Elemento de calentamiento por resistencia.
Utilización de un elemento de resistencia eléctrica que consiste principalmente en una fase de siliciuro de acuerdo con la fórmula Mo(Si1-XAlX)2,
formando dicha fase alúmina sobre la superficie del elemento, estando el valor de x comprendido entre 0,10 y 0,60, para la sinterización de polvo metálico, de polvo de aleación pesada de tungsteno, o de compuestos intermetálicos.
Tipo: Patente Internacional (Tratado de Cooperación de Patentes). Resumen de patente/invención. Número de Solicitud: PCT/SE2000/000871.
Solicitante: SANDVIK INTELLECTUAL PROPERTY AB.
Nacionalidad solicitante: Suecia.
Dirección: 811 81 SANDVIKEN SUECIA.
Inventor/es: SUNDBERG, MATS.
Fecha de Publicación: .
Clasificación Internacional de Patentes:
- C22C29/18 QUIMICA; METALURGIA. › C22 METALURGIA; ALEACIONES FERROSAS O NO FERROSAS; TRATAMIENTO DE ALEACIONES O METALES NO FERROSOS. › C22C ALEACIONES (tratamiento de alegaciones C21D, C22F). › C22C 29/00 Aleaciones basadas en carburos, óxidos, boruros, nitruros o siliciuros, p. ej. cermets, u otros compuestos metálicos, p. ej. oxinitruros, sulfuros. › basadas en siliciuros.
- H01B1/06 ELECTRICIDAD. › H01 ELEMENTOS ELECTRICOS BASICOS. › H01B CABLES; CONDUCTORES; AISLADORES; ,o EMPLEO DE MATERIALES ESPECIFICOS POR SUS PROPIEDADES CONDUCTORAS, AISLANTES O DIELECTRICAS (empleo por las propiedades magnéticas H01F 1/00; guías de ondas H01P). › H01B 1/00 Conductores o cuerpos conductores caracterizados por los materiales conductores utilizados; Empleo de materiales específicos como conductores (conductores, cables o líneas de transmisión superconductores o hiperconductores caracterizados por los materiales utilizados H01B 12/00). › compuestos principalmente de otras sustancias no metálicas.
PDF original: ES-2548561_T3.pdf
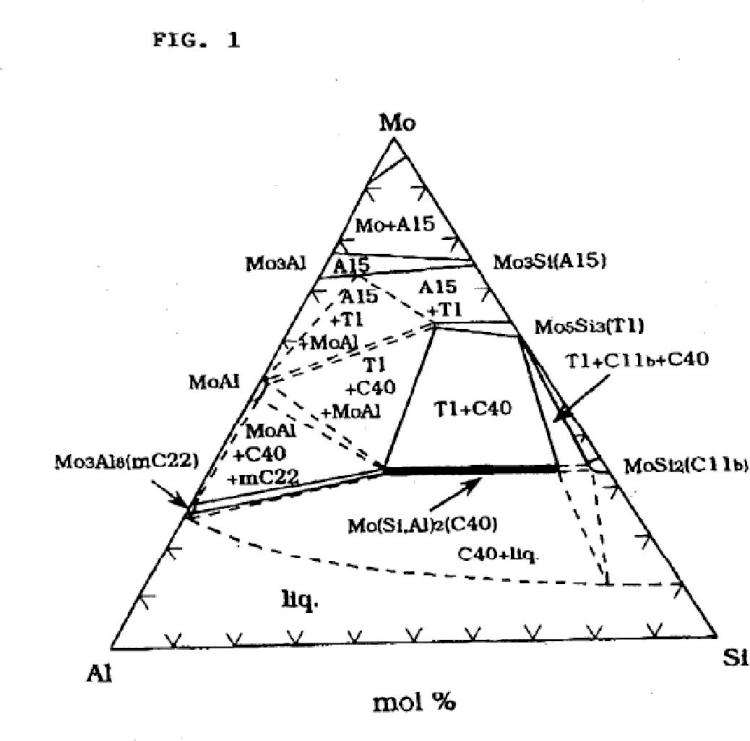
Descripción:
Elemento de calentamiento por resistencia La presente invención está relacionada con el uso de un elemento de calentamiento por resistencia eléctrica de tipo de molibdeno-silicio que está pensado para la sinterización de polvo metálico.
