Pala de rotor con orificio de drenaje.
Procedimiento para la fabricación de una pala de rotor (1) para una planta de energía eólica,
presentando la pala de rotor fabricada (1) en su extensión longitudinal, que se extiende esencialmente de una raíz de pala de rotor (2) a una punta de pala de rotor (3), al menos una zona, en la que la pala de rotor presenta un perfil de sección transversal aerodinámico (4, 4', 4") que presenta un borde de ataque de perfil (5) y un borde de salida de perfil (6) que están unidos mediante un lado de succión (7) y un lado de presión (8) del perfil de sección transversal (4, 4', 4"), y estando previstas al menos una primera pieza moldeada y al menos una segunda pieza moldeada (11, 12) fabricada en dirección longitudinal de la pala de rotor (1) para un lado de succión (7) y un lado de presión (8) de la pala de rotor (1) que se han de unir entre sí respectivamente en las zonas del borde de ataque de perfil (5) y el borde de salida de perfil (6), caracterizado por las siguientes etapas de procedimiento:
- al menos en la zona de la punta de pala de rotor (3), un elemento de unión (15) se une o está unido con un lado interior de la al menos una primera pieza moldeada (11) en el borde de ataque de perfil (5) con ayuda de un medio de unión (18), sobresaliendo el elemento de unión (15) de la primera pieza moldeada (11) en el borde de ataque de perfil (11),
- en la zona de la punta de pala de rotor (3), un elemento superficial (16) se une o está unido con el elemento de unión (15) en el borde de ataque de perfil (5) o está configurado en forma de una sola pieza con el elemento de unión (15), finalizando el elemento superficial (16) esencialmente a ras con la primera pieza moldeada (11) en la zona del borde de salida de perfil (6),
- la al menos una segunda pieza moldeada (12) se ensambla con la primera pieza moldeada (11), uniéndose un lado interior de la segunda pieza moldeada (12) en el borde de ataque de perfil (5) con la parte del elemento de unión (15) que sobresale de la primera pieza moldeada (11) e introduciéndose un medio de unión (19) entre la primera y la segunda pieza moldeada (11, 12) en el borde de salida de perfil (6), y
- un orificio de drenaje (9) está realizado o se dispone en la zona de la primera pieza moldeada (11) cerrada mediante el elemento superficial (16) del borde de salida de perfil (6).
Tipo: Patente Europea. Resumen de patente/invención. Número de Solicitud: E10187441.
Solicitante: Senvion SE.
Nacionalidad solicitante: Alemania.
Dirección: UBERSEERING 10 22297 HAMBURG ALEMANIA.
Inventor/es: BENDEL,Urs, ZELLER,LENZ SIMON.
Fecha de Publicación: .
Clasificación Internacional de Patentes:
- F03D1/00 MECANICA; ILUMINACION; CALEFACCION; ARMAMENTO; VOLADURA. › F03 MAQUINAS O MOTORES DE LIQUIDOS; MOTORES DE VIENTO, DE RESORTES, O DE PESOS; PRODUCCION DE ENERGIA MECANICA O DE EMPUJE PROPULSIVO O POR REACCION, NO PREVISTA EN OTRO LUGAR. › F03D MOTORES DE VIENTO. › Motores de viento con el eje de rotación dispuesto sustancialmente paralelo al flujo de aire que entra al rotor (su control F03D 7/02).
- F03D1/06 F03D […] › F03D 1/00 Motores de viento con el eje de rotación dispuesto sustancialmente paralelo al flujo de aire que entra al rotor (su control F03D 7/02). › Rotores.
