METODO PARA LA PRODUCCION DE ISOFORONDIAMINA (IPDA, 3-AMINOMETIL-3,5,5-TRIMETILCICLOHEXILAMINA).
Método para la producción de 3-aminometil-3,5,5-trimetilciclohexilamina (isoforondiamina,
IPDA) con una relación de isómeros cis/trans de por lo menos 70/30 a partir de 3-ciano-3,5,5-trimetilciclohexanona (isoforonnitrilo, IPN), NH2, y H2, donde es hidrogenado en presencia de un catalizador que contiene 55 a 98% en peso de cobalto, 0,2 a 15% en peso de fósforo y 0,2 a 15% en peso de manganeso así como dado el caso rutenio, calculado en cada caso como óxido y referido al peso total de catalizador, a temperaturas de 50 a 200ºC y una presión de 50 a 300 bar, caracterizado porque el contenido de metal alcalino del catalizador de hidrogenación es < =0,03% en peso, calculado como óxido de metal alcalino y referido al peso total de catalizador
Tipo: Resumen de patente/invención. Número de Solicitud: W0209600EP.
Solicitante: BASF SE.
Nacionalidad solicitante: Alemania.
Dirección: ISENBRUCK BOSL HORSCHLER WICHMANN HUHN LLP EASTSITE ONE SECKENHEIMER LANDSTRAS ,68163 MANNHEIM.
Inventor/es: SCHWAB, EKKEHARD, MELDER, JOHANN-PETER, HILL, THOMAS, DR., PETERSEN, HERMANN, DR., FUNKE, FRANK, DR., HENKES, ERHARD, DR., KORNER,REINHARD,DR, HIMMEL,WALTER.
Fecha de Publicación: .
Fecha Concesión Europea: 14 de Octubre de 2009.
Clasificación Internacional de Patentes:
- B01J23/889B
- B01J27/185A
- B01J27/187 TECNICAS INDUSTRIALES DIVERSAS; TRANSPORTES. › B01 PROCEDIMIENTOS O APARATOS FISICOS O QUIMICOS EN GENERAL. › B01J PROCEDIMIENTOS QUÍMICOS O FÍSICOS, p. ej. CATÁLISIS O QUÍMICA DE LOS COLOIDES; APARATOS ADECUADOS. › B01J 27/00 Catalizadores que contienen los elementos o compuestos de halógenos, azufre, selenio, teluro, fósforo, o nitrógeno; Catalizadores que comprenden compuestos de carbono. › con manganeso, tecnecio o renio.
- B01J37/03 B01J […] › B01J 37/00 Procedimientos para preparar catalizadores, en general; Procedimientos para activación de catalizadores, en general. › Precipitación; Coprecipitación.
- C07C209/26 QUIMICA; METALURGIA. › C07 QUIMICA ORGANICA. › C07C COMPUESTOS ACICLICOS O CARBOCICLICOS (compuestos macromoleculares C08; producción de compuestos orgánicos por electrolisiso electroforesis C25B 3/00, C25B 7/00). › C07C 209/00 Preparación de compuestos que contienen grupos amino unidos a una estructura carbonada. › por reducción con hidrógeno.
- C07C209/48 C07C 209/00 […] › por reducción de nitrilos.
- C07C253/30 C07C […] › C07C 253/00 Preparación de nitrilos de ácidos carboxílicos (de cianógeno o sus compuestos C01C 3/00). › por reacciones que no implican la formación de grupos ciano.
Clasificación PCT:
- B01J23/889 B01J […] › B01J 23/00 Catalizadores que contienen metales, óxidos o hidróxidos metálicos no previstos en el grupo B01J 21/00 (B01J 21/16 tiene prioridad). › Manganeso, tecnecio o renio.
- B01J37/03 B01J 37/00 […] › Precipitación; Coprecipitación.
- C07C209/26 C07C 209/00 […] › por reducción con hidrógeno.
- C07C209/48 C07C 209/00 […] › por reducción de nitrilos.
- C07C253/30 C07C 253/00 […] › por reacciones que no implican la formación de grupos ciano.
