Producción en serie de artículos tridimensionales hechos de compuestos intermetálicos.
Procedimiento para la producción en serie de artículos tridimensionales hechos de un compuesto intermetálico a base de titanio y aluminio mediante fusión por haz de electrones,
que comprende las etapas de:
a) generar un modelo matemático tridimensional de dichos artículos y almacenarlo en una unidad de control;
b) preparar los polvos de dicho compuesto intermetálico con la misma composición química que el compuesto intermetálico final con el que se producen dichos artículos, en el que el tamaño de grano de dichos polvos oscila desde 20 hasta 150 μm;
c) depositar una cantidad de dichos polvos en una cámara de fusión para formar una capa de polvos con un espesor regular y sustancialmente uniforme;
d) precalentar dicha capa de polvos depositada en dicha cámara de fusión a una temperatura no inferior a 700°C pero por debajo del punto de fusión de dichos polvos;
e) realizar la fusión en condiciones de alto vacío realizando un barrido con un haz de electrones convergente en la zona correspondiente a una sección transversal de dichos artículos según el modelo tridimensional almacenado en dicha unidad de control;
f) poner la superficie superior de la última sección transversal de dichos artículos así formados al nivel de los polvos ubicados en dicha cámara de fusión y que están dispuestos alrededor de las partes ya formadas de dichos artículos;
g) repetir dichas etapas desde c) hasta f) hasta que se alcance la última sección transversal de dichos artículos según el modelo tridimensional almacenado en dicha unidad de control; y
h) proporcionar una etapa de enfriamiento final de dichos artículos al final de su formación en una atmósfera de gas inerte una vez que la temperatura de los artículos ha caído por debajo de aproximadamente 1200°C.
Tipo: Patente Europea. Resumen de patente/invención. Número de Solicitud: E07013153.
Solicitante: Avioprop S.r.l.
Nacionalidad solicitante: Italia.
Dirección: Via Papa Giovanni XXIII 9 28062 Cameri (NO) ITALIA.
Inventor/es: Pasquero,Giuseppe, Zanon,Giovanni Paolo, Gennaro,Paolo.
Fecha de Publicación: .
Clasificación Internacional de Patentes:
- B22F3/105 TECNICAS INDUSTRIALES DIVERSAS; TRANSPORTES. › B22 FUNDICION; METALURGIA DE POLVOS METALICOS. › B22F TRABAJO DE POLVOS METALICOS; FABRICACION DE OBJETOS A PARTIR DE POLVOS METALICOS; FABRICACION DE POLVOS METALICOS (fabricación de aleaciones mediante metalurgia de polvos C22C ); APARATOS O DISPOSITIVOS ESPECIALMENTE ADAPTADOS PARA POLVOS METALICOS. › B22F 3/00 Fabricación de piezas a partir de polvos metálicos, caracterizada por el modo de compactado o sinterizado; Aparatos especialmente concebidos para esta fabricación. › utilizando una corriente eléctrica, radiación láser o plasma (B22F 3/11 tiene prioridad).
- B22F5/04 B22F […] › B22F 5/00 Fabricación de piezas o de objetos a partir de polvos metálicos caracterizada por la forma particular del producto a realizar. › de paletas de turbinas.
PDF original: ES-2381854_T3.pdf
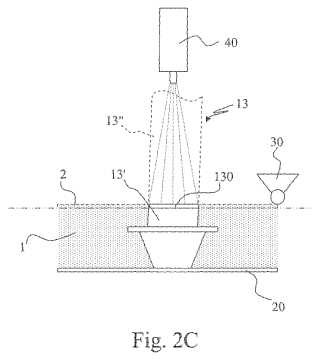
Fragmento de la descripción:
Producción en serie de artículos tridimensionales hechos de compuestos intermetálicos.
Campo técnico de la invención La presente invención se refiere a un procedimiento para producir artículos tridimensionales hechos de compuestos intermetálicos usando una técnica "capa a capa".
Antecedentes técnicos de la invención El procedimiento según la presente invención puede aplicarse, por ejemplo, en el sector de vehículos a motor y/o aeronáutico para producir componentes específicos tales como válvulas para motores de combustión interna, turbinas de gas, palas y/o rodetes para turbocompresores o similares.
Estos tipos de componentes deben tener propiedades notables de resistencia a fluencia y a fatiga a altas temperaturas. Por estos motivos, la investigación se orienta hacia diversos materiales, en particular compuestos intermetálicos, que puedan conferir las propiedades deseadas a cada artículo producido.
