Proceso y equipo de extrusión de espuma de poliéster que pueden ser utilizados en plantas para la fabricación de láminas, planchas o tubos de espuma de poliéster.
Equipo de extrusión de espuma de poliéster que comprende un armazón termorregulado (11) dotado de una entrada de alimentación (14) de material de poliéster puro y/o reciclado,
estando dispuestos en el interior de dicho armazón (11) dos husillos co-rotantes (12), definiendo dichos husillos co-rotantes (12) con las paredes internas de dicho armazón (11) una primera zona de desgasificación (A, B) interpuesta entre una zona de alimentación situada en dicha entrada de alimentación (14) y una primera zona estanca (15), una segunda zona de desgasificación (C, D) situada más abajo de dicha primera zona de desgasificación (A, B) y separada de la última por medio de dicha primera zona estanca (15), una zona de entrada (E) de agente espumante situada más abajo de dicha segunda zona de desgasificación (C, D) y separada de la última por medio de una segunda zona estanca (22) y una zona extrema (F) de bombeo del material fundido situada más abajo de dicha zona de entrada (E) de agente espumante, en el que:
- dicha primera zona de desgasificación (A, B) está adaptada para llevar a cabo una desgasificación atmosférica forzada a una temperatura menor que el punto de fusión de un material de poliéster tratado y comprende una primera columna de ventilación (13) situada en un primer segmento (B) de dicha primera zona de desgasificación (A, B) adyacente a dicha primera zona estanca (15) y una campana extractora (19) dispuesta sobre dicha primera columna de ventilación (13) adaptada para activar el tiro de dicha ventilación (13) llevando a cabo dicha desgasificación atmosférica forzada,
- dicha segunda zona de desgasificación (C, D) está adaptada para llevar a cabo una desgasificación al vacío a una temperatura igual o mayor que el punto de fusión de dicho material de poliéster tratado y
- dicha primera zona de desgasificación (A, B) comprende, más arriba de dicha primera columna de ventilación (13), una tobera (18) para la entrada de nitrógeno gaseoso precalentado en dicha primera zona de desgasificación (A, B), adaptada para arrastrar los vapores presentes en dicha primera zona (A, B) hacia la atmósfera llevando a cabo dicha desgasificación atmosférica forzada.
Tipo: Patente Internacional (Tratado de Cooperación de Patentes). Resumen de patente/invención. Número de Solicitud: PCT/IB2009/007929.
Solicitante: COSTRUZIONI MECCANICHE LUIGI BANDERA S.P.A..
Nacionalidad solicitante: Italia.
Dirección: C.so Sempione 120 21052 Busto Arsizio (VA) ITALIA.
Inventor/es: BANDERA, FRANCO, VENEGONI, ENRICO.
Fecha de Publicación: .
Clasificación Internacional de Patentes:
- B29C44/34 TECNICAS INDUSTRIALES DIVERSAS; TRANSPORTES. › B29 TRABAJO DE LAS MATERIAS PLASTICAS; TRABAJO DE SUSTANCIAS EN ESTADO PLASTICO EN GENERAL. › B29C CONFORMACIÓN O UNIÓN DE MATERIAS PLÁSTICAS; CONFORMACIÓN DE MATERIALES EN ESTADO PLÁSTICO, NO PREVISTA EN OTRO LUGAR; POSTRATAMIENTO DE PRODUCTOS CONFORMADOS, p. ej. REPARACIÓN (fabricación de preformas B29B 11/00; fabricación de productos estratificados combinando capas previamente no unidas para convertirse en un producto cuyas capas permanecerán unidas B32B 37/00 - B32B 41/00). › B29C 44/00 Conformación por presión interna generada en el material, p. ej. por hinchamiento o por espumación. › Elementos constitutivos, detalles o accesorios; Operaciones auxiliares.
- B29C47/00
- B29C47/14
- B29C47/26
- B29C47/36
- B29C47/58
- B29C47/60
- B29C47/68
- B29C47/76
- B29K105/04 B29 […] › B29K SISTEMA DE INDEXACION ASOCIADO A LAS SUBCLASES B29B, B29C O B29D, RELATIVO A LAS MATERIAS A MOLDEAR O MATERIALES DE REFUERZO, CARGAS O PREFORMADAS, p. ej. INSERCIONES. › B29K 105/00 Presentación, forma o estado de la materia moldeada. › celular o porosa.