Clasificación antigua:
- B01J23/889 B01J 23/00 […] › Manganeso, tecnecio o renio.
- B01J37/03 B01J 37/00 […] › Precipitación; Coprecipitación.
- C07C209/26 C07C 209/00 […] › por reducción con hidrógeno.
- C07C209/48 C07C 209/00 […] › por reducción de nitrilos.
- C07C253/30 C07C 253/00 […] › por reacciones que no implican la formación de grupos ciano.
Fragmento de la descripción:
Método para la producción de isoforondiamina (IPDA, 3-aminometil-3,5,5-trimetilciclohexilamina).
La presente invención se refiere a un método para la producción de 3-aminometil-3,5,5-trimetilciclohexilamina (isoforondiamina, IPDA) con una relación de isómeros cis/trans de por lo menos 70/30 a partir de 3-ciano-3,5,5-trimetilciclohexanona (isoforonnitrilo, IPN), H2 y NH3, donde se hidrogena en presencia de un catalizador de hidrogenación, cuyo contenido del metal alcalino es =0,03% en peso, calculado como óxido de metal alcalino. Además, la invención se refiere a un método para la producción de tales catalizadores así como los catalizadores en sí mismos.
La IPDA es empleada como producto de partida para la producción de isoforondiisocianato (IPDI), un componente de isocianato para sistemas de poliuretano, como componente amino para poliamidas y como endurecedor para resinas de epóxido. La IPDA es producida comúnmente a partir de IPN, donde el grupo carbonilo es transformado en un grupo amino y el grupo nitrilo es transformado en un grupo aminometilo en presencia de amoniaco, hidrógeno y catalizadores comunes. Se obtienen mezclas de cis-IPDA y trans-IPDA. Ambos isómeros exhiben diferentes reactividades, lo cual es importante para la aplicación técnica prevista. De acuerdo con la DE-A 42 11 454 mediante el empleo de una mezcla de isómeros de IPDA, consistente en más de 40% del isómero trans y menos de 60% del isómero cis como componentes de reacción en resinas de adición, como en particular resinas de epóxido, se prolonga el tiempo de proceso así como también se reduce la temperatura máxima de endurecimiento. Para obtener una velocidad de reacción tan alta como sea posible, preferiblemente se invierten las mezclas de isómeros de IPDA, las cuales exhiben una fracción tan alta como sea posible del isómero cis (=70%). Por eso el IPDA obtenible comercialmente posee una relación de isómeros cis/trans de 75/25.
Son ya conocidos diferentes métodos para la obtención de una alta relación cis/trans:
De acuerdo con la DE-A 43 43 890, la hidrogenación del IPN que genera grupo amino para dar IPDA, en la cual se deja caer una mezcla de IPN, amoniaco y un alcohol C1-C3 en presencia de hidrógeno, ocurre sobre un reactor de lecho de contacto dotado con un catalizador de lecho fijo de Co y/o Ru a 3 a 8 MPa y una temperatura de 40 a 150ºC, preferiblemente 90 a 130ºC, y se acondiciona la mezcla de reacción mediante destilación. Con el empleo de un catalizador de soporte de Ru se alcanzan altas relaciones cis/trans de 84/16 (rendimiento total de IPDA: 81%), por empleo de un catalizador de soporte de Co se alcanzan únicamente relaciones cis/trans de 60/40 (rendimiento total de IPDA: 87%). Mediante la combinación de un catalizador de Ru y un catalizador de Co, se tiene éxito en la obtención de IPDA en la relación cis/trans similarmente alta que en el empleo de un catalizador de Ru solo, no obstante en un rendimiento más alto que en el empleo de éste catalizador de Ru solo.
La DE-A 43 43 891 describe un método para la producción de IPDA, donde reacciona IPN en presencia de amoniaco y un catalizador de hidrogenación en suspensión o lecho sólido de la serie de los catalizadores de Co, Ni y metales nobles con hidrógeno a una presión de 3 a 20 MPa y una temperatura de hasta 150ºC y se acondiciona la mezcla de reacción obtenida mediante destilación, donde la particularidad del método consiste en que la reacción de dos etapas es ejecutada en rangos de temperatura exactamente definidos. Una relación de isómeros cis/trans de 80/20 permite obtener un rendimiento total en IPDA de 91,9%.