Los compuestos intermetálicos son compuestos metálicos cuyas estructuras cristalinas difieren de las de los metales de los que están compuestos. Se trata de una clase única de compuestos que están compuestos por fases ordenadas de dos o más materiales metálicos cuyas especies atómicas ocupan sitios específicos en la red cristalina. Estos compuestos se forman porque la fuerza de enlace entre átomos distintos es mayor que la de entre átomos iguales.
Los compuestos intermetálicos difieren considerablemente de las aleaciones metálicas convencionales. Éstas últimas se forman esencialmente de una disolución sólida desordenada de uno o más elementos metálicos, no tienen una fórmula química particular y se describen como consistentes en un material de base al que se han añadido porcentajes determinados de otros elementos. Los átomos de aleaciones convencionales están unidos mediante enlaces metálicos relativamente débiles, con núcleos atómicos que flotan en un "gas" de electrones que se mueven de manera relativamente libre.
Por el contrario, un compuesto intermetálico es un compuesto químico particular basado en una fórmula química bien definida, con una composición química que está fijada o en cualquier caso muy limitada en variabilidad. Los enlaces en compuestos intermetálicos pueden ser iónicos o covalentes, y por tanto particularmente fuertes. Alternativamente, la unión puede ser también completamente de tipo metálico, pero los átomos de los elementos individuales adoptan posiciones preferidas dentro de la red cristalina.
Estas peculiaridades se reflejan en las propiedades de los compuestos intermetálicos, tales como alto punto de fusión, resistencia notable a altas temperaturas pero escasa ductilidad.
Los compuestos intermetálicos de titanio y aluminio, y en particular los compuestos definidos con la abreviatura yTiAI (aluminuros de titanio y) , representan el grupo de compuestos intermetálicos de mayor interés para su aplicación en el campo de vehículos a motor y aeronáutico debido a sus propiedades de baja densidad y alta resistencia a altas temperaturas. Este grupo de compuestos intermetálicos incluye compuestos de yTiA1 con estructura L10 tetragonal centrada en las caras ordenada, y compuestos definidos con la abreviatura a2Ti3Al con estructura DO19 hexagonal ordenada. En condiciones de equilibrio termodinámico, la fracción de volumen y/a 2 se controla basándose en el contenido en aluminio y en otros elementos adicionales, pero los tratamientos térmicos y/o termomecánicos tienen una alta influencia en la fracción de volumen y/a2 en compuestos de yTiAI.
En vista del creciente interés por los compuestos intermetálicos de yTiAI, estudios llevados a cabo en los últimos 10 años han identificado intervalos de composición ideales que proporcionan un contenido en aluminio y titanio casi igual, entre 44% y 48%, junto con pequeños porcentajes de otros elementos que confieren propiedades específicas al compuesto intermetálico resultante. Para información adicional sobre compuestos intermetálicos véanse, por ejemplo, las siguientes publicaciones:
- G. Sauthoff "Intermetallics", Weinheim, Nueva York (1995) ; y
- H. Clemens, F. Appel, A. Bartels, H. Baur, R. Gerling, V. Guther, H. Kestler, "Processing and application of engineering g-TiA1 based alloys", en Ti-2003 Science and TechnoIogy, VoIumen IV, Wiley-VCH.
Las ventajas logradas mediante el uso de compuestos intermetálicos de yTiAI son principalmente su baja densidad (3, 9 a 4, 2 g/cm3 en función de su composición) , alto límite de elasticidad específico, alta rigidez específica, resistencia considerable a oxidación y buenas propiedades de fluencia hasta altas temperaturas. No obstante, como se ha mostrado, es difícil obtener un artículo producido con un compuesto intermetálico de yTiA1 con exactamente la composición y estructura deseada. Un típico ejemplo de artículos que pueden producirse ventajosamente con un compuesto intermetálico deyTiAI considera las palas de turbina de gas. Además de las dificultades ya mencionadas en cuanto a obtener un artículo producido con el material deseado, debe tenerse en cuenta también que estos artículos requieren operaciones de mecanizado extremadamente precisas pero que son difíciles de producir en serie a costes razonables con técnicas metalúrgicas convencionales, sobre todo debido a su geometría extremadamente compleja. Una dificultad adicional radica en el hecho de que artículos de este tipo deben tener un contenido en oxígeno extremadamente bajo, preferiblemente mucho menor que 1.500 ppm.