- F03D11/00
PDF original: ES-2516816_T3.pdf
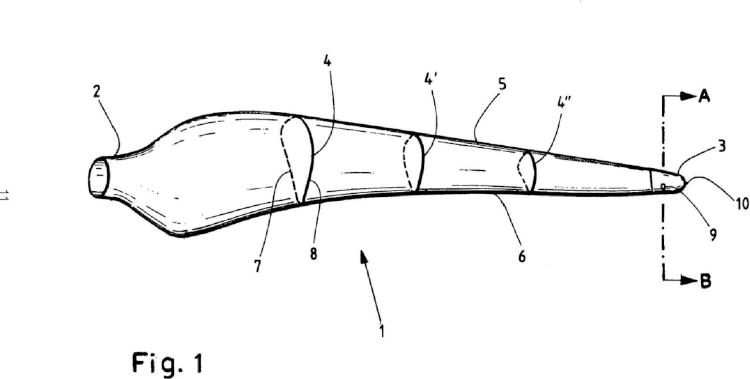
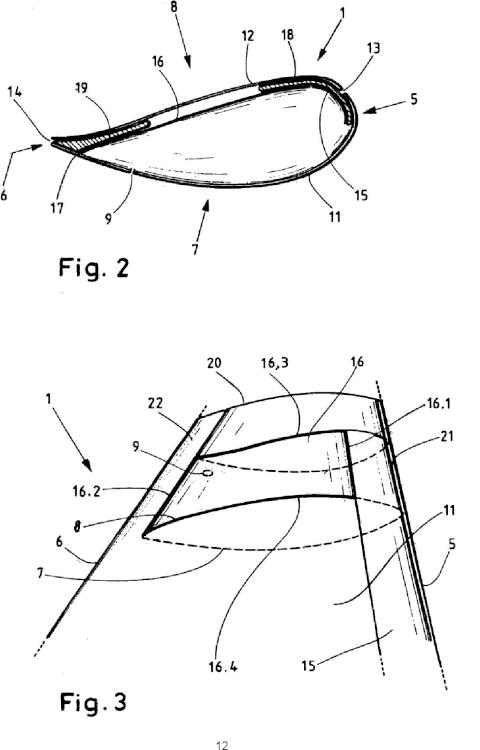
Fragmento de la descripción:
Pala de rotor con orificio de drenaje.
La invención se refiere a un procedimiento para la fabricación de una pala de rotor para una planta de energía eólica, que en la zona de la punta de pala de rotor presenta un orificio de drenaje, a una pala de rotor para una planta de energía eólica con un orificio de drenaje en la zona de la punta de pala de rotor, a una planta de energía eólica con una pala de rotor correspondiente y a la utilización de un elemento superficial en una pala de rotor para una planta de energía eólica, que en la zona de la punta de pala de rotor presenta un orificio de drenaje.
En el espacio interior de las palas de rotor de las plantas de energía eólica se acumula agua debido a la condensación o a la entrada directa y esta agua debe ser evacuada. Si el agua no puede salir, existe el peligro de que el agua se congele en invierno y la pala de rotor se dañe o se rompa como resultado de la dilatación provocada por la congelación. Otro peligro potencial radica en que debido a un rayo incidente en la punta de pala de rotor se evapore bruscamente el agua acumulada aquí, lo que puede dañar o romper asimismo la pala de rotor. Por tanto, en las palas de rotor de las plantas de energía eólica está previsto en la zona de la punta de pala de rotor un orificio de drenaje que une el lado interior de la pala de rotor a su lado exterior y posibilita la salida del agua.
Por el documento EP1342009B1 es conocida una pala de rotor para plantas de energía eólica que en la zona de la punta de pala de rotor presenta un receptor de rayos dispuesto en un orificio en la punta de pala. El receptor de rayos y el orificio forman conjuntamente un sistema de drenaje para la pala de rotor.
El documento DE102004028917A1 da a conocer una pala de rotor para una planta de energía eólica que presenta al menos una cavidad que colinda con un lado exterior de la pala de rotor y se encuentra unida al lado exterior mediante al menos un orificio de drenaje. En la cavidad está dispuesto un elemento colector permeable al agua, por ejemplo, un tamiz, de tal modo que el agua de la cavidad llega a través del elemento colector al orificio de drenaje. Esto impide que después de algún tiempo, el orificio de drenaje se llene de suciedad y partículas que están presentes asimismo en el interior de la pala de rotor y que pueden ser expulsadas con el agua a través del orificio de drenaje.