Los elementos de calentamiento por resistencia del tipo anteriormente mencionado existen desde la década de 1950, por ejemplo con la marca comercial Kanthal Super. Estos elementos suelen consistir principalmente en una fase de tipo metal de MoSi2, de forma alternativa de MoXW1-XSi2, y también una fase óxido de tipo silicato de aluminio. Se pueden utilizar tipos de material similares a temperaturas de los elementos de hasta 1900°C en atmósfera oxidante.
La Patente SE-C-210969 ó la Patente GB-B-924497 describen un elemento que consiste en una fase siliciuro.
Lo que hace posible esta elevada temperatura de trabajo es, además del alto punto de fusión del material (superior a 2000°C) , la capa de óxido de SiO2 que se formará y que rápidamente pasiva al material básico protegiéndole frente a la oxidación acelerada y que, gracias a esto, hace posible que el elemento de calentamiento tenga una larga vida útil. Esta capa exterior proporciona una protección duradera en varias atmósferas de horno y de tratamiento térmico, tales como aire, oxígeno, gas nitrógeno/hidrógeno, amoniaco disociado, y otras. Las condiciones que a menudo limitan el uso en estas atmósferas son aquellas en las que una alta temperatura del elemento coincide a la vez con un potencial de oxígeno demasiado bajo, de forma alternativa con un punto de rocío demasiado bajo, en la atmósfera. Lo que sucede si se superan las proporciones críticas entre punto de rocío - temperatura del elemento es que la capa de SiO2 se vuelve inestable y, debido a ello, después de un cierto periodo de tiempo dicha capa ya no proporciona ninguna protección al material base. Por ejemplo en gas hidrógeno esto sucede a una temperatura del elemento de 1300°C cuando el punto de rocío es menor que aproximadamente -30°C. Para hacer que la capa de SiO2 permanezca estable a una temperatura del elemento de 1450°C, es necesario un punto de rocío superior a +20°C, es decir, un gas hidrógeno que contenga más del 2, 3 por ciento en volumen. Las propiedades de estabilidad de la capa de SiO2 constituyen una restricción para el uso del elemento en ciertas conexiones.
Un ejemplo de aplicación en el que se manifiesta esta limitación es en la sinterización de polvo metálico para producir acero inoxidable. Los componentes del acero inoxidable de grado AISI316L se producen sobre todo mediante compresión de polvo o, de forma alternativa, mediante moldeo por inyección de polvo metálico. A menudo, después de la evaporación del agente ligante a una baja temperatura, es necesaria una sinterización final en el rango de temperatura entre 1300-1360°C en atmósfera reductora. El gas reductor puede ser gas hidrógeno puro con un punto de rocío de -40°C a -60°C, valores que corresponden aproximadamente a 0, 01 y 0, 001 por ciento en volumen de agua, respectivamente. Es necesario obtener el bajo punto de rocío para reducir los óxidos metálicos durante el proceso de sinterización y para, de ese modo, producir un material con alta densidad y buenas propiedades mecánicas. En este ejemplo de aplicación debería ser necesaria una temperatura de elemento de entre 1400 y 1550°C, dependiendo de la forma del elemento y del diseño del horno. Por consiguiente, bajo esas condiciones la capa de SiO2 no es estable sobre elementos de calentamiento basados en MoSi2.
Los elementos de calentamiento que se utilizan en la actualidad en muchos hornos para sinterización de polvo metálico en el rango de temperatura por encima de 1250-1300°C se fabrican, sobre todo, de molibdeno, pero también de tungsteno. Una limitación de este material es, además de su coste total relativamente alto en hornos, la necesidad de mantener a los elementos en todas las circunstancias por encima de 400°C en una atmósfera pobre en oxígeno para evitar que se produzca esa oxidación perjudicial del metal de molibdeno puro. Por ejemplo, esos elementos pueden resultar dañados como consecuencia de fugas en los hornos u otras averías.
Los materiales alternativos que existen para el calentamiento por resistencia eléctrica en estas condiciones son aleaciones y compuestos intermetálicos como FeCrAl, NiCr y MoSi2 (por ejemplo, Kanthal Super como se mencionó anteriormente) . Las limitaciones del material MoSi2 se describieron anteriormente. Cuando se usan en aire, FeCrAl y NiCr forman óxidos de Al2O3 y Cr2O3, respectivamente, sobre la superficie. En atmósfera reductora, como gas hidrógeno seco, el rango de temperatura de uso está limitado a aproximadamente 1400°C para FeCrAl y a 1250°C para, por ejemplo, NiCr de la marca registrada Nicrothal 80, respectivamente.
