PROCEDIMIENTO DE MOLDEO POR ENRASAMIENTO.
Un procedimiento de moldeo por enrasamiento, para fabricar artículos (300) de acolchamiento de gel elastómero gelatinoso,
comprendiendo el procedimiento las etapas de: obtener un molde (100) de enrasamiento, teniendo el molde de enrasamiento un cuerpo rígido, siendo el molde de enrasamiento un molde de cara abierta, teniendo el molde de enrasamiento una configuración estructural en dicho cuerpo rígido en la que se puede conformar un gel para que adopte una estructura geométrica deseada, incluyendo dicha configuración estructural ranuras (101, A111) en el citado cuerpo rígido, que acceden a un cabezal (200) de inyección, teniendo dicho cabezal (200, 220) de inyección una pluralidad de canales (202, 221, 222) de distribución en el mismo, a través de los cuales puede fluir material termoplástico, terminando dichos canales de distribución en puertos (211, 223, 224) de salida a través de los cuales el material termoplástico puede salir de dicho cabezal de inyección y entrar en el citado molde de enrasamiento, acceder a una fuente de bombeo, utilizar dicha fuente de bombeo para presurizar el material termoplástico y forzarlo en el citado cabezal de inyección, a través de dichos canales de distribución de dicho cabezal de inyección, hacia fuera de los citados puertos de salida de dicho cabezal de inyección, hacia el citado molde de enrasamiento, a través de las citadas ranuras de dicho molde de enrasamiento y hacia fuera de dicho molde de enrasamiento, y recibir un elemento de acolchamiento moldeado por medio de dicho molde de enrasamiento
Tipo: Patente Internacional (Tratado de Cooperación de Patentes). Resumen de patente/invención. Número de Solicitud: PCT/US2004/004382.
Solicitante: EDIZONE, L.C.
Nacionalidad solicitante: Estados Unidos de América.
Dirección: 123 EAST 200 NORTH ALPINE, UT 84004 ESTADOS UNIDOS DE AMERICA.
Inventor/es: PEARCE,TONY,M.
Fecha de Publicación: .
Fecha Solicitud PCT: 13 de Febrero de 2004.
Fecha Concesión Europea: 7 de Julio de 2010.
Clasificación Internacional de Patentes:
- B29C33/00J2
Clasificación PCT:
- C08J5/00 QUIMICA; METALURGIA. › C08 COMPUESTOS MACROMOLECULARES ORGANICOS; SU PREPARACION O PRODUCCION QUIMICA; COMPOSICIONES BASADAS EN COMPUESTOS MACROMOLECULARES. › C08J PRODUCCION; PROCESOS GENERALES PARA FORMAR MEZCLAS; TRATAMIENTO POSTERIOR NO CUBIERTO POR LAS SUBCLASES C08B, C08C, C08F, C08G o C08H (trabajo, p. ej. conformado, de plásticos B29). › Fabricación de artículos o modelado de materiales que contienen sustancias macromoleculares (fabricación de membranas semipermeables B01D 67/00 - B01D 71/00).
Clasificación antigua:
- C08J5/00 C08J […] › Fabricación de artículos o modelado de materiales que contienen sustancias macromoleculares (fabricación de membranas semipermeables B01D 67/00 - B01D 71/00).
Países PCT: Austria, Bélgica, Suiza, Alemania, Dinamarca, España, Francia, Reino Unido, Grecia, Italia, Liechtensein, Luxemburgo, Países Bajos, Suecia, Mónaco, Portugal, Irlanda, Eslovenia, Finlandia, Rumania, Chipre, Lituania, Letonia, Ex República Yugoslava de Macedonia, Albania.
