Síntesis de biodiesel.
Un método para la síntesis de biodiesel por reacción de un aceite natural con metanol en presencia de uncatalizador alcalino,
en el que una mezcla de aceite natural, metanol y el catalizador alcalino se suministra enuna dirección a lo largo de un reactor tubular que tiene un extremo de entrada y un extremo de salida a unavelocidad suficiente de manera que el flujo es transitorio o turbulento, en donde la mezcla de aceite natural,metanol y catalizador alcalino es turbulenta cuando esta entra en el reactor tubular y en donde la turbulencia esgenerada por inyección de un flujo de metanol, opcionalmente con el catalizador alcalino disuelto en este, en elflujo del aceite natural a un ángulo a la dirección del flujo del aceite natural, en donde el reactor tubular tiene undiámetro en el intervalo de 6-200 mm y una longitud en el intervalo de 30 a 100 metros, y el reactor tubularincluye elementos de mezclado estático que están presentes para al menos el primer 20 % de la longitud delreactor tubular y para al menos el ultimo 30 % de la longitud del reactor tubular, y en donde una porción delreactor tubular que comprende al menos el 20 % de la longitud del reactor tubular y es desplazado desde losextremos del mismo no tiene elementos de mezclado, tal que en la primera y última longitudes del reactortubular los reactivos son mezclados en una dirección normal a la dirección del flujo de modo que los reactivosse mezclan en una dirección normal a la dirección del flujo en un grado mayor que en una dirección paralela ala dirección de flujo y de tal manera que el tiempo necesario para que el 90% de los elementos de fluido pasena través del reactor esté dentro del 20% del tiempo medio de permanencia del reactivo en el reactor.
Tipo: Patente Internacional (Tratado de Cooperación de Patentes). Resumen de patente/invención. Número de Solicitud: PCT/GB2007/004010.
Solicitante: Renewable Holdings Limited.
Nacionalidad solicitante: Reino Unido.
Dirección: 60/62 Old London Road Kingston Upon Thames Surrey KT2 6QZ REINO UNIDO.
Inventor/es: DAVIES,OWEN MATTHEW, JACKSON,RICHARD DAVID.
Fecha de Publicación: .
Clasificación Internacional de Patentes:
- B01J19/24 TECNICAS INDUSTRIALES DIVERSAS; TRANSPORTES. › B01 PROCEDIMIENTOS O APARATOS FISICOS O QUIMICOS EN GENERAL. › B01J PROCEDIMIENTOS QUÍMICOS O FÍSICOS, p. ej. CATÁLISIS O QUÍMICA DE LOS COLOIDES; APARATOS ADECUADOS. › B01J 19/00 Procedimientos químicos, físicos o físico-químicos en general; Aparatos apropiados. › Reactores fijos sin elementos internos móviles (B01J 19/08, B01J 19/26 tienen prioridad; de partículas inmóviles B01J 8/02).
- C11C3/00 QUIMICA; METALURGIA. › C11 ACEITES, GRASAS, MATERIAS GRASAS O CERAS ANIMALES O VEGETALES; SUS ACIDOS GRASOS; DETERGENTES; VELAS. › C11C ACIDOS GRASOS OBTENIDOS A PARTIR DE GRASAS, ACEITES O CERAS; VELAS; GRASAS, ACEITES O ACIDOS GRASOS OBTENIDOS POR MODIFICACION QUIMICA DE GRASAS, ACEITES O ACIDOS GRASOS. › Grasas, aceites o ácidos grasos obtenidos por modificación química de grasas, aceites o ácidos grasos, p. ej. por ozonólisis (grasas o aceites sulfonados C07C 309/62; grasas epoxidadas C07D 303/42; aceites vulcanizados, p.ej. pseudocaucho C08H 3/00).