En el método de la EP-A 0 926 130 se ejecuta la hidrogenación en presencia de un ácido en los catalizadores, los cuales contienen cobre y/o un metal del octavo grupo secundario del sistema periódico. Se emplean tanto ácidos Lewis como también ácidos Bronstedt; se emplea preferiblemente ácido 2-etilhexanoico. Las relaciones cis/trans están en general en =70/30 en un rendimiento total de IPDA de = 90%.
El método de la EP-B 0 729 937 se caracteriza porque se ejecuta el método en tres espacios físicamente separados unos de otros, donde se emplean catalizadores que contienen cobalto, níquel, rutenio y/u otros metales nobles. Antes del segundo reactor se dosifica solución acuosa de NaOH, mediante lo cual se disminuye la formación de los productos en forma de anillo como 1,3,3-trimetil-6-azabiciclo[3,2,1]octano.
La EP-A 0 742 045 escribe catalizadores de cobalto, cuya masa catalítica activa está compuesta por 55 a 98% en peso de cobalto, 0,2 a 15% en peso de fósforo, 0,2 a 15% en peso de manganeso y 0,05 a 5% en peso, preferiblemente 0,1 a 3% en peso, particularmente preferido 0,13 a 1% en peso de metal alcalino, calculado en cada caso como óxido. Estos catalizadores pueden ser empleados en métodos para la hidrogenación de nitrilos orgánicos y/o iminas como IPN a temperaturas de 60 a 150ºC y presiones de 50 a 300 bar. No se dan indicaciones sobre la relación cis/trans del IPDA así producido.
En los métodos conocidos para la producción de IPDA es desventajosa la formación de subproductos difícilmente separables como productos de eliminación de HCN, subproductos metilados y/o productos intermedios incompletamente hidrogenados (ver abajo).
Es objetivo de la invención poner a disposición un método para la producción de isoforondiamina (IPDA) mediante el cual se eviten las desventajas del estado de la técnica. Se debe encontrar además un catalizador adecuado y un método para la producción de este catalizador.
Se logra el objetivo acorde con la invención mediante un método para la producción de 3-aminometil-3,5,5-trimetilciclohexilamina (IPDA) con una relación de isómeros cis/trans de por lo menos 70/30, a partir de 3-ciano-3,5,5-trimetilciclohexanona (IPN), NH3 y H2, donde se hidrogena en presencia de un catalizador de hidrogenación a temperaturas de 50 a 200ºC y una presión de 50 a 300 bar, caracterizado porque el contenido de metal alcalino de los catalizadores de hidrogenación es =0,03% en peso calculado como óxido del metal alcalino y referido al peso total del catalizador. Preferiblemente, la hidrogenación ocurre a temperaturas de 60 a 160ºC, particularmente preferido a temperaturas de 80 a 130ºC, y presiones de 100 a 250 bar, particularmente preferido a presiones de 200 a 250 bar.
El contenido de metales alcalinos abarca el contenido de Li, Na, K, Rb y Cs, entendiendo entre ellos en particular el contenido de Na.
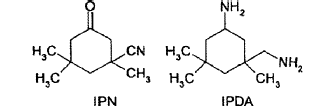
Si se compara el método para la producción de IPDA con empleo de catalizadores que contienen metales alcalinos, con el método acorde con la invención que emplea en gran parte catalizadores libres de metales alcalinos, se observa que la reacción empleando los catalizadores acordes con la invención libres en gran parte de metales alcalinos transcurre de manera selectiva respecto al producto deseado IPDA. La formación de subproductos asciende en suma a =10% del área, preferiblemente =7% del área, particularmente preferido =5% del área, comparado con el que se determinó por medio de análisis de cromatografía de gases del producto bruto reacción. Tiene lugar menos eliminación de HCN (subproductos IIa y IIb); además se forman difícilmente subproductos metilados (IIIa, IIIb). Esto es particularmente ventajoso, puesto que estos son sólo difícilmente separables del producto deseado IPDA. También disminuye la cantidad del subproducto incompletamente hidrogenado aminonitrilo (IV), el cual puede ser difícilmente separado por destilación del IPDA. Concretamente se forma más subproducto cíclico 1,3,3-trimetil-6-azabiciclo[3,2,1]octano (V), sin embargo este puede ser separado fácilmente de IPDA mediante destilación.