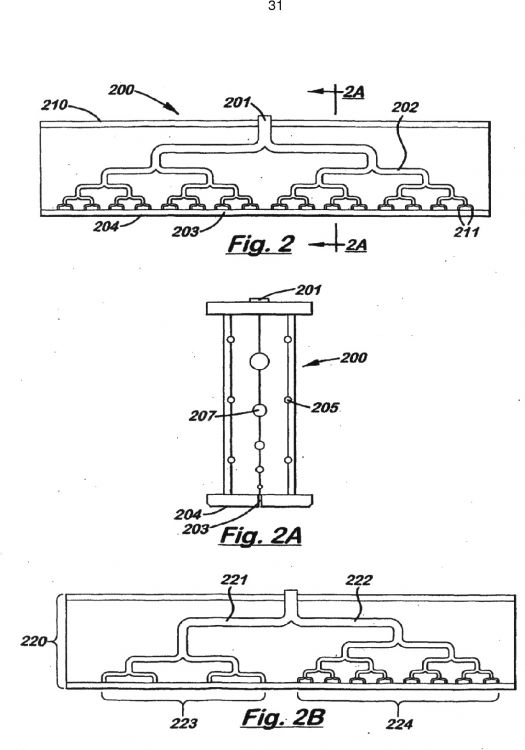
Fragmento de la descripción:
ANTECEDENTES
La presente divulgación se refiere a procesos de fabricación que utilizan moldes de cara abierta que son útiles en la fabricación de materiales moldeables, tal como materiales termoplásticos, y son particularmente útiles en la fabricación de artículos elastoméricos, incluyendo artículos que comprenden gel elastomérico. Los procedimientos y las estructuras son especialmente útiles en el moldeo de cara abierta de materiales que son de alta viscosidad o que en su caso tienen dificultad para fluir en las cavidades de un molde de cara abierta.
El documento US 6.413.458 divulga un procedimiento para la fabricación de un artículo de elastómero gelatinoso que comprende una serie de etapas. Las etapas incluyen seleccionar un plastificante, seleccionar un copolímero tribloque de configuración general A-B-A, mezclar el plastificante y el copolímero tribloque tal como mediante mezcla por fusión o utilizando un husillo de mezcla con el fin de producir un elastómero gelatinoso, permitir que el elastómero gelatinoso se enfríe, seleccionar un dispositivo de conformación tal como una matriz o molde, fundir el elastómero gelatinoso, y forzar el elastómero gelatinoso en el dispositivo de conformación, con el fin de formar una pieza de elastómero gelatinoso.
SUMARIO
Se divulgan procedimientos de moldeo por enrasamiento.
La presente invención proporciona un procedimiento de moldeo por enrasamiento para la fabricación de gel elastómero gelatinoso de acolchado de artículos, comprendiendo el procedimiento las etapas de: obtener un molde de enrasamiento, teniendo el molde de enrasamiento un cuerpo rígido, siendo el molde de enrasamiento un molde de cara abierta, teniendo el molde de enrasamiento una configuración estructural en dicho cuerpo rígido en la que el gel puede ser conformado para que adopte una estructura geométrica deseada, incluyendo dicha configuración estructural ranuras en el citado cuerpo rígido; obtener acceso a un cabezal de inyección, teniendo dicho cabezal de inyección una pluralidad de canales de distribución en el mismo a través de los cuales puede fluir material termoplástico, terminando dichos canales de distribución en puertos de salida a través de los cuales el material termoplástico puede salir del citado cabezal de inyección y entrar en el citado molde de enrasamiento; acceder a una fuente de bombeo, utilizando dicha fuente de bombeo para presurizar el material termoplástico y forzarlo en el citado cabezal de inyección, a través de dichos canales de distribución de dicho cabezal de inyección, hacia fuera de los citados puertos de salida de dicho cabezal de inyección, hacia el citado molde de enrasamiento, a través de las citadas ranuras de dicho molde de enrasamiento y hacia fuera de dicho molde de enrasamiento, y recibir un elemento de acolchamiento moldeado mediante el citado molde de enrasamiento.
BREVE DESCRIPCIÓN DE LOS DIBUJOS
Las Figuras 1 y 1A representan un ejemplo de molde de enrasamiento;
las Figuras 2, 2A y 2B representan otras vistas de un ejemplo de molde de enrasamiento;
la Figura 3 representa un ejemplo de un componente de colchón de gel realizado mediante un procedimiento de moldeo por enrasamiento.
