presentando la capa de estaño-níquel una dureza de al menos HV 750 (dureza Vickers), y un grosor de […]
Composiciones de revestimiento en polvo capaces de tener una imprimación que sustancialmente no contiene cinc, del 4 de Septiembre de 2019, de AKZO NOBEL COATINGS INTERNATIONAL B.V.: Un revestimiento compuesto que comprende una imprimación y una última capa, formándose la imprimación a partir de una composición de imprimación epoxídica termoestable […]
Procedimiento para producir un revestimiento protector contra la corrosión oscuro, del 3 de Julio de 2019, de EWALD DORKEN AG.: Procedimiento para producir un revestimiento protector contra la corrosión oscuro sobre un sustrato metálico, con las etapas: - aplicar una composición de capa de […]
Utilización de itrio, zirconio, lantano, cerio, praseodimio y/o neodimio como agente de refuerzo para una composición de revestimiento anticorrosión, del 20 de Mayo de 2019, de NOF METAL COATINGS EUROPE: Utilización de por lo menos un elemento seleccionado de entre itrio, zirconio, lantano, cerio, praseodimio y neodimio, en forma de óxidos o sales, como agente […]
Revestimiento y acero revestido, del 5 de Marzo de 2019, de Kyoto Materials Co. Ltd: Revestimiento que comprende: óxido de calcio y/o hidróxido de calcio; sulfato de magnesio; ácido benzoico y/o una sal de benzoato; y una resina, […]
Composición de recubrimiento con efecto anticorrosivo, del 26 de Octubre de 2018, de BASF COATINGS GMBH: Una composición de recubrimiento que comprende al menos un aglutinante (A) que contiene al menos una resina polimérica (A1) y al menos un agente de […]