Reducción de la transferencia de vibraciones.
Una barrera (1) de disipación de ondas vibratorias que comprende un soporte (2) que tiene una superficie internay una superficie externa,
comprendiendo el soporte sobre su superficie externa un revestimiento (3) que comprendeun material termo-expansible seleccionado entre los que, tras la expansión y a una temperatura entre -10 y +40 ºC,tienen un módulo de Young E entre 0,1 MPa y 500 MPa y un módulo de Shear G entre 0,1 MPa y 250 MPa, estandodeterminados los módulos por medio de análisis mecánico dinámico (AMD)
en el que el material termo-expansible comprende
- de 25 a 70 % en peso, preferentemente de 35 a 55 % en peso de al menos un elastómero termoplástico,
- de 0,1 a 2 % en peso, preferentemente de 0,1 a 1 % en peso, de al menos un estabilizador o antioxidante,
- de 2 a 15 % en peso de al menos un agente de soplado,
- de 0,5 a 4 % en peso de un agente de curado, que opcionalmente incluye de 0,5 a 2 % en peso de al menos unmonómero olefínicamente insaturado, y preferentemente
- hasta 10 % en peso de al menos una resina adherente,
- hasta 5 % en peso de un plastificante como coadyuvante de procesado,
- hasta 10 % en peso de al menos una cera,
- hasta 3 % en peso de un activador para el agente de soplado,
así como también opcionalmente al menos una sustancia de relleno,
estando los porcentajes expresados en porcentajes en peso del peso total del material termo-expansible, y elelastómero termoplástico está seleccionado dentro del grupo que consiste en poliuretanos termoplásticos (TPU) ycopolímeros de bloques seleccionados dentro del grupo que consiste en copolímeros de SBS(estireno/butadieno/estireno), copolímeros SIS (estireno/isopreno/estireno), copolímeros SEPS(estireno/etileno/propileno/estireno), SEEPS (estireno/etileno/etileno/propileno/estireno) o SEBS(estireno/etileno/butadieno/estireno), copolímeros de etileno-acetato de vinilo con un 5 a 40 % en peso de acetato devinilo, copolímeros de etileno y (met)acrilatos de alquilo C1 a C6 con 5 a 40 % en peso de (met)acrilato de alquilo C1a C6, que comprenden opcionalmente ácido (met)acrílico polimerizado o anhídrido maleico, poliéter-ésteres, poliéteramidaso mezclas de los elastómeros anteriormente mencionados.
Tipo: Patente Europea. Resumen de patente/invención. Número de Solicitud: E05292082.
Solicitante: HENKEL AG & CO. KGAA.
Nacionalidad solicitante: Alemania.
Dirección: HENKELSTRASSE 67 40589 DUSSELDORF ALEMANIA.
Inventor/es: WOJTOWICKI,Jean-Luc, TAHRI,Laurent, GERMES,Sylvain.
Fecha de Publicación: .
Clasificación Internacional de Patentes:
- B60R21/04 TECNICAS INDUSTRIALES DIVERSAS; TRANSPORTES. › B60 VEHICULOS EN GENERAL. › B60R VEHICULOS, EQUIPOS O PARTES DE VEHICULOS, NO PREVISTOS EN OTRO LUGAR (prevención, limitación o extinción de incendios especialmente adaptadas a los vehículos A62C 3/07). › B60R 21/00 Disposiciones o equipamientos sobre los vehículos para proteger a los ocupantes o a los peatones o para evitar ser dañados en caso de accidente o de otros riesgos de la circulación (cinturones o arneses de seguridad en los vehículos B60R 22/00; asientos construidos para proteger al ocupante de los efectos de las fuerzas de aceleración anormales, p. ej. asientos anticolisión o asientos de seguridad, B60N 2/42; disposiciones para absorber la energía en los volantes de dirección de vehículos B62D 1/11; disposiciones para absorber la energía en las columnas de dirección de vehículos B62D 1/19). › Revestimientos tapizados para el interior del vehículo.