- B29K105/26 B29K 105/00 […] › Residuos.
- B29K67/00 B29K […] › Uso de poliésteres como material de moldeo.
PDF original: ES-2553566_T3.pdf
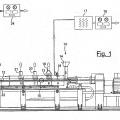
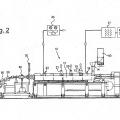
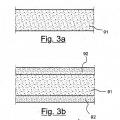
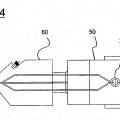
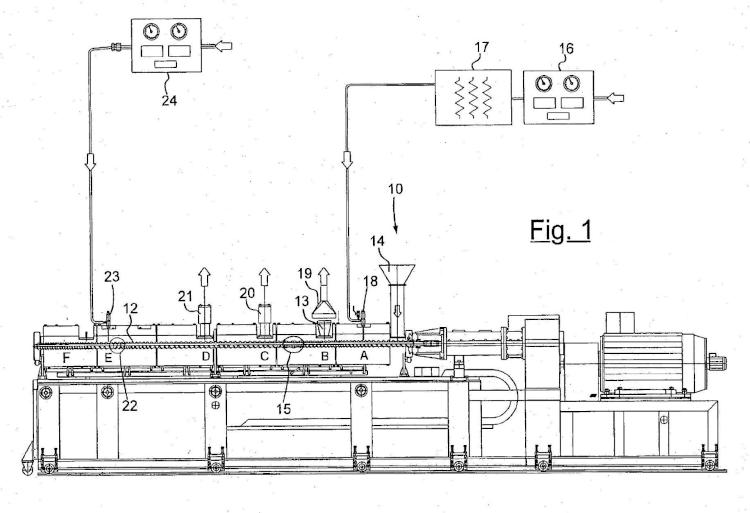
Patentes similares o relacionadas:
Disposición del accionamiento en una extrusora con desgasificación, del 24 de Enero de 2018, de EVONIK ROHM GMBH: Extrusora con desgasificación para la desgasificación de un material polimérico, que comprende al menos un accionamiento, al menos un cilindro de extrusora […]
Dispositivo y procedimiento para la desgasificación de material que va a procesarse, del 25 de Octubre de 2017, de Coperion GmbH: Dispositivo para la desgasificación de material que va a procesarse, en particular material plástico, que comprende - un motor de accionamiento para […]
Dispositivo para la extrusión de material sintético termoplástico, del 7 de Junio de 2017, de EREMA ENGINEERING RECYCLING MASCHINEN UND ANLAGEN GESELLSCHAFT M.B.H.: Dispositivo para la extrusión de material sintético termoplástico, con tornillo sinfín de extrusor alojado en una carcasa , que comprende […]
Extrusora de desgasificación para la desgasificación de un material polimérico, así como procedimiento para la desgasificación de un jarabe a base de polímeros, disolventes y/o monómeros utilizando una extrusora de desgasificación, del 10 de Mayo de 2017, de EVONIK ROHM GMBH: Extrusora de desgasificación para la desgasificación de un material polimérico, que comprende al menos un accionamiento , al menos un cilindro […]
Procedimiento para el tratamiento continuo de soluciones de polímeros, del 12 de Abril de 2017, de LIST Technology AG: Procedimiento para el tratamiento continúo de soluciones de polímeros dentro de un mezclador-amasador , realizado como un evaporador y/o desgasificador, con una cámara […]
Procedimiento y dispositivo para desgasificar una mezcla en particular de aglutinantes poliméricos, del 9 de Noviembre de 2016, de Adm-Isobloc GmbH: Procedimiento para desgasificar una mezcla que contiene componentes separables de diferente densidad, en el que la mezcla se transporta desde un tornillo sin […]
Procedimiento para la producción de masas de moldeo termoplásticas, así como masas de moldeo termoplásticas producidas según éste, del 18 de Mayo de 2016, de INEOS Styrolution Group GmbH: Procedimiento para la producción de masas de moldeo termoplásticas, en el cual se usa un extrusor, el cual está estructurado en dirección de transporte aguas abajo a partir […]
Dispositivo para la desgasificación de fluidos y procedimiento para la desgasificación de fluidos, del 4 de Mayo de 2016, de Wobben Properties GmbH: Dispositivo de desgasificación de fluidos para la desgasificación de resinas, con un elemento de alimentación de fluido para alimentar la resina, […]