La fabricación de las puntas de pala de rotor descritas en estos documentos es muy complicada, porque presentan los orificios de drenaje en el extremo de la punta de pala, de modo que en este punto son necesarios un moldeo y una fabricación de mucha precisión. En caso de una construcción de una pala de rotor con semiconchas o con piezas moldeadas correspondientes, un orificio de drenaje correspondiente, dispuesto en una junta a pegar entre las semiconchas, forma además un punto estructural débil en la unión pegada, de modo que la pala de rotor está debilitada estructuralmente en la punta de pala de rotor.
Alternativamente, un orificio de drenaje puede estar previsto también en la zona de la punta de pala de rotor en el lado de succión o en el lado de presión de la pala de rotor. El borde de ataque de perfil de una pala de rotor está
unido al borde de salida de perfil de la pala de rotor mediante el lado de succión y el lado de presión. El lado de succión de la pala de rotor es el lado con la superficie de flujo más larga con respecto al lado de presión.
Incluso, si un orificio de drenaje está dispuesto en la zona de la punta de pala de rotor en el lado de succión o en el lado de presión de una pala de rotor, el agua es empujada hacia afuera del espacio interior de la pala de rotor a 45 través del orificio de drenaje por la fuerza centrífuga durante la rotación del rotor.
Otro efecto, que apoya el drenaje, consiste en que el agua es succionada hacia afuera del espacio interior de la pala de rotor debido a la baja presión del aire que circula a alta velocidad por delante del lado de succión, de acuerdo con el principio de Bernoulli. La pala de rotor no está cerrada usualmente de manera hermética en su raíz de pala, por lo 50 que se puede originar una corriente de aire debido a este efecto. Este efecto se produce también en un grado algo menor en el lado de presión de la pala de rotor, de modo que un orificio de succión puede estar dispuesto también en el lado de presión de una pala de rotor.
Una dificultad en la fabricación de un orificio de drenaje en el lado de succión o el lado de presión de la pala de rotor 55 en la zona de la punta de pala de rotor radica en que las palas de rotor están fabricadas generalmente a partir de semiconchas, es decir, piezas moldeadas que representan el lado de succión o el lado de presión y que se pegan entre sí.
En las plantas de energía eólica de mayor tamaño, las piezas moldeadas correspondientes están fabricadas en
general de fibras de vidrio y/o fibras de carbono mediante la técnica de compuestos de fibras, que se unen con resinas artificiales, por ejemplo, resinas de poliéster o resinas epoxi. Las semiconchas pueden estar fabricadas también en cada caso a partir de varias piezas moldeadas para el lado de presión y para el lado de succión respectivamente que se deben unir asimismo entre sí.
Para la fabricación de una unión segura, las piezas moldeadas del lado de presión se pegan en general con las piezas moldeadas del lado de succión. Como medios de unión resultan adecuados en particular los adhesivos o las mezclas de adhesivo, por ejemplo, a partir de resinas de poliéster y/o resinas epoxi. En la zona precisamente de la punta de pala de rotor se necesita al respecto una gran cantidad de adhesivo.
Dado que el medio de unión es líquido al pegarse las piezas moldeadas entre sí y resulta inevitable un exceso de adhesivo para garantizar una adhesión segura, el medio de unión puede circular sin control hacia el espacio interior de la pala de rotor. Dado que el adhesivo se distribuye sin control en el interior de la pala, es imposible realizar un orificio de drenaje siempre en el mismo punto, porque este punto puede estar cubierto de medios de unión. No obstante, si el orificio de drenaje se realiza siempre de manera profiláctica a una distancia suficientemente grande de la punta de pala, una cantidad considerable de agua se puede acumular en el interior de la pala en determinadas circunstancias.