- C08J9/00 QUIMICA; METALURGIA. › C08 COMPUESTOS MACROMOLECULARES ORGANICOS; SU PREPARACION O PRODUCCION QUIMICA; COMPOSICIONES BASADAS EN COMPUESTOS MACROMOLECULARES. › C08J PRODUCCION; PROCESOS GENERALES PARA FORMAR MEZCLAS; TRATAMIENTO POSTERIOR NO CUBIERTO POR LAS SUBCLASES C08B, C08C, C08F, C08G o C08H (trabajo, p. ej. conformado, de plásticos B29). › Producción de sustancias macromoleculares para producir artículos o materiales porosos o celulares; Su tratamiento posterior (aspectos mecánicos del modelado de materias plásticas o sustancias en estado plástico para la fabricación de objetos porosos o celulares B29C).
- C09D153/02 C […] › C09 COLORANTES; PINTURAS; PULIMENTOS; RESINAS NATURALES; ADHESIVOS; COMPOSICIONES NO PREVISTAS EN OTRO LUGAR; APLICACIONES DE LOS MATERIALES NO PREVISTAS EN OTRO LUGAR. › C09D COMPOSICIONES DE REVESTIMIENTO, p. ej. PINTURAS, BARNICES, LACAS; EMPLASTES; PRODUCTOS QUIMICOS PARA LEVANTAR LA PINTURA O LA TINTA; TINTAS; CORRECTORES LIQUIDOS; COLORANTES PARA MADERA; PRODUCTOS SOLIDOS O PASTOSOS PARA ILUMINACION O IMPRESION; EMPLEO DE MATERIALES PARA ESTE EFECTO (cosméticos A61K; procedimientos para aplicar líquidos u otros materiales fluidos a las superficies, en general B05D; coloración de madera B27K 5/02; vidriados o esmaltes vitreos C03C; resinas naturales, pulimento francés, aceites secantes, secantes, trementina, per se , C09F; composiciones de productos para pulir distintos del pulimento francés, cera para esquíes C09G; adhesivos o empleo de materiales como adhesivos C09J; materiales para sellar o guarnecer juntas o cubiertas C09K 3/10; materiales para detener las fugas C09K 3/12; procedimientos para la preparación electrolítica o electroforética de revestimientos C25D). › C09D 153/00 Composiciones de revestimiento a base de copolímeros en bloque con al menos un bloque de un polímero obtenido por reacciones en las que únicamente intervienen enlaces insaturados carbono-carbono; Composiciones de revestimiento a base de derivados de tales polímeros. › Monómeros vinílicos aromáticos y dienos conjugados.
- E04C2/284 CONSTRUCCIONES FIJAS. › E04 EDIFICIOS. › E04C ELEMENTOS ESTRUCTURALES; MATERIALES DE CONSTRUCCION (para puentes E01D; especialmente concebidos para aislamiento o cualquier otra protección E04B; elementos utilizados como auxiliares para la construcción E04G; para minas E21; para túneles E21D; elementos estructurales con un campo de aplicación más amplio que el de la industria de la edificación F16, concretamente F16S). › E04C 2/00 Elementos de construcción de espesor relativamente débil para la construcción de partes de edificios, p. ej. materiales en hojas, losas o paneles (materiales o fabricación ver los lugares apropiados, p. ej. B27N, B29, D21J; fabricados in situ E04B; concebidos especialmente para el aislamiento o cualquier otra protección E04B 1/62; estructuras portantes de suelos E04B 5/02, E04B 5/16; tejados constituidos por losas que se autosustentan E04B 7/20; elementos de cubiertas de tejados o análogos E04D 3/00; para el revestimiento o el terminado E04F 13/00). › al menos uno de los materiales es aislante.
- G10K11/168 FISICA. › G10 INSTRUMENTOS MUSICALES; ACUSTICA. › G10K DISPOSITIVOS GENERADORES DE SONIDOS (juguetes musicales o sonoros A63H 5/00 ); METODOS O DISPOSITIVOS PARA PROTEGER CONTRA, O PARA AMORTIGUAR, RUIDO U OTRAS ONDAS ACUSTICAS EN GENERAL; ACUSTICA NO PREVISTA EN OTRO LUGAR. › G10K 11/00 Métodos o dispositivos para transmitir, conducir o dirigir el sonido en general; Métodos o dispositivos de protección contra el ruido u otras ondas acústicas en general, o para amortiguarlas. › Varias capas de materiales diferentes, p. ej. sandwiches.