PDF original: ES-2425371_T3.pdf
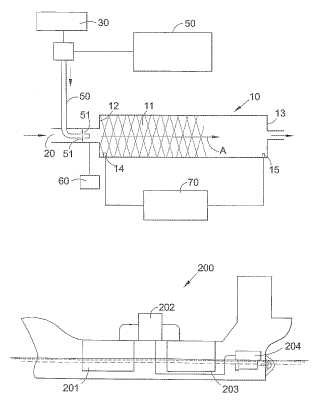
Fragmento de la descripción:
Síntesis de biodiesel
La presente invención se refiere a un método y un aparato para la síntesis de biodiesel y una nave que comprende un aparato para la síntesis de biodiesel.
El biodiesel se fabrica por transesterificación de aceites/grasas de origen animal o vegetal. Tales aceites y grasas comprenden ésteres de triglicéridos que contienen unidades de ácido graso de cadena larga. En la síntesis de biodiesel, tales triglicéridos son transesterificados con alcoholes de cadena corta, típicamente metanol, y en ocasiones se ha usado etanol entre otros alcoholes. La reacción se puede llevar a cabo en presencia de un catalizador ácido o básico y, en general, los catalizadores básicos son más rápidos, el hidróxido de sodio o hidróxido de potasio son los más comunes. Típicamente, el hidróxido de sodio o hidróxido de potasio con un nivel de agua relativamente bajo (particularmente en forma de polvo o gránulo) se mezcla con el alcohol, por ejemplo metanol, y luego se mezclan con el aceite.
Para la producción comercial de biodiesel, se prefiere alcanzar un grado relativamente alto de conversión del éster glicérido en biodiesel (preferentemente de 96.5% o superior) dentro de un período de tiempo razonable. En el pasado, se encontró que el tiempo requerido para alcanzar un alto nivel de conversión es comparativamente largo.
Un problema que ha sido encontrado es que el metanol básico y el aceite no se mezclan muy bien, debido a sus diferentes densidades y debido a la naturaleza coalescente de sus fases respectivas.
Los enfoques convencionales para mejorar la cinética global han incluido el aumento de la temperatura, y la aplicación de un alto grado de cizallamiento por agitación.
Por ejemplo, en el pasado, la reacción de transesterificación se llevó a cabo en reactores por carga provistos de agitadores. Aunque se han obtenido resultados razonables con tales reactores, para el procesamiento industrial a gran escala, se prefiere un sistema continuo, en lugar de un proceso discontinuo.
Un reactor tubular es un diseño adecuado de reactor continuo para la fabricación de biodiesel.
En los reactores tubulares se han usado varios dispositivos para proporcionar un alto cizallamiento, pero muchos de ellos (por ejemplo, chorros, mezcladores mecánicos, flujo oscilante) requieren niveles de entrada de alta energía, que son costosos de mantener o implican un equipamiento relativamente sensible. En muchos casos, aún no se alcanzan los altos grados de conversión en un período de tiempo práctico.
La WO99/26913 da a conocer un método para la producción de éster metílico de ácido graso en el que se usa un mezclador estático que crea una turbulencia alta o potente. A través del mezclador estático hay una caída sustancial de presión. Esto requiere presiones muy altas para operar, lo que es antieconómico.
La EP0041204 detalla un proceso para la producción continua de monoglicéros de ácidos grasos usando un reactor tubular que comprende elementos de mezclado estático. La presente invención tiene por objeto superar los problemas de la técnica anterior.
Los inventores se han dado cuenta de que la reacción de transesterificación en sí misma es bastante rápida (es decir, que tiene una elevada constante de velocidad) y que el tiempo requerido para alcanzar el nivel deseado de terminación no está limitado por la propia constante de velocidad, ni simplemente por factores estéricos (área de superficie de reacción de las gotas) , sino por factores de transferencia de masa y factores estequiométricos.