DESCRIPCIÓN DETALLADA
La Figura 1 representa la cara superior de un molde 100 de cara abierta, en este caso un molde de cara abierta para un cubrecolchones. El molde 100 es un componente de una realización. El molde 100 de cara abierta está además caracterizado por comprender un panal 104. El panal 104 está formado por ranuras 101 (perpendiculares o formando otros ángulos) que se entrecruzan unas con otras desde carriles 102 laterales que circundan el perímetro 105 del panal 104. Las ranuras 101 están distanciadas de modo que núcleos 103 de moldeo cuadrados [(o configurados de otra forma)] están distribuidos a través del panal 104. El molde 100 puede ser creado en una diversidad de tamaños para colchones de cualquier tamaño deseado. Cuando el colchón tiene un borde perimetral de espuma (no representado) de aproximadamente 15 cm, el panal 104 de gel podría tener una longitud de alrededor de 170 cm y una anchura de alrededor de 120 cm. En esta realización, las ranuras 101 tienen una profundidad de alrededor de 7 cm y los núcleos 103 de moldeo tienen normalmente una altura de 7 cm.
En una realización, el molde 100 está fabricado con una placa A110 metálica según se ha representado en la Figura 1A. Las ranuras A111 pueden ser fabricadas en el molde 100 mediante mecanización con una cuchilla de sierra circular (u otra herramienta de corte) de aproximadamente el 80% a través del espesor de una placa A110 metálica para formar los núcleos A113 de moldeo. En otras realizaciones, el molde 100 puede estar fabricado con un polímero no deformable tal como plástico ..., con madera, cerámica u otro material que no experimente deformación a la temperatura de inyección. Después de que las ranuras A111 han sido mecanizadas, el perímetro A115 se desbasta, en el 80% o hasta el 100% de profundidad. Se taladran orificios A116 para pernos en la placa A110 metálica.
Haciendo de nuevo referencia a la Figura 1, el molde 100 puede ser empernado o fijado de otro modo en cuatro carriles 102 laterales. Los carriles 102 laterales pueden estar hechos de diversos materiales incluyendo materiales metálicos y no metálicos. Se puede utilizar aluminio en una realización para un calentamiento y un enfriamiento rápidos. En otra realización, el acero puede servir como un material apropiado para los carriles laterales. Todavía en otra realización, se podrían utilizar materiales no metálicos.
Según se muestra en la Figura 1, el panal 104 presenta un patrón para las ranuras
101. Como ejemplo, las ranuras 101 forman un ángulo de 45 grados con el perímetro 105 del molde 100. En esta configuración en “x”, el material termoplástico (no representado) que se introduce en el molde con una trayectoria de circulación según la dirección “ascendente” de la Figura 1, puede fluir fácilmente alrededor de los núcleos 103 de moldeo. En una realización alternativa, las ranuras 101 forman un ángulo de 90 grados con el perímetro 105 para formar una configuración en “+”. Un panal 104 de gel con configuración en “x” da como resultado que el material inyectado se encuentre en una esquina 106 en vez de en un centro 107 de un núcleo 103 de moldeo, y que continúe después el flujo alrededor de un núcleo adyacente. Por el contrario, la experiencia de los inventores en cuanto a la configuración en “+” ha dado como resultado que el material se encuentre en un centro 107 de un núcleo de moldeo. Cuando el material fundido rellena el panal 104 de esa manera, se podrían introducir líneas de trenzado en la pieza moldeada, que pueden debilitar la pieza.
Otro componente de las realizaciones ha sido representado en la Figura 2. La Figura 2 muestra una vista en sección transversal del cabezal 200 de inyección. El cabezal 200 de inyección comprende una cara 210 superior y una cara 204 inferior. En la cara 210 superior, una entrada 201 abre en una red de canales 202 de distribución. El material fundido (no representado) entra en la entrada 201 y fluye a través de los canales 202 de distribución hasta que el material sale por las salidas 211 de la cara 204 inferior, y hacia la ranura 203. El canal de distribución empieza en la entrada 201 como un solo canal, y se divide en dos canales simétricamente.
Los canales 202 de distribución pueden dividirse de nuevo y de nuevo, hasta que existan varios canales. Cuanto más frecuentemente se dividan los canales, más salidas 211 aparecerán en la ranura 203. La ventaja de incrementar el número de salidas reside en que permite una distribución más uniforme del material fundido en la ranura. Según se ha representado en la Figura 2, los canales de distribución, en una realización, se dividen con frecuencia uniforme y con distribución uniforme de las salidas.