PDF original: ES-2449515_T3.pdf
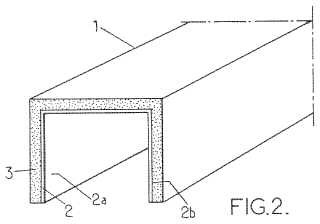
Fragmento de la descripción:
Reducción de la transferencia de vibraciones La presente invención se refiere a la reducción de la transferencia de vibraciones generadas por un generador de vibraciones.
En un vehículo, la transferencia de vibraciones generadas por medio de un generador de fuerza dinámica, tal como un motor, una bomba o caja de cambios, por medio de elementos estructurales hasta una superficie de emisión tal como un panel, conduce a la emisión de ruido transmitido por la estructura.
Se han sugerido diferentes soluciones con el fin de reducir al menos dicho ruido transmitido por la estructura. En la construcción del vehículo, se han propuesto medidas pasivas tales como el recurso de atenuadores de vibraciones o mallados de atenuación. Con frecuencia, dichos mallados de atenuación se aplican sobre paneles de vibración, por ejemplo, en las puertas o sobre el suelo del vehículo. Con frecuencia, el alcance de la reducción de ruido de estos métodos resulta insatisfactorio.
En el proceso convencional, se someten a extrusión mezclas de alquitrán o asfalto y sustancias de relleno con un elevado peso específico en el interior de las planchas, que se cortan o perforan con las formas apropiadas. Posteriormente, se unen estas planchas a las partes de plancha metálica apropiada y, en ocasiones, es preciso adaptarlas a la forma de la plancha por medio de calentamiento. Aunque estas planchas de alquitrán todavía se usan de manera frecuente debido a su reducido coste de materias primas, son muy frágiles y tienden a despegarse de la plancha metálica en particular a bajas temperaturas. De igual forma, se ha propuesto la incorporación de aditivos que con frecuencia únicamente tienen como resultado una ligera mejora que no resulta suficiente para muchas aplicaciones. Además, resulta completamente imposible aplicar las partes de alquitrán pre-conformadas a las partes de plancha metálica con forma compleja o casi inaccesibles de las máquinas o vehículos, por ejemplo, las superficies internas de las cavidades de las puertas de los vehículos a motor. Además, existe la desventaja adicional de que en muchos casos se requieren varias partes perforadas para un único vehículo o aplicación y, por tanto, se requiere un almacenamiento costoso.
Por consiguiente, no han escaseado los intentos para eliminar las desventajas de las planchas de alquitrán usando otros sistemas poliméricos. Por ejemplo, se desarrollaron las dispersiones poliméricas acuosas de copolímeros de poli (acetato de vinilo) o etileno-acetato de vinilo que contenían sustancias de relleno, y que se podían pulverizar sobre las partes de la plancha metálica con el espesor de revestimiento necesario. No obstante, estos sistemas resultan desventajosos para uso industrial cuando se generan tasas elevadas de producción, debido a que no es posible retirar el agua de forma suficientemente rápida a partir del revestimiento que se pulveriza, en particular cuando este revestimiento es bastante grueso.
Las propiedades de atenuación del sonido de los revestimientos poliméricos son las mejores dentro del intervalo de la temperatura de transición vítrea del sistema polimérico ya que, debido a la viscoelasticidad del polímero en este intervalo de temperatura, la energía mecánica del proceso de vibración se convierte en calor por medio de un fenómeno de flujo molecular. Los materiales de revestimiento pulverizables convencionales basados en plastisoles de PVC, que por ejemplo se usan ampliamente como revestimiento para bajos de carrocería en la construcción de vehículos a motor, no tienen un efecto notable de atenuación del sonido en el intervalo de temperatura de aplicación de -20 a + 60 ºC, debido a que el valor máximo de la transición vítrea es de aproximadamente -20 ºC a -50 ºC, dependiendo de la proporción de plastificante.
La patente de Estados Unidos Nº. 3.855.028 también describe capas de atenuación de sonido basadas en PVC.