Los factores de transferencia de masa se pueden explicar considerando una gota de metanol básico rodeada de triglicéridos a una temperatura, por ejemplo, de alrededor de 60 °C. La reacción en la superficie de las gotas se llevaría a cabo muy rápidamente creando una capa de éster metílico (biodiesel) y glicerina, mono y di glicéridos. Esto resultaría en un mar de triglicéridos que rodea al éster metílico (capa exterior) , glicerina, mono y di glicéridos (capa media) y la gota de metanol básico (núcleo central) . Para que la reacción continúe, el éster metílico tendrá que difundirse en los triglicéridos circundantes y la glicerina tendría que ser diluida continuamente por el metanol básico desde adentro del núcleo en reducción de la gota. En consecuencia, la reacción se vuelve limitada por la velocidad de difusión de los reactivos y productos de reacción, a pesar de que los mono y di glicéridos poseen una naturaleza surfactante. Esta limitación se hace aún más evidente dentro de aproximadamente el último cuarto de la reacción, después de que por ejemplo el 75% del éster ha sido creado, cuando el porcentaje de glicerina en las cercanías de las gotas concentradas de metanol básico reduce excesivamente la velocidad de reacción, por lo que hace que el cuarto final de la reacción tarde más que los tres cuartos anteriores en un factor significativo. El metanol es altamente soluble en glicerol. Este efecto ha sido superado en la técnica anterior mediante la eliminación de glicerina en esta etapa, a través de un proceso de separación. A medida que la glicerina removida ocupa el volumen del metanol básico original adicionado, se requiere un segundo proceso de inyección y mezclado de metanol básico para completar la reacción, después de lo cual se requiere otra etapa de remoción de glicerina. Además, después de la inyección inicial de metanol y antes de la primera etapa de remoción de glicerina, está presente una proporción significativa de mono y di glicéridos, incrementando la propensión para el éster metílico a disolverse en la glicerina y ser removido. Este biodiesel, si no se extrae por otro proceso, reduce de forma significativa el rendimiento global del proceso.
Por consiguiente, hay un problema de que un proceso de remoción de glicerina de dos etapas crea un retraso significativo, complejidad e ineficiencia en el proceso.
En otra parte en la técnica anterior, se prevé una única inyección de metanol, el cual, si se proporciona en proporciones suficientes puede completar la reacción hasta más allá del 96.5% de conversión del éster en un solo paso. En general, los parámetros del proceso que conducen a tales altos niveles de conversión no se explican y no son ampliamente entendidos. Además, algunos procesos de la técnica anterior alcanzan el resultado deseado mediante el uso de un exceso muy alto de metanol, tal como uno-a-uno por volumen, lo cual requiere posteriormente una recuperación del metanol por destilación extremadamente costosa. Los inventores se han dado cuenta que para reducir al mínimo los pasos del proceso, optimizar el uso de metanol y la recuperación en relación con toda la economía del proceso y maximizar la eficiencia del catalizador, reduciendo así la carga en las etapas de remoción de catalizador en el flujo inferior, es necesario mantener un cierto nivel de turbulencia dentro del reactor por al menos el 30 % de la longitud del reactor (si es uniforme en el área de la sección transversal) . Esta etapa final de mezclado supera los problemas de transferencia de masa creados y exacerbados por la generación de la glicerina inherentemente inerte y acorta la fase final de la conversión a segundos en lugar de minutos u horas Al considerar factores estequiométricos, la posición del equilibrio entre el éster glicérido y el éster de alcohol de cadena corta (el biodiesel) se determina por la cantidad relativa de aceite y del alcohol de cadena corta. En una reacción continua en un reactor tubular, diferentes etapas en el reactor tubular representan diferentes etapas en el avance de la reacción. Las etapas posteriores tienen menores cantidades de alcohol de cadena corta y de aceite. Los inventores se han dado cuenta de que si el volumen de reacción de la última parte de la reacción se mezcla por flujo de retorno con el volumen de reacción de una parte inicial de la reacción (la parte del flujo superior del reactor tubular) , los reactivos se pueden diluir con los productos de reacción (glicerol y éster del alcohol de cadena corta) que puede afectar negativamente la posición del equilibrio y la velocidad a la que se alcanza.