En otra realización, representada en la Figura 2B, los canales de distribución no se dividen con frecuencia uniforme ni con uniformidad en la distribución de salidas. En esta realización, el material fundido fluye a través del cabezal 220 de distribución más fácilmente hasta el canal 221 de distribución y menos fácilmente hasta el canal 222 de distribución. Cuando el cabezal 200 de inyección está configurado de esta manera, se puede aplicar una distribución no uniforme de material fundido a un molde...
Reivindicaciones:
1. Un procedimiento de moldeo por enrasamiento, para fabricar artículos (300) de acolchamiento de gel elastómero gelatinoso, comprendiendo el procedimiento las etapas de:
obtener un molde (100) de enrasamiento,
teniendo el molde de enrasamiento un cuerpo rígido,
siendo el molde de enrasamiento un molde de cara abierta,
teniendo el molde de enrasamiento una configuración estructural en dicho cuerpo rígido en la que se puede conformar un gel para que adopte una estructura geométrica deseada, incluyendo dicha configuración estructural ranuras (101, A111) en el citado cuerpo rígido, que acceden a un cabezal (200) de inyección,
teniendo dicho cabezal (200, 220) de inyección una pluralidad de canales (202, 221, 222) de distribución en el mismo, a través de los cuales puede fluir material termoplástico,
terminando dichos canales de distribución en puertos (211, 223, 224) de salida a través de los cuales el material termoplástico puede salir de dicho cabezal de inyección y entrar en el citado molde de enrasamiento,
acceder a una fuente de bombeo,
utilizar dicha fuente de bombeo para presurizar el material termoplástico y forzarlo en el citado cabezal de inyección, a través de dichos canales de distribución de dicho cabezal de inyección, hacia fuera de los citados puertos de salida de dicho cabezal de inyección, hacia el citado molde de enrasamiento, a través de las citadas ranuras de dicho molde de enrasamiento y hacia fuera de dicho molde de enrasamiento, y
recibir un elemento de acolchamiento moldeado por medio de dicho molde de enrasamiento.
2. Un procedimiento de moldeo por enrasamiento de acuerdo con la reivindicación 1, en el que:
el molde de enrasamiento tiene forma de panal en el citado cuerpo rígido, en el que se puede conformar el gel para que adopte una estructura geométrica deseada,
el molde de enrasamiento incluye una pluralidad de ranuras (101, A111) que se entrecruzan en el citado cuerpo rígido para formar dicha configuración de panal que establece un núcleo de molde,
incluyendo una etapa de obtener carriles (102) laterales, y
sujetar dichos carriles laterales al perímetro (105, A115) del molde con el fin de circundar el perímetro del molde con carriles laterales, en el que,
dichos canales (202, 221, 222) de distribución están subdivididos en canales de sub-distribución, y
dicho cabezal (200, 220) de inyección incluye al menos un elemento de calentamiento en el interior del mismo, para calentar material termoplástico, y que está situado adyacente a dicho molde de enrasamiento en una posición tal que el material termoplástico puede fluir desde dichos canales de distribución del cabezal de inyección, hacia fuera de dichos puertos de salida y al interior de las citadas ranuras del molde de enrasamiento.
3. Un procedimiento según la reivindicación 1 ó 2, en el que dicha etapa de recuperación incluye terminar periódicamente el bombeo de material termoplástico dentro del citado molde de enrasamiento,
y durante ese período de terminación, retirar el material termoplástico moldeado de dicho molde (100) de enrasamiento.
4. Un procedimiento según la reivindicación 1 ó 2, en el que dicho bombeo es un proceso continuo, y el material termoplástico moldeado es recuperado de dicho molde de enrasamiento a medida que se fuerza el material termoplástico no moldeado en el citado molde (100) de enrasamiento.
5. Un procedimiento según la reivindicación 1 ó 2, en el que el material termoplástico moldeado se recupera de dicho molde (100) de enrasamiento mediante corte del mismo según sale de dicho molde de enrasamiento debido al nuevo material termoplástico que está siendo forzado dentro de dicho molde (100) de enrasamiento.
6. Un procedimiento según la reivindicación 1 ó 2, en el que al menos algunas de las citadas ranuras (101, A111) están cortadas en no más del 80% del pasaje a través de dicho cuerpo rígido.
7. Un procedimiento según la reivindicación 1 ó 2, en el que al menos algunas de las citadas ranuras (101, A111) están cortadas en todo el pasaje a través de dicho cuerpo rígido.