Por tanto, se han llevado a cabo intentos para modificar estos plastisoles de PVC convencionales de manera que presenten mejores propiedades de atenuación del sonido en el intervalo de temperatura de aplicación de - 20 ºC a + 60 ºC. Se conocen revestimientos a partir de la solicitud de patente alemana publicada 35 14 753, que contiene compuestos insaturados múltiples, por ejemplo di- o triacrilato, agentes de reticulación de peróxido y sustancias de relleno inorgánicas, en los plastisoles de PVC convencionales. En estado endurecido estos plastisoles son, sin embargo, duros como el vidrio y frágiles, y por tanto no resultan realmente apropiados para su uso en la construcción de automóviles debido a que no tienen suficiente flexibilidad en particular a bajas temperaturas. Aparte de esto, estas formulaciones presentan un factor de pérdida tan δ muy bajo y, de este modo, el efecto de atenuación del sonido no es muy marcado.
Las composiciones se describen en la solicitud de patente alemana publicada 34 44 863, que contiene copolímeros de PVC o cloruro de vinilo/acetato de vinilo, opcionalmente copolímeros u homopolímeros de metacrilato de metilo, una mezcla de plastificante y sustancias de relleno inertes. La mezcla de plastificante comprende plastificantes que son compatibles con los polímeros de metacrilato de metilo y los plastificantes para los polímeros de cloruro de vinilo que son incompatibles con los polímeros de metacrilato que pueden estar presentes. Los plastisoles obtenidos de este modo tienen propiedades mejoradas de atenuación del sonido en comparación con los plastisoles de PVC convencionales. No obstante, en particular a temperaturas por encima de aproximadamente 30 ºC, el efecto de atenuación del sonido disminuye de nuevo. Si se lleva a cabo un intento de modificar el intervalo de factor máximo
de pérdida tan δ hasta temperaturas más elevadas, por medio de la variación de las cantidades relativas de los componentes individuales, la flexibilidad en frío del revestimiento disminuye de forma drástica. No obstante, una flexibilidad en frío reducida es precisamente lo que resulta desventajoso en la construcción de vehículos. Además el factor de pérdida disminuye de manera muy marcada a temperaturas bajas con estas formulaciones. Por tanto, estas composiciones de plastisol tienen un factor de pérdida suficientemente elevado únicamente en un intervalo de temperaturas muy estrecho.
La solicitud de patente japonesa publicada JP 2-57340 muestra una composición sofisticada de atenuación de sonido que comprende una primera capa eléctricamente conductora y una segunda capa apta para reticulación y formación de espuma. La capa apta para formación de espuma comprende un componente de caucho natural o sintético y un elastómero termoplástico.
Además, se han desarrollado medidas activas para reducir el ruido transmitido por la estructura. Normalmente, estas medidas emplean sensores, procesado de señales, accionadores y fuentes de energía para contrarrestar o aumentar de manera eficaz la disipación de la vibración por medio de la producción de las correspondientes fuerzas o tensiones.
Aunque se ha comprobado que las medidas de control activas reducen eficazmente el ruido transmitido por la estructura, requieren un equipamiento técnico sofisticado, especialmente con respecto al procesado de señales y sensores. Esto no solo aumenta los costes, sino que también conduce a un mayor riesgo de rotura.
Por tanto, existe una necesidad de medios rentables para reducir eficazmente el ruido transmitido por la estructura en un sistema, especialmente en un vehículo.
Por tanto, es un objetivo de la presente invención solucionar los inconvenientes de la técnica anterior.
Tras un amplio e intenso trabajo de investigación, los inventores acaban de descubrir que esto se puede lograr por medio de una barrera particular de disipación de ondas vibratorias de acuerdo con la reivindicación independiente 1 y un método que emplea dicha barrera de disipación de ondas vibratorias de acuerdo con la reivindicación independiente 14.