Además, si hay un alto nivel de mezclado de reactivos de diferentes etapas en el proceso, existe el riesgo de que alguna parte del volumen de reacción pasará efectivamente a través del reactor antes de que haya tenido tiempo para reaccionar completamente, de nuevo, afectando negativamente el grado total de transformación del aceite hasta éster metílico.
La presente invención, en particular, tiene por objeto proporcionar un procedimiento continuo para la reacción de aceite natural con un alcohol de cadena corta en presencia de un... [Seguir leyendo]
Reivindicaciones:
Se obtiene más de un 96.5% de conversión a éster metílico (biodiesel) .
1. Un método para la síntesis de biodiesel por reacción de un aceite natural con metanol en presencia de un catalizador alcalino, en el que una mezcla de aceite natural, metanol y el catalizador alcalino se suministra en una dirección a lo largo de un reactor tubular que tiene un extremo de entrada y un extremo de salida a una velocidad suficiente de manera que el flujo es transitorio o turbulento, en donde la mezcla de aceite natural, metanol y catalizador alcalino es turbulenta cuando esta entra en el reactor tubular y en donde la turbulencia es generada por inyección de un flujo de metanol, opcionalmente con el catalizador alcalino disuelto en este, en el flujo del aceite natural a un ángulo a la dirección del flujo del aceite natural, en donde el reactor tubular tiene un diámetro en el intervalo de 6-200 mm y una longitud en el intervalo de 30 a 100 metros, y el reactor tubular incluye elementos de mezclado estático que están presentes para al menos el primer 20 % de la longitud del reactor tubular y para al menos el ultimo 30 % de la longitud del reactor tubular, y en donde una porción del reactor tubular que comprende al menos el 20 % de la longitud del reactor tubular y es desplazado desde los extremos del mismo no tiene elementos de mezclado, tal que en la primera y última longitudes del reactor tubular los reactivos son mezclados en una dirección normal a la dirección del flujo de modo que los reactivos se mezclan en una dirección normal a la dirección del flujo en un grado mayor que en una dirección paralela a la dirección de flujo y de tal manera que el tiempo necesario para que el 90% de los elementos de fluido pasen a través del reactor esté dentro del 20% del tiempo medio de permanencia del reactivo en el reactor.
2. El método de la reivindicación 1, en donde los reactivos están bajo una presión en exceso de 0.5 bar manométricos, más preferentemente en el intervalo de 1-30 bar manométricos.
3. El método de cualquier reivindicación precedente, en donde la caída de presión a través del reactor tubular desde la entrada del flujo hasta la salida del flujo está en el intervalo 0.1 bar - 10 bar, más preferentemente 0.5 bar - 8 bar, y con mayor preferencia en el intervalo 3-7 bar.
4. El método de cualquier reivindicación precedente en donde la potencia por unidad de peso excede 0.5 W/kg, estando preferentemente en el intervalo 1 W/kg a 10W/kg, y más preferentemente en el intervalo 3 W/kg a 8 W/kg.