El documento DE102008002983A1 se refiere a un dispositivo de drenaje de una pala de rotor para una planta de energía eólica con al menos una pala de rotor hueca. Un orificio de drenaje está dispuesto en una sección puntiaguda de la pala de rotor. Asimismo, están presentes una chapa guía dispuesta en el interior de la pala de rotor y en el interior del orificio de drenaje para limitar un flujo de partículas hacia el orificio de drenaje, así como un conducto de drenaje flexible dispuesto en el interior de la pala de rotor para unirse al orificio de drenaje con respecto al flujo. Un conducto de drenaje no flexible está dispuesto en el interior de la pala de rotor para unirse al conducto de drenaje flexible con respecto al flujo, estando configurado el conducto no flexible con una pluralidad de orificios para alojar un flujo de fluido procedente del interior de la pala de rotor. De manera adicional a los conductos de drenaje flexibles y no flexibles, la pala de rotor puede estar provista además de una chapa guía dispuesta en el interior de la pala de rotor y en el interior del orificio de drenaje para limitar el flujo de partículas hacia el orificio de drenaje.
El documento DE102008055479A1 se refiere a un procedimiento para la construcción de una pala de una planta de energía eólica. En este caso se fabrica una preforma del lado de presión y una preforma del lado de succión, así como un borde de ataque y/o un borde de salida. Para la fabricación del borde de ataque o del borde de salida se acopla una preforma de cubierta a una sección de la preforma del lado presión o a una sección de la preforma del lado de succión. Al menos una sección de la preforma del lado de presión o de la preforma del lado de succión cubre solapa al menos una sección de la preforma de la cubierta de unión.
Partiendo de este estado de la técnica, la presente invención tiene el objetivo de proporcionar un procedimiento para la fabricación de una pala de rotor para una planta de energía eólica, así como una pala de rotor correspondiente, que permita fabricar de manera eficiente y simple una pala de rotor, en la que se pueda realizar un orificio de drenaje en un punto predefinido en la zona de la punta de pala de rotor, independientemente del grado de exceso de adhesivo.
Este objetivo se consigue... [Seguir leyendo]
Reivindicaciones:
1. Procedimiento para la fabricación de una pala de rotor (1) para una planta de energía eólica, presentando la pala de rotor fabricada (1) en su extensión longitudinal, que se extiende esencialmente de una raíz 5 de pala de rotor (2) a una punta de pala de rotor (3) , al menos una zona, en la que la pala de rotor presenta un perfil de sección transversal aerodinámico (4, 4â?, 4â??) que presenta un borde de ataque de perfil (5) y un borde de salida de perfil (6) que están unidos mediante un lado de succión (7) y un lado de presión (8) del perfil de sección transversal (4, 4â?, 4â??) , y estando previstas al menos una primera pieza moldeada y al menos una segunda pieza moldeada (11, 12) fabricada en dirección longitudinal de la pala de rotor (1) para un lado de succión (7) y un lado de presión (8) de la pala de rotor (1) que se han de unir entre sí respectivamente en las zonas del borde de ataque de perfil (5) y el borde de salida de perfil (6) , caracterizado por las siguientes etapas de procedimiento:
al menos en la zona de la punta de pala de rotor (3) , un elemento de unión (15) se une o está unido con un lado interior de la al menos una primera pieza moldeada (11) en el borde de ataque de perfil (5) con ayuda de un medio de unión (18) , sobresaliendo el elemento de unión (15) de la primera pieza moldeada (11) en el borde de ataque de perfil (11) , en la zona de la punta de pala de rotor (3) , un elemento superficial (16) se une o está unido con el elemento de unión (15) en el borde de ataque de perfil (5) o está configurado en forma de una sola pieza con el elemento de unión (15) , finalizando el elemento superficial (16) esencialmente a ras con la primera pieza moldeada (11) en la zona del borde de salida de perfil (6) , la al menos una segunda pieza moldeada (12) se ensambla con la primera pieza moldeada (11) , uniéndose un lado interior de la segunda pieza moldeada (12) en el borde de ataque de perfil (5) con la parte del elemento de unión (15) que sobresale de la primera pieza moldeada (11) e introduciéndose un medio de unión (19) entre la primera y la segunda pieza moldeada (11, 12) en el borde de salida de perfil (6) , y un orificio de drenaje (9) está realizado o se dispone en la zona de la primera pieza moldeada (11) cerrada mediante el elemento superficial (16) del borde de salida de perfil (6) .