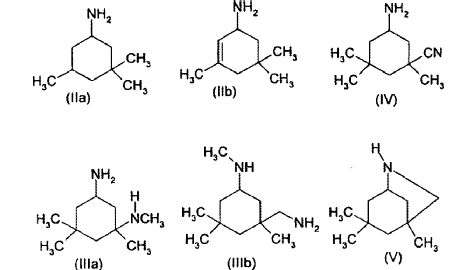
Mediante el método acorde con la invención se logran relaciones cis/trans de por lo menos 70/30, preferiblemente de por lo menos 73/27, particularmente preferido de por lo menos 75/25. La relación cis/trans se determina por ejemplo mediante examen por cromatografía de gases (GC) al producto crudo de reacción. Con esto se fijan mutuamente las superficies determinadas de los picos de IPDA cis y trans en la relación.
Con esto, el rendimiento total de IPDA es el general de =90%, en particular =93%, ante todo en particular =95%. La pureza es en general de por lo menos 98%, en...
Reivindicaciones:
1. Método para la producción de 3-aminometil-3,5,5-trimetilciclohexilamina (isoforondiamina, IPDA) con una relación de isómeros cis/trans de por lo menos 70/30 a partir de 3-ciano-3,5,5-trimetilciclohexanona (isoforonnitrilo, IPN), NH2, y H2, donde es hidrogenado en presencia de un catalizador que contiene 55 a 98% en peso de cobalto, 0,2 a 15% en peso de fósforo y 0,2 a 15% en peso de manganeso así como dado el caso rutenio, calculado en cada caso como óxido y referido al peso total de catalizador, a temperaturas de 50 a 200ºC y una presión de 50 a 300 bar, caracterizado porque el contenido de metal alcalino del catalizador de hidrogenación es =0,03% en peso, calculado como óxido de metal alcalino y referido al peso total de catalizador.
2. Método según la reivindicación 1, caracterizado porque el método es ejecutado en dos etapas con los siguientes pasos:
- A) reacción de IPN, NH2 y H2 a temperaturas de 20 a 150ºC y una presión de 50 a 300 bar, dado el caso en presencia de un catalizador de formación de iminas;
- B) transformación de la mezcla de reacción obtenida en el paso A) en presencia de un catalizador de hidrogenación a temperaturas de 60 a 100ºC y una presión de 50 a 300 bar; donde el paso A) y el paso B) son ejecutados en el mismo espacio de reacción o en dos espacios de reacción separados físicamente uno de otro.
3. Método según la reivindicación 1, caracterizado porque el método es ejecutado en tres espacios de reacción físicamente separados uno de otro con las siguientes etapas de reacción:
- a) Reacción de IPN con exceso de amoniaco en un primer espacio de reacción a temperaturas de 20 a 150ºC y presiones de 50 a 300 bar hasta dar esencialmente 3-ciano-3,5,5-trimetilciclohexanonimina, dado el caso con un catalizador de óxido metálico ácido,
- b) hidrogenación de los productos de reacción obtenidos en el paso a) en un segundo espacio de reacción, con hidrógeno en presencia de amoniaco en exceso, con un catalizador de hidrogenación a temperaturas de 60 a 100ºC y presiones de 50 a 300 bar, e
- c) hidrogenación de los productos de reacción obtenidos en el paso b) en un tercer espacio de reacción en presencia de hidrógeno y amoniaco sobre un catalizador de hidrogenación a temperaturas de 110 a 160ºC y presiones de 50 a 300 bar.
4. Método según la reivindicación 3, caracterizado porque el paso a) es ejecutado a temperaturas de 30 a 130ºC y/o presiones de 100 a 250 bar.