5. Un aparato para la síntesis de biodiesel por reacción de un aceite natural con metanol en presencia de un catalizador alcalino, que comprende un reactor tubular que tiene un extremo de entrada y un extremo de salida, y que tiene un diámetro en el intervalo de 6-200mm y una longitud en el intervalo de 30 a 100 metros, un suministro de aceite natural, un suministro de metanol y un suministro de catalizador alcalino, el suministro es arreglado para suministrar una mezcla de aceite natural, metanol y el catalizador alcalino en una dirección a lo largo del reactor tubular a una velocidad suficiente de manera que el flujo sea transicional o turbulento, se proporciona un generador de turbulencia, dicho generador de turbulencia comprende medios de inyección para inyectar un flujo de metanol, opcionalmente con el catalizador alcalino disuelto en el mismo, en el flujo del aceite natural, dichos medios de inyección incluyen boquillas de chorro construidas y colocadas para inyectar el flujo de metanol a un ángulo con la dirección del flujo del aceite natural, de manera que la mezcla de aceite natural, metanol y catalizador alcalino sea turbulenta cuando esta entra al reactor tubular, en donde elementos de mezclado estático se proporcionan para al menos el primer 20% de la longitud del reactor tubular y para al menos el último 30% de la longitud del reactor tubular, y ahí hay una porción del reactor tubular que comprende al menos 20% de la longitud del reactor y esta desplazada de los extremos del mismo y no tiene elementos de mezclado, de manera que en la primera y últimas longitudes del reactor tubular los reactivos se mezclan en una dirección normal a la dirección del flujo en un mayor grado que en una dirección paralela a la dirección del flujo y de manera que el tiempo necesario para que el 90% de los elementos del fluido pasen a través del reactor esté dentro del 20% del tiempo medio de permanencia del reactivo en el reactor.
6. El aparato de la reivindicación 5, en donde la longitud del reactor tubular está en el intervalo de 40 a 100 metros.
7. Una planta para la fabricación de biodiesel, que comprende un aparato de acuerdo con cualquiera de las reivindicaciones 5 a 6, conjuntamente con al menos uno de un aparato para desgomado del aceite natural y un aparato para la esterificación de ácidos grasos libres en el aceite natural.
Patentes similares o relacionadas:
Procedimiento de oligomerización de olefinas que usa un dispositivo de limpieza, del 15 de Julio de 2020, de IFP ENERGIES NOUVELLES: Procedimiento de oligomerización de etileno para producir alfa-olefinas que comprende: - una etapa de oligomerización de etileno en una sección de reacción […]
Proceso de alcoxilación que usa reactor tubular, del 15 de Julio de 2020, de Dow Global Technologies LLC: Un proceso para la fabricación de un poliéter por medio de polimerización de al menos un óxido de alquileno en un reactor tubular que tiene un extremo de entrada y un extremo […]
Configuraciones y procedimientos para el enriquecimiento avanzado de oxígeno para la recuperación del azufre, del 13 de Mayo de 2020, de FLUOR TECHNOLOGIES CORPORATION: Planta de procesamiento de gas, que comprende: un sistema de reactor Claus que tiene una fase térmica que comprende un incinerador y un horno de reacción, una fase […]
Conjunto de reactor y procedimiento para la polimerización de olefinas, del 6 de Mayo de 2020, de BOREALIS AG: Procedimiento para polimerizar olefinas en un reactor de lecho fluidizado, en el que el lecho fluidizado está formado por partículas de polímero en un gas de […]
Método y sistema de producción automática de partículas de tres tanques, del 1 de Abril de 2020, de Bai, Hongmei: Un método de producción automática de partículas de tres tanques, que comprende: alimentar material a tratar en un tanque de calentamiento en lotes; calentar […]
Procedimiento de preparación de poliéster utilizando un reactor tubular, del 18 de Marzo de 2020, de Grupo Petrotemex, S.A. de C.V: Un procedimiento para hacer un prepoliéster, que comprende: proporcionar un reactor tubular de esterificación que comprende un tubo, teniendo el tubo […]
Sistema de reactor con calefacción optimizada y separación de fases, del 18 de Marzo de 2020, de Grupo Petrotemex, S.A. de C.V: Un procedimiento de policondensación para producir tereftalato de polietileno que comprende: (a) calentar un medio de reacción inicial que fluye hacia arriba a través […]
Procedimiento y aparato para la producción de nanotubos de carbono, del 11 de Marzo de 2020, de Q-Flo Limited: Un procedimiento de producción de nanotubos de carbono que comprende: (A) generar un flujo dirigido de plasma desde un gas de trabajo en un dispositivo […]