8. Un procedimiento según la reivindicación 1 ó 2, en el que dicho cuerpo rígido es metálico.
9. Un procedimiento según la reivindicación 1 ó 2, en el que dicho cuerpo rígido es no-metálico.
10. Un procedimiento según la reivindicación 1 ó 2, en el que al menos algunas de las citadas ranuras (101, A111) se cruzan entre sí con una configuración en “X”.
11. Un procedimiento según la reivindicación 1 ó 2, en el que al menos algunas de las citadas ranuras (101, A111) se cruzan entre sí con una configuración en “+”.
12. Un procedimiento según la reivindicación 1 ó 2, en el que dichas ranuras (101,
A111) están dimensionadas para permitir que el material termoplástico fluya a través de las
mismas cuando es calentado.
13. Un procedimiento según la reivindicación 1 ó 2, que comprende además al menos un canal de refrigeración en el citado cabezal (200, 220) de distribución.
14. Un procedimiento según la reivindicación 1 ó 2, que comprende además la
etapa de establecer una distancia deseada entre dicho cabezal (200, 220) de distribución y
el citado molde (100) de enrasamiento con anterioridad al flujo del material termoplástico.
15. Un procedimiento según la reivindicación 1 ó 2, en el que dicho material
10 15 termoplástico incluye un copolímero tribloque A-B-A. 16.Un procedimiento según la reivindicación termoplástico incluye un plastificante. 15, 20 25 30en el que dicho material
Patentes similares o relacionadas:
Métodos, composiciones y mezclas para formar artículos que tienen resistencia al resquebrajamiento por estrés ambiental mejorada, del 15 de Julio de 2020, de VIVA HEALTHCARE PACKAGING LIMITED: Un proceso para la fabricación de artículos flexibles de paredes delgadas que comprende las etapas de moldeo por inyección de una mezcla de polímeros que tiene un MFI > […]
Métodos para formar artículos que tienen resistencia al agrietamiento por tensión ambiental, del 8 de Julio de 2020, de VIVA HEALTHCARE PACKAGING LIMITED: Un proceso para la fabricación de un artículo de paredes delgadas flexible, dicho proceso comprende moldear por inyección una mezcla de (a) por lo […]
Procedimiento para la producción de parches o elementos de celulosa estructurados y dispositivos fabricados utilizando dicho procedimiento, del 10 de Junio de 2020, de ETH ZURICH: Procedimiento para la producción autoensamblada de un elemento de celulosa estructurado topográficamente en la superficie , en el que, en una primera etapa se […]
TABLERO ECOLOGICO, del 28 de Abril de 2020, de CAMBA GARCIA, David: 1. Tablero ecológico, caracterizado porque comprende entre el 60% y el 85% en peso de cascarilla de arroz y entre un 40% y 15% de adhesivo urea-formaldehído, […]
Uso de polielectrolitos enlazados para la adsorción de cationes metálicos, del 19 de Febrero de 2020, de DTNW Deutsches Textilforschungszentrum Nord-West gemeinnützige GmbH: Uso de un material polimérico de soporte con una dotación de polielectrolitos fijados sobre él, que es adecuado para adsorber cationes metálicos mono- y divalentes, […]
Preparaciones de plastificantes, del 22 de Enero de 2020, de LANXESS DEUTSCHLAND GMBH: Preparación, que contiene: a) del 5 - 50 % en peso de triacetina, y b) del 50 - 95 % en peso de uno o varios plastificantes de la serie de poliéster de ácido adípico, […]
Mezcla de poliéster/policarbonato con excelente estabilidad térmica y estabilidad cromática, del 4 de Diciembre de 2019, de SK CHEMICALS CO., LTD.: Mezcla de poliéster/policarbonato que comprende: (a) P(ET-CT) [poli(tereftalato de etileno-co-tereftalato de 1,4-ciclohexilendimetileno)] […]
Composiciones altamente ramificadas y procedimientos para la producción de las mismas, del 27 de Noviembre de 2019, de EXXONMOBIL CHEMICAL PATENTS INC.: Una poliolefina altamente ramificada, que comprende: unidades derivadas de olefinas; en donde la poliolefina altamente ramificada tiene: […]