En el caso de las aleaciones de NiCr el Cr2O3 no es estable por encima de esta temperatura. En el caso de FeCrAl la capa de Al2O3 ciertamente permanece estable, pero la vida útil del material a esta temperatura está limitada por la cercana temperatura de fusión de aproximadamente 1500°C. De esta manera, si se debiera usar el FeCrAl para la sinterización de acero 316L, las necesidades de altas temperaturas de los elementos conducirán a vidas útiles muy limitadas.
Sería deseable utilizar un material que combinase la posibilidad de formar alúmina sobre la superficie con una temperatura de fusión considerablemente mayor que 1500°C y que, de ese modo, si fuera necesario, se podría usar 2
de forma alternativa en atmósfera reductora y en atmósfera oxidante. Además, se podrían eliminar entonces las desventajas de los elementos de molibdeno, dado que los elementos no se tienen que utilizar siempre en una atmósfera pobre en oxígeno.
El uso del siliciuro específico se describe en la reivindicación 1.
Se ha mostrado sorprendentemente que, al alear MoSi2 con Al en una cantidad suficiente y también con una fase de alúmina, se obtiene una fase de siliciuro de alúmina molibdeno, Mo (Si) 1-XAlX) 2, la cual es estable en gas hidrógeno seco a altas temperaturas. Por ejemplo, en un ensayo de corrosión en gas hidrógeno a 1450°C, se ha mostrado que el material compuesto MoSi1, 6Al0, 4/Al2O3 no muestra ninguna corrosión después de 200 horas, sino un significativo incremento de peso del 0, 2%, lo cual responde a una oxidación del aluminio presente en el aluminosiliciuro para formar Al2O3. En una investigación comparativa con Kanthal Super 1800, consistente en MoSi2 y aproximadamente un 20 por ciento en volumen de silicato de aluminio, se ha mostrado que el peso disminuyó aproximadamente un 30% en las mismas condiciones. En este caso, además de la capa de SiCO2, la fase MoSi2, Mo5Si3 y Mo3Si y también el agente ligante que contiene silicato de aluminio sufrieron reducción.
Es razonable asumir que se pueden utilizar incluso otras composiciones para obtener resultados similares. Por ejemplo, se ha mostrado que MoSi1, 75Alo0, 25/Al2O3 forma Al2O3 bajo oxidación en aire a 1200°C. Para valores de x en el rango de 0, 1-0, 6 la fase hexagonal, denominada C-40, de Mo (Si, Al) 2 es estable. Es razonable asumir que la presente invención se podría aplicar incluso con esas composiciones. El valor de x debería estar comprendido entre 0, 10-0, 60, preferiblemente entre 0, 20-0, 55.
Con trabajo experimental en conexión con la presente invención se demostró apropiado, que la fase de siliciuro esté comprendida entre 65 y 95 por ciento en peso del peso total del elemento de resistencia, preferiblemente entre 75 y 85 por ciento en peso.
Como se ha mencionado anteriormente, además de la fase de siliciuro, el elemento de resistencia también contiene alúmina.
El complemento puede consistir en SiO2, de forma apropiada entre 0 y 1 por ciento en peso.
La invención anteriormente descrita se podría utilizar en otras aplicaciones de sinterización, en las que sea necesario un bajo potencial de oxígeno o, de forma alternativa, un bajo punto de rocío. Esto sucede, a veces, en la sinterización de aleación pesada de polvo de tungsteno, ciertos tipos de aleaciones de titanio y compuestos intermetálicos, y también de aceros poco aleados. Por ejemplo, la aleación pesada W-Cu se ha sinterizado en hidrógeno a 1400°C con un punto de rocío de -36°C.
Se espera que la alúmina formada, antes mencionada, sea estable hasta una temperatura de aproximadamente 1595°C, que es la temperatura eutéctica en el sistema SiO2-3Al2O3·2SiO2 (mullita) . Se espera que este óxido tenga propiedades frente a corrosión diferentes a las de la alúmina pura. De ese modo, hasta al menos la temperatura del elemento de aproximadamente 1595°C, este material podría constituir una alternativa general a los elementos de calentamiento de tipo molibdeno.
Reivindicaciones:
1. Utilización de un elemento de resistencia eléctrica que consiste principalmente en una fase de siliciuro de acuerdo con la fórmula Mo (Si1-XAlX) 2, formando dicha fase alúmina sobre la superficie del elemento, estando el valor de x
comprendido entre 0, 10 y 0, 60, para la sinterización de polvo metálico, de polvo de aleación pesada de tungsteno, o de compuestos intermetálicos.