2. Procedimiento según la reivindicación 1, caracterizado porque el elemento superficial (16) se une a ras con la segunda pieza moldeada (12) por su borde (16.4) , opuesto a la punta de pala de rotor (3) , en la zona 30 situada entre los medios de unión (18, 19) .
3. Procedimiento según la reivindicación 1 ó 2, caracterizado porque el elemento superficial (16) con su borde (16.3) , dispuesto hacia la punta de pala de rotor, se conecta a un nervio de adaptador de pararrayos (20) o se dispone sobre un nervio de adaptador de pararrayos (20) .
4. Procedimiento según una de las reivindicaciones 1 a 3, caracterizado porque la primera y la segunda pieza moldeada (11, 12) , el elemento de unión (15) y/o el elemento superficial (16) se unen mediante pegado y/o laminación.
5. Procedimiento según una de las reivindicaciones 1 a 4, caracterizado porque antes de ensamblarse la primera y la segunda pieza moldeada (11, 12) , el medio de unión (18) se endurece o está endurecido entre la primera pieza moldeada (11) y el elemento de unión (15) en el borde de ataque de perfil (5) .
6. Pala de rotor (1) para una planta de energía eólica, presentando la pala de rotor (1) una extensión 45 longitudinal que se extiende esencialmente de una raíz de pala de rotor (2) a una punta de pala de rotor (3) , estando previsto al menos en una zona de la pala de rotor (1) un perfil de sección transversal aerodinámico (4, 4â?, 4â??) que presenta un borde de ataque de perfil (5) y un borde de salida de perfil (6) que están unidos mediante un lado de succión (7) y un lado de presión (8) del perfil de sección transversal (4, 4â?, 4â??) , y estando previstas para el lado de succión (7) y para el lado de presión (8) de la pala de rotor (1) respectivamente al menos una primera pieza 50 moldeada (11) y al menos una segunda pieza moldeada (12) que están unidas entre sí al menos en la zona de la punta de pala de rotor (3) en el borde de ataque de perfil (5) y en el borde de salida de perfil (6) con la ayuda de al menos un medio de unión (18, 19) y/o un elemento de unión (15) respectivamente, estando previsto un orificio de drenaje (9) en el lado de succión (7) o en el lado de presión (8) en la zona de la punta de pala de rotor (3) , caracterizada porque en la zona de la punta de pala de rotor (3) está previsto un elemento superficial (16) que se 55 extiende en dirección a la raíz de pala de rotor (2) hasta al menos el orificio de drenaje (9) , entrando en contacto el elemento superficial (16) con los medios de unión (18, 19) y/o los elementos de unión (15) en el borde de ataque de perfil (5) y el borde de salida de perfil (6) o está unido con los mismos y cerrándose a ras con la al menos una primera pieza moldeada (11) de manera impermeable en la zona del borde de salida de perfil (6) para medios de unión (18, 19) .
7. Pala de rotor (1) según la reivindicación 6, caracterizada porque el elemento superficial (16) comprende una estera de fibra de vidrio con una o varias capas o una chapa de aluminio.