La barrera de disipación de ondas vibratorias de acuerdo con la presente invención comprende un soporte que tiene una superficie interna y una superficie externa, presentando la barrera una sección poligonal, especialmente rectangular, opcionalmente con forma de U y que comprende sobre su superficie externa un revestimiento que comprende un material termo-expansible seleccionado entre aquellos que, tras la expansión y a una temperatura entre -10 y + 40 ºC, tienen un módulo de Young E entre 0, 1 MPa y 1000 MPa, preferentemente de 500 MPa, un factor de pérdida η (en ocasiones también denominado como tan δ) entre 0, 5 y 1 y un módulo de Shear G entre 0, 1 MPa y 500 MPa, preferentemente de 250 MPa. Los módulos,... [Seguir leyendo]
Reivindicaciones:
1. Una barrera (1) de disipación de ondas vibratorias que comprende un soporte (2) que tiene una superficie interna y una superficie externa, comprendiendo el soporte sobre su superficie externa un revestimiento (3) que comprende un material termo-expansible seleccionado entre los que, tras la expansión y a una temperatura entre -10 y +40 ºC, tienen un módulo de Young E entre 0, 1 MPa y 500 MPa y un módulo de Shear G entre 0, 1 MPa y 250 MPa, estando determinados los módulos por medio de análisis mecánico dinámico (AMD)
en el que el material termo-expansible comprende
- de 25 a 70 % en peso, preferentemente de 35 a 55 % en peso de al menos un elastómero termoplástico,
- de 0, 1 a 2 % en peso, preferentemente de 0, 1 a 1 % en peso, de al menos un estabilizador o antioxidante,
- de 2 a 15 % en peso de al menos un agente de soplado,
- de 0, 5 a 4 % en peso de un agente de curado, que opcionalmente incluye de 0, 5 a 2 % en peso de al menos un monómero olefínicamente insaturado, y preferentemente
- hasta 10 % en peso de al menos una resina adherente,
- hasta 5 % en peso de un plastificante como coadyuvante de procesado,
- hasta 10 % en peso de al menos una cera,
- hasta 3 % en peso de un activador para el agente de soplado,
así como también opcionalmente al menos una sustancia de relleno,
estando los porcentajes expresados en porcentajes en peso del peso total del material termo-expansible, y el elastómero termoplástico está seleccionado dentro del grupo que consiste en poliuretanos termoplásticos (TPU) y copolímeros de bloques seleccionados dentro del grupo que consiste en copolímeros de SBS (estireno/butadieno/estireno) , copolímeros SIS (estireno/isopreno/estireno) , copolímeros SEPS (estireno/etileno/propileno/estireno) , SEEPS (estireno/etileno/etileno/propileno/estireno) o SEBS (estireno/etileno/butadieno/estireno) , copolímeros de etileno-acetato de vinilo con un 5 a 40 % en peso de acetato de vinilo, copolímeros de etileno y (met) acrilatos de alquilo C1 a C6 con 5 a 40 % en peso de (met) acrilato de alquilo C1 a C6, que comprenden opcionalmente ácido (met) acrílico polimerizado o anhídrido maleico, poliéter-ésteres, poliéteramidas o mezclas de los elastómeros anteriormente mencionados.
2. La barrera (1) de disipación de ondas vibratorias de acuerdo con la reivindicación 1, en la que el portador (2) está formado por metal, y especialmente acero galvanizado o aluminio.
3. La barrera (1) de disipación de ondas vibratorias de acuerdo con la reivindicación 1, en la que el portador (2) está formado por un material sintético, opcionalmente reforzado con fibras, y especialmente por un material sintético termoplástico, seleccionado dentro del grupo que consiste en poliamidas (PA) , poli (sulfuro de fenileno) (PPS) , poli (éter de fenileno) (PPE) , polifenilen sulfona (PPSU) y polifenilen-imida (PPI) , estando el material sintético termoplástico opcionalmente reforzado con fibras, teniendo una baja absorción de agua y una estabilidad de dimensión hasta 180 ºC.
4. La barrera (1) de disipación de ondas vibratorias de acuerdo con cualquiera de las reivindicaciones 1 a 3, en el que el soporte (2) tiene un corte transversal poligonal, especialmente rectangular, opcionalmente con forma de U que comprende sobre su superficie externa un revestimiento (3) .
5. La barrera (1) de disipación de ondas vibratorias de acuerdo con cualquiera de las reivindicaciones 1 a 4, en la que el material termo-expansible comprende
-de 35 a 55 % en peso de al menos un elastómero termoplástico,
- de 0, 1 a 1 % en peso, de al menos un estabilizador o antioxidante,
- de 2 a 15 % en peso de al menos un agente de soplado,
- de 0, 5 a 4 % en peso de un agente de curado, que opcionalmente incluye de 0, 5 a 2 % en peso de al menos un monómero olefínicamente insaturado, y preferentemente
- hasta 10 % en peso de al menos una resina adherente,
- hasta 5 % en peso de un plastificante como coadyuvante de procesado,
- hasta 10 % en peso de al menos una cera,
- hasta 3 % en peso de un activador para el agente de soplado,
así como también opcionalmente al menos una sustancia de relleno,
estando los porcentajes expresados en porcentajes en peso del peso total del material termo-expansible.