El mecanizado a partir de piezas de trabajo sólidas conlleva costes muy altos y es por tanto inaceptable para la producción en serie. Otras técnicas de fabricación conocidas para este tipo de componente son simplemente igual de poco rentables.
Por ejemplo, la técnica de moldeo a la cera perdida puede conllevar a un alto número de descartes, sobre todo debido a las porosidades y grietas que se crean en artículos así producidos y no permite que se obtengan geometrías particularmente complejas.
Otra técnica usada ampliamente es el forjado por presión, pero además de requerir particularmente altas temperaturas y por tanto alto consumo de energía, todavía es difícil obtener geometrías complejas sin requerir varios otros ciclos de mecanizado para cada artículo producido.
Ninguna de estas técnicas conocidas es por tanto capaz de garantizar la repetibilidad necesaria en la composición del material, y por tanto de las propiedades mecánicas en artículos producidos en serie. Esto es un requisito esencial, sobre todo para la producción en serie de componentes para motores y/o turbinas, para garantizar un alto nivel de fiabilidad.
Se han añadido recientemente técnicas alternativas de fabricación a técnicas convencionales, tales como técnicas de fabricación "capa a capa", que esencialmente usan un haz de luz láser convergente para obtener fusión y/o sinterización de secciones o capas sucesivas de materiales fundidos mediante una luz láser incidente.
Estas técnicas, conocidas por ejemplo como "formación directa por láser" (DLF, Direct Laser Forming) o "conformación final mediante ingeniería por láser" (LENS, Laser Engineered Net Shaping) , conllevan un sistema de lanzamiento de los polvos metálicos generalmente solidario con el emisor de luz láser y la inyección simultánea de un chorro de gas inerte (argón) , alineado con el haz de láser para proteger la zona de fusión de la oxidación.
No obstante, se produce un alto grado de turbulencia en el punto de fusión debido no sólo al chorro de gas inerte, sino también a la evaporación de polvos metálicos, sobre todo en el caso de polvos de aluminio. De hecho, la temperatura en las cámaras de fusión es particularmente baja, del orden de aproximadamente 100°C, pero los polvos metálicos tienen temperaturas de fusión muy altas, a menudo por encima de 1000°C. El haz de la luz láser pierde convergencia haciendo difícil el procedimiento de fusión y la evaporación de parte de las especies químicas con temperaturas de fusión más bajas pone en peligro la composición final del artículo. Además, el chorro de argón solo no puede limitar la oxidación del artículo durante la fabricación a valores aceptables.
Consecuentemente, estas técnicas conocidas no pueden utilizarse para la producción en serie, ni pueden usarse para producir artículos hechos de compuestos intermetálicos, sino que, como mucho, pueden usarse para producir recubrimientos de aleaciones metálicas en artículos ya fabricados ("chapado... [Seguir leyendo]
Reivindicaciones:
1. Procedimiento para la producción en serie de artículos tridimensionales hechos de un compuesto intermetálico a base de titanio y aluminio mediante fusión por haz de electrones, que comprende las etapas de:
a) generar un modelo matemático tridimensional de dichos artículos y almacenarlo en una unidad de control;
b) preparar los polvos de dicho compuesto intermetálico con la misma composición química que el compuesto intermetálico final con el que se producen dichos artículos, en el que el tamaño de grano de dichos polvos oscila desde 20 hasta 150 !m;
c) depositar una cantidad de dichos polvos en una cámara de fusión para formar una capa de polvos con un espesor regular y sustancialmente uniforme;
d) precalentar dicha capa de polvos depositada en dicha cámara de fusión a una temperatura no inferior a 700°C pero por debajo del punto de fusión de dichos polvos;
e) realizar la fusión en condiciones de alto vacío realizando un barrido con un haz de electrones convergente en la zona correspondiente a una sección transversal de dichos artículos según el modelo tridimensional almacenado en dicha unidad de control;
f) poner la superficie superior de la última sección transversal de dichos artículos así formados al nivel de los polvos ubicados en dicha cámara de fusión y que están dispuestos alrededor de las partes ya formadas de dichos artículos;
g) repetir dichas etapas desde c) hasta f) hasta que se alcance la última sección transversal de dichos artículos según el modelo tridimensional almacenado en dicha unidad de control; y h) proporcionar una etapa de enfriamiento final de dichos artículos al final de su formación en una atmósfera de gas inerte una vez que la temperatura de los artículos ha caído por debajo de aproximadamente 1200°C.
2. Procedimiento según la reivindicación 1, en el que dichos polvos y dichos artículos están hechos de compuestos intermetálicos de yTiAI.