8. Pala de rotor (1) según la reivindicación 6 ó 7, caracterizada porque el elemento superficial (16) se
conecta hacia la punta de pala de rotor (3) a un nervio de adaptador (20) de un pararrayos (10) o se dispone sobre un nervio de adaptador (20) de un pararrayos (10) .
9. Pala de rotor (1) según una de las reivindicaciones 6 a 8, caracterizada porque el elemento superficial (16) está unido con la segunda pieza moldeada (12) por su extremo (16.4) opuesto a la punta de pala de rotor (3) en la zona situada entre los medios de unión (18, 19) y se encuentra a una distancia inferior a 10 mm, en particular inferior a 3 mm, respecto a la segunda pieza moldeada (12) .
10. Pala de rotor (1) según una de las reivindicaciones 6 a 9, caracterizada porque el elemento de unión (15) y el elemento superficial (16) están configurados en forma de una sola pieza. 15
11. Pala de rotor (1) según una de las reivindicaciones 6 a 10, caracterizada porque el al menos un elemento de unión (15) comprende en el borde de ataque de perfil (5) una solapa adhesiva, en particular tricotada o tejida, que cubre el lado de succión (7) y el lado de presión (8) y está pegada y/o laminada con la primera y la segunda pieza moldeada (11, 12) .
12. Planta de energía eólica con una pala de rotor (1) según una de las reivindicaciones 6 a 11.
13. Utilización de un elemento superficial (16) en una pala de rotor (1) según una de las reivindicaciones 6
a 11 para una planta de energía eólica, que en la zona de la punta de pala de rotor (3) presenta un orificio de 25 drenaje (9) para mantener el orificio de drenaje (9) libre de un medio de unión (18, 19) .
Patentes similares o relacionadas:
Turbina eólica con una luz de obstáculo de vuelo, del 23 de Octubre de 2019, de Senvion GmbH: Turbina eólica con una torre , que presenta al menos una luz de obstáculo de vuelo que irradia hacia fuera, que está conectada con una línea de suministro , […]
Sistema de regulación de potencia activa de un parque eólico, del 28 de Diciembre de 2018, de GAMESA INNOVATION & TECHNOLOGY, S.L: Sistema de regulación de potencia activa de un parque eólico, comprendiendo el parque eólico un grupo de aerogeneradores (Ai), una red de comunicaciones […]
Supervisión de la operación de una planta de generación eólica, del 16 de Octubre de 2018, de LM Wind Power International Technology II ApS: Un método de supervisión de la operación de una planta de generación eólica, en el que la supervisión comprende la recogida de datos de operación […]
Bomba de aceite de capacidad variable, del 30 de Mayo de 2018, de VESTAS WIND SYSTEMS A/S: Un método para el control de una presión del fluido en un sistema de suministro de fluido de una turbina eólica, incluyendo el sistema de suministro de […]
Aerogenerador, del 25 de Abril de 2018, de Wobben Properties GmbH: Aerogenerador con una torre , que se funda sobre un cimiento, y un módulo de potencia , presentando el módulo de potencia al menos un transformador y/o […]
Dispositivo que incluye un sistema adaptado para uso en compensación de temperatura de mediciones de tensión de estructuras reforzadas con fibra, del 7 de Marzo de 2018, de LM Wind Power International Technology II ApS: Un dispositivo que comprende una parte reforzada con fibra e incluye al menos un sistema adaptado para uso en la compensación de temperatura […]
Un método para fabricar una pala para una turbina eólica y una pala que comprende medios conductores segmentados, del 20 de Diciembre de 2017, de LM Wind Power International Technology II ApS: Un método para fabricar una pala reforzada con fibra para una planta de energía eólica, dicha pala se configura con por lo menos una cubierta de pala y medios para […]
Generador eólico, del 4 de Octubre de 2017, de GE Wind Energy (Norway) AS: Central eólica con una turbina eólica que comprende un eje de la turbina rotativo y un eje del generador , que puede ser una prolongación […]