6. La barrera (1) de disipación de ondas vibratorias de acuerdo con cualquiera de las reivindicaciones 1 a 5, en la que la resina adherente está seleccionada dentro del grupo que consiste en resinas de colofonia, resinas de terpeno, resinas fenólicas de terpeno, resinas de hidrocarburo procedentes de destilados de petróleo craqueados, resinas adherentes aromáticas, resinas líquidas, resinas de cetona y resinas de aldehído.
7. La barrera (1) de disipación de ondas vibratorias de acuerdo con la reivindicación 6, en la que la resina de colofonia está seleccionada dentro del grupo que consiste en ácido abiético, ácido levopimárico, ácido neoabiético, ácido dextropimárico, ácido palústrico, ésteres alquílicos de los ácidos de colofonia anteriormente mencionados, productos de hidrogenación de derivados de ácido de colofonia.
8. La barrera (1) de disipación de ondas vibratorias de acuerdo con cualquiera de las reivindicaciones 1 a 7, en la que el plastificante está seleccionado dentro del grupo que consiste en ésteres alquílicos C1-10 de ácidos dibásicos, éteres diarílicos, poli (benzoatos de alquilenglicoles) , fosfatos orgánicos, ésteres de ácido alquilsulfónico de fenol o cresol.
9. La barrera (1) de disipación de ondas vibratorias de acuerdo con cualquiera de las reivindicaciones 1 a 8, en la que la cera está seleccionada dentro del grupo que consiste en ceras parafínicas que tienen intervalos de fusión de 45 a 70 ºC, ceras microcristalinas con intervalos de fusión de 60 a 95 ºC, ceras sintéticas de Fischer-Tropsch con puntos de fusión entre 100 y 115 ºC o poli (ceras de etileno) con puntos de fusión entre 85 y 140 ºC.
10. La barrera (1) de disipación de ondas vibratorias de acuerdo con cualquiera de las reivindicaciones 1 a 9, en la que el antioxidante está seleccionado dentro del grupo que consiste en fenoles con impedimento estérico y/o tioéteres, y aminas aromáticas con impedimento estérico.
11. La barrera (1) de disipación de ondas vibratorias de acuerdo con cualquiera de las reivindicaciones 1 a 10, en la que el agente de soplado está seleccionado dentro del grupo que consiste en azobisisobutironitrilo, azodicarbonamida, di-nitrosopentametilentetramina, 4, 4´-oxibis (hidrazida de ácido bencenosulfónico) , difenil-sulfona3, 3´-disulfohidrazida, benceno-1, 3-disulfohidrazida, p-toluensulfonil semicarbazida y microperlas huecas expansibles de plástico basadas en copolímeros de poli (cloruro de vinilideno) o copolímeros de acrilonitrilo/ (met) acrilato.
12. La barrera (1) de disipación de ondas vibratorias de acuerdo con cualquiera de las reivindicaciones 1 a 11, en la que el agente de curado está seleccionado dentro del grupo que consiste en hidroperóxido de cumeno, bis (tercbutilperoxi) diisopropilbenceno, di (2-terc-butil peroxiisopropil benceno) , 1, 1-di-terc-butilperoxi-3, 3, 5trimetilciclohexano, valerato de 4, 4-di-terc-butilperoxi-n-butilo.
13. La barrera (1) de disipación de ondas vibratorias de acuerdo con cualquiera de las reivindicaciones 1 a 12, en la que la sustancia de relleno está seleccionada dentro del grupo que consiste en yesos molidos o precipitados, negro de carbono, carbonatos de calcio-magnesio, barita y sustancias de relleno de silicato del tipo silicato de aluminiomagnesio-calcio.
14. Un método para reducir la transferencia de vibraciones procedentes de un generador de vibraciones hasta un punto al cual se encuentra conectado el generador de vibraciones por medio de un elemento estructural, que comprende equipar dicho elemento estructural con medios para disipar la energía vibracional producida por el generador de vibraciones, caracterizado por que el medio comprende una barrera de disipación de ondas vibratorias de acuerdo con una cualquiera de las reivindicaciones 1 a 12.