5. Método según las reivindicaciones 3 o 4, caracterizado porque el paso b) y/o el paso c) son ejecutados a presiones de 100 a 250 bar.
6. Método según una de las reivindicaciones 1 a 5, caracterizado porque el contenido de metal alcalino de un catalizador de hidrogenación es 0,015% en peso, preferiblemente =0,01% en peso, calculado como óxido metálico y basado en el peso total de catalizador.
7. Catalizador de hidrogenación como se definió en una de las reivindicaciones 1 o 6.
8. Empleo de un catalizador de hidrogenación según la reivindicación 7 para la hidrogenación de formación de amina del isoforonnitrilo.
9. Método para la producción de un catalizador de hidrogenación según la reivindicación 7, que contiene los siguientes pasos:
10. Método según la reivindicación 9, caracterizado porque en el paso i) se precipita con una solución acuosa que contiene carbonato de amonio.
11. Método según las reivindicaciones 9 o 10, caracterizado porque en el paso i) se emplean una o varias sales de Co solubles en agua.
12. Método según una de las reivindicaciones 9 a 11, caracterizado porque en el paso i) se emplean como promotores una o varias sales de Mn solubles en agua así como uno o varios compuestos de fósforo solubles en agua.
Patentes similares o relacionadas:
Óxidos mixtos de metales de transición, catalizadores de hidrotratamiento obtenidos de los mismos y procedimiento de preparación que comprende procedimientos sol-gel, del 15 de Julio de 2020, de ENI S.P.A.: Óxido mixto, que presenta la fórmula general (A2): Xa Yb Zc Od . pC (A2) en la que X se selecciona de Ni, Co y mezclas de los mismos, […]
Uso de un material de partículas compuestas soportadas, procedimiento de producción de dicho material y procedimiento para producir compuestos usando material de partículas compuestas soportadas como catalizador para síntesis química, del 10 de Junio de 2020, de ASAHI KASEI KABUSHIKI KAISHA: Uso de un material de partículas compuestas soportadas que comprende: una partícula compuesta formada de un níquel oxidado y X, en el que X representa al menos uno de […]
Un proceso para la síntesis de carbonatos de dialquilo, del 6 de Mayo de 2020, de COUNCIL OF SCIENTIFIC AND INDUSTRIAL RESEARCH: Un proceso para la síntesis de carbonatos de dialquilo catalizada por una composición catalizadora, que comprende las etapas de: (a) cargar […]
Proceso para preparar catalizadores de metales nobles soportados mediante deposición hidrotérmica, del 29 de Abril de 2020, de TRONOX LLC: Un proceso para obtener un catalizador que tiene nanopartículas de metal(es) noble(s) depositadas en un soporte, de manera que el proceso […]
Aparato para el tratamiento de aire, del 29 de Abril de 2020, de Anglo Platinum Marketing Limited: Aparato para el tratamiento de aire, en el que aire que tiene una primera concentración de monóxido de carbono entra en el aparato y aire respirable que tiene […]
Catalizador de partículas de plata recubiertas para la preparación de formaldehído, del 26 de Febrero de 2020, de ALLGEMEINE GOLD- UND SILBERSCHEIDEANSTALT AG: Proceso para producir cristales de plata de una fracción de partículas entre 0,5 - 1 mm con un recubrimiento poroso que tiene un espesor de 0,3 μm - 10 μm de material oxigenado […]
Material a base de sílice, proceso de fabricación para el mismo, material portador de metal noble y proceso de fabricación de ácido carboxílico usando el mismo como catalizador, del 19 de Febrero de 2020, de ASAHI KASEI KABUSHIKI KAISHA: Un material a base de sílice que comprende: silicio, aluminio, al menos un elemento del cuarto período seleccionado del grupo que consiste en hierro, […]
Procedimiento de síntesis de ácido glicólico, del 22 de Enero de 2020, de Pivert: Procedimiento de síntesis de ácido glicólico, o de una de sus sales, que comprende la siguiente etapa: - una puesta en contacto en un medio […]