3. Procedimiento según la reivindicación 1, en el que dicho gas inerte está constituido por helio o mezclas del mismo.
4. Procedimiento según la reivindicación 1, en el que dicha etapa de precalentamiento d) se realiza completa o parcialmente realizando un barrido con un haz de electrones convergente.
5. Procedimiento según la reivindicación 1, en el que dicha etapa de precalentamiento d) se realiza completa o parcialmente calentando dicha cámara de fusión usando resistencias eléctricas.
6. Procedimiento según la reivindicación 1, en el que dicha etapa de precalentamiento d) se realiza a una temperatura lo suficientemente alta para provocar una sinterización débil de los polvos al menos en la zona de cada sección transversal de dichos artículos.
7. Procedimiento según la reivindicación 1, en el que dicha etapa de fusión c) se realiza moviendo dicho haz de electrones convergente a lo largo de una trayectoria de barrido transversal con un ángulo que oscila desde 60 hasta 90 grados con respecto a aquél con el que se realizó la etapa de fusión de la sección transversal de debajo.
8. Procedimiento según la reivindicación 1, en el que dicha etapa de fusión e) incluye inicialmente fundir con haz de electrones convergente a lo largo del perímetro de la zona correspondiente a una sección transversal de dichos artículos.
9. Procedimiento según la reivindicación 1, en el que durante cada repetición de dichas etapas desde c) hasta f) se proporciona la formación de una o más partes para soportar las secciones transversales que se forman sucesivamente.
10. Procedimiento según la reivindicación 9, en el que se proporciona la eliminación de dicha una o más partes de soporte después de que dichos artículos se hayan formado.
11. Procedimiento según la reivindicación 1, en el que el tamaño de grano de dichos polvos es de aproximadamente 70 !m.
12. Procedimiento según la reivindicación 1, en el que dichos polvos se obtienen mediante procedimientos de atomización de gas.
13. Procedimiento según la reivindicación 1, en el que en cada ciclo de etapas repetidas desde c) hasta f) se forma una sección transversal de dichos artículos con un espesor que oscila desde 20 hasta 150 !m.
Patentes similares o relacionadas:
Aparato de conformación tridimensional, del 29 de Julio de 2020, de MATSUURA MACHINERY CORPORATION: Un aparato de conformación tridimensional comprendiendo una plataforma de conformación que es subida y bajada dentro de un depósito de conformación […]
Sistema de conformación de laminación tridimensional, procedimiento de conformación de laminación tridimensional, dispositivo de control de conformación de laminación y procedimiento de control y programa de control para los mismos, del 29 de Julio de 2020, de Technology Research Association for Future Additive Manufacturing: Un aparato de control de laminación y fabricación que comprende:
un adquirente de datos que adquiere datos de un objeto […]
Procedimiento y dispositivo para fabricar una estructura de superficie tridimensional de una herramienta de prensa, del 22 de Julio de 2020, de HUECK RHEINISCHE GMBH: Procedimiento para la fabricación de una estructura de superficie de una herramienta de prensado de gran formato con al menos una longitud de borde de más de […]
Aparato y métodos de manufacturación de aditivos, del 15 de Julio de 2020, de RENISHAW PLC: Un método de fabricación de una pieza de trabajo en un proceso de manufacturación de aditivos en los que la pieza de trabajo es construida mediante la […]
Procedimiento para la producción de componentes metálicos por medio de fabricación generativa, del 15 de Julio de 2020, de MESSER GROUP GMBH: Procedimiento para la producción de componentes metálicos por medio de fabricación generativa, en el que se genera una capa de polvo metálico en una cámara de granallado […]
Procedimiento para la fabricación generativa y la codificación de un elemento constructivo tridimensional, del 24 de Junio de 2020, de Linde GmbH: Procedimiento para la fabricación generativa y la codificación de un elemento constructivo tridimensional, que comprende las siguientes etapas
proporcionar […]
Aparatos y métodos para fabricación aditiva de conjuntos a gran escala, del 17 de Junio de 2020, de THE BOEING COMPANY: Un aparato de fabricación aditiva que comprende: un riel lineal, que tiene una longitud L1, en el que el riel lineal es […]
Método para fabricar una herramienta de conformación en caliente y herramienta de conformación en caliente fabricada con este, del 10 de Junio de 2020, de Buderus Edelstahl Gmbh: Método para la producción de una herramienta de conformación en caliente para el endurecimiento y conformación o el endurecimiento en prensa […]