15. El método de acuerdo con la reivindicación 14 para reducir la transferencia de vibraciones desde uno de los generadores de vibraciones presente dentro de un vehículo automóvil hasta al menos una de las partes constitutivas del compartimiento del pasajero, al cual está conectado el generador de vibraciones por medio de un elemento estructural que tiene la forma de un raíl tubular con un corte transversal poligonal, en particular un corte transversal rectangular, que comprende, sucesivamente seleccionar una barrera (1) de disipación de ondas vibratorias de acuerdo con cualquiera de las reivindicaciones 1 a 13 que tiene dimensiones tales que se puede insertar en el interior del elemento estructural,
insertar la barrera (1) de disipación de ondas vibratorias en el interior del elemento estructural en una ubicación próxima al generador de vibraciones,
expandir el revestimiento termo-expansible (3) .
16. El método de acuerdo con la reivindicación 15, en el que las dimensiones de la barrera (1) de disipación de ondas vibratorias están seleccionadas de manera que se obtenga un espacio libre de aproximadamente 1 a 10 mm entre las superficies externas de la barrera (1) de disipación de ondas vibratorias y las superficies internas del elemento estructural.
17. El método de acuerdo con una de las reivindicaciones 15 ó 16, en el que el revestimiento termo-expansible se expande a una temperatura de 130 ºC a 240 ºC, preferentemente a una temperatura de 150 ºC a 200 ºC.
18. El método de cualquiera de las reivindicaciones 15 a 17, en el que el elemento estructural está sujeto a un etapa de electrorevestimiento tras la inserción de la barrera (1) de disipación de ondas vibratorias, provocando de este modo la expansión del revestimiento (3) .
19. El método de acuerdo con cualquiera de las reivindicaciones 15 a 19, en el que el soporte comprende una cantidad de material termoexpansible que está seleccionado de forma que, tras la expansión, su volumen ocupe el espacio libre que existe entre el soporte y la superficie interna del elemento estructural.
Patentes similares o relacionadas:
Composiciones térmicamente expandibles con derivados de urea, del 24 de Junio de 2020, de HENKEL AG & CO. KGAA: Composición térmicamente expandible, que contiene a) al menos un polímero de reticulación peroxídica, b) al menos un peróxido y c) al menos […]
Refuerzo de fibra de espumas que contienen agentes expansores, del 24 de Junio de 2020, de BASF SE: Procedimiento para fabricar una pieza moldeada con al menos una fibra (F), caracterizado porque en una pieza moldeada hecha de espuma que contiene agente expansor se introduce […]
Producción de materiales porosos mediante la expansión de geles polímericos, del 10 de Junio de 2020, de SUMTEQ GmbH: Un método para la producción de un material polimérico micro y nanoporoso, en donde (a) el material polimérico inicial se infla con un plastificante a una temperatura […]
Poli(fosfatos de alquileno) con higroscopía reducida, del 3 de Junio de 2020, de LANXESS DEUTSCHLAND GMBH: Mezcla, caracterizada por que contiene al menos tres poli(fosfatos de alquileno) de manera correspondiente a la fórmula (I), **(Ver fórmula)** en la que R1, […]
Material funcional con al menos un aditivo, del 6 de Mayo de 2020, de puren GmbH: Procedimiento para producir un material funcional que presenta una conductividad térmica según la norma EN 12667 de como máximo 0,10 W/(m * K), una densidad aparente […]
Uso de composiciones que comprenden HFO-1234ze o HFO-1234yf como composición refrigerante, del 29 de Abril de 2020, de HONEYWELL INTERNATIONAL INC.: Uso, como composición refrigerante, de una composición que comprende 1,3,3,3-tetrafluoropropeno (HFO-1234ze) o 2,3,3,3-tetrafluoropropeno (HFO-1234yf) y un lubricante seleccionado […]
Refuerzo con fibras de espumas de segmentos unidos entre sí, del 22 de Abril de 2020, de BASF SE: Cuerpo moldeado de espuma, donde la espuma comprende al menos dos segmentos de espuma unidos entre si, caracterizados porque al menos una fibra (F) esta ubicada con una region […]
Espuma de poliuretano termoestable que contiene retardador de llama polimérico bromado, del 15 de Abril de 2020, de DDP Specialty Electronic Materials US, Inc: Una espuma de poliuretano termoestable que comprende un polímero bromado, donde el polímero bromado ha copolimerizado en el mismo un resto butadieno […]