2. Utilización de un elemento de resistencia eléctrica de acuerdo con la reivindicación 1, donde el polvo metálico es del tipo de aleaciones basadas en hierro.
3. Utilización de un elemento de resistencia eléctrica de acuerdo con la reivindicación 2, donde el polvo metálico es un acero inoxidable.
4. Utilización de un elemento de resistencia eléctrica de acuerdo con la reivindicación 3, donde la designación de la 15 aleación es AISI316L.
5. Utilización de un elemento de resistencia eléctrica de acuerdo con la reivindicación 1, para la sinterización de aleaciones de titanio.
6. Utilización de un elemento de resistencia eléctrica de acuerdo con la reivindicación 1, para la sinterización de aceros poco aleados.
7. Utilización de un elemento de resistencia eléctrica de acuerdo con cualquiera de las reivindicaciones anteriores, donde el valor de x está comprendido entre 0, 20 y 0, 55.
8. Utilización de un elemento de resistencia eléctrica de acuerdo con cualquiera de las reivindicaciones anteriores, donde la fase de siliciuro está comprendida entre 65 y 95 por ciento en peso del peso total del elemento de resistencia, preferiblemente entre 75 y 85 por ciento en peso.
9. Utilización de un elemento de resistencia eléctrica de acuerdo con cualquiera de las reivindicaciones anteriores, donde el elemento contiene un complemento de SiO2 además de la fase de siliciuro mencionada y de la Al2O3 deseada.
Patentes similares o relacionadas:
Aleación inoculante para piezas gruesas de fundición, del 18 de Diciembre de 2019, de FERROPEM: Aleación inoculante a base de ferrosilicio para el tratamiento de una fundición para la fabricación de piezas que presentan unas partes de espesores superiores a 6 mm, […]
Variaciones de composición del tetraboruro de wolframio con metales de transición y elementos ligeros, del 18 de Octubre de 2017, de THE REGENTS OF THE UNIVERSITY OF CALIFORNIA: Una variación de la composición del tetraboruro de wolframio que comprende: wolframio (W); boro (B) y al menos un elemento seleccionado del grupo […]
Procedimiento de fabricación de un material termoeléctrico, del 14 de Septiembre de 2016, de COMMISSARIAT A L'ENERGIE ATOMIQUE ET AUX ENERGIES ALTERNATIVES: Procedimiento de fabricación de un material termoeléctrico que comprende las etapas siguientes: - preparar un polvo a partir de una aleación […]
Elemento de resistencia eléctrica, del 30 de Marzo de 2016, de SANDVIK INTELLECTUAL PROPERTY AB: Utilización de un elemento de resistencia eléctrica para sinterización de polvo metálico en particular, en hornos de sinterización de bajo […]
MATERIAL DE SILICIURO DE MOLIBDENO DE ALTA RESISTENCIA., del 16 de Julio de 2006, de SANDVIK AKTIEBOLAG: Material de siliciuro de molibdeno con una resistencia alta, tanto a temperatura ambiente como a temperaturas altas, siendo dicho material un material compuesto realizado […]
MATERIAL COMPOSITE RESISTENTE A LAS ALTAS TEMPERATURAS Y RESISTENTE AL CALOR "REFSIC", del 16 de Noviembre de 2011, de UCHREZHDENIE ROSSIISKOI AKADAMII NAUK INSTITUT FIZIKI TVERDOGO TELA RAN (IFTT RAN): Material composite refractario y resistente a la temperatura que comprende carburo de silicio y disiliciuro de molibdeno MoSi2, caracterizado porque […]
MATERIAL RESISTENTE AL CALOR REFSICOAT Y CALENTADORES ELECTRICOS PARA ALTA TEMPERATURA UTILIZANDO DICHO MATERIAL, del 16 de Abril de 2009, de INSTITUT FIZIKI TVERDOGO TELA AKADEMII NAUK SSSR: Material resistente al calor que comprende siliciuros de molibdeno y de tungsteno Me 5Si 3 y MeSi 2 y opcionalmente carburo de silicio, caracterizado porque comprende siliciuros […]
METODO PARA OBTENER UN ELEMENTO CALEFACTOR DE TIPO DE SILICIURO DE MOLIBDENO Y UN ELEMENTO CALEFACTOR, del 16 de Mayo de 2008, de SANDVIK INTELLECTUAL PROPERTY AB: Un método para producir un elemento calefactor que está constituido esencialmente por siliciuro de molibdeno y aleaciones de este material básico, caracterizado por produ-cir […]